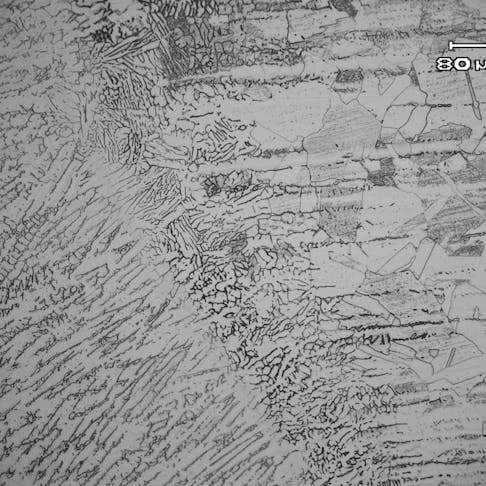
Pearlitic Stainless Steel: Composition, Uses, Performance, and Benefits in Manufacturing
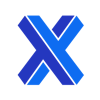
Pearlitic stainless steel is an alloy that is well-known for its distinct makeup and wide range of industrial uses. Made up of layers upon layers of ferrite and cementite, pearlite has a unique microstructure that gives it remarkable strength and durability. The performance features of this steel variation make it widely used in a variety of industrial sectors, including: construction, automotive, and aerospace.
This article will discuss pearlitic stainless steel, its composition, uses, and benefits.
What Is a Pearlitic Stainless Steel?
Pearlitic stainless steel is an alloy characterized by its microstructure composed of alternating layers of ferrite and cementite, known as pearlite. This unique arrangement imparts exceptional strength and toughness to the material. The ferrite phase consists of iron atoms, while the cementite phase is a compound of iron and carbon. This composition results in a material with superior mechanical properties, making it ideal for a wide range of industrial applications. Pearlitic stainless steel is widely used in automotive components, aerospace structures, and construction materials due to its excellent performance and durability.
What Is the Composition of Pearlitic Stainless Steel?
The main constituents of pearlitic stainless steel are carbon and iron, with additional alloying metals like: molybdenum, nickel, and chromium. More strength, toughness, and corrosion resistance are all attributes to which the alloying elements significantly contribute. Controlled cooling of the steel throughout the production process helps to generate the pearlite microstructure, which is a layered arrangement of cementite and ferrite. Stainless steel has a high level of corrosion resistance because the alloy's chromium content encourages the development of a passive oxide layer on the surface. Pearlitic stainless steel can be used in a variety of sectors and for a wide range of purposes due to its composition.
To learn more, see our full guide on the Types of Stainless Steel.
What Processes Are Involved in the Production of Pearlitic Stainless Steel?
The production of pearlitic stainless steel involves several processes:
- Melt the raw materials such as: iron ore, coal, and limestone in a blast furnace to produce molten pig iron.
- Transfer the molten pig iron to a converter to remove impurities. Add alloying elements such as chromium and nickel to achieve the desired composition.
- The molten steel undergoes further refining in a ladle furnace to adjust its composition and remove any remaining impurities.
- Pour the refined molten steel into continuous casting machines to form continuous strands of steel, which are then cut into billets or slabs.
- Heat the billets or slabs and pass them through rolling mills to reduce their thickness and shape them into intermediate products like: plates, sheets, or bars.
- Cool the intermediate products to facilitate further processing or storage.
What Distinguishes Pearlitic Stainless Steel Mechanically and Chemically?
Pearlitic stainless steel stands out mechanically due to its high strength, resistance to wear, and moderate hardness. Its characteristics render it appropriate for use in tire cords, spring components, and bridge cables for structural purposes. Alloying elements including: chromium, nickel, and molybdenum are present in pearlitic stainless steel, improving both its mechanical and corrosion resistance. Chromium causes the surface to create a passive oxide layer, which shields the steel against corrosion in abrasive conditions.
How Hard Is Pearlitic Stainless Steel?
The hardness of pearlitic stainless steel usually ranges from 300 to 500 HV (Vickers Hardness). The Vickers hardness test is used to assess hardness. It involves pressing a diamond indenter into a material's surface while applying a certain load and measuring the size of the impression that results by optical means. The Vickers hardness rating expresses how resistant the material is to deformation when subjected to applied stress. Pearlitic stainless steel's hardness makes it suitable for applications requiring durability and resistance to abrasion.
Where Is Pearlitic Stainless Steel Typically Used?
Here are five common uses of pearlitic stainless steel:
- Bridge Cables: Due to its high strength and corrosion resistance, pearlitic stainless steel is often used for constructing cables in bridges, ensuring structural integrity and durability.
- Tire Cords: Pearlitic stainless steel is utilized as tire cords in the automotive industry to reinforce tires, enhancing their strength and longevity.
- Springs: The material's combination of strength and toughness makes it ideal for manufacturing various types of springs, including those used in: automotive, industrial, and household applications.
- Cutting Tools: Pearlitic stainless steel is employed in the production of cutting tools such as: knives, chisels, and cutting blades due to its wear resistance and hardness.
- High-Strength Wires: It is commonly used in the production of high-strength wires, including piano wires, for which its robustness and durability are critical for load-bearing applications.
How Does Pearlitic Stainless Steel Compare to Ferritic Stainless Steel?
The microstructure and mechanical characteristics of pearlitic stainless steel are essentially different from those of ferritic stainless steel. Ferrite, a soft and ductile material, makes up the majority of ferritic stainless steel, whereas pearlitic stainless steel is a combination of ferrite and cementite. In contrast to ferrite, pearlite is more brittle and tougher. Higher bulk strength results from a higher amount of pearlite in steel that has a higher carbon content. Compared to ferritic stainless steel, pearlitic stainless steel has different mechanical qualities due to its different microstructure and composition, which makes it more appropriate for applications that demand higher wear resistance and hardness.
To learn more, see our full guide on What is Ferritic Stainless Steel.
How Does Heat Treatment Affect the Properties of Pearlitic Stainless Steel?
Heat treatment significantly affects the properties of pearlitic stainless steel by altering its microstructure and mechanical characteristics. During heat treatment, the pearlite microstructure changes its composition and arrangement, leading to adjustments in hardness, strength, and ductility. Depending on the specific heat-treatment process, such as: annealing, quenching, or tempering, the steel's hardness, toughness, and corrosion resistance can be tailored to meet desired specifications. For example, annealing can refine the pearlite structure, enhancing ductility, while quenching and tempering can increase hardness and strength. Thus, heat treatment plays a crucial role in optimizing the properties of pearlitic stainless steel for various applications.
What Is the Performance of Pearlitic Stainless Steel in Corrosive Environments?
Pearlitic stainless steel demonstrates excellent performance in corrosive environments due to its inherent corrosion resistance properties. The alloying elements, particularly chromium, present in pearlitic stainless steel form a passive oxide layer on the surface, which acts as a barrier against corrosion agents such as: moisture, oxygen, and aggressive chemicals. This passive oxide layer provides long-term protection to the steel, making it resistant to rust, tarnishing, and corrosion even in harsh environments. As a result, pearlitic stainless steel is widely utilized in applications in which corrosion resistance is paramount, such as: marine environments, chemical processing plants, and outdoor structures.
How Does Pearlitic Stainless Steel Perform During Welding and Machining?
Pearlitic stainless steel's microstructure and composition present difficulties for welding and machining. Carbon diffusion happens during welding, particularly in heat treatment and high-temperature operations. This results in the production of decarburization or carburization layers, which affect the microstructure and hardness of the base metal. Additionally, during post-weld cooling, variations in the linear expansion coefficients of pearlitic steel and other materials may cause thermal stress, which may have an impact on joint strength and thermal fatigue. The hardness of pearlitic steel also makes machining more difficult, necessitating the use of suitable tools and machining methods to accomplish desired results while reducing tool wear and preserving dimensional accuracy.
What Are the Benefits of Using Pearlitic Stainless Steel in Manufacturing?
Benefits of using pearlitic stainless steel in manufacturing include:
- Offers exceptional strength, making it suitable for structural applications whenever robustness is essential.
- Its microstructure provides excellent wear resistance, ensuring durability and longevity in harsh operating environments.
- Combines strength with moderate toughness, allowing it to withstand mechanical stresses without compromising performance.
- Exhibits good corrosion resistance, making it suitable for applications exposed to corrosive environments.
- Its versatile properties make it suitable for various manufacturing applications, including: bridge cables, tire cords, and spring parts.
What Are the Limitations of Pearlitic Stainless Steel in Manufacturing?
Limitations of pearlitic stainless steel in manufacturing include:
- Can exhibit brittleness, particularly at low temperatures, which may limit its suitability for certain applications requiring high ductility.
- Can be challenging to machine due to its hardness and microstructure, requiring specialized tools and techniques.
- Welding can pose challenges due to the potential for the formation of brittle zones and heat-affected-zone issues, requiring careful control of welding parameters.
Is Recycling of Pearlitic Stainless Steel Sustainable in Production?
For several reasons, recycling pearlitic stainless steel is essential to sustainable production methods. It uses a lot less energy than primary production processes, which lowers greenhouse gas emissions and preserves precious energy resources. This makes a big difference in energy efficiency. Recycling also reduces the environmental impact of mining and extraction processes, which helps maintain natural resources by reducing reliance on virgin minerals like iron ore and chromite ore. Recycling also promotes a circular economy, lessens environmental contamination, and diverts discarded material from landfills, which reduces garbage disposal and landfill burden. Recycling is advantageous from an economic standpoint since it reduces production costs, promotes employment growth in the recycling sector, and creates a more sustainable supply chain.
Is Pearlitic Stainless Steel Ductile?
No, pearlitic stainless steel is not typically considered ductile. The pearlitic microstructure, consisting of alternating layers of ferrite and cementite, tends to reduce ductility compared to other stainless steel types. The presence of cementite, a relatively brittle phase, within the pearlitic structure can limit the material's ability to deform plastically under tensile stress, making it less ductile. While stainless steel in general exhibits good ductility, the specific microstructural characteristics of pearlitic stainless steel contribute to its lower ductility compared to other stainless steel alloys.
What Is the Difference Between Pearlitic Stainless Steel and 18/10 Stainless Steel?
The main differences between 18/10 and pearlitic stainless steel are in their composition and characteristics. While 18/10 stainless steel has a lower carbon content and a greater chromium and nickel content, which leads to superior corrosion resistance and malleability, pearlitic stainless steel often contains a higher carbon content, which contributes to its hard and brittle nature. Applications for both materials include: industrial equipment, cookware, and utensils. However, because it is non-reactive, 18/10 stainless steel is more often employed in food-related applications, while pearlitic stainless steel is the ideal material for structural components that need to be highly durable and strong.
To learn more, see our full guide on What is 18/10 Stainless Steel.
Summary
This article presented pearlitic stainless steel, explained it, and discussed its composition and various applications. To learn more about pearlitic stainless steel, contact a Xometry representative.
Xometry provides a wide range of manufacturing capabilities and other value-added services for all of your prototyping and production needs. Visit our website to learn more or to request a free, no-obligation quote.
Disclaimer
The content appearing on this webpage is for informational purposes only. Xometry makes no representation or warranty of any kind, be it expressed or implied, as to the accuracy, completeness, or validity of the information. Any performance parameters, geometric tolerances, specific design features, quality and types of materials, or processes should not be inferred to represent what will be delivered by third-party suppliers or manufacturers through Xometry’s network. Buyers seeking quotes for parts are responsible for defining the specific requirements for those parts. Please refer to our terms and conditions for more information.
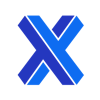