Titanium CNC Machining
Get instant quotes on custom titanium machined parts with our online titanium machining service. Make quick turn prototypes and production parts in days with free standard shipping on all US orders. ISO 9001:2015, ISO 13485, and AS9100D certified. ITAR registered.
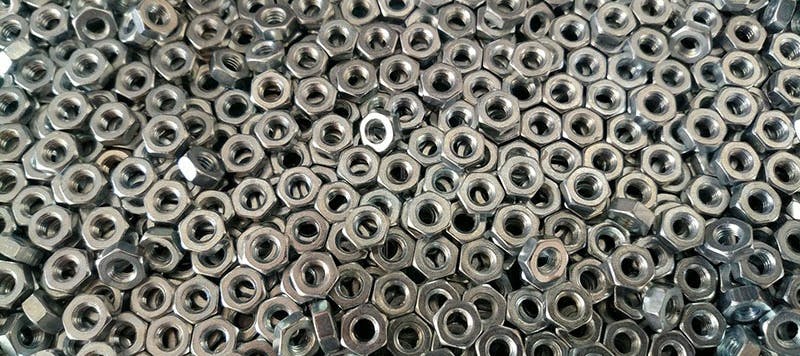
Titanium CNC Machining
Titanium (or Ti on the periodic table) is a lightweight metal with a wide range of useful properties from corrosion resistance to strength retention at extreme temperatures. You can purchase it both in pure and alloyed form. Note that even pure titanium has some (less than 1%) iron and oxygen content. More advanced alloys significantly improve the overall strength of titanium.
Titanium is an advanced material with excellent corrosion resistance, biocompatibility, and strength-to-weight characteristics. This unique range of properties makes it an ideal choice for many of the engineering challenges faced by the medical, energy, chemical processing, and aerospace industries. Select Titanium CNC machining in the Xometry Instant Quoting Engine℠.
Titanium (Grade 2)
This grade is essentially a pure (99%) form of unalloyed titanium. It has excellent corrosion resistance characteristics and is easier to machine than other titanium alloys. Grade 2 is typically the best option when aqueous corrosion resistance is desired. Desalination components and medical implants are some of its applications.
Tensile Strength, Yield (MPa) | Fatigue Strength (MPa) | Elongation at Break (%) | Hardness (Brinell) | Density (g/cm^3) |
---|---|---|---|---|
Tensile Strength, Yield (MPa) 340 | Fatigue Strength (MPa) 240 | Elongation at Break (%) 28 | Hardness (Brinell) 200 | Density (g/cm^3) 4.51 |
* Generalized values based on annealed condition. For reference only.
Titanium (Grade 5)
Titanium Grade 5 or Ti 6Al-4V is the most popular alloy of titanium. Its primary alloying elements are aluminum and vanadium. It also contains a small amount of nickel, palladium, and ruthenium that improve its corrosion resistance far above that of standard titanium. This alloy is significantly stronger than Grade 2 and retains its corrosion-resistant properties at a wide temperature range. Grade 5 is a common choice for engine components and aircraft airframes.
Tensile Strength, Yield (MPa) | Fatigue Strength (MPa) | Elongation at Break (%) | Hardness (Brinell) | Density (g/cm^3) |
---|---|---|---|---|
Tensile Strength, Yield (MPa) 880 | Fatigue Strength (MPa) 240 | Elongation at Break (%) 14 | Hardness (Brinell) 334 | Density (g/cm^3) 4.43 |
* Generalized values based on annealed condition. For reference only.
Finishes and Post-Processing Options
We offer a wide range of surface finishes applicable to titanium.
Case hardening: Titanium surfaces tend to gall when they come into sliding contact with each other. This problem can be eliminated using case hardening techniques.
Anodizing: Titanium is anodized to either improve its wear resistance (type 2 anodizing) or to color the material (type 3 anodizing). Parts made for the medical industry sometimes make use of type 3 for color-coding purposes.
As machined: If left in its as-machined state, titanium forms a protective oxide layer as soon as it’s exposed to air. This layer significantly improves its corrosion resistance. If scratched, the oxide layer will naturally reform, creating a self-healing effect.
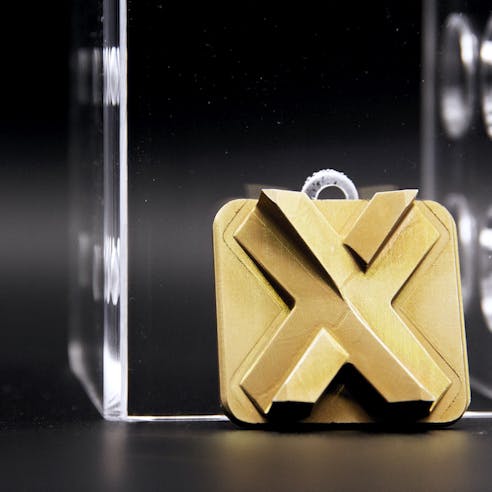
Cost-saving Design Tips
Titanium is a costly material so remember cost considerations during the design phase. Below are some tips that can reduce the expenses of working with it.
Material selection: Select the correct material for your application so that its high price doesn’t become excessive. For example, if a lot of material is machined away, Grade 2 titanium may be the better option as it is more machinable. Grade 5, on the other hand, is applicable for high strength at extreme temperatures.
Design for manufacturing: Titanium is machined as easily as high-performance steels, but it does make a few unique demands on the machinist. As such, it is critical to follow the specific DFM principles that apply to the metal. Inefficiently designed parts can slow the machining process and thus drive up costs.
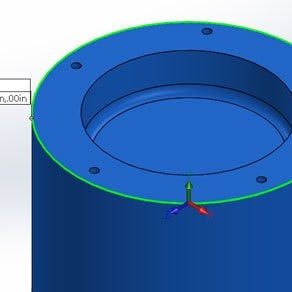