Fiberglass Laser Cutting Services by Xometry
Xometry offers the highest quality custom fiberglass laser cutting services and can assist in the production of parts with intricate and complex geometries and excellent surface finishes.
Fiberglass laser cutting is the process of removing or marking fiberglass sheets or panels with a concentrated beam of electromagnetic energy. It is a highly precise, efficient, and largely automated non-contact process that is a viable alternative to mechanical cutting. With mechanical cutting, fiberglass tends to dull the teeth or blades of the cutting tool. This is due to the hard glass fibers embedded in the composite material that is difficult to cut through unless the right type of tool is used. While laser cutting fiberglass can be much quicker and more precise than mechanical cutting, this can be a dangerous process if not done correctly due to toxic fumes released during the process. Careful attention and proper preparation are paramount to ensuring a successful fiberglass laser cutting operation. In spite of the challenges, fiberglass laser cutting is used to fabricate parts for several different industries including: industrial textiles, construction, automotive, piping, and more.
Xometry offers superior-quality fiberglass laser cutting services for a variety of industries and applications.
What Is Laser Cut Fiberglass?
Laser cutting of fiberglass is the process of using a focused beam of electromagnetic energy to rapidly heat and vaporize fiberglass material to produce clean, precise cuts. It is closely related to laser marking. Laser marking is the production of markings on a workpiece surface by vaporizing and discoloring the epoxy material in the fiberglass to a very shallow depth. Laser marking can also be performed on fiberglass. Compared to other fabrication methods, fiberglass laser cutting is a highly precise and efficient manufacturing method that can be used to make parts with complex shapes and designs.
Fiberglass is notorious for being difficult to process due to its hardness, which tends to dull cutting tool blades unless the correct tool is used. However, since no physical tool contacts the workpiece during laser cutting, no tool becomes dull. Parts can thus be fabricated consistently to precise dimensions. However, laser cutting of fiberglass should not be undertaken using underpowered machines in poorly ventilated fabrication areas. A well-ventilated space and a laser cutter with sufficient power are required.
Laser Cutting Processes for Fiberglass
Two types of laser cutting processes are used on fiberglass: laser cutting and laser marking. Well-ventilated workspaces and high-power CO2 laser cutting machines are best suited to cut fiberglass. This is because fiberglass readily absorbs the wavelengths produced by CO2 lasers and ventilation ensures toxic fumes do not linger in the workspace. The two processes are described in more detail below:
- Laser Cutting
- Laser Marking
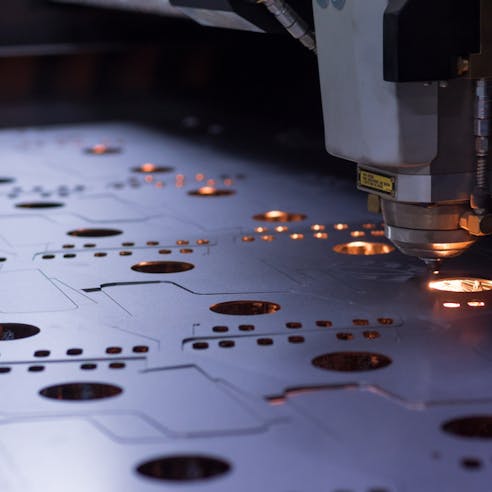
Laser Cutting
Laser cutting is the process of trimming through the entire workpiece thickness to create different fiberglass shapes. Fiberglass laser cutting is possible due to the material’s ability to readily absorb the wavelengths of the electromagnetic energy produced by the laser. The CNC-controlled and focused laser beam rapidly heats the fiberglass material and vaporizes it away to produce clean-cut and precise edges.
Laser Marking
Laser marking is the process of creating permanent marks on the workpiece surface to create elaborate logos and designs or traceability features like barcodes and QR codes. Unlike the case in laser cutting, in laser marking the laser does not penetrate through the entire workpiece’s thickness. Instead, the laser is used to burn or “carbonize” the material on the workpiece surface. Marks produced by lasers are durable and long-lasting since they are recessed into the surface of the part.
Advantages of Laser Cutting Fiberglass
There are many advantages of laser cutting fiberglass. The list below describes some of those advantages:
- Exact Cut Edges
- High Precision
- Versatile
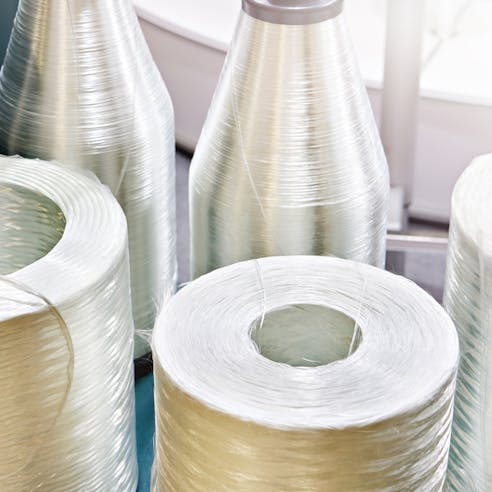
Exact Cut Edges
Workpiece edges produced by laser cutting do not require significant post-processing to obtain desired dimensions because it is a non-contact process and does not leave splinters or burrs on cut edges. This makes laser cutting a highly efficient and repeatable process that produces few defects like burned edges or cuts out of required tolerances.
High Precision
Fiberglass laser cutting results in minimal distortion. It is used to achieve highly precise dimensions with tolerances as small as +0.0004” (or 1 micron in diameter). There is no distortion in the part because laser cutting is a non-contact process. Additionally, although laser cutting is a thermal process, minimal heat is applied to the overall workpiece since electromagnetic energy is concentrated on an area with a diameter as small as 1 micron. This results in minimal thermal distortion.
Versatile
Fiberglass laser cutting is suitable for producing parts for a variety of industries and applications such as in the oil and gas industry, construction, and more. The same laser-cutting machine can be used to make complete cuts through the material or produce marks on the material’s surface. This presents numerous opportunities for manufacturers to be creative in how to produce different, complex shapes or in making elaborate logos and designs.
Disadvantages of Laser Cutting Fiberglass
There are a few disadvantages of laser cutting fiberglass as well. These must be taken into consideration and handled properly to ensure safe process operation and desired product quality. The disadvantages are described below:
- Environmental Challenges
- Health Concerns
- Post-Processing Required for Aesthetics
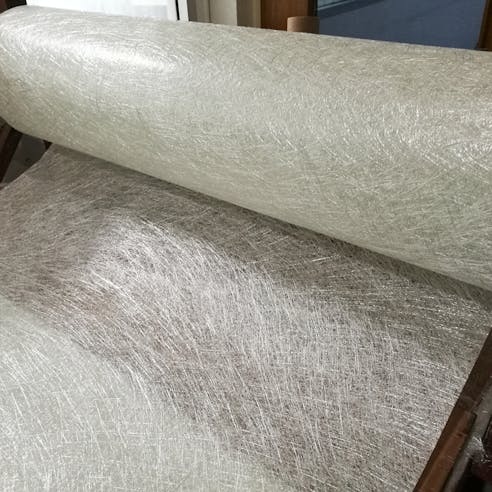
Environmental Challenges
As fiberglass is cut using a laser, the epoxy resin holding the material together is vaporized. This releases toxic fumes that are not safe for the environment. While proper ventilation can be used to ensure a safe workspace, the fumes released during laser cutting fiberglass are released into the atmosphere and adversely affect its health. Charcoal or HEPA filters, as well as HVAC exhaust systems, can be employed to prevent contaminants from leeching into the atmosphere.
Health Concerns
The fumes produced from vaporized epoxy during the fiberglass laser cutting process are toxic and pose an immediate danger to human health. In addition to adequate ventilation in a fabrication area, workers should wear respirators. The fumes produced, which may include cyanide and benzene, are extremely dangerous. Inhaling too many of them can lead to death.
Post-Processing Required for Aesthetics
Laser cutting fiberglass may produce clean-cut edges made to exact dimensions, but laser cutting also blackens the cut edges. This is because the cut surface that was not vaporized essentially chars. While removing the blackened edges adds an extra process to laser cutting fiberglass, the blackening can easily be removed with a solvent cleaner.
In need of custom fiberglass laser cut parts?
Laser-Cut Fiberglass Applications
Laser-cut fiberglass has numerous applications — from use in construction and piping to use in the automotive industry. Some of the applications are listed and described below:
- Storage Tanks
- Home Construction
- Oil and Gas Artificial Lift Systems
- Piping
- Automotive Components
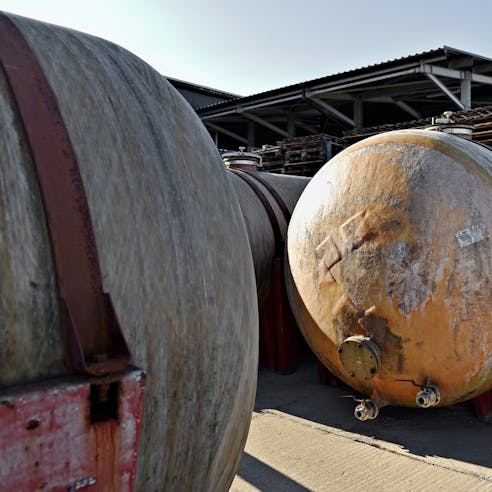
Storage Tanks
Laser cutting is often used in the fabrication of fiberglass storage tanks for water and other fluids. It is used to cut a fiberglass sheet to desired dimensions before it is rolled to the desired shape of the storage tank.
Home Construction
Fiberglass is often used in home insulation, but also for both interior and exterior wall panels. Laser cutting is an efficient way to repeatably produce fiberglass panels and insulation to exact dimensions.
Oil and Gas Artificial Lift Systems
Fiberglass components are commonly used in the oil and gas industry for artificial lift systems. Artificial lift systems are devices that facilitate the movement of subterranean oil to the surface by increasing the pressure within the underground oil reservoir. Sucker rods, the components that connect the surface components and subterranean components in beam pump systems used to pump oil are commonly made from fiberglass. Laser cutting can be used for the fabrication of these components.
Piping
Fiberglass pipes are created by plastic extrusion processes and cut to length using lasers.
Automotive Components
Fiberglass is commonly used in the automotive industry for front and rear bumpers, doors, hoods, casings, V-belts, timing belts, clutch disks, and more. Fiberglass laser cutting can make fabrication of these components simpler and more efficient, while also achieving high levels of precision.
Alternatives to Laser Cutting Fiberglass
Xometry offers several alternatives to laser cutting fiberglass if laser cutting is not viable. Some of the alternatives are listed and described below:
- CNC Mechanical Cutting
- Waterjet Cutting
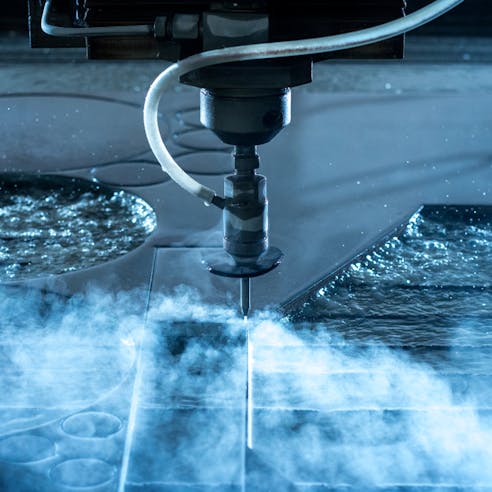
- CNC Mechanical Cutting: Mechanical cutting using CNC-operated saws, end mills, routers, or other tools is a suitable alternative to laser cutting fiberglass. Mechanical cutting is perhaps the most used method to fabricate fiberglass parts, but non-contact cutting methods are slowly becoming more common. While mechanical cutting fiberglass is possible, blades wear out easily and must be replaced frequently due to the hard glass fibers embedded in the fiberglass material. Still, mechanical cutting is a tried-and-true method to fabricate fiberglass parts - albeit not as fast as laser cutting.
- Waterjet Cutting: Waterjet cutting uses high-pressure water (up to 60,000 psi) to cut parts. It is a great but expensive alternative to laser cutting. Abrasives such as garnet are added to the waterjet to enhance its ability to cut materials. Waterjet cutting, like laser cutting, is a precise process. Unlike laser cutting machines, however, waterjet cutting machines cannot be used to mark parts and are only used for removing entirely through the material.
Why Choose Xometry for Custom Fiberglass Laser Cutting Services?
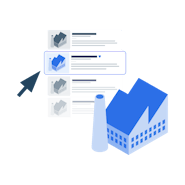
Endless Options
Choose from millions of possible combinations of materials, finishes, tolerances, markings, and certifications for your order.
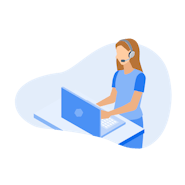
Easy to Use
Get started with our easy-to-use platform and let our experts take care of managing the project from locating the right manufacturing partner to delivery logistics.
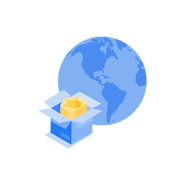
Vetted Network
We are ISO 9001:2015, ISO 13485, and AS9100D certified. Only the top shops that apply to become Suppliers make it through our qualification process.