CNC machining and 3D printing are extremely prominent manufacturing methods today, not only here at Xometry but globally. While they differ in almost every way, they’re direct competitors for the creation of solid parts, and among their biggest differences is that one method works by removing material, while the other adds it layer by layer. Let’s find out more.
3D Printing Definition and Comparison to CNC Machining
Also known as additive manufacturing, 3D printing actually refers to a family of processes that work similarly. A model is designed on a computer and then sliced into different parts. The thickness is set according to what machine and settings are used, and the printer will take that information and build each layer until the entire part is finished. That’s how it can turn a series of 2D steps into a 3D object—by adhering each layer to the one beneath it and bonding them internally, too. These machines can usually work with many different materials, some of which include extruded polymer filaments, light-sensitive resins, laser-melted powders, filament feedstock, waves, and biological materials.
To produce parts with additive manufacturing, you’ll need more than just a printer. You’ll also need a CAD (computer-aided design) package to make your design and save it as an STL (stereolithography) file. A slicer software package will then use that STL file to give the printer a series of 2D instructions to make the part. 3D printing systems first started creeping into the market in the late 1980s, though nowhere near as efficient and widely compatible with materials as modern 3D printers are. The following image is an example of an FDM 3D printer:
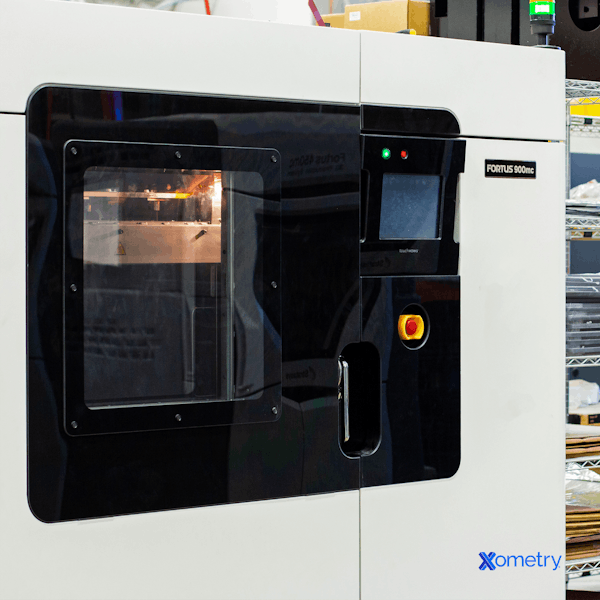
There are several reasons why 3D printing is so popular, starting with the fact that it’s relatively quick to set up and doesn’t cost crazy amounts of money to make complex shapes. It also doesn’t require any intervention during the process—you can just let it do its thing until it’s finished. Also, many 3D printers are office- and beginner-friendly.
Some potential drawbacks, though, are that 3D-printed parts can vary significantly in strength, especially when compared to the strength of the original material. For example, if you were to use FFF (fused filament fabrication) to print an ABS (acrylonitrile butadiene styrene) part, it might only be about 10% as strong as solid ABS. But something like SLS (selective laser sintering) using nylon can result in close to 100% as strong as solid nylon. Also, 3D printing is good for dimensional accuracy but can be tricky when it comes to extremely precise parts and features, and it struggles with smooth surfaces, especially when it comes to the Z-resolution (the layer height), which can create visible steps on sloped or curved surfaces.
What are the Advantages of 3D Printing Compared to CNC Machining?
The advantages of 3D printing compared to CNC machining are:
- 3D printing delivers net shape parts quickly, whereas CNC machining requires individual setup and (generally) manual programming plus supervision.
- 3D printing is generally a lower-cost method than other ways of making complex net shapes. It requires minimal setup and operational intervention. It’s common for CNC components to be 10x the price of 3D printed parts.
- 3D printers that are office friendly and require only modest skills in setup and maintenance are increasingly common. They are also increasingly capable of satisfying the majority of needs. CNC remains a heavy-engineering and highly skilled process requiring constantly refreshed skills in the operators.
What are the Disadvantages of 3D Printing Compared to CNC Machining?
The disadvantages of 3D printing compared to CNC machining are:
- Various 3D printing processes offer varied strength compared with the “native” properties of the materials. For example, as low as 10 % of material UTS for FFF in ABS is reported, and as much as 100% for SLS of nylon. CNC machining produces parts in undisrupted native materials, so the strength is generally high.
- 3D printing can achieve good dimensional accuracy, but where high precision is required it can be challenging. CNC machining is highly precise and allows improved accuracy by slower processing.
- 3D printing is generally affected by process mechanics concerning surface finish. Z-resolution in particular brings stepped surfaces and visual disruptions. CNC surface finish is as machined; it can be extremely uniform and highly precise if cutter paths are programmed for a smooth finish.
CNC Machining Definition and Comparison to 3D Printing
A computerized manufacturing process, CNC (computer numerical control) machining uses software and codes that have been programmed beforehand to control the movement of several cutting and shaping tools like lathes, mills, and grinders and create a variety of CNC machining parts. The idea is credited to James Parson, who was trying to find a better way to make helicopter and aircraft blades. In 1958, Richard Kegg, along with MIT engineers, created the first CNC milling machine. Even though the process can be rather expensive and complicated to set up, it’s worth it if you want to make high-quality and durable parts with smooth surfaces. You can learn more about CNC machining by reading our dedicated article. Here’s what a CNC machine looks like:
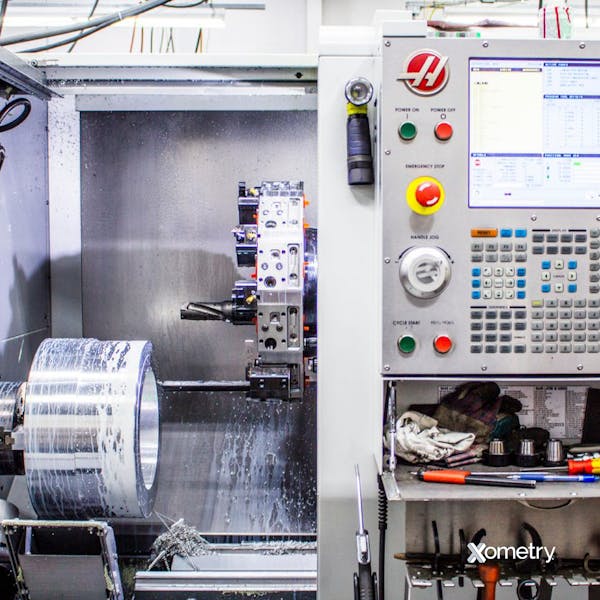
Aside from producing parts that are more precise, CNC machining uses engineering materials that maintain their full properties with no disruptions by the process. As with anything, though, there are a couple of potential downsides to this method. It usually needs fixtures or mounts to hold the workpiece in place securely, and designing and setting up these mounting tools—also called jigs—can be tricky and require both time and money. This is much more complicated than 3D printing, which simply prints on a moving bed. Also, CNC machining cuts away material that’s no longer needed, ultimately creating waste. This doesn’t happen in 3D printing.
What are the Advantages of CNC Machining Compared to 3D Printing?
The advantages of CNC machining compared to 3D printing are:
- CNC machining uses engineering materials and delivers the full properties of the materials, undisrupted by the process. 3D printing, on the other hand, can sometimes achieve this, but generally uses weaker material approximations.
- CNC parts are more precise, as machine tolerances can be held closer than 3D print tolerances.
What are the Disadvantages of CNC Machining Compared to 3D Printing?
The disadvantages of CNC machining compared to 3D printing are:
- CNC machining often requires mounting tools to be made. This complicates the job considerably, whereas 3D printing makes free floating parts built on a table or scaffold.
- CNC machining cuts away not required material, making ‘waste’ in the cutting. 3D printing is characterized as a ‘low waste’ option.
Attribute | 3D Printing | CNC Machining |
---|---|---|
Attribute Unlimited material availability | 3D Printing No | CNC Machining Yes |
Attribute Part design | 3D Printing Unrestricted by process constraints | CNC Machining Limited by undercut and internal access, tool path and type, axis-defined minimum radii, and the need for repositioning mid-task |
Attribute Precision | 3D Printing Processes vary from 0.016 resolution to 1 mm+. Typically around 0.2 mm. | CNC Machining 0.005 mm precision, especially when using a slow feed, new cutters, and shallow cuts. |
Attribute Operator skill | 3D Printing Usually low | CNC Machining Very high |
Attribute Speed of build | 3D Printing Low setup time, but build time can take hours | CNC Machining Can take ages to set up and program, but cutting can be very fast |
Attribute Surface finish | 3D Printing Grained, rough, and stepped, and features can be blurred quite often | CNC Machining Can create very high-quality surfaces by taking longer to cut |
Attribute Strength | 3D Printing Typically 10–20% of native material | CNC Machining Usually stays at 100% of the native material |
Attribute Cost example | 3D Printing $50 per part for a small, simple design | CNC Machining $250–$500 per part for the same design (unless you use Xometry) |
3D Printing vs. CNC Machining
3D printing offers advantages in terms of cost and time to build parts. CNC machining, on the other hand, can deliver a close correlation to mass production characteristics whenever the precision of the part is a critical factor.
3D Printing vs. CNC Machining: Lead Cost Comparison
CNC machining will carry all of the programming and setup costs and it will be expensive in comparison to 3D printing – often five to ten times the price. However, whenever a series of prototypes with small adjustments are required, the modified CNC-cut parts will carry a much lower setup cost, whereas a second 3D printed part will cost the same as the first.
3D Printing vs. CNC Machining: Speed Comparison
Preparation for the printing of a 3D component requires little time to set up before a print can commence. Although printing is slow by some measures, most prints will likely complete within a few hours and be ready to use. CNC machining, on the other hand, requires skilled preparation of programming for cutter selection and cutter path. It often requires custom or modified jigs to retain the part during processing (including possible repositioning of the part). This can consume considerable time before the first cut. Cutting, however, is generally fast, and complex parts can generally be completed in an hour or less of actual machining. Total time for preparation and machining can run into a day or more, depending on complexity.
3D Printing vs. CNC Machining: Volume Comparison
When the extensive setup effort can be shared over multiple parts, CNC machining can produce more cost-effective parts compared to 3D printing. 3D printing has fewer volume advantages, as each part takes the same material and machine costs, irrespective of volume.
3D Printing vs. CNC Machining: Materials Comparison
In material selection (and successful delivery of material properties), CNC offers better options. Essentially the material choice is open to all engineering materials, up to and including spark-erosion CNC machining of pre-hardened tool steels. CNC-machined parts deliver the native properties of the billet material, largely undisturbed by processing characteristics.
3D printed parts are restricted to those supported by particular processes. The construction methods of the particular 3D print technology impose severe restrictions on the delivery of properties. Prints are often weakened by anisotropic “grain” in the construction method, porosity, poor layer bonding, and the substitution of printable but non-engineering materials.
Frequently Asked Questions About 3D Printing and CNC Machining
What are the Mutual Alternatives to the 3D Printing and CNC Machining?
Yes, of course. An alternative that could potentially fit both of these is injection molding, in that it’s a single-operation process that can produce parts that are identical to their 3D file. But making the molds for this can be rather expensive and time-consuming, so it’s only really worth it if you’re making a ton of parts. So ultimately, especially when compared to day-to-day 3D printing jobs, injection molding isn’t all that practical.
What are the Similarities Between 3D Printing and CNC Machining?
3D printing and CNC machining are similar in that both processes can produce functional products. In terms of processes, however, 3D printing and CNC machining do not have anything in common.
What are the Other Comparisons for 3D Printing Besides CNC Machining?
Some types of 3D printing use lasers, like SLS (selective laser sintering), DMLS (direct metal laser sintering), and SLM (selective laser melting), and, just like laser cutting, it’s also used in many industries and works with lots of different metals. But laser cutting uses that same laser to engrave or cut away material from a workpiece, rather than build up. You can read more in our article all about their differences.
What are the Other Comparisons for CNC Machining Besides 3D Printing?
Similarly to CNC machining, die casting is another great way of making complex metal parts. But die casting is really not cheap, especially when it comes to tooling costs. If you’re interested in huge production runs, though, the cost comes down, making it a more comparable option.
How Xometry Can Help
If anything in this article is unclear to you, or you’d simply like to learn more about either of these methods, other manufacturing processes, or about us here at Xometry, why not reach out to one of our representatives? In addition to online CNC and 3D printing, we offer a huge range of related services, including laser cutting and powder coating. You can request a free, no-obligation quote directly from our website today!
Disclaimer
The content appearing on this webpage is for informational purposes only. Xometry makes no representation or warranty of any kind, be it expressed or implied, as to the accuracy, completeness, or validity of the information. Any performance parameters, geometric tolerances, specific design features, quality and types of materials, or processes should not be inferred to represent what will be delivered by third-party suppliers or manufacturers through Xometry’s network. Buyers seeking quotes for parts are responsible for defining the specific requirements for those parts. Please refer to our terms and conditions for more information.
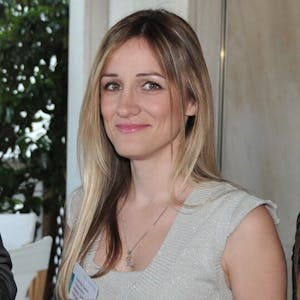