Nylon Injection Molding Service
Get custom plastic molded prototypes and production parts in as few as 10 business days. We provide expert engineering reviews and $500 off your first mold. Dozens of materials and finishes are available.
Nylon plastic injection molding is a process used to create parts requiring strength, smooth textures, and stiffness. It does this through a combination of the properties that come from the manufacturing process and the plastic itself. This process also replaces low-strength metals for manufacturing. These properties, among others, make nylon injection molding useful for applications including car tires and vehicle engine components.
Nylon plastic, also known as Polyamide (PA), is an engineering-grade thermoplastic used in injection molding applications due to its balanced properties. Some of those applications have found uses in industries like consumer goods, automotive, electronics, and more.
Even though there are different types of polyamides, all of them are characterized by high temperature, chemical, and electrical resistances due to their crystalline structure. In terms of mechanical properties, this material is durable, versatile, and exhibits high tensile strength and fatigue resistance. It also possesses excellent abrasion and friction behavior (while not being the most slippery plastic available on the market, this property shouldn’t be overlooked). This material can also be easily flame retarded.
We’re going to take a deep dive into how Xometry deals with this process, its characteristics, and what you can expect for the end part. For more detailed information on Xometry’s lead times, machine sizes, and more, check out our main page describing our injection molding services.
Nylon Injection Molding Process
The nylon injection molding process follows the many of the same practices as the usual plastic molding technique through the following steps:
1. Drying
Nylon requires drying, often vacuum drying, before it can be melted and molded. While for most plastics this is recommended, it is required for this material because excess water will degrade the plastic when it’s exposed to heat.
2. Clamping
In clamping, the two pieces of the mold are clamped together before the injection itself takes place. Both sides are put into a clamping unit, which is a machine that pushes them together.
3. Injection
Once the clamping step is complete, the injection itself begins. Nylon (also known as PA) pellets are fed into a hopper. The plastic is then melted down to liquid form and pumped into the mold. Temperature is kept constant throughout this step.
4. Dwelling
Following the injection, we enter the dwelling phase where the mold is filled with the liquid. Pressure is applied so that the liquid fills all the mold cavities, ensuring the structural integrity of the part.
5. Cooling
Next comes the cooling stage where the plastic solidifies inside the mold. This can take from seconds to minutes depending on part size.
6. Ejection
The mold is opened and the part is ejected out of the mold, revealing the final nylon plastic product.
Physical Properties of Nylon Materials
Nylon, as an engineering-grade plastic, features stronger tensile strength, high temperature resistance, and more friction resistance than more standard, non engineering plastics.
Tensile Strength
Nylon already has basic high tensile strength, as well as durability, making it suitable for applications that require the material to survive impact. In some applications, nylon plastic is filled with 10-40% glass fibers to increase tensile strength further. While strength is increased in such situations, the glass fibers change the potential defects that can occur. No glass fill means that the plastic will bend and yield before a potential break. With the addition of fibers (especially in a higher percentage), the break (or failure) comes earlier, with minimal bending. However, for reinforced nylon the resultant tensile strength can be up to 70% higher than normal nylon plastic.
High Melting Temperature
Nylon’s high melting point comes from its chemical composition. This property makes nylon plastic an attractive alternative to metal components suitable for high-temperature environments or applications (in a related vein, nylon’s high temperature resistance makes it good for dealing with friction). Its resistance to high temperatures is what makes it useful for automotive engine parts. While the heat resistance will require a higher mold temperature, this should not translate to increased cost in the molding process for those ordering parts.
Nylon will also melt to a liquid and not burn, making it an easily recyclable option.
Low Friction
The same chemical composition allows nylon injection molding parts to resist heating up easily. This translates to low coefficients of friction, a property high beneficial in parts like slides, gears, plastic bearings, and bushings. This property also confers a certain wear resistance to parts, though there are other plastics that feature stronger wear resistance.
As mentioned above, there are multiple types of nylons, named by the number of units in the chain for each type. The length of the molecular chain determines how exaggerated the plastic’s properties are. Xometry specializes in processes involving PA 6 and PA 66, the properties of which are quite similar though not identical.
PA 6 (Polyamide 6 or Nylon 6)
PA 6 is popular for its cost-effectiveness. Some of its key properties include:
- Easy processing
- Decent wear and abrasion resistance
- Fuel and oil resistance
- Electrical insulation capabilities
- Low viscosity, which translates into a smooth surface appearance
- Absorbs moisture easily (which leads it to grow and shrink)
- Increased rigidity
- Good stability under heat
- Chemical resistance
PA 66 (Polyamide 66, Nylon 66)
PA 66 exhibits similar traits to its cousin PA 6. However, it features less moisture absorption as well as better wear and heat resistance. Its other properties include:
- High strength and stiffness
- Good heat resistance
- Chemical resistance, especially to hydrocarbons
- High lubricity
- Poor chemical resistance to strong acids and bases
Besides these, Xometry also offers polyphthalamide (PPA) injection molding. PPA is a subset of nylon plastics that exhibits a higher melting point and lower moisture absorption.
PPA is preferred in applications related to the automotive industry, as well as general industrial uses. It’s an especially attractive option in applications related to fuel and fluid manifolds, as well as headlight housings. Other advantages include:
- Lightweight
- Increased part life span
- High-temperature resistance
- Excellent cost-performance ratio
- Very good impact strength
- Can resist infrared soldering environments
Types of Injection Molded Nylon Parts
The physical properties mentioned above are what make nylon such a versatile option with applications in industries from the automotive to aerospace sectors.
- Automotive applications include pump parts, under-hood parts, gears, and sprockets
- Medical equipment including MRI machine parts
- Electrical components, such as enclosures and battery casings
- Aerospace products including fan blades
- General industrial use products, such as spools, screws, manifolds, fasteners, bearings and bushings
- Consumer products like food packaging and cookware
Nylon Injection Molding Additives
Some of the most popular additives used in nylon injection molding include glass fiber, flame retardant, and UV resistant additives.
- Glass fiber is the most common additive for nylon. Glass adds rigidity and durability, as well as high temperature resistance.
- UV resistant additives in the form of blockers, absorbers, and stabilizers enable nylon to be used in outdoor applications in sunlight without the plastic breaking down.
- Flame retardant additives are also commonly used to add safety and to enhance nylon’s heat-resistant capabilities.
Nylon Plastic Injection Molding with Xometry
Some of the advantages Xometry’s clients can expect when choosing nylon injection molding overlap with our general plastic injection molding services, such as:
- Sample Parts : Once the ordered mold is created, Xometry delivers 10 part samples (T1) for inspection and approval
- Precision: Xometry specializes in fulfilling tight tolerance requirements
- High scalability: We build molds to fit your needs whether it’s for a single low-volume run, or for millions of units
- First mold discount: First-time clients will receive a $500 discount on their first mold ordered from Xometry
- A range of finishing options: You can choose from a range of finishes on your products ranging from high gloss to matte to texturing.
Nylon plastic injection molding is a highly sought-after process due to the benefits it instills onto the underlying parts. PA (nylon) exhibits properties comparable to metals in some situations, which makes it a convenient and cheap alternative to products requiring high strength, durability, and outstanding chemical and thermal properties.
Xometry offers a large array of customization options, some available with just one click through our Instant Quote engine, which requires only a 3D CAD file in order to provide you with an initial estimation and overview of your order. Accepted CAD formats include .STEP, .STP, .SLDPRT, .STL, .IPT, .3DXML, .PRT and .SAT.
Why Choose Xometry For Nylon Injection Molding?
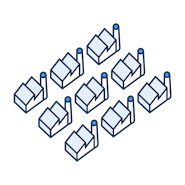
Endless Options
Choose from millions of possible combinations of materials, finishes, tolerances, markings, and certifications for your order.
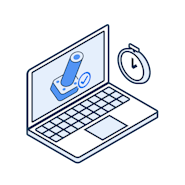
Easy to Use
Get your parts delivered right to your door without the hassle of sourcing, project management, logistics, or shipping.
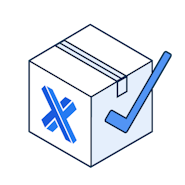
Vetted Network
We are ISO 9001:2015, ISO 13485, and AS9100D certified. Only the top shops that apply to become Suppliers make it through our qualification process.
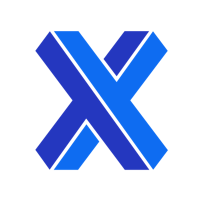