Custom CNC Cutting Service by Xometry
Xometry offers the highest quality custom CNC cutting services and can assist in the production of parts with intricate and complex geometries and excellent surface finishes.
Xometry offers the highest quality CNC cutting services, including: CNC milling, routing, and laser cutting. This specialized service utilizes Computer Numerical Control (CNC) machines equipped with computer-controlled tools to deliver precise and accurate cutting of a wide range of materials. Each machine brings its own set of advantages and disadvantages to the table. With the ability to work with various materials such as metals, plastics, wood, foam, and composites, CNC cutting finds its applications in manufacturing, prototyping, decorative art, and architectural projects.
What Is CNC Cutting?
Computer Numeric Control (CNC) uses specialized tools to cut parts of different sizes and shapes. The process begins when designers create drawings using software like AutoCAD®. Digital drawing computer-aided manufacturing (CAM) software is employed to translate the design into instructions for the workpiece. The CAM software generates a toolpath and produces G-code that directs CNC machines. The program is then sent to the CNC machine which interprets the design.
In the case of CNC routers and milling machines, the cutting tool moves along the "X" axis horizontally, along the "Y" axis backward and forwards, and along the "Z" axis vertically. Both CNC routers and milling machines can perform cutting operations simultaneously along the three axes. In CNC-controlled laser cutting, CNC laser cutters rely on CNC and G-code instructions to carry out precise cutting operations. Laser cutting operates on a thermal-based process that does not require physical contact with the workpiece. The machine consists of a laser head equipped with a focusing lens as well as a nozzle. The laser head focuses an intense beam of light, known as the laser beam, onto the workpiece through the nozzle.
CNC cutting offers advantages over traditional methods, including: enhanced precision, automation, reproducibility, versatility across materials, capability for complex shapes, and improved time efficiency. However, traditional cutting methods still have their place for smaller-scale projects or situations in which high precision is not as important.
Types of CNC Cutting Machines
There are different CNC cutting machines on the market, each with its own unique function and material capabilities. CNC cutting machines are divided into two types: the traditional milling and routing CNC machines, and laser CNC-controlled cutters. Each of these different laser cutter types is discussed in the following sections, together with traditional CNC milling and routing machines:
- CNC Milling Machines
- CNC Routing Machines
- CNC CO2 Laser Cutters
- CNC Fiber Laser Cutters
- CNC Crystal Laser Cutters
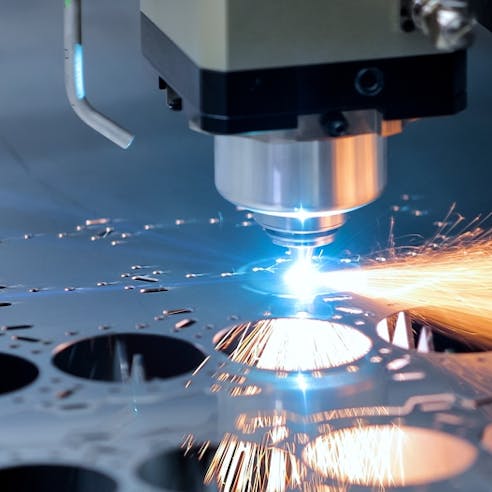
CNC Milling Machines
CNC milling machines are widely used in metalworking processes and are specifically designed for working with harder materials like metal. These machines operate by keeping the cutting head stationary while the workpiece moves along the three axes. The cutting tools used in CNC milling machines are typically designed to withstand the high forces involved in metal cutting. This allows milling machines to make deeper cuts and operate at slower speeds, providing the necessary torque and power for efficient metalworking. CNC milling machines excel in precision and accuracy, making them suitable for applications that require intricate metal parts with tight tolerances. They can also perform milling, drilling, and cutting operations on steel, plastic, aluminum, and wood.
CNC Routing Machines
CNC routing machines are primarily used for cutting softer materials such as: acrylic, wood, and MDF (medium-density fiberboard). These machines are known for their high-speed operation and versatility in working with various soft materials. Unlike CNC milling machines, CNC routers have a fixed cutting area, and the cutting head moves within this designated space along the three axes. They are often used in woodworking, sign-making, and prototyping industries. CNC routers can produce intricate shapes, patterns, and detailed cuts with precision. Their cutting tools are designed to provide clean and smooth cuts on softer materials. While they are capable of milling and cutting operations on metals, their speed and power may be limited in comparison to dedicated CNC milling machines.
CNC CO2 Laser Cutter
CO2 laser cutters stand out as gas laser systems that harness the power of carbon dioxide as their active laser medium. The laser cutting process has found widespread application across various industries for its exceptional power output and efficiency. CO2 laser cutters can generate power outputs up to an impressive 15 kW while achieving efficiencies of up to 30%.
CO2 laser cutters excel in precision cutting tasks, particularly when intricate details and sharp angles are involved. They prove especially effective in working with thin sheet metals and metals that are thinner than 10 mm. Moreover, higher-powered CO2 cutters can cut thicker metals, without compromising on the cut quality.
CNC Fiber Laser Cutters
A fiber laser cutter operates by utilizing a series of diodes in order to generate the laser, which is then transmitted through a fiber-optic cable. In comparison to CO2 laser cutters, fiber laser cutters offer distinct advantages, particularly when it comes to cleaner and faster cutting processes, especially for materials that are thinner than 5 mm.
The versatility of fiber lasers extends to a wide range of materials; however, it is essential to exercise caution when working with silver. Silver tends to retain heat coming from the laser, which can result in warping during the cutting process. This poses a challenge in achieving the desired precision in the final machined part. To mitigate this issue, reputable machine shops often employ a heat sink bracket as a solution to effectively transfer heat from the workpiece.
CNC Crystal Laser Cutters
This type of cutter uses laser beams generated from specific crystal materials, such as: neodymium-doped yttrium ortho-vanadate (Nd:YVO) and neodymium-doped yttrium aluminum garnet (Nd:YAG).
One notable advantage of crystal laser cutters over CO2 laser cutters is their typically higher laser power or intensity. This elevated power enables crystal laser cutters to effectively cut through thicker metal materials with precision. Moreover, crystal laser cutters exhibit compatibility with a diverse range of materials, including: metals, wood, glass, and plastics, expanding their versatility in various cutting applications.
Advantages of CNC Cutting Service
CNC cutting services offer several advantages that make them a preferred choice for precision cutting needs. Some of the key advantages include:
- Intricate Designs
- Low Risk of Metal Distortion
- Fast Turnaround Times
- Precision and Accuracy
- Material Versatility
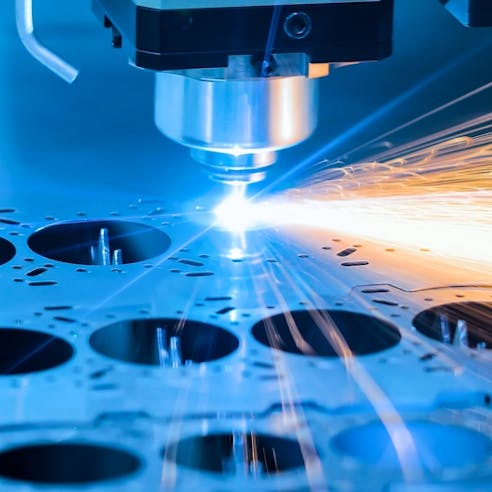
Intricate Designs
CNC cutting machines can accurately reproduce intricate and complex designs that would be difficult to achieve using traditional cutting methods. This capability enables the production of intricate shapes, patterns, and details with precision.
Low Risk of Metal Distortion
The non-contact characteristic of CNC laser cutting significantly reduces the likelihood of material distortion, as well as material contamination.
Fast Turnaround Times
CNC cutting services offer efficient and time-saving solutions. The automated nature of CNC machines allows for rapid production and reduces the time required for manual labor. This leads to increased productivity and faster turnaround times.
Precision and Accuracy
CNC cutting services utilize computer-controlled machines that ensure precise and accurate cuts. The cutting process is guided by computer programs and precise measurements, resulting in consistent and high-quality cuts every time. When using a cutting tool like an end mill with a diameter of 1/8", the smallest inside radius that can be achieved is typically around .062". In contrast, with laser cutting, the laser operator has the capability to set the laser beam to achieve a radius as small as .005".
Material Versatility
CNC cutting services can work with a wide range of materials, including: metals, plastics, wood, foam, and composites. This versatility allows for the production of diverse parts and components for various industries and applications.
Disadvantages of CNC Cutting Service
While CNC cutting services offer numerous advantages, there are also a few potential disadvantages to consider:
- Surface Quality
- Scale Effect
- Costly
- Metal Thickness Limitations
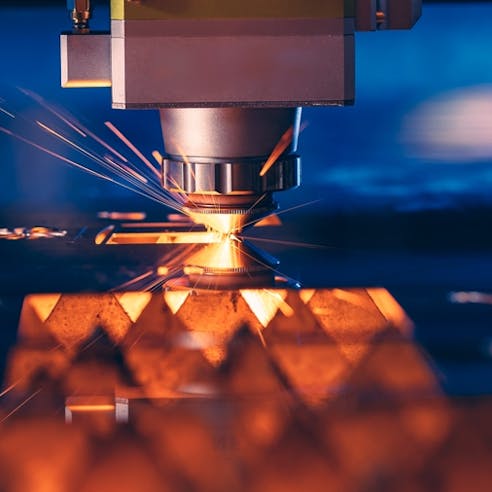
Surface Quality
Depending on the material and cutting method used, CNC cutting can sometimes result in rough or uneven surfaces. This may require additional post-processing steps, such as sanding or polishing, to achieve the desired smoothness or surface finish. The surface quality limitation is more pronounced when working with certain materials like plastics or brittle metals, in which the cutting process may generate heat and cause melting or deformation of the edges.
Scale Effect
CNC cutting services may face limitations in accurately reproducing extremely small or delicate features due to tool size constraints in the precision of the cutting machine. Achieving precise cuts on a micro-scale or intricate details may require specialized equipment or alternative manufacturing techniques.
Costly
Setting up CNC cutting services can involve a significant initial investment. The cost of purchasing and maintaining CNC machines, as well as training operators, can be substantial. This may pose a challenge for small businesses or individuals with limited resources.
Metal Thickness Limitations
While CNC cutting services can handle a wide range of materials, there may be limitations on the maximum thickness that can be effectively cut. Thicker materials may require specialized equipment or alternative cutting methods, which may increase costs or reduce efficiency.
In need of custom CNC cutting services?
Applications of CNC Cutting Services
CNC cutting machines find different applications in different industries. Some of the most common applications include:
- Decorative Wall Art
- Custom Signage
- Architectural Models
- Automotive Parts
- Aircraft Components
- Medical Devices
- Rapid Prototyping
- Molds and Patterns
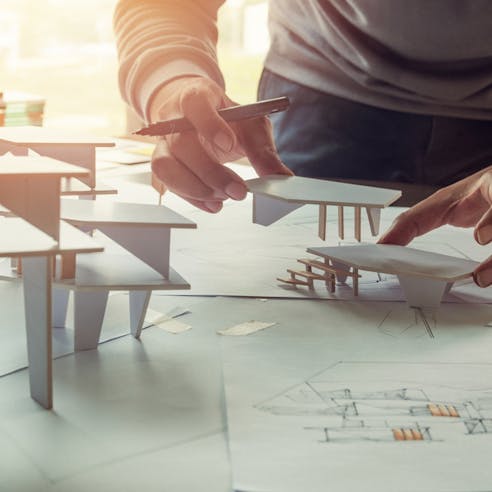
Decorative Wall Art
CNC cutting services are commonly used in the production of decorative wall art. This application finds its place in various industries, including: interior design, architecture, and retail. CNC routers or laser-cutting machines can be used for this purpose. The choice of machine depends on the material being used. For instance, CNC routers are suitable for cutting wood or acrylic, while laser cutting machines are more appropriate for working with materials like metal or glass. The precision and versatility of CNC cutting allow for intricate designs, precise detailing, and the ability to work with different thicknesses of materials.
Custom Signage
CNC cutting services are widely employed in the production of custom signage due to their speed and accuracy. This application is relevant to industries such as: advertising, marketing, retail, and hospitality. Both CNC routers and laser-cutting machines can be used depending on the desired outcome. CNC routers are suitable for cutting materials like wood, acrylic, PVC, or foam, while laser cutting machines are ideal for materials such as: metal, plastic, or glass.
Architectural Models
CNC cutting services are valuable for creating architectural models. This application is particularly relevant to architecture firms, real estate developers, and educational institutions. CNC routers are commonly used in this context due to their ability to work with a wide range of materials, including: foam, wood, plastic, and composite materials. CNC cutting allows for the precise fabrication of scaled models, intricate details, and complex structures.
Automotive Parts
CNC cutting services play a significant role in the manufacturing of automotive parts. This application is essential in the automotive industry, particularly for prototyping, custom parts production, and mass production. CNC milling machines and CNC laser cutting machines are commonly utilized in this domain. CNC milling machines are capable of machining various materials, including: metals, plastics, and composites, to create precise automotive components. CNC laser cutting machines are often used for intricate, high-precision cutting of sheet metal parts.
Aircraft Components
The aerospace industry relies heavily on CNC cutting services for the production of aircraft components. The complex shapes, varied sizes, and diverse materials used in aerospace engineering demand the extremely high levels of precision which CNC machines can deliver. CNC cutting ensures that aircraft parts meet stringent quality standards, ensuring safety and optimal performance.
Medical Devices
CNC cutting machines play a crucial role in the healthcare sector by manufacturing certain medical components such as: electronic enclosures, implants, surgical instruments, and orthotics. The precision and accuracy of CNC cutting enable the creation of intricate medical devices that meet strict regulatory requirements and provide better patient outcomes.
Rapid Prototyping
CNC cutting services are invaluable for rapid prototyping across various industries. CNC machines can quickly produce functional prototypes from digital designs with high accuracy. This allows for efficient product development, testing, and refinement before moving to mass production.
Molds and Patterns
CNC cutting machines are employed in indirect manufacturing processes such as producing molds for use in injection molding, and metal patterns which are used in sand castings. By using CNC cutting services, manufacturers can create intricate and precise molds and patterns, ensuring the production of high-quality end products.
Alternatives to CNC Cutting
Here are some alternatives to CNC cutting machines:
- Waterjet Cutting
- Plasma Cutting
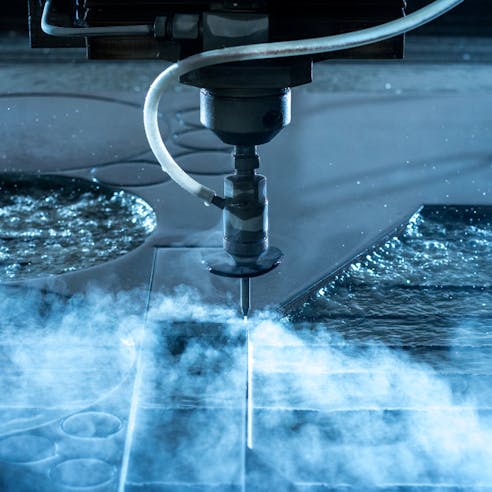
- Waterjet Cutting: This technique utilizes high-pressure streams of water containing abrasive particles which cut through various materials. It is a versatile and precise cutting method that can handle a wide range of materials, including: metals, plastics, composites, stone, and glass.
- Plasma Cutting: The process of plasma cutting uses high-temperature plasma arcs to cut through electrically conductive materials, primarily metals. It is a fast and efficient method for cutting thick metal sheets and is commonly used in industries such as: metal fabrication, automotive, and construction.
Why Choose Xometry for Custom CNC cutting Services?
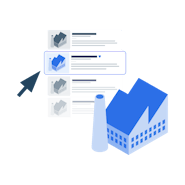
Endless Options
Choose from millions of possible combinations of materials, finishes, tolerances, markings, and certifications for your order.
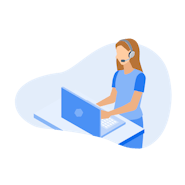
Easy to Use
Get started with our easy-to-use platform and let our experts take care of managing the project from locating the right manufacturing partner to delivery logistics.
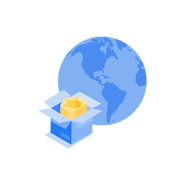
Vetted Network
We are ISO 9001:2015, ISO 13485, and AS9100D certified. Only the top shops that apply to become Suppliers make it through our qualification process.