Sheet Metal Punching Service by Xometry
High quality sheet metal punching services with a variety of material options, serving industries such as aerospace, automotive, and consumer products.
Metal punching is a simple process for making shaped holes in metal sheets or plates. The typical punch and die set includes a punch of the desired profile for the hole and a matching die for it to engage with. The punch is aligned with the die, either by an integrated guide or as part of a machine setup. The workpiece is placed between the two. An impact or pressure on the punch will then shear the material at the punch edges, driving it out of the workpiece and leaving a hole of a predetermined shape. It is the industrial-strength equivalent of a paper hole-punch.
Xometry offers excellent sheet metal punching services. Xometry CNC punching services come in a variety of material options to meet client requirements, including: mild steel, stainless steel, aluminum, and brass. We can handle one-off parts or millions of components. We serve extensively in the aerospace, automotive, and consumer products development/manufacturing sectors and beyond. Our team of experts can cater to all your sheet metal punching requirements.
About the Sheet Metal Punching Process
CNC sheet metal punching is a highly versatile and efficient method for producing precise and repeatable features in sheet metal. The general process is listed below:
- Prepare the Material: Make sure that the material is clean and flat. Secure it in place with a clamping device, vacuum table, or magnetic system.
- Select Tooling and Punch: Select the appropriate tooling and punch for your task. Your selection will depend on the material type and thickness. In many cases, CNC tool changers can swap out punches within a single program/setup. The CNC then moves the punch and die set into contact with the sheet metal and the punch descends rapidly, shearing or piercing through the material. The resulting slug (the punched-out piece) is ejected through the die.
What Is Metal Punching Used For?
Metal punching is the creation of shaped holes in metal sheets or plates using a punch and die set. It is a versatile and common method with various applications across nearly all industries. Here are some common uses of metal punching:
- Hole Creation
- Perforated Sheets
- Electrical and Electronics
- Automotive and Aerospace
- Signage and Advertising
- Furniture
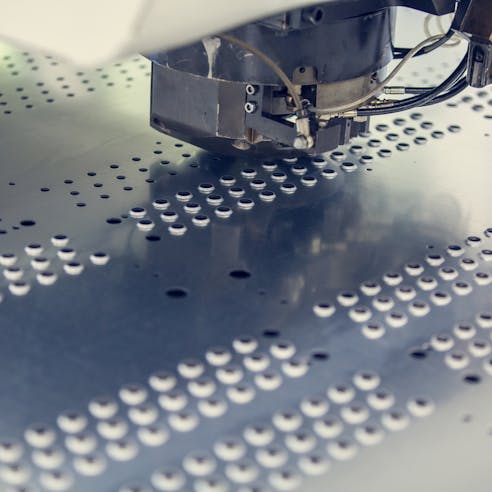
- Hole Creation: Metal punching is most used for making holes of various sizes and shapes in metal sheets or plates. These holes can be for facilitating assembly, ventilation, drainage, or allowing the passage of cables, wires, or pipes.
- Perforated Sheets: The process can be used to create perforated sheets with a pattern of regularly spaced holes. Perforations are used for decorative and functional purposes in architecture, interior design, filtration, acoustics, etc.
- Electrical and Electronics: Metal punching is commonly used in the electrical and electronics industries to create cutouts for switches, displays, and wire routing.
- Automotive and Aerospace: In the automotive and aerospace industries, holes and cutouts are regularly punched in metal components such as chassis, brackets, panels, and body parts. This reduces the parts’ weight and creates attachment points for other components.
- Signage and Advertising: Metal punching is used in signage and advertising displays. It allows for the production of durable lettering, logos, and decorative patterns.
- Furniture: Metal furniture and shelving components often have punched parts. The holes may be used for hardware attachment, adjustment features, or decorative elements.
Material Options for CNC Punching Services
The suitability of a particular material for CNC punching depends on factors such as the material's thickness and properties, plus the punching machine’s capabilities.
- Mild Steel
- Stainless Steel
- Aluminum
- Brass
- Copper
- Galvanized or Bright Zinc-Plated Steel
- Precoated Materials
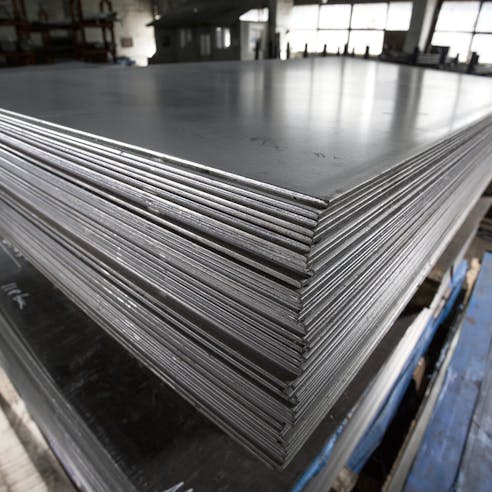
- Mild Steel: A strong and machinable and comes at a moderate price. Most manufacturing sectors find uses for mild steel.
- Stainless Steel: Stainless steel has better corrosion resistance and aesthetics than others, making it a popular choice in most manufacturing sectors. It is common in industries such as food processing, medical equipment, architecture, and marine applications.
- Aluminum: Aluminum is lightweight, corrosion-resistant, and has excellent thermal and electrical conductivity. It is widely used in aerospace, automotive, electronics, signage, and lightweight structures.
- Brass: Brass is easy to punch with appropriate tools. The process creates aesthetically appealing products, but it also has good electrical conductivity and corrosion resistance. Brass is widely used in decorative applications, electrical components, musical instruments, and plumbing fixtures.
- Copper: Copper requires specialized tooling and techniques because it’s softer than most industrial metals. It is widely employed in electrical and electronic items such as electrical connectors, heat sinks, and shielding.
- Galvanized or Bright Zinc-Plated Steel: This material punches very cleanly, even with the most basic of tooling. It is steel that has been electroplated or hot dip-coated with a layer of zinc to protect against corrosion. It is commonly used in construction, automotive components, and other outdoor items that require protection against environmental elements.
- Precoated Materials: Precoated materials such as pre-painted steel or pre-anodized aluminum take well to CNC punching. While the punched surfaces will be exposed, the main coating can be left undamaged and minimally marked.
Different Types of Metal Punches
Many patterns of hole punch tools are available off the shelf and a wide range of custom services can also manufacture punches to any required pattern. The punch styles are listed below:
- Knockout punch
- Plane Punch
- Beveled Punches
- Compound Dies
- Progressive Dies
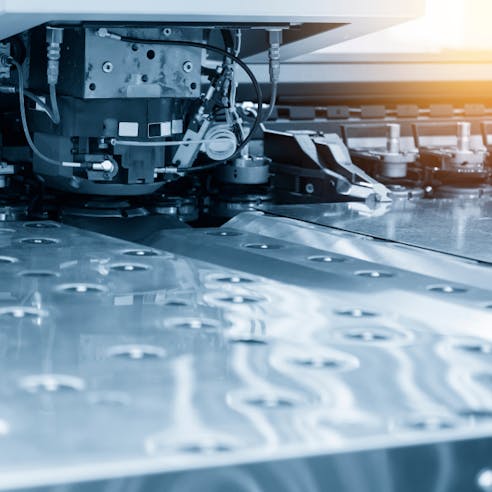
- Knockout punch: Also called chassis punches, this type generally uses a small location or pilot hole to align the punch with the die. The operational force is applied by tightening a nut onto the stud that passes through the location hole. Knockout refers to the fact that all removed material (the blank) is retained in the tool, which must be unscrewed and cleared by hand. This punch type generally uses a progressive shearing action, with a curved presentation at the hole edge to reduce the necessary operational force. It must travel further as a result, but it allows the punch to cut through heavier materials. Knockout punches can also be hydraulically operated with a powered manual or CNC press, which reduces the operational and clearance overhead.
- Plane Punch: In many CNC setups, the punch face is simply flat and square-edged. These punches rely on precise positioning of both punch and die plus a large force to shear the blank from the workpiece.
- Beveled Punches: These have a flat face that is not perpendicular to the punch’s direction of motion. This helps it shear through thicker workpieces and reduces the initial force requirement. Beveled punches risk adding distortion to the sheet material because the shearing action applies an asymmetrical force to the workpiece.
- Compound Dies: These use a single punch action over a longer range, dividing punching into distinct stages by means of a stepped tool. This enables more complexity of shape without needing excessive force. Such tools cost more and are slower to operate than others, but can increase the range and capabilities of punching machines significantly.
- Progressive Dies: These separate the punching of more complex holes into distinct stages, indexing the workpiece through a series of punch operations.
Metal Finishes for Punch Services
Xometry offers several metal finishes for punch services. These include:
- Anodizing
- Alodining
- Black Oxide Coating
- Electroless Nickel Plating
- Gold Plating
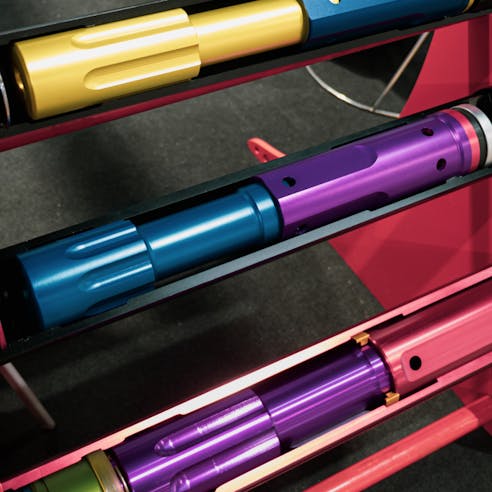
- Anodizing: Anodizing applies a tough oxide coating to aluminum through an electrolytic process. Anodization is not limited to one style of underlying texture. Plus, the oxide coating can be tailored to your preferred thickness, color (to include clear), and surface texture.
- Alodining: This process is the conversion of the surface to a chromate film that is thinner than an anodized layer and allows much greater precision.
- Black Oxide Coating: This process is applicable to ferrous metals. It is a chemical alteration of the surface to form black oxides. This coating is most commonly applied to stainless steel parts for cosmetic reasons. It also improves the corrosion resistance of medium- and high-carbon steel parts.
- Electroless Nickel Plating: This applies a chemically deposited coating of nickel onto the surface, leaving it with a matte, hard, and powdery appearance. It is common on military equipment and can be used as a pre-plating stage to force otherwise non-electroplatable components to accept electroplating.
- Gold Plating: This creates a cosmetic finish on brass and base metal materials, making cheaper materials look like gold. It is also used extensively in the electronics industry as a method for preventing oxide accumulation on surfaces, reducing PCB degradation, and improving solderability.
Why Choose Xometry for Sheet Metal Punching Services?
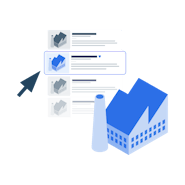
Endless Options
Choose from millions of possible combinations of materials, finishes, tolerances, markings, and certifications for your order.
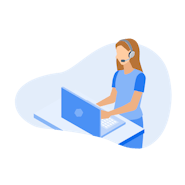
Easy to Use
Get started with our easy-to-use platform and let our experts take care of managing the project from locating the right manufacturing partner to delivery logistics.
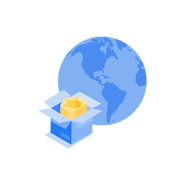
Vetted Network
We are ISO 9001:2015, ISO 13485, and AS9100D certified. Only the top shops that apply to become Suppliers make it through our qualification process.