Fused Deposition Modeling (FDM) is a 3D printing technology that builds a part layer by layer by depositing heated thermoplastic along an extrusion path. In this process, there are several different ways the interior areas of a part can be interpreted when the part is built. Infill describes how those interior areas of a part should be filled in.
Xometry offers three types of infill options: ultralight, light, and solid, each with its own properties. When quoting a part to be made in the FDM process, you will see these options listed under "Material Options".
We simultaneously built examples of an identical FDM part with the three different infill options. We paused the build mid-way to produce these cross-section examples to help you determine the best option for your project.
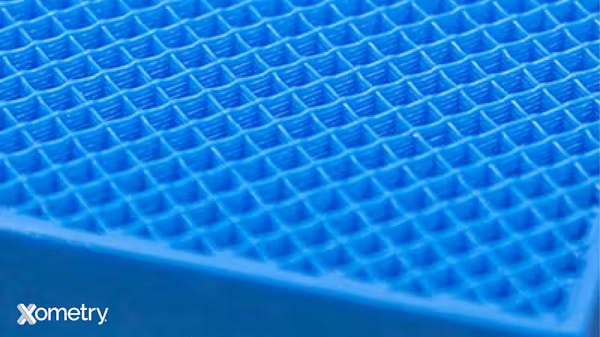
Xometry’s ultralight infill parts are filled with a single zig-zag pattern. This is the lightest and least expensive infill option.
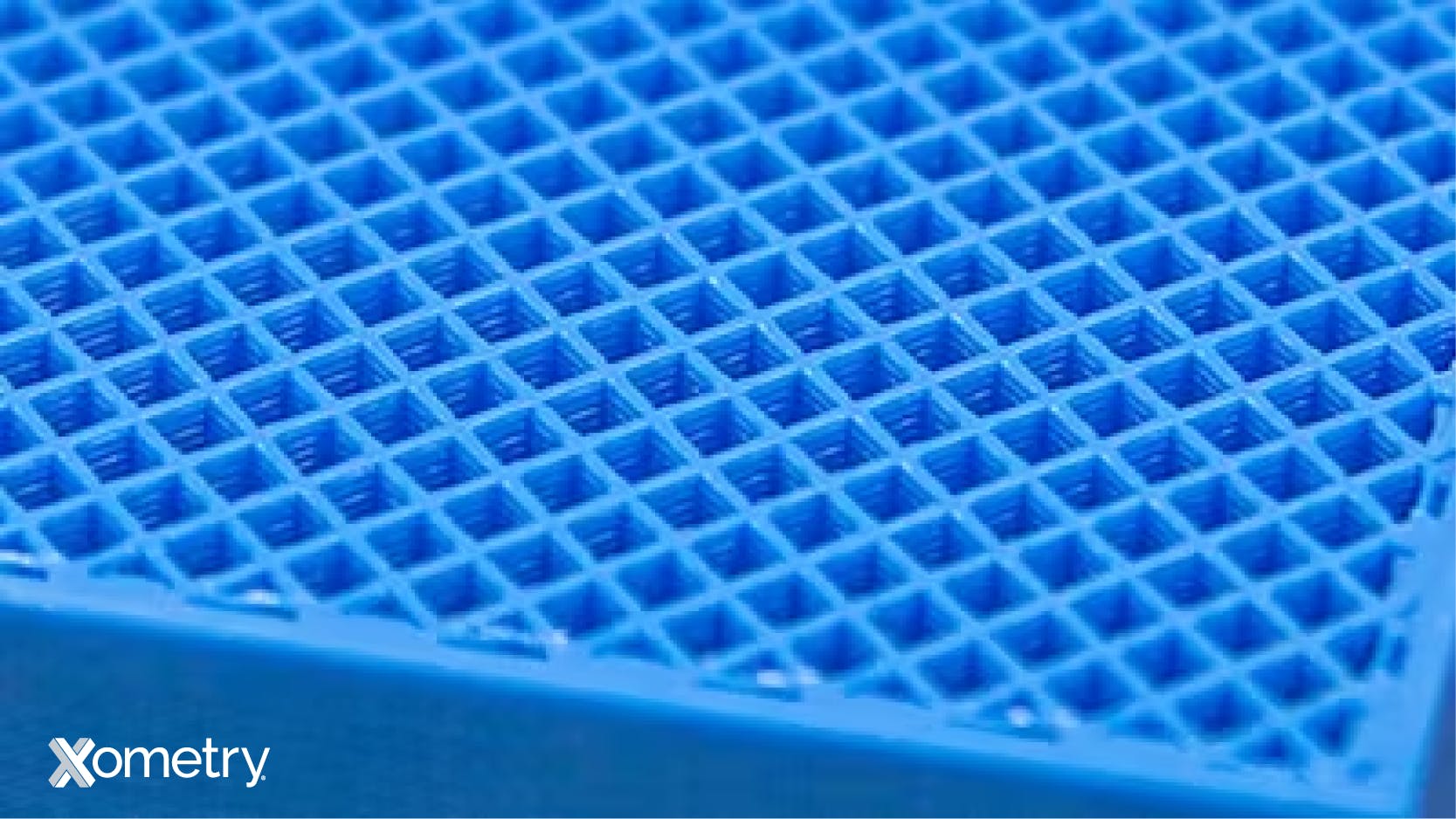
Xometry’s light infill parts are filled with a double cross-hatch pattern. This option provides increased rigidity and is lighter than a complete solid infill.
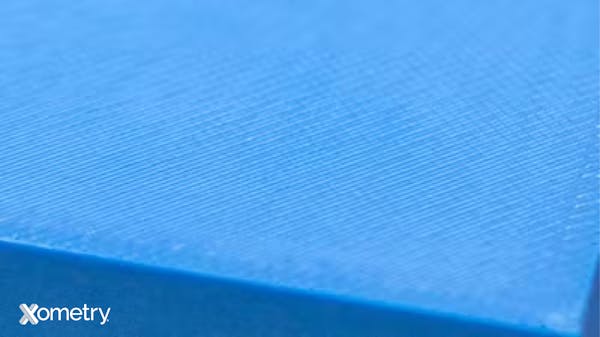
Xometry’s solid infill parts are completely filled for the highest density. This is the heaviest and more expensive option but offers the highest strength.
Takeaways
If you are looking to reduce the part weight as much as possible, then you may want to consider the ultralight infill option. If you are looking to get a part that is as strong and dense as possible, the solid infill option would be most appropriate. The light infill option offers a happy medium between weight and rigidity of the part.
