Laser and Sheet Cutting Services
Instant quotes for laser cutting or waterjet cut parts | No minimums | Get parts in days | Free standard shipping on U.S. and international orders | International prototype pricing includes tariffs | ISO 9001:2015, ISO 13485, IATF 16949:2016, AS9100D certified. ITAR registered.
What is Sheet Cutting?
Sheet cutting is a manufacturing process that involves slicing flat stock material along a defined profile to create a specific shape. This is typically done using a high-powered CNC laser or waterjet. From one-off batches to mass production, custom designs can be cut in various materials, including plastics, elastomers, composites, metals, and more. Sheet cutting is also typical for blank preparation in other manufacturing processes like sheet metal fabrication or metal stamping.
From clear acrylic panels to thick tool steel, Xometry's manufacturing marketplace offers a one-stop-shop solution for any project with instant quotes, tight tolerance capabilities, and a wide selection of materials, including:
- Metals
- Plastics
- Wood
- Composites
- Foams
- Rubber & Gaskets
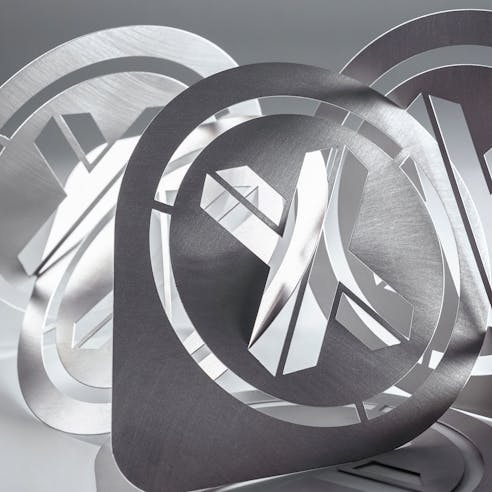
Sheet Services Available at Xometry
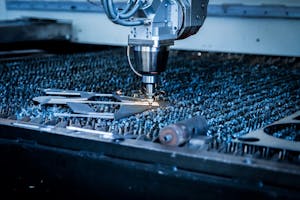
Custom Online Laser Cutting Service
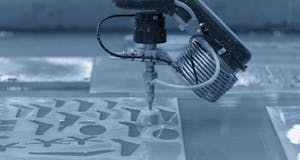
Online Waterjet Cutting Service
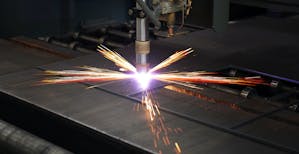
Plasma Cutting Service
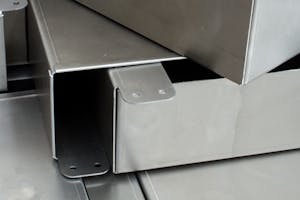
Sheet Metal Fabrication Services
Xometry Sheet Cutting Standards and Tolerances
Standard | Description |
---|---|
Standard Blank Size | Description Xometry has access to platforms up to 10’ x 20’ for laser cutting and waterjet cutting. However, many sheet stock sizes commonly cap out at 48” x 96” (4’ x 8’) or smaller. |
Standard Standard Lead Time | Description 3 business days |
Standard Sheet Thickness | Description 0.020" up to beyond 1.00" depending on materials. Thinner or thicker stock may be possible through manual review. |
Standard Tight Tolerances | Description We can automatically quote sheet cutting tolerances as tight as +/- 0.005". Tolerances tighter than this are available after manual review. |
Standard General Tolerances | Description For full details on Xometry's general tolerances and standards for our sheet cutting service, please consult our manufacturing standards. |
This table contains general information concerning Xometry’s sheet cutting services. Learn more about our official sheet cutting manufacturing standards.
How Xometry Sheet Cutting Works
Xometry's sheet cutting services utilize the top laser cutting and waterjet suppliers in the US and worldwide. Our fabricators convert CAD and drawing data into machine code, which guides a laser cutter, waterjet, or plasma cutting machine to cut the sheet material precisely. If any assembly or post-processing is required, our manufacturers will provide turnkey finishing to the part.
The efficiency and high precision of these CNC-controlled cutting tools, coupled with Xometry’s variety of materials, range of suppliers, and post-processing options, means you can get parts for any application. We regularly support industries such as aerospace, defense, automotive, energy, industrial, medical, dental, art, robotics, and consumer products.
The price you see is the price you’ll pay. When ordering prototypes—originals or models of parts intended exclusively for non-commercial purposes—the price shown at checkout includes tariffs for international orders. Shipping is also included, as long as your package is standard-size. Freight or oversized packages may require additional shipping charges.
How are Laser Cutting and Waterjet Cutting Different?
Laser cutting is a common method for creating two-dimensional profile cuts using concentrated heat. It produces a narrow kerf, typically under 0.010". In contrast, waterjet cutting uses high-pressure water to cut through materials without heat, making it ideal for thicker metals and heat-sensitive materials.
Waterjets have a wider kerf (0.040”–0.050”) but maintain the same general tolerance as lasers at ±0.010". They excel at cutting soft materials like foams, gaskets, and certain plastics that can release hazardous fumes when exposed to heat. Lasers, however, are faster and well-suited for engraving, part marking, and cutting thin metals and plastics efficiently.
Xometry works with a diverse range of suppliers offering laser and waterjet cutting, ensuring the right supplier is automatically matched to each job.
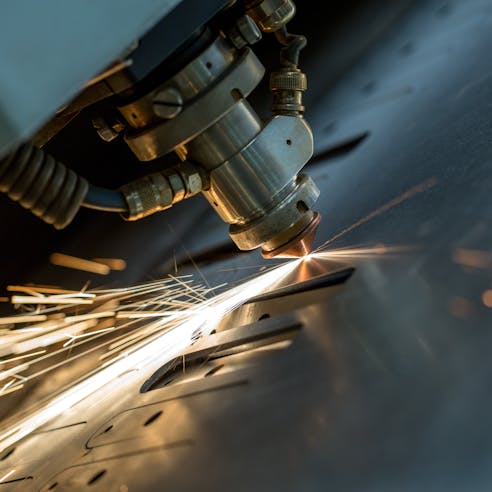
Xometry's Powerful DXF Quoting Tools
The Xometry Instant Quoting Engine is equipped with various features to ensure your sheet cutting quotes are quickly generated, straightforward, and unbeatable. In addition to 3D CAD, one of the most commonly used formats for sheet cut parts is 2D DXF. We made sure to include extensive features and support for the format. Below are a few of the key elements we've incorporated to offer you the most optimal DXF quoting experience for your flat-cut parts:
- Automatic DXF File Repair -- Common issues found in DXF files are automatically fixed when detected.
- 2D DXF File Viewer -- Our built-in vector based DXF viewer makes it quick and easy to review your uploaded designs.
- Simple Material Selections -- Only see the sheet thicknesses applicable to your chosen material through easy to use drop-down menus.
- Nested DXF File Support -- Upload a single pre-nested DXF file containing multiple components to consolidate your line items and receive discounted family pricing.
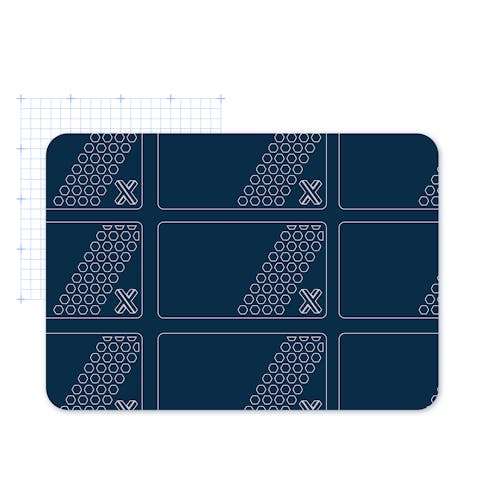
Need Tips for DXF Files?
Learn more about best practices and tips for preparing your DXF files for sheet cutting.
Sheet Cutting Materials
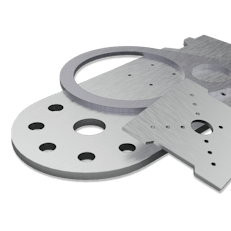
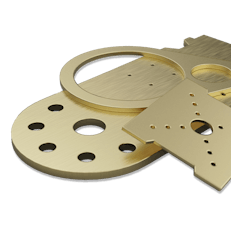
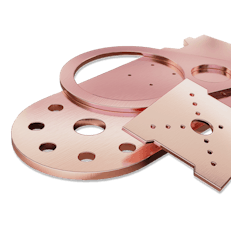
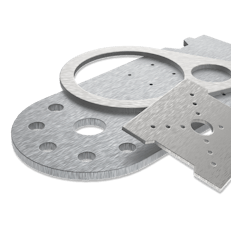
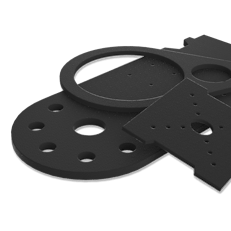

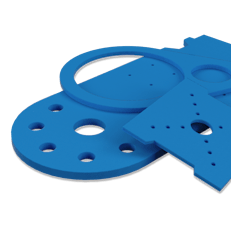
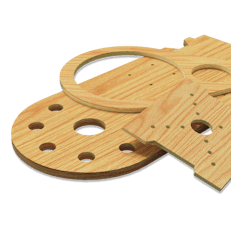
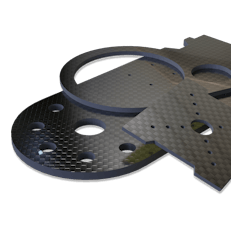
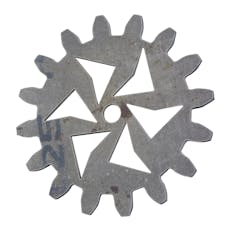
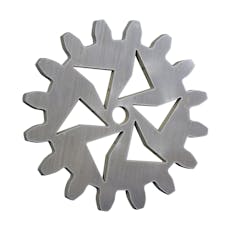
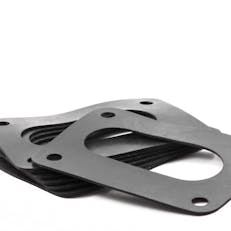
Not seeing the material you are looking for? We will source it! Submit your quote request using "Custom" in the material drop-down and our expert team will be happy to review the project.
Standard Sheet Gauges
De-Tabbing, Deburr, and Finishing
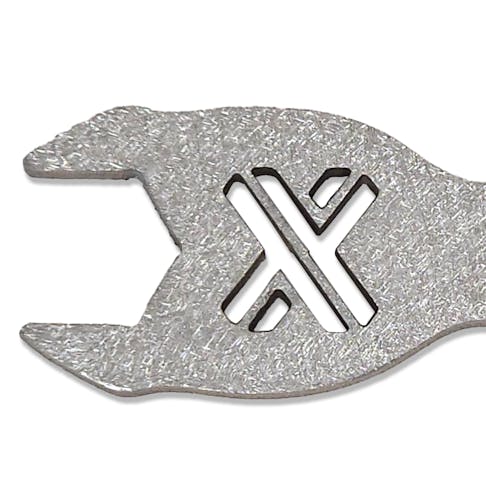
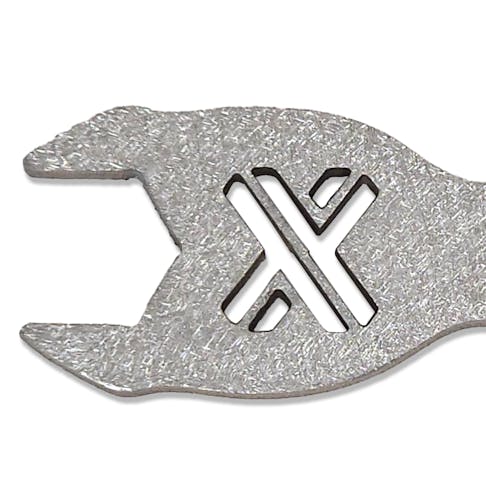
Parts will be separated, the tab will be ground off, and all burrs will be removed. Additionally, parts are cleaned to remove discoloration, surface debris, manufacturer markings, and scratches.
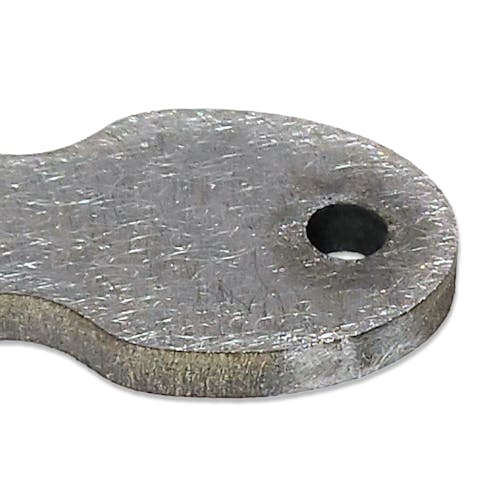
Parts will be separated from each other, and the source sheet and any vestigial tabs will be ground off. The area where tabs are removed may have a slightly different texture or appearance than the rest of the part.
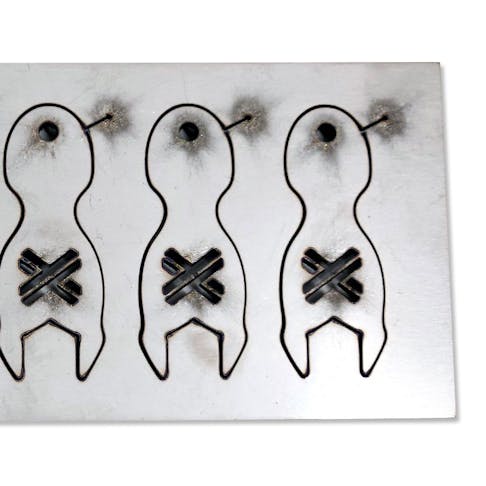
Reduce costs by receiving the parts tabbed together on the source sheet, to each other, or a support structure. You are then responsible for separating the parts from the sheet. Laser and waterjet cut parts may have fine burrs after cutting.
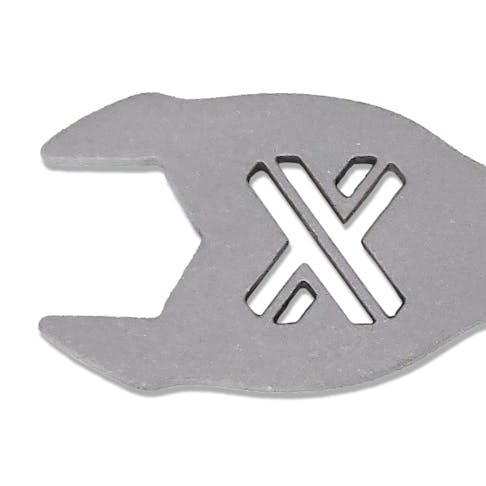
Parts are finished in a blasting cabinet with a high-pressure stream of fine glass beads, typically using 80-grit media applied between 70-100 psi. This gives the surface of the parts a uniform matte or satin-like cosmetic appearance.
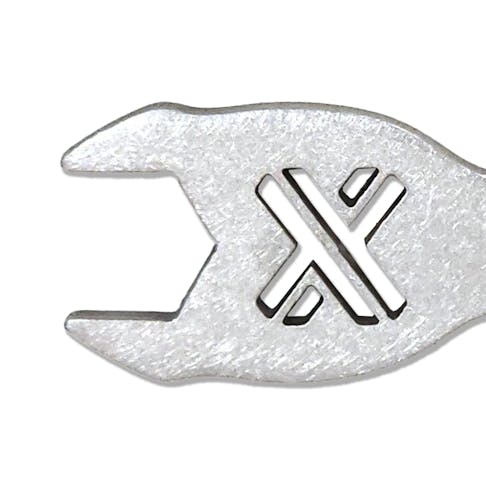
Parts are finished in a vibratory or rotary tumbler with tumbling media. This provides an even stippled finish over the face of the entire part. It also tends to round sharp corners and edges.
What Other Finishes are Available for Sheet Cut Parts?
Standard
A standard finish is available for all materials. No additional post-processing is performed, leaving the surface as-is after your choice of de-tabbing and deburring is performed. Plastics and cosmetically finished products may have an overwrap left on the faces for production. It is common for pre-polished, brushed, or textured materials to have only one side cosmetically finished.
Sanding with Grain
Metal parts are sanded by hand, abrasive belt sander, or timesaver, in the direction of the grain to create a uniform finish. This is also called linear finishing.
Sanding Random
Metal parts are sanded by hand, orbital sander, or timesaver, in a random pattern or swirl to create a uniform finish. This is also called a random swirl finish.
Other Finishes
Like our other services, Xometry can offer turnkey finishing services like anodizing, chem-film, metal plating, powder coating, heat treating, passivation, and even multiple custom finishes. See samples and learn more by visiting our Metal Finishes Gallery.
Design Guide: Laser and Sheet Cutting
Sheet Cutting FAQs
What Files Can Xometry Use for Laser Cutting or Waterjet Cutting?
Xometry can accept DXF, STEP, STP, SLDPRT, IPT, and SAT files for laser and waterjet sheet cutting services. These files should be flat profiles extruded to the appropriate thickness or gauge of the intended material. Xometry’s instant online quoting tool also allows 2D DXF files to be uploaded and their thickness defined directly on the platform.
What Is the Smallest Part Size Xometry Can Cut?
Xometry can cut features down to about 0.25” x 0.25” depending on complexity. Parts below the size of a nickel may require specialized workholding. It is recommended that parts under 2” x 2” may need to be tabbed to a sheet or bridged on as a strip to prevent falling between machine slats.
Holes and cutouts should be larger than the material thickness or 0.050”, whichever is greater.
Can Xometry Cut Both Outside and Inside Features?
Yes! Sheet cutting, such as laser cutting services, can cut the outline of a part and any top-down through features such as holes, design patterns, grate features, etc. These features should be provided all in one file.
Sheet cutting cannot do partial-depth features like blind bosses, counterbores, undercuts, or side holes. This would require CNC machining services.
What Is Kerf?
Kerf refers to the material that is burnt or cut away during laser cutting. Kerf is the gap thickness created by the laser and is usually around 0.008” with a +/- 0.004” tolerance depending on the process and material thickness.
Waterjet cutting has a stream thickness of between 0.04” to 0.05”. Think of it as a regular sharpie with medium pressure regarding detail resolution.
Xometry’s typical part tolerance is +/- 0.010” for laser cutting or waterjet cutting; this includes compensation for kerf. Small holes, thin gaps, and relief cuts may be slightly larger than dimensioned if their design is close to the kerf thickness.
What Is the Material Grain?
Extruded materials such as metals and some plastics will have a grain direction. This is presented by linear features, which are generated as the material is created. Hardwood and wood veneer will also have a grain direction based on the growth.
Parts are weaker or may crack more easily along their grain. If grain direction is important to a part's function or cosmetics, please identify that using an attached technical drawing or notes. Otherwise, Xometry’s suppliers will use their best practices when cutting the parts.
What Do Edges Look Like After Sheet Cutting?
Laser beams have a slight cone shape and will show a small taper from the top cut to the bottom face of a material. This is more exaggerated over thicker parts. Waterjet cutting will also spray in a tight cone, showing a small reverse taper from top to bottom.
In both laser cutting and waterjet cutting, there will be vertical striations on a cut surface. This differs from a CNC milled, or CNC routed edge, which will appear smoother.
We offer various de-tabbing and deburring options to allow you to balance costs and time. Learn more about these options by visiting our FAQ page.
What Do Holes Look Like After Sheet Cutting?
The holes a laser can cut or a waterjet can cut are rougher than a standard drill due to the edge condition. If the holes are tolerance-critical it is recommended to undersize the hole by 0.005” and post-drill the feature.
Can Xometry Add Threads to Sheet Cut Parts?
Xometry can tap most sheet cut parts using our standard threads. Adding inserts, such as PEM inserts, is also available for metal sheet parts.
Can I Send Nested Designs for Laser Cutting?
Yes! You can nest your design into a 2D DXF file and upload it for quoting.
Can You Cut Shim Stock?
Yes! We may need to manually quote shim stock or spring stock materials, but if there is a readily available gauge of your design, we can quote your project.
Note that as metal material stocks are thinner, it is more likely they are provided in a roll (think aluminum foil). This means that flatness is not guaranteed on shim material.
Shim stock may need to be sandwiched with sacrificial material for cutting, which can increase costs.
Will Waterjet Cut Parts Be Wet?
Nope. Your parts will ship dry!
If you have any special packing requirements or requests, please let us know in the part notes section when building your quote.
Will I Need to Pay Tariffs on Internationally Produced Parts?
Xometry's checkout price for internationally produced prototypes shipped to the US includes tariffs and shipping for standard parcels. You can learn more by reading our article on understanding international shipping costs.
Ready to Get a Sheet Cutting Quote?
Free shipping available for domestic sheet cutting orders ; learn more!
Why Use Xometry's Sheet Cutting Services?
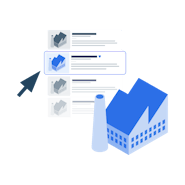
Endless Options
Choose from thousands of possible combinations of sheet materials, finishes, tolerances, markings, and certifications for your order.
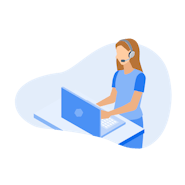
Easy to Use
Get your parts delivered right to your door without the hassle of sourcing, project management, logistics, or shipping.
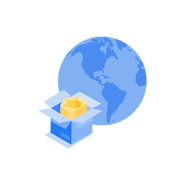
Vetted Network
We are ISO 9001:2015, ISO 13485, and AS9100D certified. Only the top shops that apply to become Suppliers make it through our qualification process.