Polypropylene (PP) CNC Machining
Get instant quotes on custom polypropylene machined parts with our Online CNC Machining Service. Make quick-turn prototypes and production parts in days with free standard shipping on all US orders. ISO 9001:2015, ISO 13485, and AS9100D certified. ITAR registered.
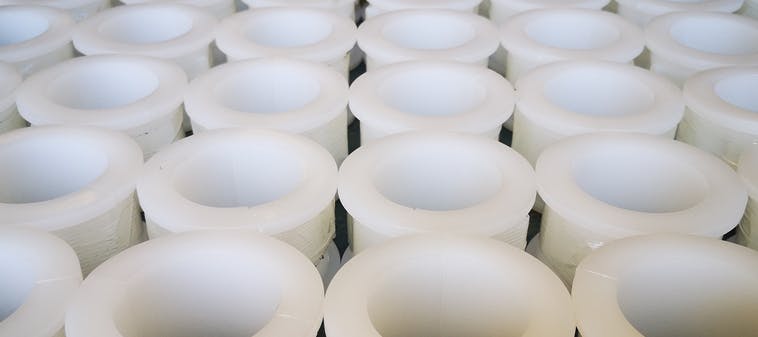
About Polypropylene Machining
Polypropylene (PP) is a semi-crystalline thermoplastic that comes in two different forms; it can be composed of homopolymers or copolymers. Homopolymer polypropylene is the most generic grade whereas copolymer polypropylene has varying degrees of ethylene mixed into it. Machining polypropylene may be more challenging than with other common plastics due to its tendency to gall and melt. Polypropylene’s excellent chemical resistance and fatigue strength make it especially useful for flexible parts and parts that are exposed to corrosive environments.
Polypropylene (PP) is a BPA-free, lightweight plastic with exceptional fatigue resistance and toughness. These properties make it a popular material for use in a wide range of applications across the automotive, packaging, and consumer product industries.
Applications | Advantages | Disadvantages | Lead Time | Price | Tolerances |
---|---|---|---|---|---|
Applications BPA-free food containers, electrical equipment, household appliances | Advantages Low density, chemically resistant to a range of acids and bases, high fatigue resistance | Disadvantages Not suitable for high-temperature applications, degrades when exposed to UV light | Lead Time Starting at 3 days | Price Medium ($$) | Tolerances Standard ±0.010"; ±0.002" are achievable; sub-±0.002" are available after manual review |
Generic Polypropylene
While CNC machining in polypropylene is challenging due to its tendency to gall and melt, homopolymer polypropylene offers a range of benefits for CNC machined parts. Its slick surface makes it ideal for mechanical items like gears and its fatigue resistance means that thin features such as living hinges are easy to incorporate into designs.
Tensile Strength, Yield (MPa) | Elongation at Break (%) | Hardness (Shore D) | Heat Deflection Temperature (°C) | Melting Point (°C) |
---|---|---|---|---|
Tensile Strength, Yield (MPa) 25-40 | Elongation at Break (%) 100-600 | Hardness (Shore D) 65-75 | Heat Deflection Temperature (°C) 100 @ 0.45 MPa | Melting Point (°C) 160-170 |
Note: For reference only. Values can vary slightly depending on the grade, manufacturer, and filler.
Finishes
Polypropylene parts are a natural off-white color. PP does not accept surface finishes like paints very well. Its hydrophobic nature also makes it very difficult to dye.
As Machined: The most common surface finishing option for anyone CNC machining in polypropylene is to simply leave the part in an as-machined state. Machined faces may have visible tool marks.
Bead Blast: CNC machining in polypropylene tends to leave burrs on part edges and the polypropylene easily melts when in contact with the cutting tool, which can result in a sub-par surface finish. Bead blasting helps mitigate this by removing these minuscule imperfections with blasted media that also help remove tooling marks to produce a more consistent and uniform surface finish.
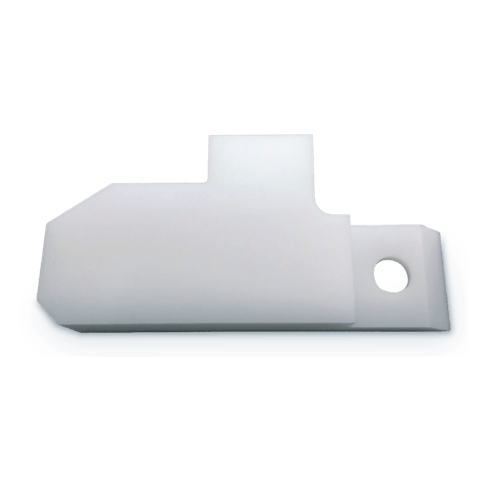
Cost-saving Design Tips
CNC machining in polypropylene can be cost-effective thanks to the low cost of the material. However, reducing excessive machine and post-processing time is critical to keeping costs low. One way this can be achieved is by keeping the tolerances standard:
+/- 0.010” for features of size (length, width, height, diameter)
+/- 0.010” for location (position, concentricity, symmetry)
Avoid calling out tighter tolerances when they are not necessary. This is especially important because machining plastics generates heat, which can cause the plastic to warp or lead to dimensional creep.
Find more design tips in our CNC Machining Design Guide.
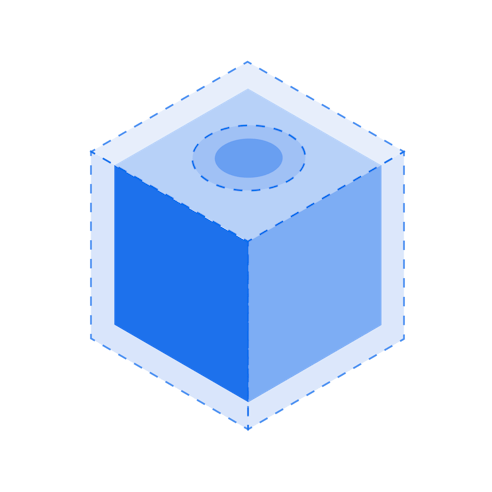
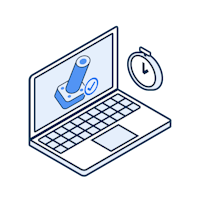