Nexa3D LSPc® Resin 3D Printing Service
Blazing Fast Parts Made From Production Photopolymers
Free Shipping on All US Orders
Blazing Fast Prototypes and Production Parts without Tooling
Nexa3D's Lubricant Sublayer Photo-curing (LSPc®) technology provides extremely fast and accurate 3D printing, making it suitable for low volumes to production quantities. Get parts made from a wide selection of materials, including ones that emulate ceramic and rubbers to engineered functional resins for medical, dental, and commercial industries. Xometry’s supplier network utilizes the NXE 400Pro and XiP Pro production printers and the XiP desktop printer for low-volume and prototype work.
In addition to traditional printed prototypes, Nexa3D LSPc® and its advanced resins can produce end-use parts, making it a great alternative to urethane casting or low-volume injection molding.
LSPc Materials Gallery
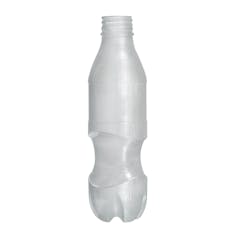
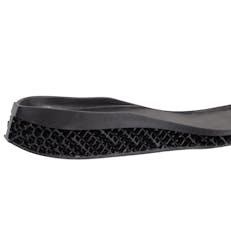
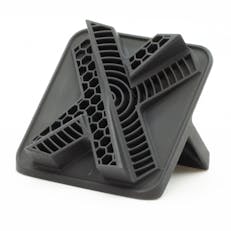
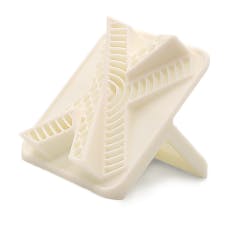
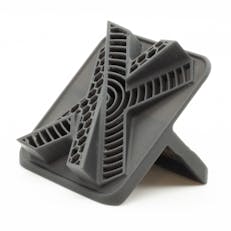
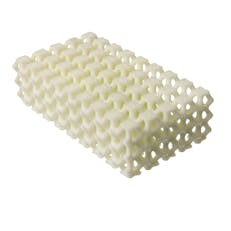
Nexa3D LSPc® Materials
Material Name | Description | Tensile Strength (MPa) | Elongation at Break (%) | HDT at 0.45 MPa (°C) | Data Sheets |
---|---|---|---|---|---|
Material Name xMODEL17 Clear | Description Clear/Translucent prototyping resin | Tensile Strength (MPa) 30 MPa | Elongation at Break (%) 22% | HDT at 0.45 MPa (°C) 47°C | Data Sheets |
Material Name 3843-xABS Black | Description Engineering grade, ABS-like | Tensile Strength (MPa) 32± 1 MPa | Elongation at Break (%) 50% | HDT at 0.45 MPa (°C) 56°C | Data Sheets |
Material Name xESD | Description Engineering grade, static-dissipative (10^7 Ω) | Tensile Strength (MPa) 68.1 MPa | Elongation at Break (%) 3.8% | HDT at 0.45 MPa (°C) 91.3°C | Data Sheets |
Material Name xPP405 Black | Description Engineering grade, black PP-like | Tensile Strength (MPa) 35 ±2 MPa | Elongation at Break (%) 100% | HDT at 0.45 MPa (°C) 52.8°C | Data Sheets |
Material Name xPEEK147 | Description Engineering grade, High temp (HDT 238C) | Tensile Strength (MPa) 75 ±2.0 MPa | Elongation at Break (%) 3% | HDT at 0.45 MPa (°C) 238°C | Data Sheets |
Material Name xFLEX402 | Description Semi-firm rubber-like elastomer (Shore A 73) | Tensile Strength (MPa) 5.5 MPa | Elongation at Break (%) 230% | HDT at 0.45 MPa (°C) (Unavailable) | Data Sheets |
Material Name xFLEX475 Black | Description Soft, high-rebound, rubber-like elastomer (Shore A 44) | Tensile Strength (MPa) 2.48 ±0.3 MPa | Elongation at Break (%) 150% | HDT at 0.45 MPa (°C) (Unavailable) | Data Sheets |
Material Name xFLEX475 White | Description Soft rubber-like elastomer (Shore A 55) | Tensile Strength (MPa) 3.8 ±0.8 MPa | Elongation at Break (%) 159% | HDT at 0.45 MPa (°C) (Unavailable) | Data Sheets |
Material Name xCERAMIC3280 | Description Ceramic composite-filled resin, Highly stiff | Tensile Strength (MPa) 85 MPa | Elongation at Break (%) 1.2% | HDT at 0.45 MPa (°C) 205°C (278°C After Post-Thermal Cure) | Data Sheets |
More LSPc® materials are available; select "Other" when quoting for custom requests!
Available Finishes for Nexa3D LSPc® Parts
Matte
Our default finish. The supported surfaces will be lightly sanded with 220 or 320 grit sandpaper, then media blasted for a uniform matte finish.
Natural
Supported surfaces will be lightly sanded with 220 or 320 grit sandpaper for improved surface quality. Sanding scratches will be visible on supported surfaces.
Strip and Ship
Supported areas may show small grid-like dots or surface blemishes as a result of support removal.
Custom
Xometry provides additional finishing options, including but not limited to sanding, polishing, painting, post thermal processing, and plating to meet your needs.
Design Tips for LSPc
Feature | Recommended Size - Any Material (mm) | xPEEK | xABS, xPP | xFLEX (elastomers) |
---|---|---|---|---|
Feature Wall Thickness | Recommended Size - Any Material (mm) 1-5 mm | xPEEK 0.3-25 mm | xABS, xPP 0.6-25 mm | xFLEX (elastomers) 0.5-50 mm |
Feature Gap Clearance | Recommended Size - Any Material (mm) 0.5 mm | xPEEK 0.5 mm | xABS, xPP 0.5 mm | xFLEX (elastomers) 0.5 mm |
Feature Minimum Features, Extrude | Recommended Size - Any Material (mm) 0.5 mm | xPEEK 0.3 mm | xABS, xPP 0.6 mm | xFLEX (elastomers) 0.8 mm |
Feature Minimum Features, Hole | Recommended Size - Any Material (mm) 1 mm | xPEEK 0.3 mm | xABS, xPP 0.5 mm | xFLEX (elastomers) 0.6 mm |
Feature Hole Depth | Recommended Size - Any Material (mm) <3x Diameter (blind), <8x Diameter (thru) | xPEEK <10x Diameter (blind), <25x Diameter (thru) | xABS, xPP <8x Diameter (blind), <25x Diameter (thru) | xFLEX (elastomers) <4x Diameter (blind), <12x Diameter (thru) |
Feature Text | Recommended Size - Any Material (mm) 0.4-0.8mm depth, >4mm height | xPEEK 0.2-1.5mm depth, 2.5mm height | xABS, xPP 0.2-1.5mm depth, 2.5mm text height | xFLEX (elastomers) 0.2-1.5mm depth, 2.5mm text height |
Feature Unsupported angle | Recommended Size - Any Material (mm) >30° | xPEEK >5° | xABS, xPP >10° | xFLEX (elastomers) >40° |
Feature Unsupported overhang | Recommended Size - Any Material (mm) <2mm | xPEEK <4mm | xABS, xPP <3mm | xFLEX (elastomers) <2mm |
Feature Unsupported span | Recommended Size - Any Material (mm) <5mm | xPEEK <20mm | xABS, xPP <15mm | xFLEX (elastomers) <8mm |
Source: Nexa3D
Ready to get started on your 3D printing quote?
Free shipping available for domestic 3D printing orders ; learn more!
Applications for Nexa3D LSPc® Technology
Ultrafast Printing
LSPc® technology is the fastest in it's category, enabling rapid prototyping and production quantities
Engineering Grade Materials
Choose from a wide selection of materials designed for end-use including rigid composites, rubber-like elastomers, and specialty options
Direct Digital Manufacturing
LSPc® technology provides accurate parts from low volume to production quantities, making it a cost-effective alternative to traditional molding or casting processes
Benefits of LSPc® 3D Printing
The speed and efficiency of Nexa3D's LSPc® 3D printing process make it an excellent solution for quickly iterating designs and producing pieces in higher quantities. A host of carefully selected and engineered printing resins allows components to exhibit unique properties and withstand end-use applications and environments. LSPc® printed parts demonstrate high resolution, detail, dimensional accuracy, and excellent surface finish.
With LSPc®, the number of parts does not affect the printing speed of each layer. This makes it particularly advantageous for printing high quantities of smaller pieces in a short amount of time. Simple post-processing procedures and swappable build trays in platforms like Nexa3D's XiP printer allow further production efficiency. LSPc® can act as a great bridge between initial production and higher quantity production solutions such as our injection molding service.
- Ultrafast printing speeds
- Wide range of engineered materials
- High dimensional accuracy and detailed resolution
- Smooth natural surface finish
- End-use parts in high quantities
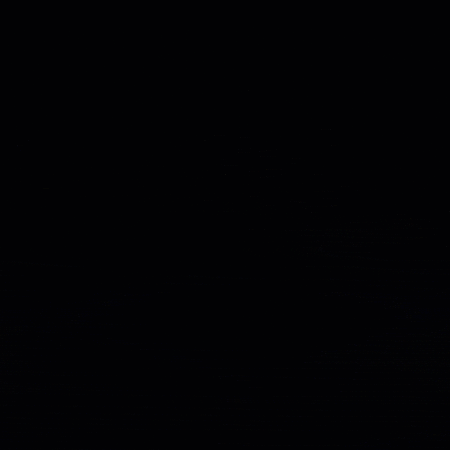
Nexa3D LSPc® General Tolerances
Description | Tolerance Notes |
---|---|
Description Tolerance, XY Plane | Tolerance Notes +/- 0.005” for the first inch is typical, plus +/- 0.002” for every inch thereafter |
Description Tolerance, Z Plane | Tolerance Notes +/- 0.010” for the first inch is typical, plus +/- 0.002” for every inch thereafter |
Description Layer Height | Tolerance Notes 100 µm / 0.004 in |
Description Ideal Part Size | Tolerance Notes Part's below 2" x 1" x 3" or smaller tend to have the best production economy of scale. |
Description Build Volume | Tolerance Notes Up to 10.8 x 6.1 x 15.7 in |
Description Minimum Wall Thickness | Tolerance Notes 0.030" or larger is suggested for any walls, text, or lattice features. |
Description Pixel Size | Tolerance Notes 52µm - 76.5µm |
This table depicts the general tolerances for LSPc®. Stresses during the build, support strategy, and other geometry considerations may cause deviation in tolerances and flatness. Improved tolerances may be possible with a manual quote review, after the successful completion of a prototype build, and must be approved on a case-by-case basis. General tolerances apply before secondary finishing or post-processing unless otherwise specified. Please check out Xometry's Manufacturing Standards for more information on tolerances per process.
Overview: What is Nexa3D LSPc® Technology?
LSPc stands for Lubricant Sublayer Photo-curing, which can be categorized as a type of mSLA (masked stereolithography apparatus) printing process. This type of printing technology uses an LED (light-emitting diode) array as a light source and an LCD (liquid crystal diode) photomask to selectively shape image layers. The images pass through a membrane on which layers of photopolymer resin are cured. As each layer is cured, the build platform moves up, the resin is replenished, and the next layer begins to set, building up parts over time. The key to Nexa3D's LSPc technology is their proprietary Everlast membrane designed to minimize peel and separation forces during printing. The specialized membrane is chemically inert, flexible, and does not rely on oxygen-permeable elements for lubricity. This enables LSPc technology to print in a wide range of resins with unparalleled speed and efficiency.
After printing, the parts are washed to remove uncured resin and receive a final post-cure in a UV light oven. Nexa3D's open material platform has a host of engineered resins, most of which do not require any additional post-processing steps other than the standard UV cure to achieve final part properties. While similar technologies and their materials, such as Carbon DLS™, may require and benefit from additional processing steps, they can lead to longer post-processing times and higher material costs. The efficiency and simplicity of post-processing LSPc® parts is another factor that makes this technology advantageous for high-volume 3D printing and a potential substitute for other production methods such as urethane casting or quick-turn molding.
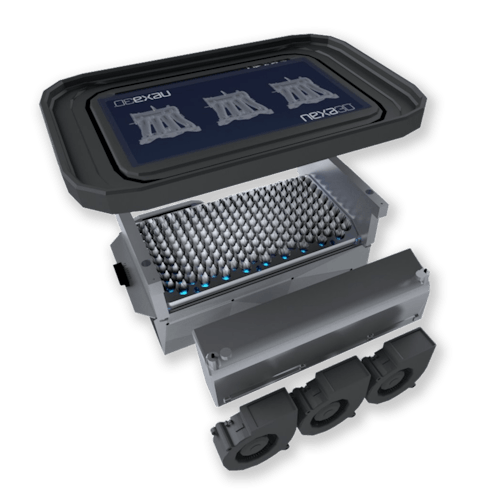
Why Choose Xometry for Your Production Needs?
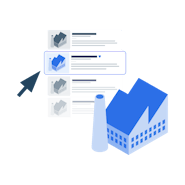
Endless Options
Choose from millions of possible combinations of materials, finishes, tolerances, markings, and certifications for your order.
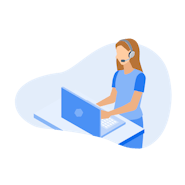
Easy to Use
Get your parts delivered right to your door without the hassle of sourcing, project management, logistics, or shipping.
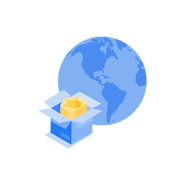
Vetted Network
We are ISO 9001:2015, ISO 13485, and AS9100D certified. Only the top shops that apply to become Suppliers make it through our qualification process.
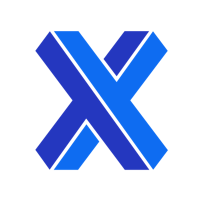
Ready to Start Your Project?
Free shipping available; learn more!