Engendering a Strong American Manufacturing Workforce
Ensuring manufacturing’s place in the future of the U.S. economy requires a well-trained, highly-skilled, and diverse workforce, capable of handling the complex and adaptive work that makes up modern-day manufacturing.
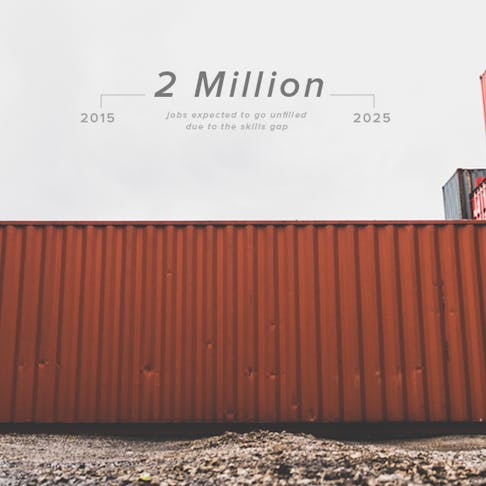
Manufacturing has been silently coming back onshore for the last few years. The manufacturing job “bleed” that started during the first heady days of globalization and continued through 2010 has effectively been stanched. According to the Re-shoring Initiative, On-shoring now breaks even with offshoring, and will soon surpass it.
Manufacturing is officially coming home to roost.
From the fast growth of technology in manufacturing to the reality of steadily rising wages in developing countries, making things “over there” is no longer as cost-effective, time-effective or reliable as it used to be. More and more American companies are on-shoring, and the nation has surpassed China to lead in foreign direct investment (FDI). Manufacturing has shifted, and while the American worker stands to gain, this meaningful shift in American manufacturing is still no guarantee of future success.
Over the course of the next decade, the U.S. economy is projected to need 3.5 million manufacturing jobs. Unfortunately, 2 million of these are likely to go unfilled due to a skills and training gap that is only starting to be addressed. And that’s looking ahead at a problem that’s already here. The Manufacturing Institute reports that 82% of manufacturers today suffer from a moderate to severe skills gap, meaning that products never make it to market, growth is impeded and the ability to sustain current business is at risk simply because there are not enough people to do the work. Add to this number the fact that nearly a quarter of workers who are currently employed will reach retirement age in the next few years, and the true skills gap in manufacturing starts to emerge.
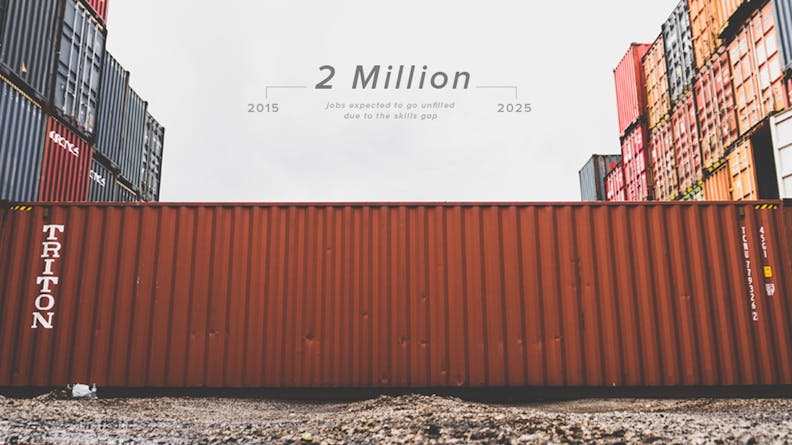
Meanwhile, the nature of work is changing —and changing quickly. Automation, robots, cobots, IIoT, additive manufacturing and other advances are allowing every industry to do vastly more with fewer traditional workers and U.S. manufacturing is especially ripe for this transformation. Unless the U.S. workforce can actually do the manufacturing jobs coming back from overseas, they’re likely to languish here before landing elsewhere. What’s needed to secure America’s future in Manufacturing is a comprehensive way to assist displaced workers with skills training and education, as well as a revitalization effort to bring in new, diverse talent into the manufacturing workforce.
Investment in a 21st-century manufacturing workforce is essential. Whether that investment comes, as former editor-in-chief of International Business Times, Jeffrey Rothfeder, has suggested, via tax incentives given to companies that offer real-world apprenticeships, STEM education or via federally funded retraining programs, is beside the point — they are all crucial efforts.
But just training and retraining the current workforce is not enough to create energy and change in the American manufacturing industry. Both the Manufacturing Institute and The National Association of Manufacturers (NAM) are in agreement that for U.S. manufacturing to compete in coming years and decades, it also must attract, train and embrace a more diverse workforce. Greater diversity — what someone is born with and what he or she acquires from life’s experiences — is proven to engender a more innovative atmosphere in the companies that employ it. And innovation is the bread and butter of any successful, enduring industry.
People of color and immigrants should be sought out and welcomed by those manufacturing companies that want to maintain competitiveness, and within that advance, greater gender diversity is also a vital element. Women are the largest source of untapped talent in the U.S. Labor force — a gap which is particularly relevant in manufacturing. To attract a more varied workforce, manufacturing must become a supportive industry for those workers.
From capturing new markets and increasing market share to inspiring and driving innovation, there are real bottom line reasons to make sure your workforce isn’t homogenous. That U.S. manufacturing is vital to the success of everyone working in or invested in the industry (as well as the U.S. economy’s health as a whole) is something everyone can agree on. Ensuring manufacturing’s place in the future of the U.S. economy requires a well-trained, highly skilled, and diverse workforce, capable of handling the complex and adaptive work that makes up modern-day manufacturing.
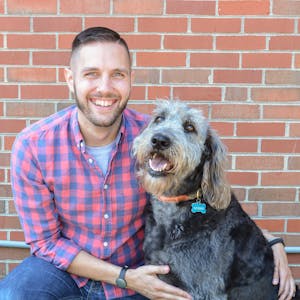