3D printing, more technically known as additive manufacturing, is not as new as people think. It dates back to the 1980s, but in recent years has become a popular manufacturing method for many Xometry customers, including those in aerospace, automotive, architecture, education, jewelry, and art. In medicine and healthcare, it has impressively been used to make prosthetics, medical equipment, and even replacement organs. While Xometry hasn’t 3D printed any organs on-demand (yet?), there are plenty of other applications in this field we have worked on with our medical and healthcare customers.
In this article, we’ll go over everything there is to know about 3D printing in the medical and healthcare industries.
Medicine and Healthcare
First, let’s briefly cover exactly what we mean by medicine and healthcare. These are umbrella terms that refer to all the practices and procedures involved in the prevention, treatment, relief, and cure of illnesses, diseases, injuries, and other medical conditions, both physical and mental.
“Medicine” is used to describe aspects that doctors and medical professionals have to deal with, like prescribing actual medication, treating patients, performing surgeries, and psychiatric services. “Healthcare” is a broader term that covers medicine as well as support services, like pharmacists, therapists, and even those who design and make medical equipment.
3D Printing in Healthcare
Traditional manufacturing in healthcare involves a lot of manual labor to create medical equipment from scratch. The process takes the raw materials and removes sections via grinding, carving, and machining until the final product is made. 3D printing has made the process easier, much less labor-intensive, and sometimes quicker and cheaper.
3D printing doesn’t shape a slab of material to make the products but rather builds them layer by layer using filaments, resins, or fused powders. The product’s designs are typically created using computer-aided design (CAD) software, but it is also possible to create models from 3D scans performed by digital resonance imaging (MRI) machines. In healthcare, you can find both large-scale 3D printing manufacturers like Xometry and point-of-care printing facilities.
A Brief History of 3D Printing in Healthcare
Although it’s not quite 150 years old, the first-ever sign that humans were on the right track when it comes to 3D printing was in the 1860s when François Willème, a French artist, invented the “photo sculpting” method. This involved taking pictures (well, it would have been drawings in those days) of an object from many different angles and then using those images to make a 3D representation.
A whole hundred and some years later, in 1985, an American from Colorado called Chuck Hall invented the first solid imaging process, also known as stereolithography. This was the first step towards the creation of 3D printers. The healthcare industry started using 3D printing in 2000, and a year later the first synthetic scaffolds for human bladder tissue were 3D printed. In 2008, the first-ever 3D-printed prosthetic leg was made.
Since then there have been many advancements in relation to 3D printing in medicine and healthcare. Blood vessels were 3D bioprinted (a process integrating living cells and biomaterials) in 2009, and 3D-printed human liver tissue was commercially launched in 2014. Scientists started bioprinting hearts and lung sacs in 2019. A year later, British biotech company FABRX brought out a personalized medicine-making machine called M3DIMAKERTM. The sector has only advanced since then, with 3D printing being commonplace within medicine and healthcare.
Applications of 3D Printing in Medicine and Healthcare
3D printing has been massively adopted in the medical and healthcare industries, in large part due to the fact that everything can be customized and patient-specific. These include spinal and orthopedic implants, prosthetic limbs, sockets, and parts, dental crowns, bridges, and other orthodontic devices, drug formulations, and delivery devices (i.e., inhalers, patches, and implants), hearing aids, and detailed anatomical models based on real patients and their personal needs.
But that’s not all! It’s commonly used for specialized and patient-specific surgical tools, procedural guides, and even facial reconstruction. What’s more, quick and precise design adjustments can be made using the surgeons’ valuable feedback. 3D-printed implants are made via many different 3D printing processes in a variety of materials—both of which we will cover further down. For now, let’s take a more in-depth look at some of these applications.
Implants
Being able to quickly and accurately design and produce customized implants for patients, including dental, spinal, and hip implants, has greatly improved the world of medicine. These personalized parts have the ability to reduce surgery time, complications, having to manually alter standard-sized implants, and the number of invasive bone graft surgeries that doctors have to carry out. All these factors lead to speedier patient recovery and greater chance of success.
Prosthetics
The ability to personalize 3D-printed prosthetics is undoubtedly one of the most impressive ways the method is being used in healthcare, and it has proved to be a total game-changer for amputees. These parts, which include arms and legs, perfectly match the patient’s body for greater comfort and functionality. Traditional prosthetics and their components are notoriously expensive (anywhere from $1,500 to $8,000) and need extensive and rather invasive regular manual adjustments. Not to mention that they take a long time to be ordered and made.
A 3D-printed prosthetic is often more cost-effective. It also has a quick turnaround time (in some cases as little as a day) and requires much less adjusting thanks to its being completely bespoke. These factors are particularly useful for children who quickly outgrow their prosthetics. 3D printing also helps make the not-very-pleasant process a little more tolerable for children and adults alike as they get to choose the different colors, designs, and styles of their prosthetics.
Anatomical Replicas
In addition to prosthetics, anatomical replicas for use in education, training, and pre-surgery planning can be created. These prints very closely, if not precisely, mimic real organs that are designed from the patient’s actual imaging data to allow the practitioners to rehearse their surgeries before the big event. Complicated surgeries can be simulated, allowing doctors and trainees to improve their skills and confidence for fewer complications, and a greater chance of success. At Xometry we offer full-color printing via PolyJet 3D printing technology, which allows us to create life-like replicas with realistic textures and colors. You can learn more about that technology on our PolyJet service page.
Organ and Tissue Printing
Bioprinting, not a service Xometry offers, has been used to create scaffolds resembling human tissue have been the first step in the manufacturing of 3D-printed organs and tissues. While 3D-printed organs, like livers and kidneys, are not entirely mainstream yet, a lot of progress is being made. Researchers are constantly working on new technologies and approaches to bring these out as soon as possible. These machine-made organs have the potential to save millions of lives as ailing folk won’t need to be put on long waiting lists or just hope for the best.
Other Applications
For greater precision and customization, medical devices and tools specifically tailored to each patient can be (and are being) 3D printed within healthcare. The method is also being used for custom medication doses and formulas. This reduces the chance of unpleasant side effects. As an example, the U.S. Food and Drug Administration (FDA) approved Spritam, an epilepsy drug, made via 3D printing. The process improved this medication and made it easier to dissolve than other pills.
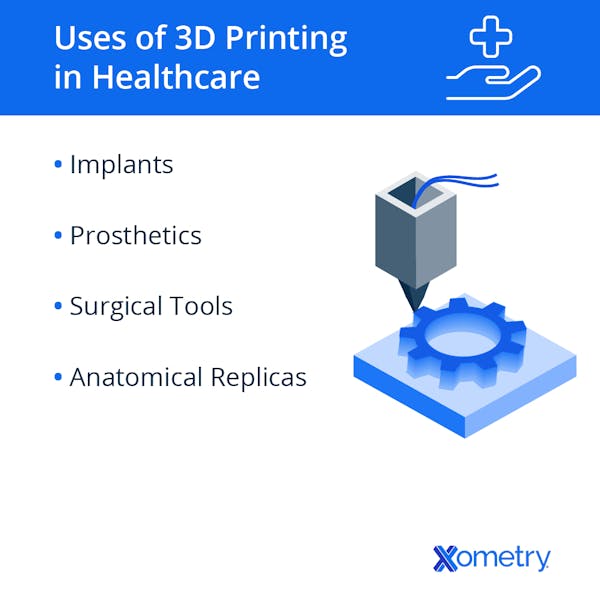
Advantages of 3D Printing Technology in Medicine and Healthcare
Medicine and healthcare have been one of the first industries to adopt 3D printing technology as the advantages are endless. It doesn’t take a rocket scientist to see just how important 3D printing already is, and has the potential to be, in healthcare. The main goal here is to improve patient care and health. Personalized parts, medicines, drug delivery methods, and other solutions based on each patient’s data from MRI and CT scans are greatly changing the way patients are being treated, lowering their recovery times and potential complications, and increasing the chances of success.
3D-printed parts in healthcare are designed to be more compatible with the human body than traditionally made parts and can be more easily adapted to a patient’s exact anatomy and needs. The process allows for the quick creation of necessary medical items, including on-demand manufacturing, which reduces the need for large and expensive inventories, and lowers patient wait times. The speed of 3D printing also means that any design adjustments needed after testing won’t take a long time either. In emergencies, this is an invaluable perk.
Compared to usual manufacturing methods, 3D printing is a lot more eco-friendly and keeps waste to a minimum. It’s also much more cost-effective as not very much manual labor or tools are needed, other than the printer and the material. Thanks to the materials used in 3D printing, parts can be made much lighter and sturdier than traditionally manufactured ones. Surgeons and those still in education can practice surgeries on life-like 3D printed parts, and test new devices and treatments without having to go through the typically long delivery wait times.
As this method gains popularity, it will make healthcare much more accessible for patients, and enable facilities and professionals to do their jobs much more quickly and efficiently.
Get Instant Pricing and Lead Times for 3D Printed Parts
Disadvantages of 3D Printing in Healthcare
While the advantages of 3D printing in healthcare far outweigh the disadvantages, there are a few snags that will hopefully be ironed out and improved as the technology advances. For starters, the range of materials suitable for 3D printing in the field is rather limited in comparison to traditional manufacturing methods. There are also still issues with the consistency in the quality of prints.
In addition, just like with regularly made healthcare items, 3D-printed ones need to go through a copious FDA approval process to ensure they meet all the necessary standards, like quality, safety, and efficiency. More than 100 3D-printed medical items have been already approved by the FDA, but these are mostly medical devices (i.e., orthopedic implants), and not medicines. Professionals in the industry have expressed that the FDA really needs to make relevant adjustments to these regulations to be more specific for 3D printing.
The main problem when it comes to FDA approval is that it focuses more on the 3D-printed products and not the printers, and there aren’t any specific guidelines on how to safely make medicines. Despite the lack of guidance, these products still have to go through the same lengthy testing and approval process as other medical products.
Another issue is that anyone can make medical 3D products if they have a good printer, including those who don’t really have a good grasp on all the FDA’s rules and regulations. This makes oversight quite the feat when compared to trusted 3D printing manufacturers like Xometry. Point-of-care 3D-printed products are also hard to monitor since they are made directly at the hospital or clinic and not at a manufacturing facility.
Further complicating matters, there doesn’t seem to be a clear distinction between medical products and practice. The boards of some medical facilities do all the overseeing when it comes to practice, while the FDA takes care of the products, but with 3D printing, the lines get a little blurred. As an example, if a hospital 3D prints a customized surgical tool, it can be hard to tell whether the oversight is the responsibility of the board or the FDA.
FDA Regulations of 3D Printers and Products
The FDA regulates 3D-printed products for use in medicine and healthcare in almost the same way it does for traditionally manufactured products. However, as stated above, it focuses more on the products and the method and doesn’t regulate the printers. The FDA has a different reviewing process depending on the type of product, what it will be used for, and any potential risks.
The risk level is what the FDA uses to put items into categories. Class I is low-risk and needs minimal oversight, Class II is medium-risk, and Class III is the high-risk category that requires the most thorough testing and review.
3D Printers Used in Healthcare
There are a handful of different 3D printer types used for making healthcare products, each with its own set of pros and cons. Here are the most commonly used 3D printers in the medical industry.
Stereolithography (SLA)
These printers make products by curing liquid resin with lasers. We offer this process for making high-resolution and precise products with smooth finishes. It’s useful making things like prototypes and anatomical models, but it does need some post-processing.
Selective Laser Sintering (SLS)
These printers are preferred for complex and intricate mechanical and custom parts. They have high-powered lasers that fuse powdered material to make the final product. They often print in nylon and other polyamides (PA). SLS nylon prints can be sterilized with the right equipment thanks to the materials ability to handle high heat, making it beneficial for medical devices. Generally these printers are meant for industrial spaces as they are very large and complex machines, however at Xometry we offer it as a standard service, making it easily accessible.
Fused Deposition Modeling (FDM)
After melting a thermoplastic filament, an FDM printer strategically extrudes it onto it’s build platform and builds up layer by layer, until the final product is built. It’s cost effective and great for basic prototypes and simple parts. Its lower resolution means that it won’t be the best choice for complex products, and will likely need more post-processing. The microgaps between the layers also present a challenge for sterilization, so this technology is best kept to prototyping purposes.
Direct Metal Laser Sintering (DMLS)/Selective Laser Melting (SLM)
Both these types of printers have lasers that melt metal powder to create strong and biocompatible parts, like custom implants. They are, however, almost exclusively meant for industrial environments and to be operated by experts. They are also very costly machines to purchase and operate. We offer DMLS printing to our customers so they have an easy way of accessing this powerful printing technology.
3D Printing Materials Used in Healthcare
There are many different materials used for 3D printing in healthcare, all of which need to meet strict safety, quality, and efficiency standards. They must be strong, durable, sterilizable, corrosion-resistant, and lightweight. Not all materials that are 3D printer-compatible are safe for medical use, but here’s a list of the most commonly used 3D printing materials in medicine and healthcare that can meet the necessary requirements:
- Nylon PA-12
- PC-ISO
- ABS M30i
- Titanium
- Cobalt chrome
- Stainless steel
- Thermoplastic polyurethane (TPU)
- Polylactic acid (PLA)
- Polyetheretherketone (PEEK)
- Polyetherketoneketone (PEKK)
- Polymethyl methacrylate (PMMA)
- Bioceramics
- Polyethylene glycol (PEG)
How Xometry Can Help
At Xometry we offer several manufacturing processes that medical and healthcare customers can take advantage of. This includes various types of online 3D printing, CNC machining, urethane and silicone casting, and injection molding services. Xometry is ISO 13485:2016 certified and understands the strict requirements the medicine and healthcare fields require. If you need custom parts, you can get started today by visiting the Xometry Instant Quoting Engine® today!
Copyright and Trademark Notice
- M3DIMAKERTM is owned by FabRx Ltd., a pharmaceutical biotechnology spin-out from University College London (UCL)
Disclaimer
The content appearing on this webpage is for informational purposes only. Xometry makes no representation or warranty of any kind, be it expressed or implied, as to the accuracy, completeness, or validity of the information. Any performance parameters, geometric tolerances, specific design features, quality and types of materials, or processes should not be inferred to represent what will be delivered by third-party suppliers or manufacturers through Xometry’s network. Buyers seeking quotes for parts are responsible for defining the specific requirements for those parts. Please refer to our terms and conditions for more information.
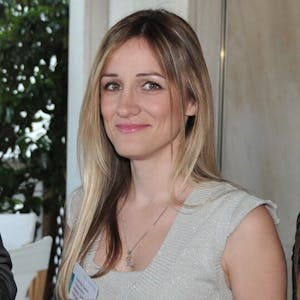