Electroplating Services by Xometry
Xometry offers the highest quality electroplating services and can assist in the production of parts with intricate and complex geometries and excellent surface finishes. Subject to availability. Xometry doesn't guarantee that we can provide this service at any given time.
Electroplating is a widely used surface finishing technique that plays an essential role in the function and performance of parts in many industries. It is a cost-effective process that enables manufacturers to blend the hardness, electrical properties, abrasion, temperature and corrosion resistance, and the appearance of a particular metal in a material that otherwise lacks the desired traits. Different electroplating methods, such as barrel plating, rack plating, and reel-to-reel plating, can be used to obtain the desired combination of properties of a product. Electroplating is a versatile process with many different uses such as: plating integrated circuit components to improve electrical conductivity, plating aerospace components such as landing gear to improve their corrosion resistance, and plating metals to have the appearance of precious metals in the jewelry industry.
Xometry offers electroplating as a value-added, turnkey service to our primary manufacturing processes, including CNC, 3D printing, injection molding, casting, sheet cutting, etc. A product can be fully customized using the Xometry Instant Quoting Engine®. Xometry does not provide secondary processing or finishing to parts supplied by a third party, with few exceptions.
About Electroplating
Electroplating is the process of coating an object in a layer of metal using electrolysis. This is used by engineers to transfer the metal coating from an anode to a cathode. This process occurs in a bath where the cathode is immersed in an electrolyte solution to facilitate the transfer of the metal ions from the anode to the cathode. The bath is typically composed of salt and the metal to be plated. A DC power source creates an electric current that drives the metal ions from the anode to the cathode. The cathode can be an electrically conductive metal or a non-conductive material such as plastic which has been coated to make its surface conductive. This conductive surface attracts the metal ions being supplied by the anode. The ions then adhere to the surface of the cathode. Once adhered, the ions turn back into atoms and form a thin layer of metal on the substrate’s surface.
Electroplating Methods
There are a variety of electroplating methods that can be used to deposit metals onto a substrate. The preferred electroplating method depends on the application and on the geometry of the part. The various electroplating methods are listed and described below:
Barrel Plating
Barrel plating is a form of electroplating used to achieve uniform plating coverage on a high volume of parts. In barrel plating, parts are placed into a barrel that is submerged in a metal plating solution consisting of a salt and the metal to be plated. While immersed in the liquid, the barrel slowly rotates as electric currents facilitate the transfer of ions from the anode to the cathode. The constant contact between parts in the barrel allows the parts to all be connected electrically. Additionally, although parts should be cleaned and descaled before plating, the rotation mechanism of the barrel plating process also helps to further clean and descale parts. However, the constant surface contact between parts may not be ideal for applications that require precise or ornamental finishes since the friction between parts can affect plating quality and create non-uniform surfaces.
Rack Plating
Rack plating is another commonly used electroplating process. In rack plating, parts are suspended from a frame and immersed in a plating solution. In contrast to barrel-plated products, rack-plated parts do not contact each other during the plating process, and each has its own continuous electrical connection to the cathode. Providing an environment with more constant current density available to each part makes it possible to electroplate complex contours and deep crevices while simultaneously avoiding potential damage due to excessive part-to-part contact. These features of the rack plating process lead to more tightly controlled plated surfaces on the parts. While rack plating cannot electroplate parts as quickly as barrel plating, it is often preferred for parts that must satisfy particular dimensional or aesthetic requirements.
Reel-to-Reel Plating
Reel-to-reel plating is an electroplating process that is used for plating raw materials before they are fabricated into complete parts through processes like stamping. In reel-to-reel plating, raw material is unwound from a reel, immersed in an electroplating solution, and then respooled onto another reel. The process repeats until the desired plating quality is achieved or as different materials are deposited. Reel-to-reel plating is particularly useful for parts in the electronics or semiconductor industries due to the small nature of the parts used.
Electroplating Materials
Electroplating is compatible with many different metal substrates, and some non-metals - plastics, for example. It can be a great method for increasing hardness or improving corrosion and wear resistance. Some of the materials that are compatible with electroplating are listed below:
- Brass: Brass is often used in electroplating processes to create corrosion-resistant, decorative finishes on parts, particularly for fasteners, plumbing valves and fittings, and home decor. Typical brass-plated substrates are steel and iron. Although brass can tarnish and lose its aesthetic appeal over time, it still adds corrosion resistance to materials typically susceptible to corrosion.
- Cadmium: Cadmium is not used in electroplating as widely as other metals like copper, gold, or silver because cadmium is toxic, and the extra safety precautions required for its safe use add cost to the plating process. However, it can improve the wear and corrosion resistance of parts. Additionally, cadmium has antibacterial properties and mitigates the growth of mold. Cadmium plating is often used for parts in the aerospace and marine industries.
- Chromium: Chromium plating is popularly used to create visually attractive parts in the form of chrome-plated surfaces. Beyond that, chromium is naturally corrosion-resistant and hard which helps to improve a material’s corrosion and abrasion resistance. However, chromium plating creates hazardous byproducts in the form of hexavalent chromium or trivalent chromium compounds that must be properly disposed of to mitigate health and environmental hazards.
- Copper: Copper electroplating is applied to a wide range of parts across different industries due to its ability to improve a part’s electrical conductivity, antibacterial properties, and corrosion resistance. However, copper oxidizes over time which can eventually lead to a dull or undesirable appearance.
- Gold: Gold is a popular metal used for electroplating due to its electrical conductivity, and aesthetic appeal. However, gold is expensive compared to other metals, which leads to a costlier electroplating process.
- Iron: Iron is seldom used for electroplating due to the material’s tendency to rust.
- Nickel: Nickel is one of the most commonly used metals for electroplating due to its ability to improve corrosion and wear resistance, as well as its aesthetic appeal. However, nickel is considered one of the more expensive electroplating materials compared to cheaper alternatives like zinc and tin.
- Silver: Silver is another metal often used in electroplating due to its high electrical conductivity and corrosion resistance. However, like copper, the appearance of silver changes over time and can tarnish in ambient environments, which leads to diminished aesthetic appeal.
- Titanium: Titanium cannot be electroplated onto other metals since it is too reactive.
- Zinc: Zinc plating is another popularly used metal in electroplating due to its relatively low cost and good corrosion protection it offers materials normally susceptible to corrosion like steel or iron. However, zinc electroplated surfaces can corrode in high humidity or when exposed to saltwater, and fumes from the electroplating solution tanks during processing can be toxic if inhaled.
Electroplating Benefits
Electroplating offers many benefits beyond a beautiful surface. These benefits are listed and described below:
Temperature Resistance
Metals commonly used for electroplated coatings, such as gold and nickel alloys, can withstand extremely high temperatures due to their high melting points. Depending on the substrate material and the coated metal, electroplating can effectively improve the substrate’s ability to resist complications due to excessive heat. Consequently, the plated parts’ lifespans can be increased.
Corrosion Resistance
Another advantage of electroplating is the process’s ability to improve a material’s corrosion resistance by creating a thin metal layer that acts as a protective barrier against environmental conditions. Parts that have been electroplated have a longer life in harsh conditions and consequently require less frequent maintenance and replacement.
Cost Savings
Electroplating enables manufacturers to use a cheaper material with less corrosion resistance, electrical conductivity, or wear resistance, and apply a thin coating of a more expensive that provides the needed properties. For example, plating gold only on the portions of electrical contact that require it rather than the entire part is much cheaper. Additionally, depending on the type of electroplating, electroplating can be great for plating large volumes of parts simultaneously. This enables manufacturers to save both time and money.
Meets Tight Dimensional Tolerances
The electroplating process deposits a thin layer of metal onto the surface of a metal part. This layer is typically 0.0001” to 0.020” thick. Control of the process through controlling current density at the part means that a tight thickness tolerance, typically +0.0001” can be maintained. Producing electroplated parts with accurate and repeatable dimensions is particularly important in the electronics industry, which must produce good electrical connections in very small parts.
Maintains Electrical Conductivity
Metals are inherently electrically conductive due to the free electrons present in their atoms. Some metals are more electrically conductive than others. However, electroplating can be used to increase the conductivity of a metal to improve its performance in particular applications like integrated circuit components in cell phones, computers, and other devices. Gold and silver, two of the best electrical conductors, are often plated onto electrical connectors in small amounts despite their high cost because they improve conductivity so much.
Provides a Unique Finish
A key advantage of electroplating is the process’s ability to provide unique, lustrous, and aesthetically pleasing surfaces on metal parts. Because of this, electroplating is often used in art pieces such as sculptures, architectural trim, and jewelry. In the creation of jewelry, in particular, electroplating can be used to make metals such as nickel, zinc, or copper appear like pure gold or other precious metals. Therefore, electroplating is a cost-effective method for making products more appealing.
In need of electroplating services?
Electroplating Limitations
Electroplating is not without its disadvantages and limitations. Some of those limitations are listed and described below:
Time-Consuming
Electroplating can be a time-consuming process that can be a process bottleneck for manufacturers, leading to long lead times for products. The desired coating thickness has a large impact on the electroplating process time. Additionally, if multiple layers of electroplating are to be added to the substrate, the process can take even longer.
Cost
Electroplating can be an expensive process, from the machinery needed to complete the process to the time it takes to coat parts. Additionally, the metals to be plated can also be expensive depending on the type of metal. Moreover, larger parts may require larger electroplating setups, while parts with complex geometry may require a more tightly controlled electroplating process or multiple passes — which can further increase the process cost. Still, buying plated products is often cheaper than buying products made entirely of plated material.
Environmental Concerns
The electroplating process often involves the use of hazardous chemicals such as various cyanide solutions or hexavalent chromium. Additionally, plating heavy metals produces wastewater that often contains heavy metals. Manufacturers must properly dispose of byproducts that result from the process and effectively treat wastewater to reduce their environmental impact. Moreover, the process consumes a significant amount of electrical energy which can have adverse environmental impacts if derived from non-renewable resources.
Applications and Industries That Use Electroplating
Many industries utilize electroplating to improve material performance or to add an aesthetic appeal to parts. Some of the applications and industries in which electroplating is used are listed and described below:
- Aerospace
- Art and Home Decor
- Automotive
- Jewelry
- Medical and Dental
- Power Generation
- Prototyping
- RF and Microwave Products

Aerospace
Electroplating is often used in the aerospace industry to improve the corrosion and wear resistance of critical components such as landing gear components (including connecting rods, actuators, and struts), and engine parts like turbine blades and fasteners. Titanium and aluminum are the two materials that are most often electroplated in the aerospace industry.
Art and Home Decor
Electroplating is popular for art and home decor pieces due to the process’s ability to coat lustrous and decorative metals onto metals with otherwise dull and insignificant surfaces. From home decor pieces and sculptures to architectural trim pieces, metals like nickel, gold, silver, and copper can be plated onto materials like iron or steel to create beautiful works of art.
Automotive
The automotive industry is one of many industries that benefit greatly from electroplating due to the improved aesthetic appeal and corrosion and wear resistance added to parts. Chromium, zinc, and gold are three materials commonly used for automotive electroplating for parts such as: electro-galvanized zinc parts like exterior panels, fenders, chromium-plated wheels, and under-the-hood components like steering columns.
Jewelry
Jewelry is an industry that commonly employs electroplating processes to create visually appealing products. Jewelry made from pure precious metals like gold, silver, and platinum can be expensive. However, with electroplating, manufacturers can use cheaper metals such as steel, and nickel as a substrate, and then deposit precious metals only onto the surface. This can help material costs and costs to the consumers while retaining the attractive appearance of expensive jewelry.
Medical and Dental
Electroplating is used in the medical and dental industry to coat parts such as surgical and dental instruments. Electroplating helps improve the hardness and corrosion resistance of these parts. Nickel and chromium are two metals often used for electroplating medical and dental parts.
Power Generation
Components in the power generation industry, such as turbines, heat exchangers, and shafts, experience tremendous amounts of friction, abrasion, heat, and stress when in use. Electroplating of power generation parts like power transmission shafts and turbines is a great solution to mitigate the effects of these phenomena which result in parts with longer life, but also parts with more heat, wear, and corrosion resistance.
Prototyping
Because electroplating can be used on both metals and plastics, electroplating can be used on 3D-printed parts without having to go through the costly and long process of producing metal prototypes. This enables manufacturers to save both cost and time and allows them to use the electroplating process to test the corrosion and wear resistance of different types of coatings.
RF and Microwave Products
Electroplating is great for RF (radio frequency) and microwave products such as: antennas, radios, navigation beacons, and more. Gold and silver all can be used to improve the electrical conductivity of parts when electroplated.
Alternatives to Electroplating
If electroplating is not a viable process because of an application’s geometry or tolerance requirements, one of Xometry’s alternate process services may be appropriate. Some of the alternatives to electroplating are listed and described below:
- Electroless Nickel Plating
- Physical Vapor Deposition (PVD)
- Anodizing
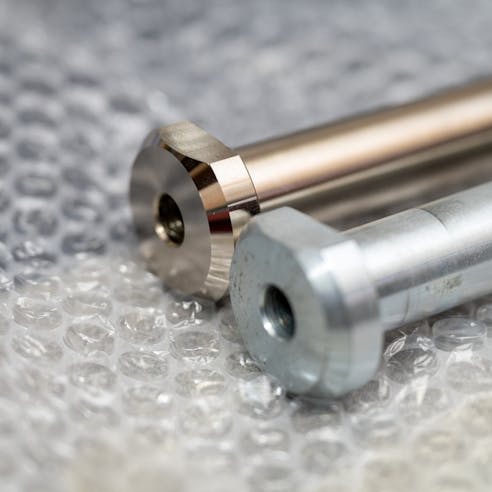
Electroless Nickel Plating
Electroless nickel plating is similar to electroplating but is used to coat nickel alloys onto parts by chemical reduction without the need for an electric current. Electroless nickel plating can be superior to nickel electroplating due to its improved wear and corrosion resistance. This is because electroless nickel-plated surfaces are amorphous and have little to no grain or phase boundaries where corrosion can initiate. In addition, electroless nickel plating adds ductility to parts which is not possible with electroplating. However, electroless nickel plating is a slower process, and thus more expensive, than electroplating.
Physical Vapor Deposition (PVD)
Physical vapor deposition is a coating process where parts are placed in a vacuum chamber as a coating material is heated, turned into a vapor or plasma, and condensed on the workpiece’s surface. There are two PVD methods: evaporation and sputter. In evaporation PVD, the coating material is heated until it evaporates or sublimates into a vapor. The atoms of the coating material then precipitate and condense everywhere within the vacuum chamber. In sputter PVD, the coating material is turned into plasma with extreme heat that then forms a cloud to coat everything in the vacuum chamber. Because both processes only coat exposed surfaces, rotating the workpiece during the PVD process is essential to ensuring the entire part is coated. PVD coatings are thinner than electroplated coatings since coating occurs at an atomic level but takes longer to complete due to the time needed to produce the vacuum and heat the coating material. Moreover, the machinery for physical vapor deposition is also more expensive.
Anodizing
Anodizing is a process similar to electroplating in that it uses electricity and a chemical reaction to coat parts. In anodizing, an oxide surface layer is coated onto a part to improve the material’s wear and corrosion resistance, but also to add a more attractive finish. The process is most commonly used for aluminum but can be used for other metals like titanium and magnesium. Compared to electroplating, coatings made by anodizing are harder and more durable.
Why Choose Xometry for Electroplating Services?
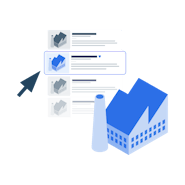
Endless Options
Choose from millions of possible combinations of materials, finishes, tolerances, markings, and certifications for your order.
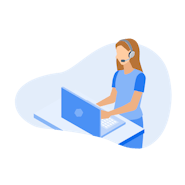
Easy to Use
Get started with our easy-to-use platform and let our experts take care of managing the project from locating the right manufacturing partner to delivery logistics.
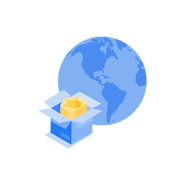
Vetted Network
We are ISO 9001:2015, ISO 13485, and AS9100D certified. Only the top shops that apply to become Suppliers make it through our qualification process.