Blanchard Grinding Services
High-quality Blanchard Grinding Services in Days Not Weeks | Free Standard Shipping on All US Orders | Subject to availability. Xometry doesn't guarantee that we can provide this service at any given time.
Blanchard grinding is a surface finishing process where a vertically oriented spindle rotates a horizontally oriented grinding wheel to precisely remove material from a metal part. In Blanchard grinding, also known as rotary surface grinding, the part may be fixtured either magnetically (for ferrous materials) or mechanically (for non-magnetic materials). The part rotates in a circle while the stationary grinding wheel removes material. Blanchard grinding can achieve tolerances as small as +0.001” on surfaces. It is an economical process due to the ease of loading and unloading parts and the process’s ability to produce precise surfaces on large parts.
Xometry offers Blanchard grinding as a value-added, turnkey service to our primary manufacturing processes, including CNC, 3D printing, injection molding, casting, sheet cutting, etc. A product can be fully customized using the Xometry Instant Quoting Engine®. Xometry does not provide secondary processing or finishing to parts supplied by a third party, with few exceptions. Our manufacturing experience across a variety of industries, coupled with our extensive manufacturing network, ensures that your part will be fabricated to the highest standards, within lead times that will get your finished products to your customers on time.
Blanchard Grinding Process
Blanchard grinding is an economical way to achieve good parallelism, flatness, and dimensional accuracy on large, flat parts. Metal is removed to the desired depth by the action of a horizontally rotating grinding wheel driven by a vertical spindle. Ferrous workpieces can be held in place magnetically. Other materials must be mechanically clamped to the work table. Once the part is fixed in place, the table rotates, and the grinding wheel is lowered onto the part. The action is similar to the spinning of street sweepers or floor polisher heads. The table and the grinding wheel rotate in opposite directions. This creates the signature cross-hatched surface appearance of a part subjected to Blanchard grinding. The grinding wheel continuously contacts the part until the desired surface characteristics and dimensions are obtained. Tolerances as small as +0.001” can be achieved, with flatness and parallelism deviations as small as +0.005”.
Advanced Machinery for Blanchard Grinding
Our Blanchard grinding process utilizes cutting-edge technology in the form of CNC control and state-of-the-art equipment that enables high-capacity grinders. CNC and automation allow Blanchard grinding to rapidly remove material from large flat parts while also removing the possibility of grinding surfaces not intended to be ground.
Additionally, advances in Blanchard grinding have increased the throughput of grinding machines and the rate of material removal. Moreover, advances in ceramic abrasive technology and the creation of grinding fluids have led to further improvements in the quality of grinding processes. Each advance has improved the ability of Blanchard grinding to compete as one of the most efficient, cost-effective, and reliable methods for achieving precise dimensions and high degrees of parallelism and flatness in large parts.
Advantages of Blanchard Grinding
Blanchard grinding has a number of advantages, which are listed below:
Fast Material Removal
The large grinding area and the depth of cut associated with Blanchard grinding make the process able to remove material fast. Blanchard grinding wheels can be as large as 100” and can remove up to 0.5” of material. While Blanchard grinding is ideal for larger parts like mold plates and large castings, forgings, stampings, and plate stock, the process is also great for removing material from multiple small parts simultaneously. This makes Blanchard grinding a fast, efficient, and effective method for removing rapidly material and achieving beautiful surfaces on parts.
Parallelism
Parallelism is the degree to which two opposite surfaces are parallel to each other. The ability to produce two parallel surfaces of a part largely depends on the surface quality and flatness of the baseplate and the size of the grinding wheel. Blanchard grinding services are best suited for single-sided material removal and grinding applications too large for double-disc grinding. can be made parallel to each other quickly and effectively. Once one surface is ground, the part is flipped and the surface opposite the first surface is ground in the same manner. Blanchard grinding can achieve a parallelism of 0.001” between two surfaces.
Flatness
Flatness is similar to parallelism but describes one surface rather than two surfaces. Flatness is the degree to which a surface extends without any bends, dips, bumps, or other features that may alter the surface of the part. Achieving a high degree of flatness, as with parallelism, is easy when using Blanchard grinding. The grinding wheel rotates parallel to the part’s surface and is lowered to remove material. Although precision grinding can achieve flatter surfaces than Blanchard grinding, Blanchard grinding can achieve 0.001” of flatness quickly and for large parts. This results in Blanchard grinding being economical.
Cost-Effective Solution
Blanchard grinding is a cost-effective surface finishing technique that can be used on large parts or multiple small parts. Required surface finishes and tolerances for one large part or multiple small parts can be achieved in one process when using Blanchard grinding.
Disadvantages of Blanchard Grinding
Blanchard grinding has several potential drawbacks, as listed and described below:
Limited to Flat Surfaces
Only flat surfaces can be ground since the part is held parallel to the grinding wheel. This limits the process’s ability to be used on angled or curved surfaces or parts with non-flat geometry. An alternative technique such as surface grinding, cylindrical grinding, or CNC machining must be used on such surfaces and parts to achieve desired tolerances and surface finishes.
Not Suitable for All Materials
Although Blanchard grinding can be used for all types of metals, it is best suited for ferrous materials like steel and iron. Using Blanchard grinding for non-ferrous metals like aluminum, brass, titanium, and more incurs more cost due to the need to design and fabricate custom fixtures that hold the non-ferrous workpiece. The design and fabrication of these custom fixtures are counterproductive to the cost-effectiveness that Blanchard grinding offers. Additionally, softer materials such as thermoplastics and materials with generally low machineability ratings are not able to be Blanchard ground.
Heat Generation
The Blanchard grinding process generates heat due to the friction between the grinding wheel and the part. The heat generated can lead to thermal distortion in the part, which can ultimately affect the flatness, parallelism, and dimensional accuracy of the part. This phenomenon is more common when working with thin materials since the heat is transmitted through the material more quickly. Heat generation can be mitigated by a properly used cooling fluid such as machining coolant.
In need of custom blanchard grinding services?
Applications and Industries Using Blanchard Grinding
Blanchard grinding is used for numerous applications across a variety of industries to achieve precise and aesthetically pleasing surfaces on parts. Some of those industries are listed below:
Manufacturing
Blanchard grinding is commonly used in several different manufacturing industries such as food and beverage, packaging, plastics, and more for surface finishing of plate stock or for fabricating complete parts such as mold and die plates. It also excels at preparing flat parts for other processes where flat surfaces are critical to the process being successful such as with painting or coating such as ship hulls. Additionally, Blanchard grinding is good for preparing parts that must be assembled together. It creates flat and parallel surfaces that help ensure assembly and dimensional tolerances satisfy customer requirements in a quick and cost-effective manner.
Aerospace
Blanchard grinding’s ability to produce parallel and flat surfaces in a precise and cost-effective manner makes the process prime for use in the aerospace industry. Blanchard grinding is often applied to: landing gear components, fuselage structures, bulkheads, connecting rods, spacers, and more. Blanchard grinding helps ensure that these components meet customer tolerance and flatness requirements common in the aerospace industry.
Automotive
Blanchard grinding is often used in the production of automotive parts. Automotive applications for surface finishing by Blanchard grinding include: disc brake rotors, flywheels, gears, gearbox housings, and engine blocks. It is an ideal process for these types of large, mass-produced parts since Blanchard grinding can economically achieve the required dimensional accuracy, parallelism, and flatness.
Construction
Metal fabrication for the construction industry employs Blanchard grinding for the surface finishing of parts such as large washer plates, brackets, and architectural trim pieces. Blanchard grinding is a good choice for these applications due to the process’s ability to produce parallel and flat surfaces as well as the aesthetically attractive cross-hatch pattern that results from the grinding process.
Oil and Gas
The oil and gas industry often utilizes Blanchard grinding to satisfy stringent dimensional requirements in parts such as gauge blocks, valve bodies, seats, flanges for pipelines, and heat exchanger plates. Additionally, Blanchard grinding is great for the surface preparation of large parts for welding due to the large grinding wheel used in the process.
Alternatives to Blanchard Grinding
Xometery's application engineers can help select an alternative grinding method when Blanchard grinding is not the best choice. Listed below are other surface finishing options available through Xometry:
Surface Grinding
Surface grinding is the most common type of grinding—of which Blanchard grinding is a type. Other types of surface grinding such as surface grinding: horizontal spindle grinding and vertical spindle grinding are two viable alternatives to Blanchard grinding. These methods are preferred over Blanchard grinding when needing to remove smaller amounts of material or satisfy smaller tolerances. Both use an abrasive grinding wheel to remove material from a part. In horizontal spindle grinding, the workpiece is fixed to a reciprocating table and the grinding wheel rotates parallel to the surface of the part. The grinding wheel is held stationary while the table’s position adjusts to feed the part into the wheel to grind the desired areas.
In vertical spindle grinding, the grinding wheel rotates perpendicularly to the part, as it does for Blanchard grinding. However, the table motion is reciprocating, not rotary. Vertical spindle grinding is best for grinding angled surfaces, slots, and tapered features in parts. Surface grinding may be preferred over Blanchard grinding if grinding non-ferrous parts or if parts are not wholly flat due to the magnetic rotary table and large grinding wheel used in the process.
Centerless Grinding
Centerless grinding is a grinding process suited for obtaining precise dimensions in round or cylindrical parts. This is in contrast to Blanchard grinding which is only suitable for use with flat parts. In centerless grinding, the workpiece rests on a support between the grinding wheel and a regulating wheel. The two wheels—the abrasive grinding wheel, and the regulating wheel—rotate in the same direction. During the grinding process, the grinding wheel forces the workpiece against both the support and the regulating wheel. As the two wheels and the workpiece rotate, the workpiece material is removed. Because the workpiece is not gripped in a chuck or fixture, the workpiece is not ground between centers meaning part features may have different surface characteristics but still meet dimensional requirements. Parts like camshafts and valve stems are examples of parts where centerless grinding can be used. Centerless grinding is a superb process for obtaining accurate dimensions and satisfying stringent tolerance requirements.
Cylindrical Grinding
Cylindrical grinding is another process tailored for cylindrical or round workpieces. In cylindrical grinding, the workpiece and grinding wheel rotate simultaneously, but in opposite directions. This enables all the external surfaces between the two opposite centers of the part to be ground. Unlike centerless grinding where the workpiece is supported between the grinding wheel and regulating wheel, the workpiece is supported by the machine in cylindrical grinding. Blanchard grinding can only be used on flat parts. Cylindrical grinding is best for obtaining precise dimensions in rotationally symmetric workpieces.
Milling
Milling is a subtractive manufacturing process that uses an end mill to remove material from a workpiece. The process is not limited to use on flat parts, as with Blanchard grinding. Milling can be used to achieve beautiful surface finishes on cut faces and can achieve tolerances as precise as +0.005”. While this is impressive, it is not as good as the precision offered by Blanchard grinding (+0.001”). Still, milling can be a reasonable alternative to Blanchard grinding if trying to achieve precise and aesthetically attractive surfaces on parts with complex geometries, albeit in a slower and likely more expensive manner.
Lapping
Lapping is a finishing process that utilizes an abrasive slurry to remove material from the workpiece. The slurry is created by a combination of an abrasive powder mixed with water or oil. During the lapping process, the workpiece is stationary while a lap plate performs an oscillating motion against the part. While the lap plate passes over the part, the abrasive slurry fills the gap between the plate and the part. This enables tiny amounts of material to be removed with each pass of the lap plate. Lapping can achieve extremely precise dimensions, with tolerances as small as +0.00002” (0.5 microns). Like Blanchard grinding, lapping is best suited for flat parts. It can achieve dimensions more precise than those yielded by Blanchard grinding, but lapping is a slower process, and produces surfaces with an even matte finish. Consequently, lapping cannot replicate the aesthetic qualities of surfaces that have been put through Blanchard grinding.
Why Choose Xometry for Blanchard Grinding Services?
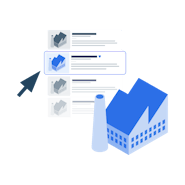
Endless Options
Choose from millions of possible combinations of materials, finishes, tolerances, markings, and certifications for your order.
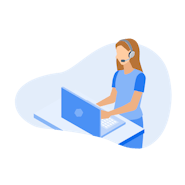
Easy to Use
Get started with our easy-to-use platform and let our experts take care of managing the project from locating the right manufacturing partner to delivery logistics.
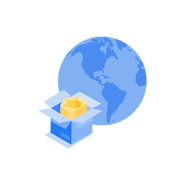
Vetted Network
We are ISO 9001:2015, ISO 13485, and AS9100D certified. Only the top shops that apply to become Suppliers make it through our qualification process.