Brittle failure is the sudden fracture of a material with minimal plastic deformation. This can be a dangerous situation since there is little to no warning that failure is about to occur, and cracks in the material propagate quickly. Brittle failure can occur for several reasons, including environmental factors such as low operating temperatures (which can cause a ductile-to-brittle transition in metals), material imperfections like inclusions and grain structure defects, and inadequate design that leads to stress concentrations or insufficient load-bearing capacity.
Engineers need to understand the mechanisms behind brittle failure so that appropriate measures can be taken to prevent it. Preventive measures include operating structures within their safe temperature range, performing regular inspections to detect and mitigate cracks, selecting materials with high fracture toughness, and optimizing designs to reduce stress concentrations (e.g., avoiding sharp corners and using appropriate load distribution techniques). This article will discuss brittle failure, from what it is, to what causes it, to how to prevent it.
What Is Brittle Failure?
Brittle failure is the sudden breakage of a material characterized by little to no plastic deformation of the material, and rapid crack propagation. While brittle materials may exhibit high strength, they absorb less energy before fracture than ductile materials. Small impact loads can initiate brittle fracture, especially in materials with pre-existing defects or when operating below the ductile-to-brittle transition temperature (DBTT).
What Does Brittle Mean?
In materials science, brittle is a term that describes a material that, when subjected to stress, fractures with no or minimal plastic deformation. In contrast to ductile materials, which experience varying degrees of plastic deformation before breakage with applied loads, brittle materials fracture with minimal plastic deformation, often failing before significant yielding occurs.
What Happens When Brittle Failure Occurs?
In brittle materials, failure begins with the creation of a crack at a defect or point of concentrated stress in a part. Cracks propagate quickly in a direction nearly perpendicular to the direction that the stress is applied. This is called cleavage, or the splitting of the atomic bonds in the crystal structure of the material along definite planes. Once cracks propagate beyond a critical size, the material fractures, sometimes producing an audible snap, depending on the material type and fracture speed. This process occurs rapidly, often in milliseconds, depending on the material and loading conditions.
What Does Brittle Failure Look Like?
Brittle failure appears as cracks propagating nearly perpendicular to the applied tensile stress, with minimal plastic deformation in the material. This results in a fracture surface that is relatively flat compared to the rough, fibrous surface seen in ductile failure, though some brittle materials may exhibit granular or cleavage patterns. In brittle failure, V-shaped chevron marks often form in metals near the center of the fractured cross-section and point toward the origin of crack initiation. These markings are particularly useful in forensic failure analysis.
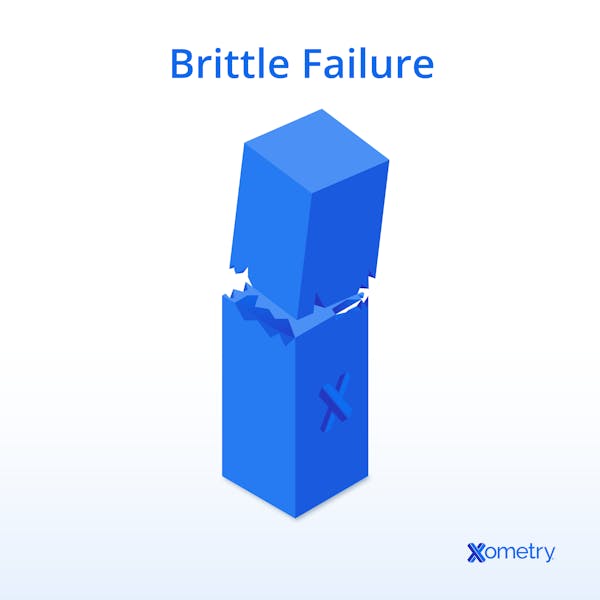
What Are the Causes of Brittle Failure?
While some materials are inherently brittle due to their chemical composition, some normally ductile materials become brittle under certain conditions. The four main causes of brittle failure are listed below:
1. High Material Thickness
Material thickness influences stress distribution, and thicker sections can experience triaxial constraint, which limits plastic deformation and increases susceptibility to brittle failure. Each of these stresses is perpendicular to the other, and the material will deform along each of these axes when loaded. For example, a material that is under tension will be stretched in the direction of the applied force but will shrink in the directions perpendicular to the force.
In thicker materials, plastic deformation is restricted due to triaxial constraints; when under tension, the material cannot effectively deform in the directions perpendicular to the applied force, resulting in brittle fracture when the tensile force is sufficiently high. A brittle fracture occurs, and a flat surface oriented perpendicular to the load is created when the tensile force is sufficiently high to cause a fracture.
2. Colder Operating Temperatures
At colder temperatures, the thermal energy of a material is reduced. This means that the atoms of a material are less excited and their movement is restricted. Therefore, the material is less likely to plastically deform, since its atoms tend to resist dislocating when a load is applied. This contributes to brittle behavior and is a common reason why normally ductile materials experience brittle failure.
3. Metallurgical Degradation
There are many factors that contribute to metallurgical degradation. Examples include thermal effects, hydrogen embrittlement, and intergranular corrosion. Cold temperatures can embrittle a material, as explained before. Hydrogen embrittlement reduces ductility by weakening atomic bonds and promoting crack formation, particularly at grain boundaries and dislocations. This makes the material more brittle since it makes the material more resistant to deformation. Intergranular corrosion can also embrittle a material. This is because of the corrosion of the grain boundaries of the material. Corrosion causes the boundaries to weaken, making cracks propagate much easier through the material’s grains. Each of these factors contributes to metallurgical degradation and can embrittle a material.
4. Steel Cleanliness and Grain Structure
The alloying elements present in steel and its grain structure have a big impact on its brittleness. Alloying elements affect the metal’s microstructure since the atoms of the alloying element (impurities) squeeze between the atoms of the metal. Metal can be modified to have desired properties that it normally wouldn’t have if it were in its pure form. The modification will depend on the concentration of the impurities, the alloying element, and the temperature at which the impurities are introduced. Some impurities promote grain growth, which can increase brittleness by reducing grain boundary resistance to crack propagation. However, other alloying elements can refine grain structure and improve toughness. Cracks propagate more quickly through large grains since there is less resistance by the material.
How To Prevent Brittle Failure?
To prevent brittle failure, consider the items listed below:
- Control the Operating Temperature: Maintaining operating temperatures above the material’s ductile-to-brittle transition temperature (DBTT) prevents embrittlement. The DBTT varies by material, and certain steels become brittle at sub-zero temperatures.
- Increase Material Toughness: Material toughness can be improved by various heat treatment methods. Examples of heat treatment include: tempering, annealing, quenching, and precipitation hardening. The toughness of the material will increase to varying levels depending on the type of heat treatment process used. In general, however, heat treatment processes reduce the material’s grain size and make it less susceptible to cracking.
- Design Structures to Have Smaller Cross-Sections: Design parts to avoid abrupt thickness transitions and stress concentrations. While smaller cross-sections may allow for more plastic deformation, the primary factor in brittle failure is stress distribution and material selection. The Poisson effect describes lateral contraction when a material is stretched, but it is not the main cause of brittle failure. When stretched in one direction, structures with thicker cross-sections do not deform much in the other two directions. This leads to brittle failure.
- Avoid Using Parts That Are Inherently Brittle: If possible, avoid parts that are overly brittle. Brittle materials are sometimes preferred in abrasive applications where parts rub against each other or in applications where compressive strength is ideal. This is because brittle parts are typically harder, which makes them more wear-resistant. Additionally, brittle materials are often strong when subjected to compressive loads due to the atoms’ resistance to dislocation. If it can be achieved, use tougher and more ductile materials that have sufficient strength to fulfill the application to prevent brittle failure.
- Minimize Defects in the Part: All defects can increase stress concentrations in parts and make it easier for cracks to form. For example, marks and nicks leftover from machining processes and voids in castings can allow cracks to form more easily.
How to Fix Brittle Failure?
If catastrophic brittle failure has occurred, it is not possible to fix the broken component. The component must be replaced. However, in larger structures such as bridges that are composed of several structural and load-bearing members, the failure of one member does not compromise the integrity of the entire structure. Cracks may exist in structural members due to brittle failure or fatigue, but propagation is stopped or arrested by a crack arrestor. In some cases, arrested cracks can be temporarily repaired by welding, but improper welding can introduce residual stresses and further embrittlement. Specialized techniques, such as stress-relief heat treatments, may be required. Design modifications of the structure are required to prevent the cracks from appearing again.
What Are Some Examples of Brittle Materials?
Some examples of brittle materials are listed below:
- Cast iron
- Martensitic steel
- High-carbon steel
- Alkali metals, when sufficiently cold
- Ceramics
- Glass
- Graphite
- Concrete
What Are the Types of Brittle Failure?
There are two types of brittle failure, as described below:
- Transgranular: In transgranular brittle failure, the crack travels through the grains rather than along the grain boundaries, often changing direction to follow the planes of least resistance within the crystal lattice.
- Intergranular: In intergranular brittle failure, cracks propagate along the grain boundaries. This mode is typical when the grain boundaries are weakened, for example by corrosion or impurity segregation.
What’s the Difference Between Ductile Failure and Brittle Failure?
The main difference between ductile failure and brittle failure lies in the amount of plastic deformation prior to fracture. In ductile failure, significant deformation is evident, often with necking and tapered fracture surfaces, indicating that the material absorbed energy before breaking. In contrast, brittle failure occurs with little to no plastic deformation, resulting in a relatively flat fracture surface that lacks the tapering seen in ductile failure. For more information, see our guide on Ductile Failure.
Summary
This article presented brittle failure, explained what it is, and discussed how to manage it. To learn more about brittle failure, contact a Xometry representative.
Xometry provides a wide range of manufacturing capabilities, including 3D printing and other value-added services for all of your prototyping and production needs. Visit our website to learn more or to request a free, no-obligation quote.
Disclaimer
The content appearing on this webpage is for informational purposes only. Xometry makes no representation or warranty of any kind, be it expressed or implied, as to the accuracy, completeness, or validity of the information. Any performance parameters, geometric tolerances, specific design features, quality and types of materials, or processes should not be inferred to represent what will be delivered by third-party suppliers or manufacturers through Xometry’s network. Buyers seeking quotes for parts are responsible for defining the specific requirements for those parts. Please refer to our terms and conditions for more information.
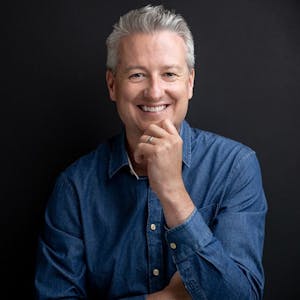