CNC Machining in HDPE
High-Density Polyethylene or HDPE is an engineering plastic that is employed extensively in the packaging industry. CNC machining in HDPE can also be used to create components for the construction, electrical, and automotive industries, among others. HDPE has an excellent strength-to-weight ratio, as well as good chemical and moisture resistance.
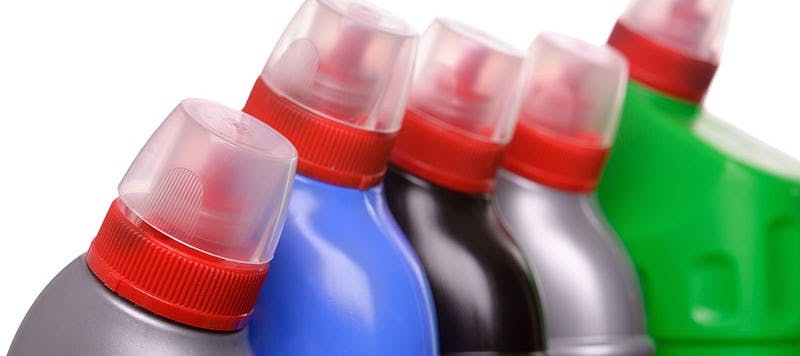
About HDPE for CNC Machining
HDPE is sometimes called PEHD (polyethylene high-density) and is part of the polyethylene (PE) family of plastics. Despite its name, HDPE has only marginally higher density than LDPE (low-density polyethylene). However, the difference in strength between the two plastics is more significant than the difference in density. This makes HDPE a great choice for applications that require high strength and low weight. CNC machining in HDPE is similar to that of other engineering plastics.
Generic HDPE
CNC machining in HDPE produces strong but lightweight parts. HDPE parts also have excellent corrosion resistance against a wide range of chemicals. Typical applications include boat components, piping, and containers.
Tensile Strength, Yield (MPa) | Elongation at Break (%) | Hardness (Shore D) | Flammability Rating | Glass Transition Temperature (°C) |
---|---|---|---|---|
Tensile Strength, Yield (MPa) 25.9 | Elongation at Break (%) 622 | Hardness (Shore D) 62.3 | Flammability Rating 80.6 | Glass Transition Temperature (°C) 130 |
Finishes
Like other plastics in the PE family, HDPE is highly resistant to coatings. It resists adhesives for much the same reason and, as such, needs to be bonded via plastic welding. HDPE is most often available in black or white but can occasionally be found in a wider range of colors. Due to the above factors, HDPE parts are usually left in their as-machined state.
As Machined: The challenges of CNC machining in HDPE are similar to those experienced with other engineering plastics. The machined surface of HDPE comes out with a matte finish.
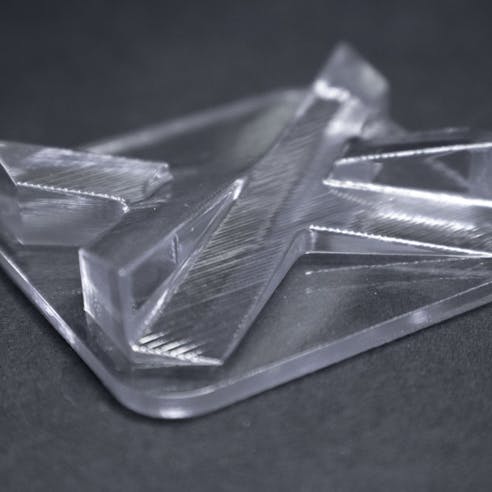
Cost-saving Design Tips
CNC machining in HDPE can produce lightweight and low-cost components. Below are some additional cost-saving tips to make production more economical.
Sub Assemblies: HDPE is purchased as sheet or bar stock in varying sizes. Designing parts as separate components that can then be assembled into the final whole is often a good idea. As mentioned above, HDPE does not work well with adhesives but can be welded. Alternatively, mechanical fasteners can be used to bolt components together.
Annealing: HDPE is prone to developing surface cracks when exposed to the heat and stress of machining. Annealing HDPE will help prevent cracks that may render the part useless.
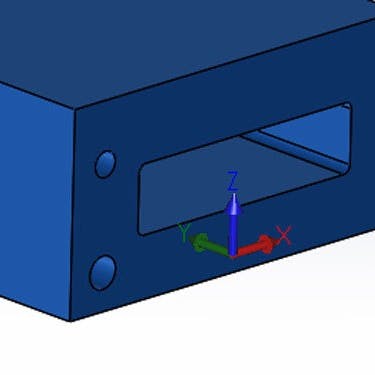