Both DXF (drawing exchange/interchange format) and STL (stereolithography or standard triangle/tessellation language) are traditional file formats used in design and 3D printing. DXF files typically represent detailed 2D and 3D designs and can accurately exchange data between CAD programs, while STL files are mainly used for 3D printing and focus on representing a part’s outer surface (which it does as a mesh of triangles). Converting one to the other is actually a very straightforward process, and we provide the exact steps a little further down. First, let’s have a brief look at how these files work and what they’re used for today.
What is DXF?
Originally developed in the early 1980s as the native file type for the AutoCad design package, DXF was created to be interoperable and usable across various CAD software applications—the first of its kind at the time. When it was released, it impressed users with the way it stored 2D (and later 3D) design data so efficiently. AutoDesk wanted to make a file type that would become the universal standard CAD data storage, something the company managed with DXF; it not only survived the shift from 2D to 3D but thrived and maintained its relevance. It’s also a widely trusted interchange tool between CAD and CAM as it provides error-free, highly accurate data and is user-friendly, too.
DXF files organize all the information from the 3D data into “group codes” and “value pairs” and then separate these into graphical (i.e., line types) and non-graphical (i.e., settings) objects. By keeping all this information, DXF files can represent a complete design, whether in 2D or 3D.
If we were to break down the information in a DXF file, it would look something like this:
File Part | Description |
---|---|
File Part Header | Description Info like the AutoCAD version with which it was created, dimension types for both angular and linear measurements, and other settings |
File Part Classes | Description Details relating to application definitions for blocks, objects, and entities |
File Part Tables | Description Line types, fonts and styles of text, user coordinate systems, viewports |
File Part Blocks | Description Groups of graphical and drawing entities |
File Part Entities | Description Actual object data that describes each entity separately |
File Part Objects | Description Non-graphical info like AutoCAD dictionaries |
DXF File Information
Sometimes, parts from these categories will be null, so they won’t have any content if they’re not needed. But the more complex a part is, especially when it comes to curvature or manufacturing data, it’s all pretty important. The following illustration shows a 2D DXF file:

What is STL?
STL is considered the standard file type that most 3D printers use today. It’s pretty old and doesn’t contain information on color or texture. It works by storing points on the surface of an object as geometric data. It uses triangles of different sizes to form a sort of net that describes the exterior 3D shape of an object, although it also doesn’t keep information on thickness either. The following image is an STL preview of the Xometry logo on a tile:
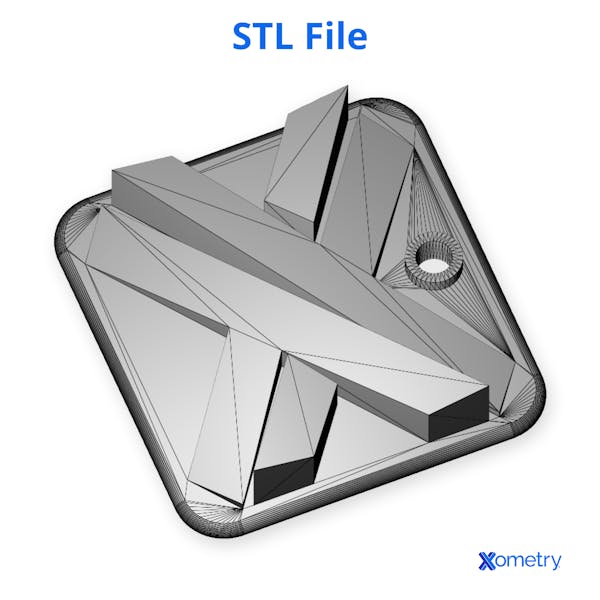
Converting a 3D DXF File to STL with Spin 3D
If you want to convert a DXF file to an STL file for your slicer software, you can use one of several programs or CAD packages available, and many of them are free to download or use online, like FreeCAD. The program we’ll use as an example below is the Spin 3D mesh converter.
Note: The DXF to STL conversion process applies to DXF files containing 3D information. To create a 3D STL model from a flat drawing or 2D DXF file, you will need to open the DXF as a sketch in an appropriate CAD package, extrude the shape, and modify the features as desired to create a fully defined 3D model that can then be saved as an STL.
The conversion process is a piece of cake—you basically just open the DXF and save it as an STL. You could also use a file format converter which you might find easier to use. Here are the very simple steps to follow:
- Open Spin 3D, select the DXF file you want to convert and click Choose File.
- Go to the File Converter page and follow the on-screen instructions; drag and drop the file from your computer into the window, then click Convert.
- When it’s finished, go to the location it’s been exported to, and open the file in an STL viewer. You could even upload it to the Xometry Instant Quoting Engine® to see if the conversion worked!
Property | DXF | STL |
---|---|---|
Property Valid and usable shape definition | DXF Yes | STL Yes |
Property Vector x-y-z (point cloud) | DXF No | STL Yes |
Property Vector graphics | DXF No | STL Yes |
Property Color attributes | DXF Yes, using a color number | STL Not in common ASCII format, can be present in digital files |
Property Texture attributes | DXF Yes, but only as a material property | STL No |
Property Shape elements | DXF Yes, full inclusion of simple and complex shape parameters, including splines | STL No |
DXF vs. STL File Comparisons
Frequently Asked Questions on DXF to STL
What programs can open DXF files?
There are loads out there, but some of the more traditional and well-loved programs include AutoDesk DWG TrueView, EDrawings Viewer (which allows you to do more than just view 2D and 3D data formats), and DXF Viewer (a Chrome extension).
Why do I need to convert DXF files to STL?
Mainly because most hobbyist and lower-cost machines don’t accept DXF files. Some high-end printers with integrated slicer software accept DXF, but unless you have the money to grab yourself one of those, you’ll need to convert to STL.
How long does the conversion take?
It sort of depends on the software and how complicated the file is, but even then, it should only take a few seconds to complete. You’ll find that setting up directories and properties and uploading the files into the software actually takes longer than the conversion itself.
How Xometry Can Help
For assistance with your file conversions or more information on DXF and STL files, particularly in relation to 3D printing (our forte!), reach out to a Xometry representative (we can also help with all your manufacturing needs—just click here to get an instant and free, no-obligation quote.
Disclaimer
The content appearing on this webpage is for informational purposes only. Xometry makes no representation or warranty of any kind, be it expressed or implied, as to the accuracy, completeness, or validity of the information. Any performance parameters, geometric tolerances, specific design features, quality and types of materials, or processes should not be inferred to represent what will be delivered by third-party suppliers or manufacturers through Xometry’s network. Buyers seeking quotes for parts are responsible for defining the specific requirements for those parts. Please refer to our terms and conditions for more information.
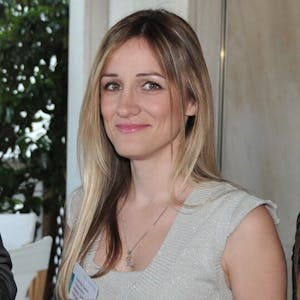