Sinker EDM Services by Xometry
Xometry offers sinker EDM machining as a value-added, turnkey service to our primary manufacturing processes, including CNC, 3D printing, injection molding, casting, sheet cutting, etc. A product can be fully customized using the Xometry Instant Quoting Engine®. Xometry does not provide secondary processing or finishing to parts supplied by a third party, with few exceptions.
Xometry provides top-notch sinker electrical discharge machining (EDM) services, ensuring finished parts are of exceptional quality for our customers. Sinker EDM uses electrical discharges to remove material and create precise shapes in conductive materials. To meet the unique requirements of each project, Xometry’s skilled team adheres to a thorough and complete process for designing both parts for EDM and the details of the EDM for a specific part.
Xometry's sinker EDM services offer precision machining for complex shapes with high accuracy. The versatility of sinker EDM allows for the production of intricate components using a wide range of conductive materials. Sinker EDM is the ideal method for creating intricate hollows and hidden recesses in a workpiece. These hollows often have complicated geometries that make it impossible to use traditional techniques like CNC milling. Surprisingly, the electrode's ability to remove material is unaffected by the material's hardness. As a result, sinker EDM becomes a formidable option for creating cavities in hardened steels, particularly to fabricate injection molds. In small-batch CNC machining, customers frequently specify aluminum, stainless steel, or brass for their excellent mechanical and physical properties, and Xometry can provide sinker EDM machining for these and any other conductive metals or alloys a customer may require.
What Is Sinker EDM Machining?
Sinker EDM (electrical discharge machining) is also referred to as ram EDM, plunge EDM, conventional EDM, and die-sinking EDM. It is a precise manufacturing procedure used to make complex shapes in electrically conductive materials. It works by creating a controlled electrical discharge between the workpiece, which is immersed in a dielectric fluid, and an electrode, also known as the tool. As a way to shape the workpiece into the desired shape, the electrical discharge erodes the material by removing tiny particles from the workpiece. Sinker EDM is especially well suited for intricate parts and materials that are challenging to machine using traditional techniques.
Sinker EDM Capabilities
Capability | Description |
---|---|
Capability Dimensional Tolerance | Description The allowable deviation from the intended dimensions is +/-0.004 mm. |
Capability Cutting Axis | Description Sinker EDM cuts a workpiece by moving along the z-axis. |
Capability Length | Description Maximum workpiece length is 47″. The maximum workpiece length in sinker EDM is typically limited by the stroke length or travel distance of the machine's Z-axis (vertical movement). This axis controls the movement of the electrode (usually made of graphite or copper) that creates the electrical discharges to erode the workpiece material. |
Capability Height | Description A workpiece can be accommodated in Sinker EDM up to a height of 14". The size of the workpiece, however, can vary depending on a number of factors such as the workspace and maximum workpiece dimensions. |
Capability Accuracy | Description It is possible to attain accuracy within a range of ±0.004 mm. It is recommended to carefully choose the electrode material and monitor the discharge current and frequency. |
Capability Repeatability | Description Sinker EDM’s repeatability and dependability depend on several technical factors. These include efficient spark discharge control, constant electrical parameters, accurate tool, and workpiece alignment, reliable dielectric flushing, and a controlled environment to reduce process-affecting environmental factors. |
Capability Width | Description The maximum width of the workpiece is 27″. |
Capability Surface Finish | Description Sinker EDM can produce highly smooth and uniform finishes. Additional processing might be needed based on the specific requirements of the part being machined. |
Table 1: Sinker EDM Capabilities
Sinker EDM Materials
The sinker EDM process can be used on a variety of materials. The only requirement is that the material be electrically conductive. The following is a list of potential raw materials and their typical applications:
- Aluminum
- Brass
- Copper
- Exotic Metals
- Copper
- Galvanized or Bright Zinc-Plated Steel
- Molybdenum
- Titanium
- Tungsten
- Carbide
- Tool Steels
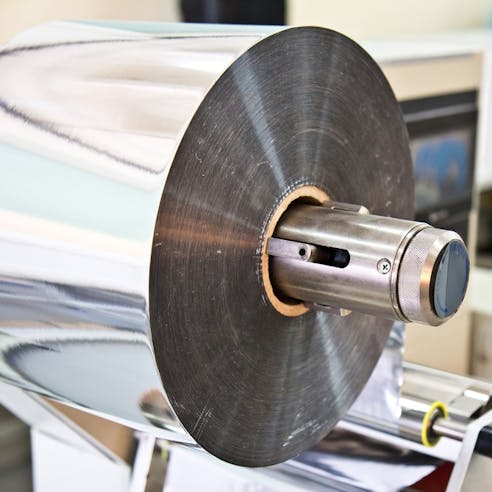
- Aluminum: Aluminum, renowned for its lightweight nature and exceptional thermal conductivity, is extensively utilized in various industries. It is particularly favored in aerospace components, automotive parts, and electronics due to its advantageous properties. the application of sinker EDM technology further enhances the precision and efficiency of manufacturing processes involving aluminum, ensuring high-quality end products.
- Brass: The creation of intricate designs on brass surfaces is an innovative application that makes use of sinker EDM. Plumbing fittings, electrical connectors, and musical instruments often use brass because of its exceptional electrical conductivity and reputation for corrosion resistance.
- Copper: Copper is an excellent choice for a variety of applications due to its exceptional electrical and thermal conductivity. Sinker EDM makes use of copper as a conductive electrode to incredibly precisely shape and machine different components.
- Exotic Metals: Sinker EDM finds extensive use in the manufacturing of intricate components from exotic metals like Inconel® and Hastelloy. With its precise material removal capabilities, sinker EDM enables the creation of complex shapes and features, catering to the specific requirements of aerospace, oil and gas, and chemical processing applications.
- Molybdenum: The high melting point and high-temperature strength of molybdenum make it a popular material for use in many different industries. Sink EDM uses the exceptional conductivity and durability of molybdenum to precisely shape complex designs for furnace parts, electrical contacts, and aerospace components, ensuring superior performance and longevity.
- Titanium: One innovative application that leverages sinker EDM technology is the precision machining of titanium components. Titanium is a desirable material because of its low weight, high strength, and corrosion resistance. Sinker EDMprecisely fabricate intricate titanium parts for sporting goods, medical implants, and aerospace applications.
- Tungsten: The high density and exceptional hardness of tungsten are highly valued in the automotive and aerospace industries. Sinker EDM is a precise and effective way to form and shape tungsten. It is frequently used in the production of intricate components in this industries.
- Carbide: Carbide cutting tools, molds, and wear parts can have complex shapes and feature with the use of sinker EDM. By utilizing the high wear resistance of carbide, this cutting-edge method creates precise, long-lasting tools with exceptional performance capabilities.
- Tool Steels: Sinker EDM enables the accurate production of complex shapes when used in conjunction with an application, such as tooling for dies, punches, and molds. Utilizing the remarkable hardness, toughness, and wear resistance of steels, this technology creates robust and excellent tooling solutions.
Sinker EDM Advantages
The benefits of sinker EDM are listed below:
- Cuts Exotic Materials Easily
- Easy Cutting of Tough Materials
- Little or No Post-Process Polishing Required
- Cuts Thin Materials Without Damage
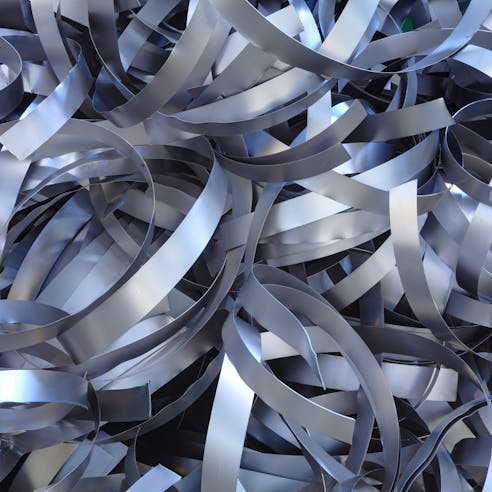
- Cuts Exotic Materials Easily: Sinker EDM excels at machining exotic materials like titanium or Inconel®, commonly used in aerospace or high-performance applications.
- Easy Cutting of Tough Materials: For use in tool and die applications, sinker EDM can efficiently machine tough materials like tungsten or hardened steel.
- Little or No Post-Process Polishing Required: The precision and fine surface finish achieved by sinker EDM often eliminate the need for extensive polishing, saving time and cost in the manufacturing process.
- Cuts Thin Materials Without Damage: Sinker EDM is a noncontact machining process which enables the precise cutting of thin and delicate materials, including thin sheets or delicate components, without resulting in any damage. It uses electrical discharges between an electrode and the workpiece to erode the material, ensuring little stress and distortion and making it just right for cutting fragile materials with high precision and accuracy.
Sinker EDM Disadvantages
The following are the disadvantages of the sinker EDM process:
- Slow
- High Operating Costs
- Limited to Conductive Materials
- Excessive Power Consumption
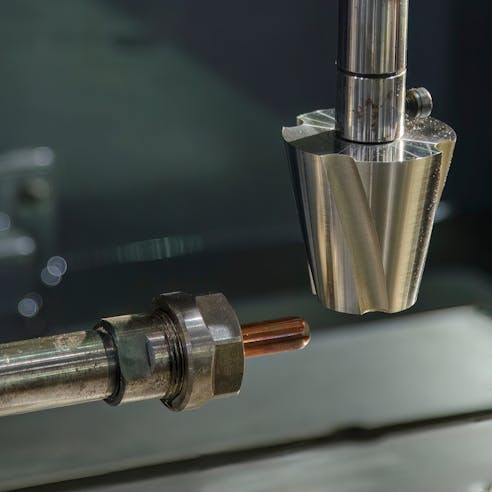
- Slow: Sinker EDM procedures can take a while, especially when working with intricate or complicated designs that may call for multiple passes and electrode replacements.
- High Operating Costs: Due to factors like electrode wear, dielectric fluid usage, and maintenance needs, sinker EDM can have high operational costs.
- Limited to Conductive Materials: Because it needs electrical conductivity to produce spark discharges, sinker EDM can only be used on conductive materials. Electrical current can move through electrically conductive materials, which speeds up erosion. Contrarily, non-conductive materials like ceramics, plastics, and composites do not conduct electricity and thus do not allow the sparks needed for sinker EDM to form. This technique cannot be used to shape or machine non-conductive materials without electrical conductivity.
- Excessive Power Consumption: The sinker EDM process uses a lot of electrical energy because it relies on high-intensity electrical discharges to erode and shape the workpiece. These discharges generate intense heat and require significant power input. Consequently, the process can lead to high energy costs, making it important to optimize the process parameters to minimize power consumption and maximize efficiency.
Sinker EDM Applications
Sinker EDM services have the following uses:
- Rapid Tooling
- Injection Molding Molds
- Dies
- Fine Details
- Sharp Inside Corners
- Deep and Thin Ribs
- Blind Cavities
- Blind Keyways
- Internal Splines and Threads
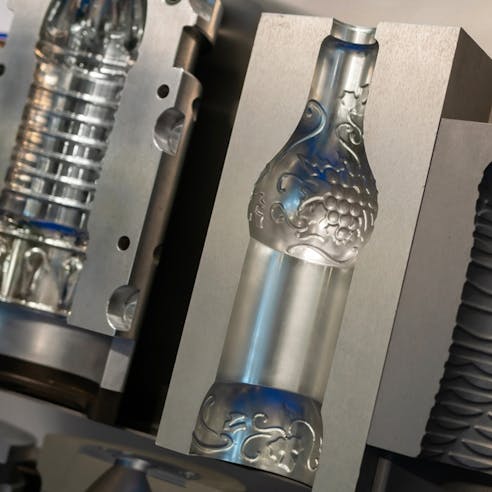
- Rapid Tooling: Fast, precise, and effective tooling component fabrication is possible with sinker EDM. It makes it possible to produce inserts, cores, and cavities quickly, all of which are essential in different manufacturing processes. Sinker EDM can accurately produce intricate details and complex geometries in less time than other techniques. Its capacity to speed up the production of essential components boosts general productivity and cuts down on lead times in the manufacturing process.
- Injection Molding Molds: Sinker EDM guarantees precise mold production, allowing for accuracy in dimensions and intricate detailing. The sinker EDM technique leaves behind a fine surface finish that requires little or no post-processing.
- Dies: When it comes to creating metal stamping dies, sinker EDM offers definite advantages over conventional techniques. Its use makes it simple to create intricate and precise shapes and profiles. High-quality stamped products can be produced using sinker EDM to create dies with precise dimensions and intricate details. This method guarantees exceptional accuracy and precision, which makes it a dependable and effective method for creating dies of high quality.
- Fine Details: Sinker EDM is excellent at producing intricate details in components for many industries, including: jewelry, electronics, and medical devices. Sinker EDM is indispensable in producing complicated design features like filigree patterns, engravings, and gemstone settings. It produces intricate electronic components with accuracy and repeatability, such as connectors, sensors, and circuitry. Sinker EDM is also used to manufacture precise surgical tools and parts for medical implants.
- Sharp Inside Corners: Sinker EDM can generate sharp inside corners with exceptional accuracy. This method is commonly used to make molds with exact inside-corner features, such as injection molds for plastic components or dies for metal stamping.
- Deep and Thin Ribs: In the aerospace industry, it is used to machine deep and thin ribs in parts like aircraft engine blades or structural components. These ribs improve the parts' structural stability while lowering their weight, allowing for more fuel-efficient designs. Similarly, sinker EDM can be used in the automobile industry to make complex and lightweight ribs in parts like cylinder heads or chassis components, enhancing performance and fuel efficiency.
- Blind Cavities: Sinker EDM can effectively create blind cavities in components, useful in applications where hidden features or internal structures are required. Blind cavities, created through sinker EDM may be used in various industries to achieve weight reduction or enhance structural integrity. For example, in aerospace applications, blind cavities can help reduce the overall weight of a component without compromising its strength. By removing material selectively, engineers can achieve weight savings while maintaining the necessary structural support. In the automotive industry, engine blocks can have internal coolant passages created using sinker EDM.
- Blind Keyways: Blind keyways are essential in many mechanical parts, including shafts and gears. Sinker EDM ensures precise and accurate cutting of keyways even in tight spaces where conventional machining techniques are ineffective. This ability makes it possible to build complex and exact features inside blind keyways, ensuring a secure connection between components.
- Internal Splines and Threads: Sinker EDM can produce internal splines and threads in components. Precision internal splines are often necessary for the machinery manufacturing industry for gear hubs, couplings, and transmission components to ensure proper power transmission. In the automotive industry, internal splines are essential in components such as drive shafts and differential gears.
Alternatives to Sinker EDM Machining
Xometry provides several alternatives to sinker EDM machining, including:
- Precision Grinding
- Wire EDM Machining
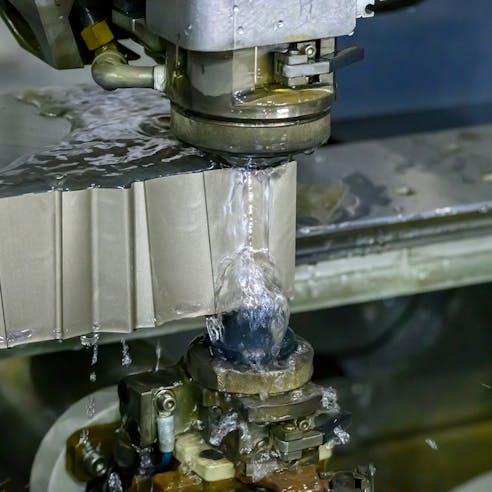
- Precision Grinding: Precision grinding is best for achieving high-quality surface finishes and tight tolerances. It involves removing material from a workpiece using abrasive wheels or belts. Precision grinding services are often employed as an alternative to sinker EDM when the material being machined is not conductive since insulating materials cannot be processed using the sinker EDM method.
- Wire EDM Machining: Wire EDM machining is a precise cutting process that uses an electrically charged wire to erode conductive materials. It shares a close relationship with sinker EDM, although there is a notable difference: wire EDM cannot create blind holes. By creating controlled electrical discharges between the wire and the workpiece, this method excels at machining intricate shapes, thin sections, and challenging-to-machine hard materials.
Why Choose Xometry for Sinker EDM Services?
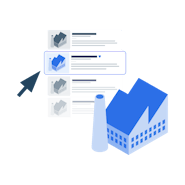
Endless Options
Choose from millions of possible combinations of materials, finishes, tolerances, markings, and certifications for your order.
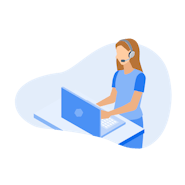
Easy to Use
Get started with our easy-to-use platform and let our experts take care of managing the project from locating the right manufacturing partner to delivery logistics.
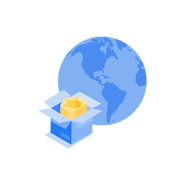
Vetted Network
We are ISO 9001:2015, ISO 13485, and AS9100D certified. Only the top shops that apply to become Suppliers make it through our qualification process.