High-Volume Injection Molding Services
High-volume Injection Molded Parts.
High-volume injection molding is a specialized manufacturing process that is of key importance in mass-producing plastic components. The process is straightforward, typically involving just two steps: obtaining the mold and using it to create the parts. It efficiently produces a large number of identical parts in a short period of time. The process is highly systematic, which reduces cycle times and ensures consistent output. Moreover, it is cost-effective for large-scale manufacturing projects due to economies of scale, as the cost per part decreases with increasing volume. The process supports a wide range of plastic materials, offering flexibility in material selection.
At Xometry, we prioritize quality control throughout our high-volume injection molding process, ensuring that each plastic component meets the highest standards of precision and reliability. With our dedication to continuous improvement, we are well-equipped to meet the demands of large-scale manufacturing projects efficiently and effectively.
High Volume Injection Molding Process
Our high-volume injection molding process is a comprehensive and efficient method for producing large quantities of plastic components while maintaining strict quality control. The process involves several key steps. First, our team of experts works closely with clients to understand their design specifications, material preferences, and production goals. Based on this assessment, we proceed with the design phase. Next, our skilled tooling engineers and technicians use CAD models to create high-quality injection molds tailored to the exact specifications of the components. A comprehensive validation process is conducted to ensure that the molds and equipment are functioning optimally. State-of-the-art injection molding machines and automated production lines are utilized to produce large quantities of plastic components with exceptional efficiency and accuracy. Robust quality control measures are implemented at every stage, from incoming raw materials inspection to final product inspection. Finally, data is continuously collected and analyzed throughout the production cycle.
High-Volume Injection Molding Materials and Technologies
At Xometry, our high-volume production injection molding services cater to a wide variety of materials including: thermoplastics such as polyethylene (PE), polypropylene (PP), polystyrene (PS), and polyvinyl chloride (PVC), as well as thermosets including epoxy, phenolics, and melamine.
Precision molds are crucial for obtaining high-quality, consistent series production injection-molded parts. Utilizing advanced computer-aided design (CAD) and computer-aided manufacturing (CAM) technologies, our molds are tailored precisely to the requirements of each component. At Xometry, automation plays a vital role in optimizing our high-volume injection molding process. Automation streamlines production increases efficiency, and reduces the need for manual intervention, leading to consistent and reliable product output.
Advantages of High Volume Injection Molding
High-volume injection molding offers several key advantages, which are listed below:
- Speed
- Consistency
- Scalability
- Low Labor Costs
- Cost Savings
- High-Precision Dimensional Tolerances
- Low Unit Costs and Cycles Times
- Automated Production
- Minimal Post-Production Work
- Versatile Material Options
- Flexibility in Design
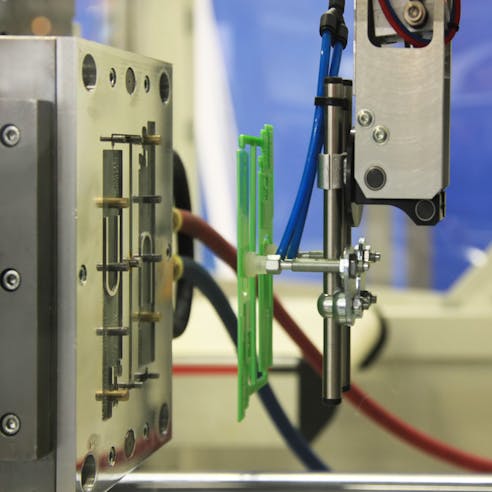
Speed
The automated nature of high-volume injection molding, coupled with advanced machinery and precision molds, allows for the rapid production of plastic components. The shortened production cycles result in cost savings and can enable businesses to meet tight deadlines and respond quickly to market demands.
Consistency
High-volume injection is known to be a very precise manufacturing process. The molding ensures uniformity in the dimensions, appearance, and properties of the molded parts. However, achieving consistency in the quality of molded parts is a multifaceted process that relies on several factors, including: well-maintained equipment, optimized processes, and rigorous quality control measures. While high-volume production can enhance the speed and uniformity of production, it doesn't guarantee quality on its own.
Scalability
High-volume injection molding's scalability stems from its ability to efficiently adapt to demand fluctuations. It is achieved through factors like multi-cavity molds that produce multiple parts per cycle. It ensures consistent quality and dimensions, vital for maintaining product integrity. Swift cycle times, modular machine design enabling easy adjustments, and automated processes with minimal labor intervention contribute to its agility in scaling.
Low Labor Costs
Automation plays a significant role in high-volume injection molding. Once the molds are set up and the process parameters are established, the machines can operate with minimal human intervention. This not only increases production efficiency but also lowers labor costs.
Cost Savings
High-volume injection molding leads to substantial cost savings when compared to various alternative manufacturing approaches, such as traditional CNC machining. This cost-effectiveness is attributed to several factors, including: efficient utilization of materials, a combination of faster cycle times and reduced labor costs, and consistent quality of the molded parts reduces the likelihood of defects.
High-Precision Dimensional Tolerances
High-volume injection molding guarantees exceptional precision and tight tolerances in molded parts. For instance, in the aerospace sector, the production of intricate turbine components demands precise tolerances to ensure optimal aerodynamics and reliable engine operation.
Low Unit Costs and Cycles Times
The combination of faster cycle times, high production rates, and reduced labor costs leads to significant cost savings per unit. Manufacturers can achieve economies of scale, lowering the cost of production for each part. Enhancing cycle times involves strategies like optimizing mold design, fine-tuning processing parameters, and advanced cooling systems. Evaluating cooling and setup times increases productivity while decreasing energy consumption.
Automated Production
Automation plays a central role in high-volume injection molding. Modern machines, equipped with advanced robotics and real-time monitoring, streamline the production process, enhancing efficiency, and minimizing errors.
Minimal Post-Production Work
The precision and consistency of the injection molding process often result in minimal requirements for post-molding finishing work. The molded parts typically meet the required specifications directly from the mold. However, in some cases, it might still be necessary to do some minimal finishing. The need for additional finishing steps depends on the intended purpose and requirements of the part. These finishing touches should be taken into account when calculating the overall part cost.
Versatile Material Options
High-volume injection molding supports a wide range of thermosetting and thermoplastic materials. It allows manufacturers to choose the most suitable material for the specific application.
Flexibility in Design
Injection molding offers design flexibility, allowing for the production of complex geometries and intricate details in the molded parts. This design freedom opens up possibilities for innovative and functional product designs.For instance, in the automotive industry, injection molding allows the production of intricately designed interior components, such as dashboard panels with precisely integrated air vents and multimedia controls.
Industries Using High-Volume Injection Molding
At Xometry, we offer top-notch plastic injection molding services to a diverse range of industries. Some of the key industries that benefit from high-volume injection molding include:
- Automotive
- Consumer Electronics
- Medical Devices
- Aerospace
- Packaging
- Construction
- Agriculture
- Consumer Goods
- Electrical and Electronics
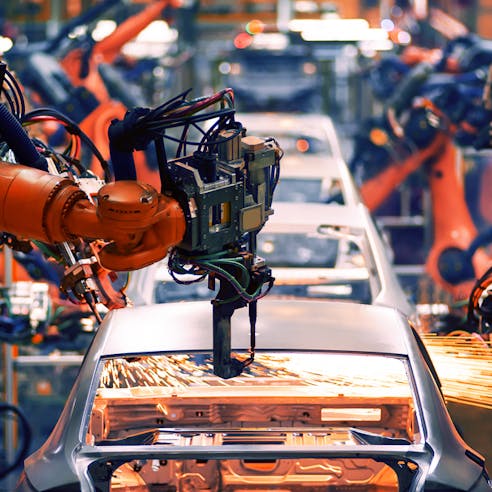
Automotive
The automotive industry relies on high-volume injection molding to manufacture a wide range of plastic components, including interior and exterior trim parts and complex engine components. Injection molding offers the precision, consistency, and cost-effectiveness required for large-scale production in the automotive sector.
Consumer Electronics
High-volume injection molding enables the mass production of casings, bezels, buttons, and other plastic parts used in smartphones, tablets, laptops, gaming consoles, and other electronic devices. The ability to produce these components quickly and with high precision meets the demands of the fast-paced consumer electronics market.
Medical Devices
In the medical industry, high-volume injection molding is invaluable for manufacturing medical device components and disposable items. This includes syringes, IV components, and diagnostic equipment housings, where accurate and consistent production is critical for patient care.
Aerospace
High-volume injection molding is utilized in the aerospace sector for producing lightweight, high-strength components for aircraft. These include interior components, cabin elements, ventilation systems, and specialized parts requiring tight tolerances and excellent performance under extreme conditions.
Packaging
The packaging industry benefits from high-volume injection molding to produce a wide range of plastic packaging solutions, such as bottles, containers, caps, and closures. Injection molding enables the manufacturing of packaging items in large quantities, meeting the demands (high volume at a low price) of the food, beverage, pharmaceutical, and consumer goods sectors.
Construction
High volume injection molding produces various components and building elements where stability and durability are required. These include small accessories, fasteners, and tools like measuring devices and protective gear components. While its use in construction might not be as widespread as in other sectors, its ability to produce precise, durable components offers efficiency and innovation potential to the construction field.
Agriculture
High volume injection molding offers reinforced plastic options with advantageous characteristics such as: UV resistance, impact resistance, humidity resistance, and corrosion resistance among others. Examples of parts made with high-injection molding are: animal feed and water troughs, food storage, plastic containers, water tanks, and cleaning equipment.
Consumer Goods
High-volume injection molding is also used in the production of various consumer goods, including toys, kitchenware (e.g., Tupperware) and appliances, household items, garden furniture, and pet products. The process's efficiency and ability to create intricate designs and shapes make it an attractive choice for manufacturers in this sector.
Electrical and Electronics
Apart from consumer electronics, high-volume injection molding is utilized in the electrical and electronics industry for manufacturing connectors, switches, sockets, and other plastic components required for electrical equipment and appliances.
Alternatives to High-Volume Injection Molding Services
In cases where high-volume injection molding services may not be the most suitable option for a particular project, clients can consider several alternative manufacturing processes to meet their specific needs. Some of these alternatives include:
- 3D Printing
- CNC Machining
- Blow Molding
- Thermoforming
- Compression Molding
- Rotational Molding
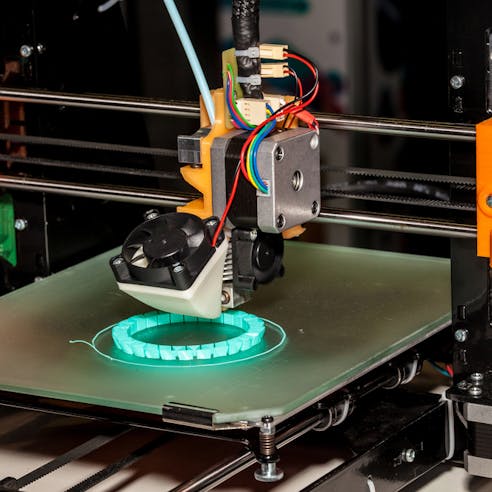
- 3D Printing: 3D printing, also known as additive manufacturing, is a versatile technology that creates objects by building up material layer by layer from a digital model. It is particularly beneficial for rapid prototyping, low-volume production, and the production of complex geometries that may be challenging to achieve with traditional manufacturing methods. While 3D printing is not as cost-effective for mass production as injection molding, it offers great design flexibility and allows for quick iterations and customization.
- CNC Machining: Computer Numerical Control (CNC) machining is a subtractive manufacturing process where the material is removed from a block or sheet to create the desired shape. CNC machining is suitable for producing precise, high-quality parts from various materials, including metals, plastics, and composites. It is a viable alternative for lower-volume production and for parts that require tight tolerances and intricate features.
- Blow Molding: Blow molding is a process used to create hollow plastic parts, such as bottles and containers. It involves melting plastic material and inflating it to form the desired shape within a mold. Blow molding is well-suited for large-volume production of hollow plastic parts with consistent wall thickness, making it an excellent option for packaging and container manufacturing.
- Thermoforming: Thermoforming, or vacuum forming, is a manufacturing process where a plastic sheet is transformed using heat, vacuum, and pressure. Thermoforming is commonly used to produce large, shallow parts with simple shapes, such as trays, cups, and automotive interior components. It is a cost-effective alternative to injection molding for certain applications.
- Compression Molding: Compression molding is a technique where a pre-measured amount of plastic material is placed in a heated mold and compressed under high pressure until it takes the shape of the mold. This method is often used for producing parts with reinforced materials or with intricate designs and relatively low to medium production volumes.
- Rotational Molding: Rotational molding, also called rotomolding, is a method used to create hollow plastic parts. It involves rotating a mold in an oven, causing the plastic material to coat the inside of the mold evenly. Rotational molding is commonly used for large, durable items such as playground equipment, storage tanks, and certain automotive components.
Why Choose Xometry for High-Volume Injection Molding?
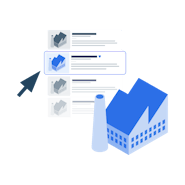
Endless Options
Choose from millions of possible combinations of materials, finishes, tolerances, markings, and certifications for your order.
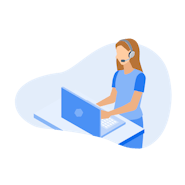
Easy to Use
Get started with our easy-to-use platform and let our experts take care of managing the project from locating the right manufacturing partner to delivery logistics.
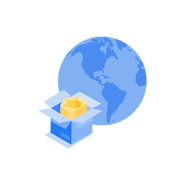
Vetted Network
We are ISO 9001:2015, ISO 13485, and AS9100D certified. Only the top shops that apply to become Suppliers make it through our qualification process.