The DXF (Drawing Interchange(X) Format) is among the most common formats for CAD and CAM packages. While it can represent 3D wireframes, the format is predominantly used for 2D applications in practice. Its main role is serving as an interoperability tool to share models and drawings across incompatible CAD programs. Being a vector system, it reproduces precisely, without the degradation that is common in some formats.
This universal interoperability means that virtually any 2D and 3D CAD viewer, file converter, design package, or CAM machine can handle input data in DXF format and produce a precise interpretation of the original. It is in CAM (Computer Aided Manufacturing) tools that DXF matters most. Many CNC tools use DXF directly to generate the G-code they require as machine instructions.
This article seeks to answer the question “What is a DXF file?” and considers the history, importance, file types, and applications of use.
What Is a DXF File?
A DXF file is a CAD format mostly used by engineers, designers, and architects for drawings during product design and manufacturing. It is the first universal 2D CAD format launched by Autodesk in 1982. While DXF can handle 3D files, it is important to remember that it can only work in 3D with data that was saved as 3D DXF. As previously mentioned, 3D DXF files are not common. Furthermore, they are not advised for certain engineering fields like mechanical engineering. In many cases, what is referred to as 3D DXF is nothing more than 2D projections of a 3D geometry (e.g., this is how SolidWorks exports 3D geometry to DXF).
DXF began as a vector file construction. This means that you can zoom in on a DXF file, and the resolution of the view remains unaltered until the zoom limit is reached. It is worth noting that during format conversion, it is very common for the scale/dimension units to be lost. Therefore, when making an STL file, be careful that your model hasn’t become 100 m across rather than 100 mm.

How To Convert a DXF File
A DXF file can be converted using installed apps and online tools. The steps in converting a DXF file will vary depending on the app and online tool being used. It is recommended to check the specific steps per app/tool before converting a DXF file. For more information, see our guide on how to Convert a DXF File to STL.
How Do I Open a DXF File?
- A DXF file can be opened using a viewer or CAD/CAM software. For instance: one can use the Autodesk online viewer by simply dragging and dropping the DXF file or browsing to locate and upload it.
How Can I Make a DXF File?
Creating a DXF file is the result of a save-as or export action in the range of 2D or 3D design, visualization, and rendering packages. Because DXF has such a long history, there are sometimes complications in the way CAD packages handle the format. However, when saving a file to transfer it to a CNC supplier or a home CAM machine (vinyl cutter, laser engraver, etc.), DXF is a reliable and widely trusted tool. Since the vast majority of CAD tools support exporting DXF files, it is best to refer to the specific user manual of the chosen package, as the process will depend on the individual tool. When exporting 3D geometry, care must be taken to ensure that a true 3D file is exported, as opposed to 2D projections of the 3D geometry. In the latter case, if the tool does not allow exporting a true 3D DXF file, opting for a different 3D format like STL or STEP is advisable.
What Is the Importance of a DXF File?
DXF is one of the formats that allows divergent design tools to communicate for design sharing. It provides precise and reliable information to the full range of CNC and CAM equipment to manufacture products as designed.
What Are the Types of DXF Files?
DXF files have existed in two formats historically—exclusively ASCII from 1982 to 1988 and binary and ASCII from 1988. Current DXF tools that operate the openly documented file structure correctly can handle both types. DXF originated as a 2D drawing format to allow organizations outside Autodesk to use their data without getting proprietary DWG format data. The extension of DXF format to 3D enabled the sharing of basic 3D files as the wider CAD market (and AutoCAD) evolved. However, 3D capabilities in DXF remain limited compared to more advanced formats like STEP or IGES. Therefore, the main practical use of DXF files is in 2D applications, making them more suitable for production processes like sheet metal cutting or folding rather than 3D printing.
What Are the Best DXF File Converters?
Some of the best DXF file converters are:
- Bear File Converter: The Bear File Converter is a reliable and easy-to-use tool that will handle DXF to STL conversions for files of 50 MB or less. Bear also handles conversion to DXF well.
- Filestar: The Filestar DXF to STL converter is an installed, lightweight tool that avoids complications. Though it is not widely known, it is well supported and performs its task well.
- FreeCAD: FreeCAD is equipped to perform a wide range of file conversions and, with a little practice, will allow users to do much more than simply convert file formats.
What Are the Best Applications for DXF Files?
There are many applications that allow more than just viewing and reviewing DXF files. Below are some of the best applications:
- SolidWorks is a leading professional design package that puts massive 3D power within easy reach. Icon-driven menus make it easy to learn the basics. The downside is that it is expensive, with a fee of approximately $3,000 per year for commercial use.
- FreeCAD is a free and modest package that will provide powerful design capabilities and allow rapid skill development. It is widely used and well-liked, with a great online community and many free DXF files.
Is a DXF File the Same as a CAD File?
Yes, a DXF file is the same as a CAD file in that DXF is a CAD format. However, the DXF file format was specifically created to allow AutoCAD users to provide data to non-AutoCAD users and manufacturers without sending out their “native” DWG data. DXF is not a design format. Design is carried out in one of a wide range of CAD packages with a native format. DXF contains (almost) all of the design data and is widely accepted as a CAD communications tool. As already mentioned, in practice it is mostly used for 2D applications rather than 3D.
What Is the Difference Between a DXF and an STL File?
DXF and STL files have several differences. STL 3D printer files store a 3D form as a series of 2D polygons (generally triangles) with standardized X-Y-Z coordinates for the corners. It also has a “unit normal” line of length 1 unit to indicate the outer face. DXF, on the other hand, stores the definitions of edges and curvature as pure mathematical functions. This approach produces a much higher precision interpretation of a 3D shape, however complex. Another difference is that STL will often mishandle the common axes of two polygons and make them coincident but not joined. This results in a file fault that must be repaired. DXF is very precise in the joining of surfaces, as the correlation line between them is defined mathematically—and only once. STL is a simple and lightweight system that generally contains only sufficient data to reproduce a body’s surface. This representation is approximated by a linear and angular resolution (triangle size) that is defined as the file is created. DXF is a much more content-heavy format that describes a part or assembly at very high resolution at all times. Additionally, STL can carry color information in binary format, but this facility is rarely used. DXF applies a color number to each mathematically generated surface, and this information is intrinsic to the file format.
Finally, as the name suggests (STL stands for Stereolithography), STL files are specifically designed for 3D printing. In contrast, DXF files are primarily used in practice for 2D-based processes such as profile cutting or sheet metal folding.
Summary
This article provided a review of the DXF file format, including its history, uses, and importance. To learn more about the DXF file format and how you can use it for your projects, contact an Xometry representative.
Xometry provides a wide range of manufacturing capabilities, including 3D printing and other value-added services for all of your prototyping and production needs. Visit our website to learn more or to request a free, no-obligation quote.
Disclaimer
The content appearing on this webpage is for informational purposes only. Xometry makes no representation or warranty of any kind, be it expressed or implied, as to the accuracy, completeness, or validity of the information. Any performance parameters, geometric tolerances, specific design features, quality and types of materials, or processes should not be inferred to represent what will be delivered by third-party suppliers or manufacturers through Xometry’s network. Buyers seeking quotes for parts are responsible for defining the specific requirements for those parts. Please refer to our terms and conditions for more information.
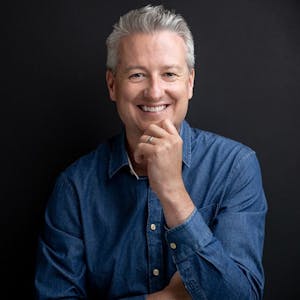