3D printers produce three-dimensional parts via additive manufacturing methods. This technology adds material in layers to produce a 3D object. Most 3D printing software reads a file format known as STL (Standard Tessellation Language or Standard Triangle Language). The STL file format was originally native to 3D Systems’ stereolithography CAD (Computer Aided Design) software, but it has become a 3D printing industry standard. STL prescribes the outer shape of the model object. Before printing a 3D print model, the image must be transformed from the STL format to G-code (referred to as the printing machine code).
This article provides a complete guide to 3D printing STL files, including the process, description, and the format’s pros and cons.
1. Recognize the STL Resolution.
To print a part with the proper specifications, the STL file must be built at an appropriate resolution. STL files define the 3D model’s outer shape by subdividing the surface into interconnected triangles. At higher resolution, the CAD program breaks the model down into smaller triangles so it can more closely approximate the desired shape. Reducing resolution, likewise, creates a less accurate approximation and is thus less desirable. However, there is a balance. As the digital resolution increases, the file size grows dramatically. Large files overtax both the design and printing computer. And since every 3D printer has a physical resolution limit, there is no benefit to exceeding that resolution in the digital STL model.
2. Select the Appropriate Exporting Settings.
The export settings can impact the quality, dimensional accuracy, and surface finish of the 3D printed part. Those settings must be selected in the CAD software before converting the model to STL format. Most programs require you to specify two key settings when you export: the chordal tolerance/deviation and the angular tolerance/deviation.
The chordal tolerance/deviation defines the maximum allowable divergence (in microns) between the as-designed CAD surface and the surface of an STL triangle face. Most experts recommend a chord deviation of about 1/20th of the printer’s layer thickness, but not less than 1 micron.
The angular tolerance/deviation, on the other hand, defines how far the exported model can deviate from any given angle in the CAD model. The standard recommended setting is 15°. Some programs define angular tolerance as a value between 0 and 1 with 0 equating to 15°. Angular tolerance is important in small angular features that might get cut off because they’re smaller than the chord tolerance.
3. Export STL Files From Your CAD Software.
Nearly all CAD programs can export files in STL format, but each one does it a little differently. Most often, the export option will be found under ‘File’ and ‘Save as,’ but it’s best to consult your specific software’s documentation if you’re unsure. The export menu is often where you specify chord and angular tolerances as well as properties like poly count. You may also have the option of saving in binary or ASCII format.
What Is an STL File?
An STL file is the digital file format that 3D printers and slicing programs can read. It defines the surface geometry of the object in a simplified, purely geometrical manner, ignoring aesthetics.
For more information, see our All About STL Files guide.
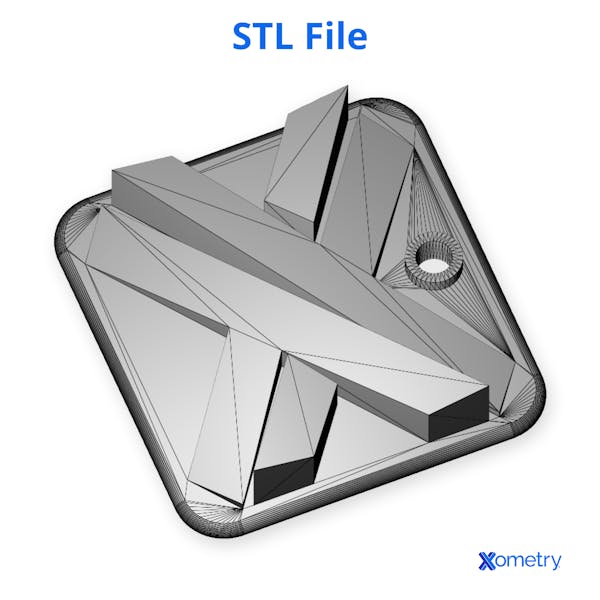
Purpose of STL Files
STL files deliver a description of the 3D model’s outer shape. Aesthetic details such as color, texture, and material are not included in the file contents. The STL export process converts the overall model into a more basic, faceted model composed of triangular polygons. That model can then, in turn, be interpreted by slicing software or by the 3D printer itself.
Why Are STL Files Used by 3D Printers?
3D printers use the simplified STL file format because it is easier to convert into 2D “slices” that can be laid down successively. Though many CAD programs build in their own file formats, STL is compatible with nearly all of them.
Pros | Cons |
---|---|
Pros
| Cons
|
Creating STL Files for 3D Printing
The process of creating 3D printing STL files should follow these general steps:
- Select a suitable CAD application software.
- Create and complete the design.
- Save and export the design into 3D printing STL file format.
- Pick a suitable slicer program.
- Allow the slicer to convert the STL file into a printable G-code.
Modifying the Resolution of STL Files
Modify the resolution of STL files by following the steps below:
- Check the program's configuration. It determines how models are exported.
- Click Save.
- Choose the applicable format (binary or ASCII).
- Choose the optimal resolution or configure it according to the requirements.
Programs that Can Open STL Files
The following types of programs can usually open STL files:
- CAD Software: CAD programs allow you to create solid virtual models to very exact specifications.
- Mesh Editing Tools: Mesh editing tools can modify images, breaking them down into vertices, faces, and image edges. The polygonal array can then be manipulated vertex by vertex if necessary.
- Slicer Software: Slicers turn the STL 3D model into G-code, the digital representation of the 2D slices to be printed one at a time.
Surfaces of a Solid Model in an STL File
STL models typically only represent the outer or exposed surfaces of a 3D object. The surface’s 3D shape is approximated by interconnected triangles, but the format doesn’t inherently represent the object’s inner composition. The STL object can be interpreted by the computer as solid, however, if it is configured as such beforehand. The simplest way to do so is to define it as solid in the original CAD program; that solidity should carry over when it is converted into STL format. If, however, your starting point is already an STL file, your CAD program should have an option to “fill it in.” This generally works fine if the outer surface contains no gaps or holes in the 3D object’s interior. If there are gaps, you may have to close them off before the model can be rendered “solid.”
Disclaimer
The content appearing on this webpage is for informational purposes only. Xometry makes no representation or warranty of any kind, be it expressed or implied, as to the accuracy, completeness, or validity of the information. Any performance parameters, geometric tolerances, specific design features, quality and types of materials, or processes should not be inferred to represent what will be delivered by third-party suppliers or manufacturers through Xometry’s network. Buyers seeking quotes for parts are responsible for defining the specific requirements for those parts. Please refer to our terms and conditions for more information.
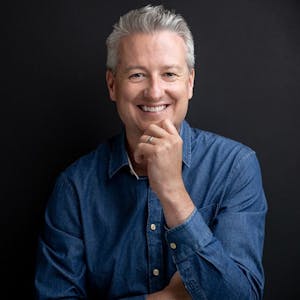