3D Printing Production Service
3D Print End-Use Production Parts Using Our Advanced Technologies and Materials
Free Shipping on All US Orders
Tool-Free Production With 3D Printing
With Xometry, you can access advanced 3D printing technologies such as Carbon DLS™ , Multi Jet Fusion, and others which offer industry-leading printing speeds and quality. Combined with a vast selection of materials from real thermoplastics to engineering-grade photopolymers, these technologies can create parts that will hold up to end-use applications and environments. With production printing, there is no need to invest in expensive tools or molds, which means economic parts are in your hands more quickly than traditional production processes like injection molding.
Our production viable proccesses are excellent choices for parts from various industries, including:
- Medical & Dental
- Automotive
- Aerospace
- Robotics & Electronics
- And more!
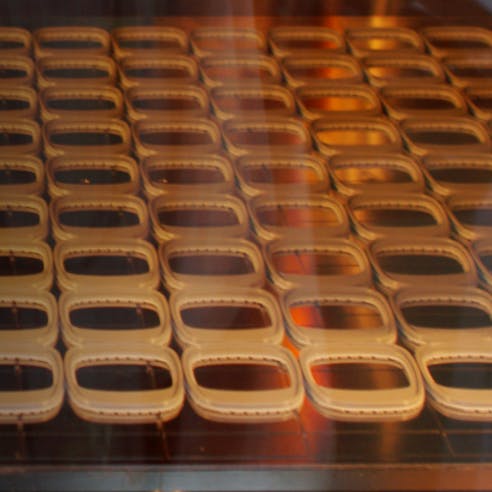
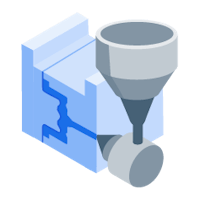
[Webinar] 3D Printing vs. Injection Molding for Production
Learn about when to choose each method for plastic part production.
About Additive Production Processes
Additive manufacturing processes viable for production share a few similarities. One of the most important factors for production is being able to make a large number of parts simotaneously. This means technologies with larger build volumes, ability to nest components, and print at a high speed are good candidates for production work. Material selection is another important consideration. There are many processes great for prototyping, but don't work in materials appropriate for end-use applications. For example popular photopolymer printing technologies, such as Stereolithography (SLA) and PolyJet, are excellent for creating detailed prototypes or lifelike concept models; however, the resins they work with are relatively fragile compared to other materials on the market.
It should be noted that when considering 3D printing for production, not all parts may be good fits. Generally smaller parts up to a few inches in their maximum dimension work best, as a higher quantity of pieces can fit into a single build that way. Parts with broad and flat geometries may be suseptible to warping during printing, making them difficult to guarentee quality and consistency at scale. Our experts are happy to review your project and provide the solutions that best fit your needs.
You can find out more about the specific processes we offer and recommend for production 3D printing in the sections below:
HP Multi Jet Fusion
Like all powder-based 3D printing processes, multi jet fusion technology builds parts layer by layer, however, MJF works a bit more like a traditional ink-jet printer with a printhead that deposits material followed by a heat activated fusing agent. These are applied across the entire build plate in one pass, allowing for the printing of multiple parts simultaneously, allowing you to print parts at rates up to 10X faster than SLS or other 3D printing processes. Multi Jet Fusion also delivers more balanced mechanical properties across the X, Y, and Z axes compared to SLS. Due to its affordability, speed, and high resolution, multi jet fusion technology can be used for end-use, low-volume production, rapid prototyping, or as a bridge process to injection molding. While MJF doesn't have as wide of a selection of materials compared to some other production processes, it offers popular go-to options such as Nylon, Polypropylene, and TPU.
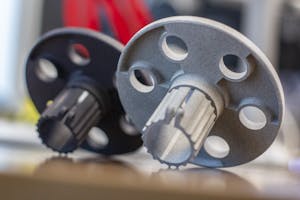
HP Multi Jet Fusion (MJF) 3D Printing Service
Selective Laser Sintering
Selective laser sintering (SLS) is another powder bed 3D printing technology that produces highly accurate and durable parts capable of being used directly in end-use, low-volume production. Parts are formed by heating material near it's melting point and utilizing a laser to precisely fuse particles together to construct a part layer by layer. Production is viable with SLS thanks to the ability to densely nest parts in the build volume, as well as handle larger geometries better than MJF. While it primiarly works with polyamides, it offers a good selection of both general purpose and engineering grade materials. Parts typically come out with an off-white appearance but can be customized a variety of colors with our dyeing options.
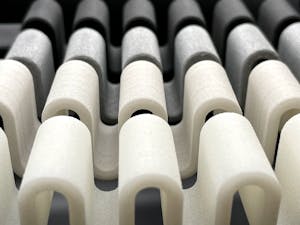
Selective Laser Sintering (SLS) 3D Printing Service
Carbon Digital Light Synthesis™
Carbon uses digital light projection, oxygen-permeable optics, and programmable liquid resins to produce products with end-use durability, resolution, and surface finish. The digital light synthesis process is continuous, without stopping layer-by-layer, as with most additive manufacturing. This gives the parts isotropic properties, meaning that strength is even regardless of orientation. DLS™ materials are urethane-based or epoxy-based, giving excellent mechanical properties, including elastomer and silicone resins that outperform most additive-manufactured rubber-like materials. Secondary thermal processing steps activate dormant epoxies or urethanes, making them much more robust than UV-curing alone. Along with Carbon's custom liquid resins, this technology unlocks new business opportunities and product designs previously impossible, including mass customization and on-demand inventory of end-use products.
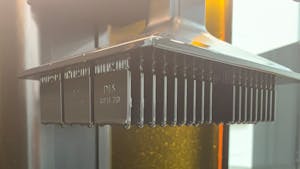
Carbon Digital Light Synthesis™ (DLS™) 3D Printing Service
Fused Deposition Modeling
With FDM technology, a spool of the chosen material is carefully regulated and fed by motors into a gantry-mounted hotend consisting of an extruder and nozzle where the filament is heated until it melts. This molten polymer is extruded through the nozzle and precisely deposited onto the build platform filling out the parts cross-section one layer at a time. While FDM may not be as quick as DLS™ or able to nest parts as effectively as MJF, it's build area gives it an advantage for production printing. With build volumes up to 24″ x 36″ x 36″, the process can fit tens or hundreds of parts into a single build, depending on their size. FDM also has one of the broadest ranges of materials to choose from out of all 3D printing processes, with real thermoplastic options ranging from general purpose to engineering-grades.
Fused Deposition Modeling (FDM) 3D Printing Service
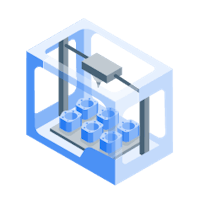
Ready to Start Production?
Free shipping available for domestic 3D printing orders ; learn more!
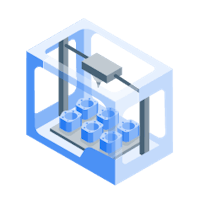
Production Materials Offered By Xometry
Xometry offers a wide selection of materials suitable for production parts. Our options comprise specially engineered resins, thermoplastics, and durable materials designed for practical end-use applications. The characteristics and properties of each vary greatly, allowing you to select the perfect one for your unique application. The chart below lists our standard production material options and can help you determine the right choice for your project.
General Purpose Production Materials
Material Name | Process | Characterstics | Use Case Examples | Elongation At Break (%) | Data Sheets |
---|---|---|---|---|---|
Material Name MJF Nylon 12 | Process HP MJF | Characterstics Highly durable, heat resistant, water tight | Use Case Examples Housings, enclosures, watertight parts, general use | Elongation At Break (%) 15% - 20% | Data Sheets |
Material Name SLS Nylon 12 | Process SLS | Characterstics Highly durable, heat resistant, natural white appearance | Use Case Examples Housings, enclosures, watertight parts, general use | Elongation At Break (%) 18% | Data Sheets |
Material Name MJF Polypropylene | Process HP MJF | Characterstics Chemical resistant, low-moisture absorbtion, durable | Use Case Examples Piping, fluid systems, containers, medical parts | Elongation At Break (%) 20% | Data Sheets |
Material Name ABS-M30 | Process FDM | Characterstics Strong, tough, lightweight, rigid | Use Case Examples Consumer electronics, housings, appliance parts | Elongation At Break (%) 2-7% | Data Sheets |
Material Name ASA | Process FDM | Characterstics UV resistant, strong, lightweight, matte finish | Use Case Examples Outdoor applications, consumer parts, tools | Elongation At Break (%) 3-9% | Data Sheets |
Material Name UMA 90 | Process Carbon DLS™ | Characterstics Single-cure resin, customizable color options, tougher than most SLA resins | Use Case Examples Prototyping, jigs, fixtures, general purpose | Elongation At Break (%) 17% | Data Sheets |
Material Name RPU 70 | Process Carbon DLS™ | Characterstics High flexural strength, tough, moderate heat resistance | Use Case Examples Housings, mechanical features, guides, end-use | Elongation At Break (%) 100% | Data Sheets |
Engineered Production Materials
Material Name | Process | Characterstics | Use Case Examples | Elongation At Break (%) | Data Sheets |
---|---|---|---|---|---|
Material Name MJF Nylon 11 | Process HP MJF | Characterstics Ductile, high impact and chemical resistance | Use Case Examples Snap fits, living hinges, sporting goods | Elongation At Break (%) 40% - 55% | Data Sheets |
Material Name MJF Nylon 12, GF | Process HP MJF | Characterstics Glass Bead Filled, highly stiff, dimensional stability | Use Case Examples Fixtures, tooling, housings | Elongation At Break (%) 10% | Data Sheets |
Material Name SLS Nylon 11EX | Process SLS | Characterstics Excellent elasticity and ductility, impact resistant | Use Case Examples Snap fit and thin-wall designs, living hinges | Elongation At Break (%) 45% | Data Sheets |
Material Name SLS Nylon 12, GF | Process SLS | Characterstics Glass filled, highly stiff, dimensional stability | Use Case Examples Larger rigid parts, jigs, fixtures, enclosures | Elongation At Break (%) 9% | Data Sheets |
Material Name Nylon 12, CF | Process SLS | Characterstics Carbon filled, very stiff, high impact strength | Use Case Examples Under hood engine components, tooling | Elongation At Break (%) 4% | Data Sheets |
Material Name Nylon 12, AF | Process SLS | Characterstics Aluminum filled, strong, stiff, wear resistance, detail reproduction | Use Case Examples Fixturing, wind tunnel models, automotive and aerospace components | Elongation At Break (%) 3% | Data Sheets |
Material Name Nylon 12, HST | Process SLS | Characterstics Mineral filled, non-conductive, high stiffness and temperature resistance | Use Case Examples High temperature load bearing parts, enclosures, structural components | Elongation At Break (%) 3% - 5% | Data Sheets |
Material Name Nylon 12, FR | Process SLS | Characterstics FAR 25.853 Flame-retardant, durable, slightly ductile | Use Case Examples Aerospace and automotive duct components, snap fits, electrical enclosures | Elongation At Break (%) 24% | Data Sheets |
Material Name PC-ABS | Process FDM | Characterstics Strong, tough, heat resistant, flexural strength | Use Case Examples Enclosures and casings, tool bodies, panels | Elongation At Break (%) 6% | Data Sheets |
Material Name Polycarbonate | Process FDM | Characterstics High strength, high impact and heat resistance | Use Case Examples Mechanical components, tools, brackets | Elongation At Break (%) 2.5% - 4.8% | Data Sheets |
Material Name ULTEM 9085 | Process FDM | Characterstics High strength-to-weight ratio, chemical and heat resistant, flame retardant | Use Case Examples Aerospace parts, electrical enclosures, structural components | Elongation At Break (%) 2.2% - 5.8% | Data Sheets |
Material Name ULTEM 1010 | Process FDM | Characterstics Very high thermal resistance and strength, chemical resistant, flame retardant | Use Case Examples Biocompatible devices, aerospace and automotive parts, tooling and fixtures | Elongation At Break (%) 2.0% - 3.3% | Data Sheets |
Material Name EPX 82 | Process Carbon DLS™ | Characterstics High chemical resistance, impact strength & toughness, good temperature resistance | Use Case Examples Automotive housings and connectors, parts for use in industrial environments | Elongation At Break (%) 5.9% | Data Sheets |
Material Name FPU 50 | Process Carbon DLS™ | Characterstics Excellent elongation, impact and fatigue resistant | Use Case Examples Repetitive stress applications, living hinges, friction fits, clips | Elongation At Break (%) 280% | Data Sheets |
Flexible & Rubber-Like Materials
Material Name | Process | Characterstics | Use Case Examples | Elongation At Break (%) | Data Sheets |
---|---|---|---|---|---|
Material Name TPU 88A | Process HP MJF | Characterstics Shock absorbing, high flexability, durability and fatigue resistance | Use Case Examples Insoles, seals and gaskets, grips, shock absorbing enclosures | Elongation At Break (%) 120% - 220% | Data Sheets |
Material Name EPU 40 | Process Carbon DLS™ | Characterstics Extremely durable rubber-like, excellent elongation, Shore 68A | Use Case Examples Buttons, grommets, strain reliefs | Elongation At Break (%) 310% | Data Sheets |
Material Name SIL 30 | Process Carbon DLS™ | Characterstics Tear-resistant silicone urethane elastomer, Shore 35A durometer | Use Case Examples Wearable devices, cushioning, gaskets | Elongation At Break (%) 330% | Data Sheets |
More materials are available! Select "Other" when quoting for custom requests.
Why Choose Xometry for Your Production Needs?
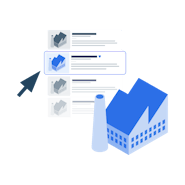
Endless Options
Choose from millions of possible combinations of materials, finishes, tolerances, markings, and certifications for your order.
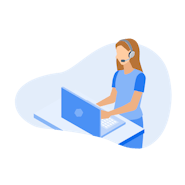
Easy to Use
Get your parts delivered right to your door without the hassle of sourcing, project management, logistics, or shipping.
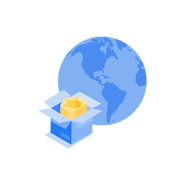
Vetted Network
We are ISO 9001:2015, ISO 13485, AS9100D and IATF 16949:2016 certified. Only the top suppliers make it through our qualification process.