A jet engine uses air and fuel to produce power to either provide thrust out of the exhaust or drive a shaft connected to a propeller or rotor blades. A jet engine is made up of a cold and hot section. The cold section includes the intake, bypass ducts, compressor, diffuser, and drive shaft. The hot section consists of a combustion chamber, turbine, nozzle, afterburner, and exhaust. The jet engine works by drawing in cold air, compressing it, mixing it with fuel, combusting it, and then expelling it out of the exhaust. This article will further discuss the jet engine's major components.
What Are the Parts of a Jet Engine Hot Section?
The hot section of a jet engine starts at the combustion chamber, also known as the gas generator. This is where hot gas is created and moves rearwards expanding in through the turbine blades, supersonic nozzle, afterburner, and finally through the exhaust. The hot section is referred to as such because it contains the hot gas produced in the combustion chamber. Gases in the exhaust range between 550–850 °C, or up to 1,500 °C with an afterburner.
1. Combustor
The combustion chamber is where the air and fuel are mixed and ignited. The combustion chamber must slow down the airflow from around 80–500 ft/s and create a dead zone in the middle where the flame is ignited. The fuel is swirled around the chamber to ensure proper mixture with the air. The temperature of the gases released from the combustion chamber is in the range of 1,800–2,000 °C. To prevent the chamber from melting, two things are necessary. Firstly, some air from the pre-combustion airflow is introduced as a boundary layer between the hot gas and the chamber. Secondly, the combustion chamber is made out of a titanium alloy coated in a ceramic coating. These very thin ceramic coatings reduce the material temperature down to around 300 °C. Titanium combustion chambers are cast and then welded together before having a ceramic coating applied.
2. Turbine
The hot gas then leaves the combustion chamber and expands at rapid rates. The expansion of gas is partially absorbed by the turbine blades to spin them. The turbine blades are connected via a drive shaft to the compressor blades to draw in new air. Turbine blades are manufactured from a single nickel-based alloy crystal to prevent creep between metal boundary layers. The turbine blades are also coated in a ceramic coating to prevent them from melting. In addition to the coating, the blades have internal air channels which allow a cold air bleed to vent out of holes on the surface to create a cool air boundary layer over the blades.
3. Supersonic Nozzle
In most jet engines, the exhaust nozzle is a convergent duct. It accelerates the gas flow to a supersonic speed for introduction to the free stream velocity outside of the engine.
4. Afterburner
Afterburners are simply fuel injection systems that add extra fuel to the hot gas post-combustion to add extra power to the engine for a short duration. For a jet engine with an afterburner, there is usually a double wall with an air gap in between. The existing hot gas is mixed with a flow of cold air from the front of the engine through the space called the internal wall of the engine. This also prevents the heat from transferring to the aircraft structure.
5. Exhaust
Exhaust gases leaving the exhaust are in the range of 550–850 °C. To withstand these conditions, the exhaust is made out of a nickel alloy or titanium alloy. One commonly used nickel alloy is Inconel®.
What Are the Parts of a Jet Engine Cold Section?
Inside the jet engine cold section, there is the air intake, compressor, bypass ducts, shafts connecting the compressor and turbine blades, and a diffuser section. The cold section of the engine can actually be quite hot due to the friction and compression of air that it experiences. However, the cold section is cold compared to the hot section of the engine, which is the combustion chamber to the exhaust.
1. Air Intake
Air intakes seem simple but are in fact quite complex. The geometry of an air intake is either converging or diverging. A converging intake is used to speed up air to roughly 0.5 Mach for engines that have speeds below 0.5 Mach. Divergent ducts are used to slow the air down to 0.5 Mach for engines that operate at above 0.5 Mach. Air intakes also incorporate heating systems to prevent the build-up of ice which creates turbulent flow into the engine and can stall the engine if it falls off in large chunks.
2. Shaft
The shafts of a gas turbine transmit power from the turbine discs in the rear of the engine to the compressor blades at the front to allow the compressor to draw in air. The number of shafts depends on the spool of the engine. A single spool engine has one compressor disc, one turbine disc, and one shaft. A twin spool has two compressor and turbine discs and shafts which move independently of each other. The shafts of a jet engine are made out of heat-treated steel as they need to withstand extreme temperatures and torque. Shafts are commonly machined out of large pieces of steel with the use of a turning machine.
3. Compressor
Compressors are used to compress the incoming airflow by increasing the kinetic energy of the air. The diffuser then slows down the air and converts the kinetic energy to potential energy (pressure) which increases the efficiency of the engine. The compressor can be a radial flow impeller which accelerates the flow outwards to a diffuser. Or the compressor can be an axial flow compressor which accelerates airflow rearwards to a diffuser. Both blades are traditionally made out of titanium, aluminum, or steel. Titanium is often preferred due to its light weight and its corrosion and creep resistance. Carbon fiber blades are also in use, most notably in the GEnx engine. Metal compressor blades are cast with molten metal, cooled, and then machined to their final shape.
4. Bypass Ducts
Bypass ducts allow air compressed by the bypass fan to travel around the outside of the engine core and be either used as thrust or for re-introduction to the engine for cooling functions. The bypass ducts are a large section of the engine, so they are usually made out of aluminum or carbon fiber to reduce their weight. Aluminum is used to make panels that are fitted to create the duct. Carbon fiber ducts are made by laying up carbon fiber into a mold and curing it with a resin. Once cured, the carbon fiber panels can be installed onto the engine to create the duct.
5. Defuser Section
The diffuser section is used to turn the kinetic energy of the air created by the compressor blades to potential (pressure) energy to increase combustion efficiency. Diffusers are usually stator vanes which are essentially static compressor blades that are used to slow down the airflow in the engine. Stator vanes are produced from either steel or nickel-based alloys such as Inconel®.
What Is a Jet Engine?
A jet engine is an engine constructed of an air intake, compressor, diffuser, combustion chamber, turbines, and exhaust. Jet engines will either provide thrust out of the exhaust or drive a turbine disc which drives a propeller or helicopter main rotor. The jet engine works on a continuous cycle during which at all times a stream of air is being drawn in, compressed, combusted, and expelled.
Jet engines are large, complex machines that are assembled in parts. Once the design of an engine is approved, the components need to be manufactured. Some of them will be made in-house, but many will be brought in from other companies and then assembled. For example, the Rolls-Royce Trent is made in eight modules. Major components such as the combustion chamber and compressor are built separately and then married up together at final production. After the assembly of the main parts, accessories such as cabling and hydraulics are added. The final stage of manufacture is testing, during which the engine is run on a test bed to ensure it meets the operational performance specifications. For more information, see our guide on What is Aluminum Casting?
How Does the Jet Engine Work?
A jet engine works by drawing in air from the intake and compressing it. Compression is achieved by speeding up and slowing down air rapidly to create kinetic energy and transform it into pressure energy. The compressed air is then mixed with fuel and ignited. The ignited mixture then expands rapidly. The expanding gas achieves two things, firstly it drives the turbines which drive the compressor to draw in more air. Secondly, it propels the aircraft by either leaving rapidly as thrust through the exhaust or by driving a different set of turbines which drive a propeller or main rotor head of a helicopter.
How Are Jet Engines Manufactured?
Jet engines are large, complex machines that are assembled in parts. Once the design of an engine is approved, the components need to be manufactured. Some of them will be made in-house, but many will be brought in from other companies and then assembled. For example, the Rolls-Royce Trent is made in eight modules. Major components such as the combustion chamber and compressor are built separately and then married up together at final production. After the assembly of the main parts, accessories such as cabling and hydraulics are added. The final stage of manufacture is testing, during which the engine is run on a test bed to ensure it meets the operational performance specifications.
What Are the Material Compositions of the Jet Engine?
Jet engines are made out of many advanced, strong, and also lightweight materials due to the extreme loads and environments they experience. It takes an incredible amount of force to fly, so keeping weight to a minimum while maximizing power is a key goal for jet engine manufacturers. Most of the materials are metallic alloys which include:
- Nickel-based alloys
- Cobalt-based alloys
- Titanium alloy
Engines also use non-metallic materials such as:
- Silicon Carbide
- Carbon Fiber
Manufacturing jet engines is extremely difficult due to their extreme operating conditions as well as the safety requirements an engine has to comply with. Jet engines are subject to extreme thermal, mechanical, and aerodynamic loads. They must also have a very low rate of failure for safety reasons. These two factors combined are what make manufacturing jet engines so difficult.
Additionally, some parts of jet engines are 3D printed. While it is challenging to print engine parts due to the mechanical properties required, the production of some parts now includes this method. General Electric’s GE9X has 3D-printed turbine blades that use the material TiAl which is too brittle to be used using other manufacturing techniques. For more information, see our guide on 3D Printing in Aerospace Industry.
How Is the Quality Control for Manufacturing Jet Engine Components?
Many manufacturers adhere to AS9100 which is the aeronautical counterpart of the ISO 9001 Quality Management System (QMS). AS9100 is an internationally recognized standard that sets out the requirements for effective quality management. The requirements include implementing systems of working and using the correct documentation to ensure all parts are of the right quality and traceable.
Frequently Asked Questions About Jet Engine Components
What Are the Factors That Affect Jet Engine Performance?
There are many factors that can affect a jet engine's performance. One of the main factors is its operating environment. For example, at sea level in a cold atmosphere, an engine will draw in denser air which will increase its thrust. Similarly, an increase in altitude or air temperature (or a pressure drop) results in less dense air which will reduce the engine’s thrust. Another variable is the speed of the engine/aircraft; if the aircraft is moving faster than its design intends, then air will form a pressure wave on the engine intake, limiting airflow. If the engine is moving too slowly, it won’t receive enough ram air which can lead to a stall.
How Long Does a Jet Engine Last?
Jet engine life will vary with the design and maintenance. Engines performing short-haul flights will last fewer flying hours than those on long-haul aircraft because they go through more landings and take-offs per flying hour. GE’s latest CFM56 engine will accumulate over 100,000 flying hours during its lifetime. However, there is a lot of maintenance required for the operation of a jet engine. The Time Between Overhaul (TBO) for a more-typical turbine engine can range from 3,500–6,000 hours.
Why Are Jet Engines Difficult To Manufacture?
Manufacturing jet engines is extremely difficult due to their extreme operating conditions as well as the safety requirements an engine has to comply with. Jet engines are subject to extreme thermal, mechanical, and aerodynamic loads. They must also have a very low rate of failure for safety reasons. These two factors combined are what make manufacturing jet engines so difficult.
Are Jet Engine Components Made Out of Strong Lightweight Materials?
Yes, jet engines must be made out of strong but lightweight materials. This is because a jet engine's thrust-to-weight ratio is one of its most important metrics. It takes an incredible amount of force to fly, so keeping weight to a minimum while maximizing power is a key goal for jet engine manufacturers.
Is a Jet Engine Expensive?
Yes, a jet engine is very expensive—both to buy and to maintain. Prices vary greatly for jet engines but commercial jet engines usually cost between $5,000,000 and $50,000,000. A specific example would be the General Electric 90 engines which cost Emirates approximately $2 billion for 30 units, including spares, and required a repair and overhaul contract worth $1 billion. It should be noted that the GE90 is one of the largest jet engines.
Are Some Jet Engine Components 3D Printed?
Yes, some parts of jet engines are 3D printed. While it is challenging to print engine parts due to the mechanical properties required, the production of some parts now includes this method. General Electric’s GE9X has 3D-printed turbine blades that use the material TiAl which is too brittle to be used using other manufacturing techniques.
Summary
This article presented jet engine major components, explained what each is, and discussed their functions. To learn more about jet engines, contact a Xometry representative.
Xometry provides a wide range of manufacturing capabilities, including 3D printing and other value-added services for all of your prototyping and production needs. Visit our website to learn more or to request a free, no-obligation quote.
Copyright and Trademark Notices
- Inconel® is a registered trademark of Special Metals Corporation
Disclaimer
The content appearing on this webpage is for informational purposes only. Xometry makes no representation or warranty of any kind, be it expressed or implied, as to the accuracy, completeness, or validity of the information. Any performance parameters, geometric tolerances, specific design features, quality and types of materials, or processes should not be inferred to represent what will be delivered by third-party suppliers or manufacturers through Xometry’s network. Buyers seeking quotes for parts are responsible for defining the specific requirements for those parts. Please refer to our terms and conditions for more information.
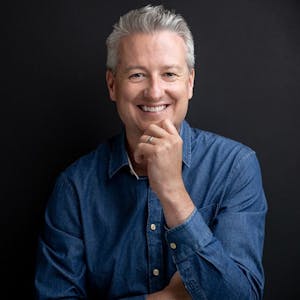