MJF, which is an abbreviation for multi-jet fusion, is a much-beloved type of 3D printing that comes packed with some pretty impressive benefits, like the fact its parts can be up to 98% isotropic, the powder is reusable (up to 80% of unused material), it’s fast, and its parts are very detailed. MJF printers also come with removable build volumes, allowing you to remove a completed part and cool it while you install another part and carry on with the printing process, making it excellent for high-volume production. Another bonus is that no support structures are required during printing. So, with all these benefits in mind, what exactly is MJF, and how does it work? Let’s see.
What is MJF?
Multi-jet fusion creates 3D-printed parts using nylon, polypropylene, or TPU (thermoplastic polyurethane), all in powdered form. It was developed by HP Additive and commercially released in 2016. Compared to other more established methods of 3D printing, MJF is a relatively new kid on the block but has gained popularity because of how good it is.
It works by applying a fusing and detailing agent to a thin layer of powder that’s been placed in the shape of the part’s cross-section at a pre-set height. The fusing agent is good for absorbing heat and the detailing agent helps the edges be crisper and sharper, as well as prevents the molten plastic from bleeding past the edges of the part. An infrared heat source then bonds the powder into the final part by sintering the particles together wherever the fusing agent is applied, which is followed by the print bed moving down by the thickness of one layer (usually around 80 microns), and the process repeats itself. The following image shows a part made using this process:
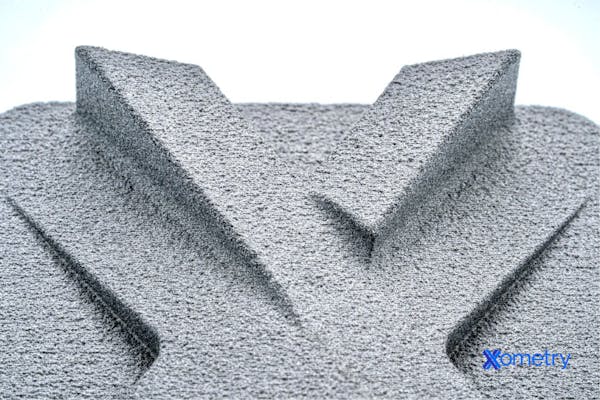
Available Materials
Lots of materials can work with MJF printing, the most common of which is probably PA12, which is a form of nylon. These types of printers can also print elastomeric parts. Here’s the full range of materials compatible with MJF:
- PA11 (nylon) is very flexible yet tough—even more so than PA12, which we’ll consider shortly. It’s a great material for end-use parts.
- PA12 (nylon) has very good resistance to cracking and has the lowest moisture absorption of all the polyamides. You can also find glass-filled variants. This material is good for making functional prototypes.
- PP (polypropylene) is perfect for prototypes that can imitate the performance of injection-molded polypropylene.
- TPU01 (thermoplastic polyurethane) is a material that has a great balance between flexibility and shock absorption. It can also make features with high resolutions.
- TPU M95A (thermoplastic polyurethane) has very good resistance to abrasion, as well as high elongation at its break strength. You can use this material to make a variety of things, like shoe insoles and seals, as well as functional prototypes.
- TPA (thermoplastic polyamide) is a lightweight, highly flexible elastomer. In low temperatures, it has impressively high elongation.
The image below shows a polypropylene part we made at Xometry using MJF:
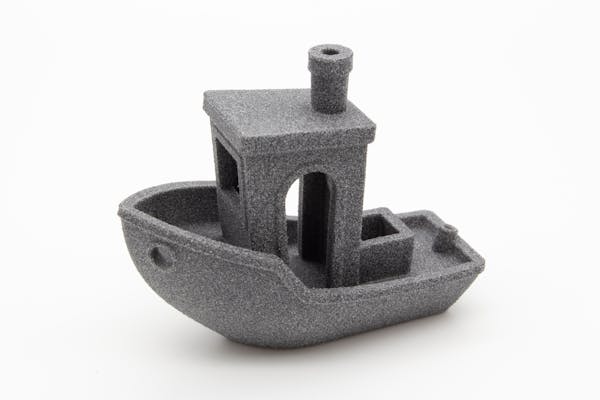
Property | Minimum Size |
---|---|
Property Layer height | Minimum Size 80 μm |
Property Minimum slit between walls | Minimum Size 0.5 mm |
Property Minimum hole diameter (part thickness of 1mm) | Minimum Size 0.5 mm |
Property Minimum feature size | Minimum Size 0.1 mm |
Property Minimum font size for debossed or embossed text | Minimum Size 6 pt |
Table credit: HP MJF Handbook
Frequently Asked Questions on MJF
How dimensionally accurate are MJF parts?
Multi-jet fusion can create parts that can potentially only veer off by ± 0.15 % from nominal dimensions with a lower limit of 0.3 mm. After that point, the dimensional accuracy is neither defined nor guaranteed by machine manufacturers.
Are MJF 3D-printed parts water-resistant?
They can be. It boils down to how well-designed they are. HP has tested the IP (Ingress Protection) rating of the raw materials it typically uses and has achieved IP66 and IP67 waterproof ratings with them. In case you’re not familiar with these numbers, the first digit in the IP rating means that the part is completely protected against the ingress of dust. The second number, especially if it’s a 6, means that the part resists water intrusion. If that number is a 7, it means the part won’t absorb water, even if submerged.
What’s the maximum construction size with this method?
The largest HP MJF printer at the moment is the Jet Fusion 5200 series. It has a usable build volume of 380 x 284 x 380 mm. MJF printers differ from other types in that they allow you to stack parts in the entire volume, which maximizes the entire available space. That’s mainly because you don’t need support structures—the powder itself supports the part. A side note: if you’re making large hollow parts, you might want to consider including permanent support inside it to increase its mechanical strength.
What’s the difference between MJF and SLS?
They’re both powder bed fusion printing methods, but SLS, which stands for selective laser sintering, uses a laser to fuse the powder together, unlike the infrared energy source in MJF. It also requires support structures when printing. We have a whole guide on the difference between these two methods which you can check out.
How Xometry Can Help
If you have any other questions about MJF, SLS, or any other type of 3D printing, one of our representatives would be happy to help. Xometry also offers a plethora of other manufacturing services, including CNC machining, laser cutting, and powder coating. You can get started today by requesting a free, no-obligation quote from our website.
Disclaimer
The content appearing on this webpage is for informational purposes only. Xometry makes no representation or warranty of any kind, be it expressed or implied, as to the accuracy, completeness, or validity of the information. Any performance parameters, geometric tolerances, specific design features, quality and types of materials, or processes should not be inferred to represent what will be delivered by third-party suppliers or manufacturers through Xometry’s network. Buyers seeking quotes for parts are responsible for defining the specific requirements for those parts. Please refer to our terms and conditions for more information.
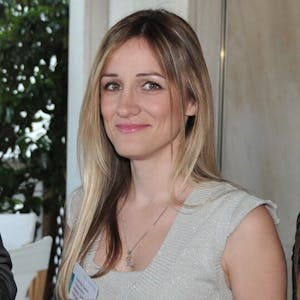