Laser-Cut HDPE Services by Xometry
Xometry offers the highest quality laser-cut HDPE services and can assist in the production of parts with intricate and complex geometries and excellent surface finishes.
HDPE is commonly used for a wide range of applications, such as: packaging and display solutions, signage and graphics production, as well as prototyping and model making. Laser cutting HDPE (High-Density Polyethylene) uses a high-powered laser beam to cut through sheets or blocks of HDPE material. It is recommended to optimize the laser power, cutting speed, and other parameters when laser cutting this material.
Xometry is a reputable provider of laser cutting services, offering high-quality laser cutting of HDPE (high-density polyethylene) materials. With our state-of-the-art laser cutting machines, Xometry ensures precise and accurate cuts for HDPE components, meeting custom specifications with excellence.
What Is HDPE?
HDPE (high-density polyethylene) is made from petroleum and is one of the most widely used thermoplastic polymers. It is known for its high strength-to-density ratio, high impact resistance, high melting point, excellent chemical resistance, and durability.
HDPE is manufactured through a polymerization process that chemically links ethylene molecules, creating lengthy chains. This molecular structure gives the material its high density, hence the name "high-density polyethylene." HDPE is commonly available in various forms, including solid sheets, pipes, and molded products.
Laser cutting HDPE can be used for shaping and fabricating HDPE components with intricate designs or precise dimensions. Polyethylene is suitable for laser cutting up to a thickness of approximately 10 mm. However, although laser cutting can be used to cut HDPE, care should be taken when a laser beam is used to cut this material. It's advisable to optimize the laser power, cutting speed, and other parameters to achieve the desired results.
It's important to note that the values provided for HDPE are given in a range. Different companies produce various blends of HDPE, each having its unique set of material properties. Table 1 below highlights some of the properties of HDPE:
Property | Value |
---|---|
Property Density | Value 0.933–1.27 g/cm^3 |
Property Yield Strength (Tensile, @ -30.0–70.0 °C/ -22.0–158 °F) | Value 6.89476–30 MPa |
Property Modulus of Elasticity | Value 0.483–1.45 GPa |
Property Flexural Yield Strength | Value 16.5–91 MPa |
Property Izod Impact, Notched | Value 0.20–7.50 J/cm |
Property Melting Point | Value 26.0–135 °C |
Property Maximum Service Temperature (Air) | Value 80.0–120 °C |
Property Linear Mold Shrinkage | Value 0.00500–0.0400 cm/cm |
Property Water Absorption | Value 0.0100–0.300% |
Property Coefficient of Friction | Value 0.200–0.280 |
Property Price-to-quality ratio | Value Good |
Advantages of Laser-Cut HDPE
Laser cutting HDPE offers several advantages, including:
- Cost Effective
- Food Safe
- Strong
- Chemically Resistant
- Non-Contact Process
- Design Flexibility
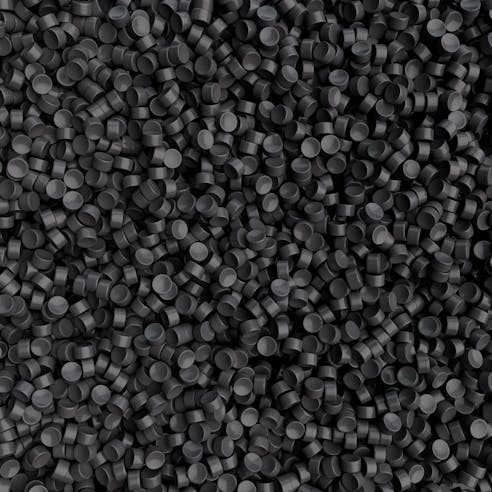
Cost Effective
Laser cutting HDPE can be a cost-effective solution due to its precision and minimal material waste. The accuracy of laser cutting helps optimize material usage, reducing waste, and saving costs. Additionally, the non-contact nature of laser cutting minimizes tool wear and reduces the need for frequent tool replacement or maintenance.
Food Safe
HDPE is considered a food-safe material. It is suitable for applications that involve direct contact with food or beverages. Laser cutting is a clean process that produces minimal dust, debris, or particles. This makes it suitable for applications such as: food packaging, cutting boards, utensils, and food processing equipment.
Strong
HDPE is known for its strength and durability. Laser cutting does not compromise the inherent strength of the material, as it does not introduce excessive heat or mechanical stress during the cutting process.
Chemically Resistant
HDPE exhibits excellent chemical resistance, making it resistant to a wide range of substances including acids, alkalis, and solvents. Laser cutting does not affect the chemical resistance of HDPE, allowing the cut components to maintain their resistance to chemical exposure. This property makes laser-cut HDPE suitable for applications in industries such as: chemical processing, laboratory equipment, and storage containers for corrosive substances.
Non-Contact Process
Laser cutting is a non-contact cutting method, meaning the laser beam does not physically touch the HDPE material. This eliminates the risk of tool wear or deformation of the material.
Design Flexibility
Laser cutting provides design flexibility, allowing for the creation of intricate shapes, curves, and patterns. It enables the production of customized and unique HDPE components to meet specific requirements.
Disadvantages of Laser-Cut HDPE
While laser cutting HDPE offers some advantages, it is important to consider some potential disadvantages as well. Here are a few drawbacks associated with laser cutting HDPE:
- Highly Flammable
- Sensitive to Stress Cracking
- Thermal Impact
- Potential for Melting
- Material Odor and Emissions
- Limited Thickness Range
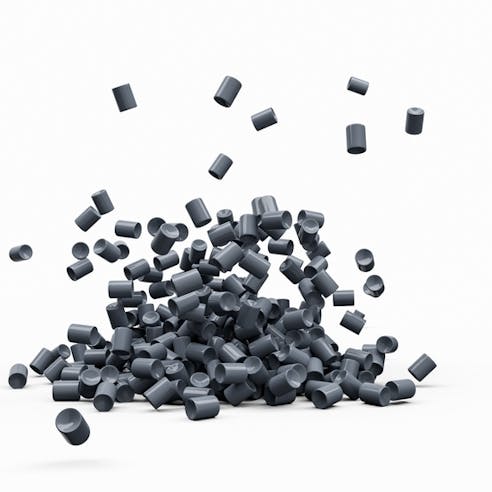
Highly Flammable
HDPE has a relatively low ignition point and is considered highly flammable. When exposed to an open flame or high temperatures, it can ignite and sustain a fire. Adequate fire safety precautions and adherence to fire codes are necessary when laser cutting HDPE, regardless of the cutting method employed.
Sensitive to Stress Cracking
HDPE is prone to stress cracking when exposed to certain chemicals, especially those with a high stress-cracking agent content. The combination of stress and chemicals can lead to the development of cracks or fractures in the material. It is important to consider chemical compatibility when working with HDPE.
Thermal Impact
Laser cutting involves the use of a high-powered laser beam that generates heat. The thermal impact of the laser can cause melting and re-solidification of the HDPE material along the cut edges. This may result in a slight change in the material properties near the cut, such as reduced crystallinity or increased brittleness. While these changes may not be significant for many applications, they should be considered in scenarios in which the material properties are critical.
Potential for Melting
HDPE has a relatively low melting point compared to some other materials. The high temperatures generated by the laser beam during cutting can potentially cause localized melting of the HDPE material, leading to distortions or undesired changes in shape. Careful control of the laser power, speed, and other cutting parameters is required to minimize the risk of excessive melting.
Material Odor and Emissions
Laser-cutting HDPE can release fumes and odors, especially if the HDPE material contains additives or impurities. These emissions may include volatile organic compounds (VOCs) and potentially hazardous byproducts. Adequate ventilation and proper extraction systems are necessary to ensure the safety of the operators and to minimize exposure to these emissions.
Limited Thickness Range
Laser cutting is most commonly used for cutting relatively thin sheets of HDPE (up to about 10 mm). While it is possible to cut thicker HDPE materials using laser cutters with a higher power, there are practical limitations to the maximum thickness that can be effectively cut. Thick HDPE sections may require multiple passes or alternative cutting methods, which could impact efficiency and cost-effectiveness.
Applications of Laser-Cut HDPE
Here are some common applications of laser-cut HDPE:
- Containers
- Cutting Boards
- Piping
- Bulkheads
- Packaging
- Automotive Components
- Electronics and Electrical Enclosures
- Prototyping and Model Making
- Medical and Laboratory Equipment
- Gaskets and Seals
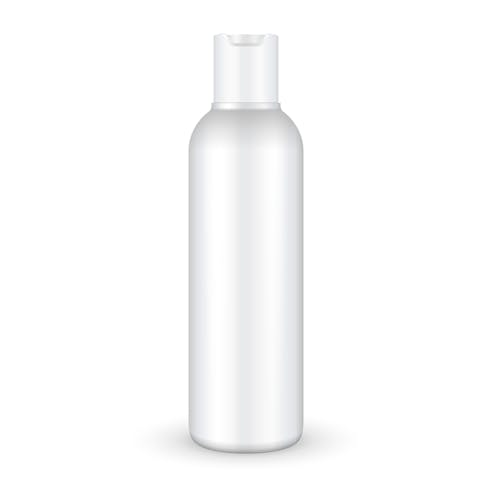
Containers
HPDE is commonly used for different types of plastic containers, including: plastic bottles, milk jugs, bleach containers (due to their excellent chemical resistance), shampoo bottles, and more.
Cutting Boards
Laser-cut HDPE is commonly used in the production of cutting boards, including those used in professional kitchens, households, and marine environments.
Piping
The non-absorbent nature of HDPE and its ease of welding contribute to its widespread adoption among pipe manufacturers. The exceptional properties of HDPE make it an ideal material choice for creating lightweight, rigid, and long-lasting piping systems.
Bulkheads
In the maritime industry, bulkheads are structural partitions or walls within a vessel or ship. Laser-cut HDPE is used in the fabrication of bulkheads due to its excellent properties.
Packaging
HDPE sheets can be laser cut to create custom packaging solutions such as inserts, trays, and dividers. The precise cutting ensures a perfect fit for products, providing protection during shipping and handling.
Automotive Components
HDPE is widely used in the automotive industry for various components such as: interior trim panels, door panels, and electrical enclosures. Laser cutting allows for the precise shaping of HDPE parts, ensuring a perfect fit and finish.
Electronics and Electrical Enclosures
Laser-cut HDPE is commonly used in the manufacturing of electrical enclosures, control panels, and switchgear components. The material's excellent electrical insulating properties, combined with precise cutting, make it ideal for these applications.
Prototyping and Model Making
Laser cutting HDPE is popular in the prototyping and model-making industries. It enables the quick and accurate production of intricate shapes, helping to bring designs to life.
Medical and Laboratory Equipment
HDPE is widely used in the medical and laboratory sectors due to its chemical resistance and low moisture absorption. Laser cutting allows for the production of custom components such as sample holders, trays, and equipment enclosures.
Gaskets and Seals
HDPE sheets can be laser cut to create gaskets and seals for various industries, including plumbing, HVAC, and automotive. The precise cutting ensures tight tolerances and a reliable sealing solution.
In need of custom laser-cut HDPE services?
Alternatives to Laser-Cut HDPE
Xometry offers several services that can be alternatives to laser cutting HDPE. Here are a few options:
- CNC Routing
- Waterjet Cutting
- CNC Milling
- CNC Turning
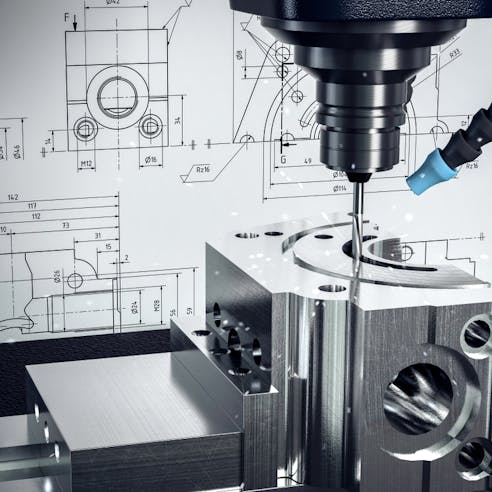
- CNC Routing: CNC routers use cutting tools to remove material from the HDPE sheet, creating the desired shapes and designs. This method is suitable for larger and thicker HDPE sheets and offers precise cutting capabilities.
- Waterjet Cutting: Waterjet cutting uses a high-pressure jet of water mixed with an abrasive material to cut through HDPE. This method is suitable for various thicknesses and can achieve precise cuts with high accuracy.
- CNC Milling: CNC milling uses rotating cutting tools to remove material from the HDPE block or sheet, allowing for precise shaping and machining. It is suitable for creating complex shapes, cavities, and detailed features on HDPE parts.
- CNC Turning: If your HDPE project requires cylindrical or rotational parts, CNC turning can be a suitable alternative. CNC turning utilizes a lathe machine to shape the HDPE material while it rotates, creating cylindrical or rotational features.
Why Choose Xometry for Laser-Cut HDPE Services?
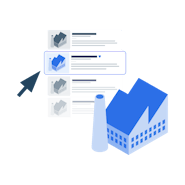
Endless Options
Choose from millions of possible combinations of materials, finishes, tolerances, markings, and certifications for your order.
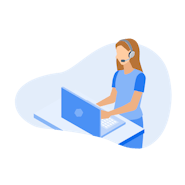
Easy to Use
Get started with our easy-to-use platform and let our experts take care of managing the project from locating the right manufacturing partner to delivery logistics.
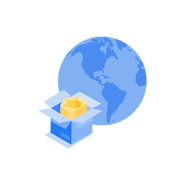
Vetted Network
We are ISO 9001:2015, ISO 13485, and AS9100D certified. Only the top shops that apply to become Suppliers make it through our qualification process.