ASA 3D Printing
ASA (acrylonitrile styrene acrylate) was created to serve as a weather-resistant alternative to ABS and is well suited to outdoor applications due to its UV stability, tolerance of temperature changes, and chemical resistance.
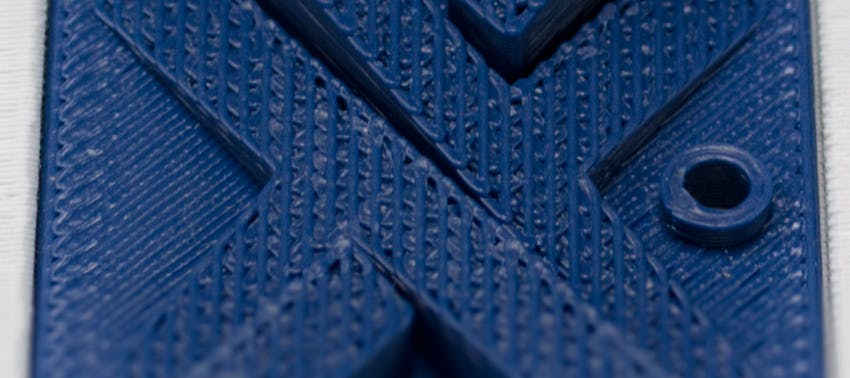
About 3D Printing With ASA
ASA filament (acrylonitrile styrene acrylate) is similar in composition to ABS but replaces butadiene with acrylate in its formulation. This addition is what makes ASA a superior material. It has excellent UV stability, enhanced toughness, high impact resistance, and improved resistance to temperature effects and can be made in a wide range of colors, and does not fade or yellow as readily as other plastics when exposed to sunlight.
Applies to US-based production only.
FDM ASA Prints
FDM, or fused deposition modeling, is the most widely recognized 3D printing technology and is capable of printing parts in a wide range of materials. As mentioned previously, ASA is a good material for parts that will be used outdoors. This makes it ideal for both end-use parts and functional prototypes that will be exposed to sunlight and harsh environmental conditions. Some typical applications can include housings for sensitive equipment or sporting equipment prototypes.
Tensile Strength (MPa) | Elongation at Break (%) | Hardness (Rockwell) | Heat Deflection Temperature (℃) | Glass Transition (℃) |
---|---|---|---|---|
Tensile Strength (MPa) 29 | Elongation at Break (%) 2 | Hardness (Rockwell) 82 | Heat Deflection Temperature (℃) 98 | Glass Transition (℃) 108 |
Applies to US-based production only.
Finishes
3D printing in ASA using FDM technology does not lend itself to many types of surface finishes. There are, however, up to 10 different colors of raw material available. In addition to this, some basic surface finishes are listed below.
Standard: Support structures are removed and some light sanding is performed at the support locations. In general, FDM parts typically have clear stepping, or layer lines. If a surface finish with smaller layers or no layers is required right off the machine, clients should consider other plastic 3D printing technologies like SLS, HP Multi Jet Fusion, SLA, PolyJet, and DLS.
Custom: Custom surface finishes like painting and additional sanding can be requested.
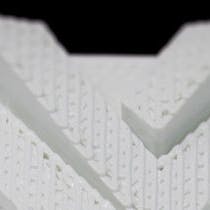
Cost-saving Design Tips
To save money when 3D printing in ASA, follow these cost-saving design tips:
DFM: FDM 3D printing in ASA requires special considerations when designing parts. FDM machines construct parts from the bottom up, so any large overhangs will require support. Large internal cavities are not ideal as support structures cannot be removed. This can, however, be overcome with special soluble supports, though this adds complexity to the construction. In addition to this, care must be taken when designing load-bearing components because FDM parts are generally weaker along the Z-axis due to the bond strength between layers. 3D printing in ASA is especially sensitive to interlayer adhesion during the print process—hence, the requirement for higher print temperatures.
Material Choice: ASA is more expensive than ABS and as such should not be used if its unique properties are not required. For example, if a part is only created as a visual prototype and will not see rough outdoor use, then standard ABS may be a better option.
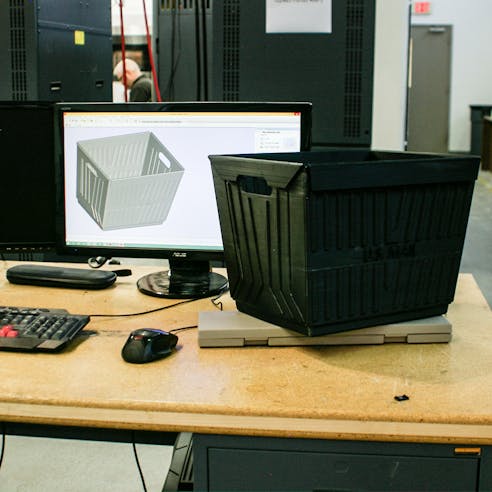