FDM and FFF are common prototyping methods that melt and deposit a polymer filament via a heated nozzle in order to build a 3D object. Stratasys Inc. owns the trademark rights to the term Fused Deposition Modeling (FDM). The wider market refers to this basic process as fused filament fabrication or FFF. There are, however, some differences between FDM and the typical generic FFF.
FDM produces higher quality, (and more expensive) models that better meet the expectations of professional manufacturers. FDM parts are generally much stronger than FFF. The parts feature smoother surfaces with less evidence of the layering process. The internal FDM equipment and parts are more expensive but put out significantly better prints as a result. However, FFF machines are good options for home use. They make parts that are fit for less demanding users. This article will carefully compare FDM vs. FFF, examine their advantages and disadvantages, and list some alternative technologies as well.
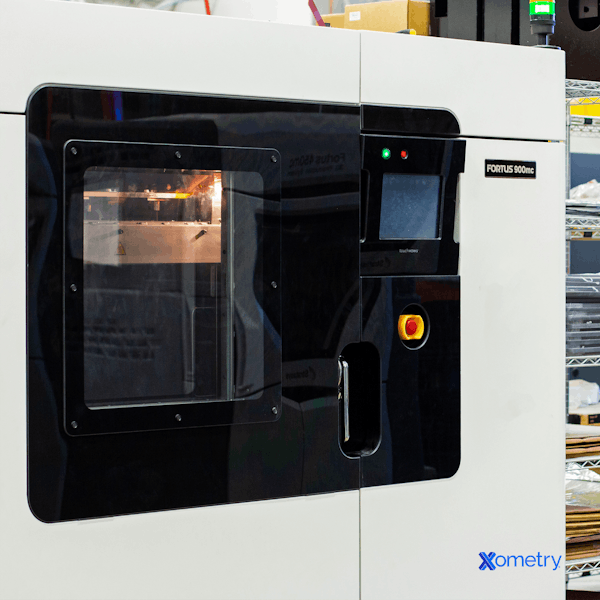
FDM and How It Compares to FFF
FDM was first developed by S. Scott Crump, and patented by Stratasys in 1989. It was one of the earliest 3D printing processes. FDM uses common manufacturing materials and additives to make precise models. Most professional manufacturers prefer FDM over FFF because of its production quality. FDM models are more likely to fit stringent demands than FFF parts.
FDM uses an X-Y transport mechanism to move a print head containing a temperature-controlled extruder. It translates across a table that itself moves on the Z (vertical) axis. The extruder releases a semi-melted polymer filament in the pattern of the part’s 2D cross-section. Each cross-sectional “slice” is applied to the one below. The part gets constructed from mutually bonded strands of feedstock polymer filament. Apart from the advanced machinery, another difference between FDM vs. FFF is its heated chamber. The entire print environment is kept near the polymer’s glass transition temperature in order to relieve build stress during printing. This results in better accuracy and fewer warped models than from FFF.
FDM equipment is more office-friendly than FFF because its fumes are contained and the machine needs less maintenance. Minimum wall thickness differentiates FDM from FFF as well. FFF systems often use larger filaments, so they have a lower x-y resolution. As a rule of thumb, the minimum practical wall thickness is equal to three filament diameters, so FFF needs thicker walls to make its structures stable.
For more information, see our article on What is FDM Printing.
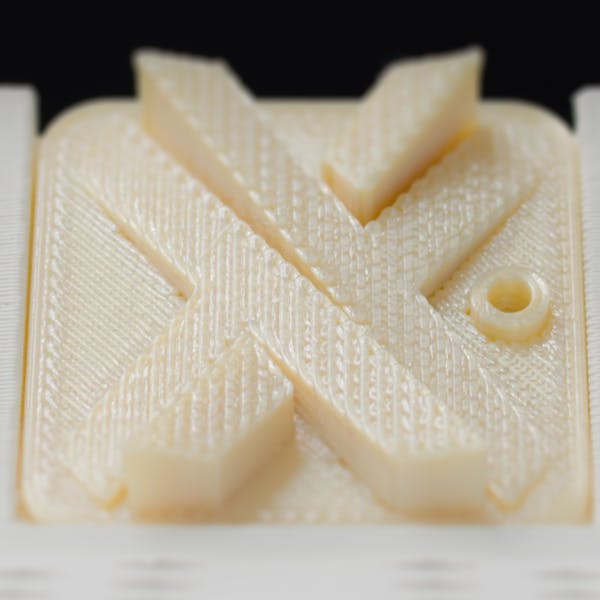
The Advantages of FDM Compared to FFF
The following summarizes the advantages FDM has over FFF
- FDM creates stronger parts because layers fuse more closely and are less porous.
- Because of the higher resolution and better fusion, FDM creates smoother, more cosmetically appealing parts.
- FDM printers have bigger build volumes, on average, than FFF, so they can make larger parts.
- FDM print heads move quicker so parts are completed faster.
- FDM systems have heated build chambers that reduce warping.
- FDM can accept a wider range of materials than FFF.
The Disadvantages of FDM Compared to FFF
The following lists the disadvantages of FDM when compared to FFF:
- FDM’s running and standby power demands are considerably higher than FFF.
- Industrial-grade FDM operations are more complex to set up and operate than FFF.
FFF Definition and Comparison to FDM
FFF originated in 2009 when the Stratasys patent expired. Rep-Rap was the first company to capitalize on the technology’s availability. They popularized home 3D printing with cheap machines that were easy to use. The range of FFF machines has since expanded. Operationally, FFF machines are simple to use, fit on a desk, and have low operational overheads.
FFF employs the same process as FDM. It applies layers of filaments to a flat printing bed using a heated nozzle or extruder. The main difference between FFF and FDM is the lack of a heated print environment. FDM’s heated chamber helps control the part’s temperature and reduce residual stresses in the finished product. The uncontrolled temperature in FFF machines makes their results less accurate and more likely to warp.
The Advantages of FFF Compared to FDM
The following outlines the advantages FFF has over FDM:
- FFF machines are more affordable compared to FDM. FFF is priced for home/hobby use.
- FFF systems are smaller than FDM ones, so they fit better in homes or small offices.
- FFF has lower electricity requirements than FDM.
The Disadvantages of FFF Compared to FDM
The following is a list of disadvantages of FFF compared to FDM:
- FFF-printed parts are lower-quality; they are more porous, exhibit “Z-steps,” and cannot contain especially small, detailed features.
- FFF printed parts tend to distort and warp, particularly on larger builds.
- FFF machines produce foul-smelling fumes whereas FDM machines contain such fumes in the enclosed chamber.
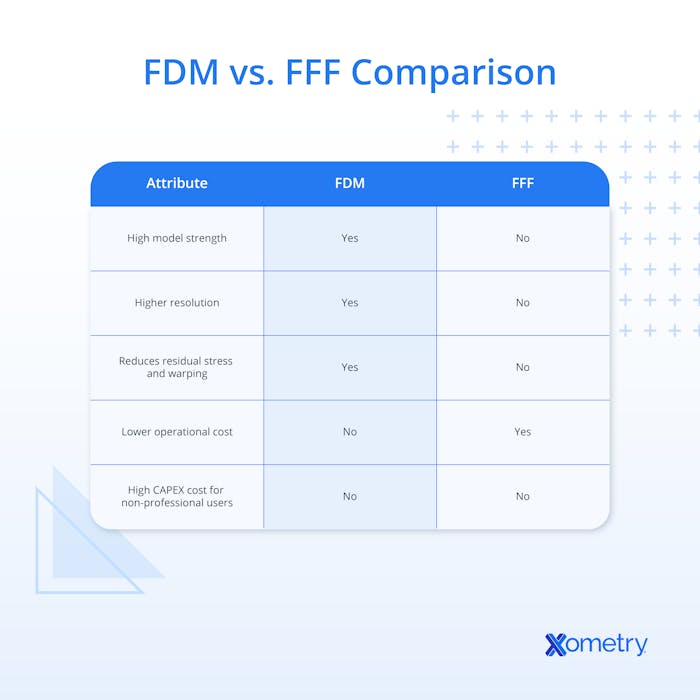
At Xometry, these are some of the comparisons between the FDM and FFF processes we see most often.
Most Common FDM to FFF Comparisons
Technologies
FDM machines are well built, rugged, and capable and require little maintenance. FFF machines, on the other hand, range from the basic, open frame types to professional devices that seem like ‘baby’ FDM machines. Both technologies use similar X-Y-Z rails and stepper motors. Stiffness, however, is a big factor in model resolution/quality. Heavier machines print better models because they’re more mechanically and thermally stable.
Materials
FDM and FFF machines can both use a wide range of materials, including many that are great for mass production. FDM machines, however, have better control over nozzle temperatures. They can handle engineering polymers with higher melting points. They are also better with additives in the filament.
Applications
FFF makes porous, low-strength, low-resolution models. These are suited for shape-and-feel evaluation but not for operational or waterproof parts. The layers of FDM parts, on the other hand, fuse more completely and exceed FFF part strength. This makes FDM-printed parts better suited to engineering models.
FDM printers also accept a wider range of filament properties including melt temperature and additives. If used for prototyping, this means the models will more closely resemble finished products. FFF printers are not suited to fine-featured model builds. They simply cannot produce small features.
Print Volume
FDM systems are designed to meet professional standards; their greater costs are meant to be offset by the higher quality of their products. These machines are built with volumes ranging from 305 x 305 x 254 mm (X-Y-Z) up to 914 x 914 x 609 mm. This compares with typical FFF machines which run between 150 x 150 x 150 mm and 600 x 600 x 600 mm worth of build space. Most FFF machines are small but still struggle to produce models whose quality is consistent across the entire Z-axis range. FFF printers have relatively poor dimensional accuracy and their parts tend to warp.
Surface Finish
Of the two, FDM parts are generally built using finer filament feedstock and smaller Z steps, so their surface finish is more impressive. FFF stock is of larger diameter so the resulting parts are lower resolution and the layers do not fuse as well.
Cost
FDM machines are generally aimed at the professional market with prices ranging from around $2,500 up to $25,000 for advanced industrial grades. This reflects high build quality, stiff axes of motion, and the ability to print all day without problems. While FFF machines are beginning to filter into professional use, they are more often aimed toward light, hobby, and home use. Prices usually start at $500.
Processes Other Than FDM and FFF
Mutual alternatives for both FDM and FFF are listed below:
- SLS: SLS (Selective Laser Sintering) works by dropping layers of polymer powder onto the bed/model. A laser then melts the particles to fuse them together. Like FDM and FFF, SLS builds parts out of thermoplastic.
- SLA: SLA (Stereolithography) uses UV laser light to cure liquid photopolymer material. It builds the plastic part layer-by-layer much like FDM and FFF but does so with the part upside-down. The model “emerges” from the liquid photopolymer reservoir.
How Xometry Can Help
We hope this article helped clarify the differences between FDM and FFF for you. Xometry offers a wide range of 3D printing services across nine processes, from plastic to metal printing processes. Through our wide selection of processes and materials, we likely have a solution to meet your project needs. Best of all, most 3D printing projects quote within seconds! Head over to the Xometry Instant Quoting Engine® today to get your instant quote.
Disclaimer
The content appearing on this webpage is for informational purposes only. Xometry makes no representation or warranty of any kind, be it expressed or implied, as to the accuracy, completeness, or validity of the information. Any performance parameters, geometric tolerances, specific design features, quality and types of materials, or processes should not be inferred to represent what will be delivered by third-party suppliers or manufacturers through Xometry’s network. Buyers seeking quotes for parts are responsible for defining the specific requirements for those parts. Please refer to our terms and conditions for more information.
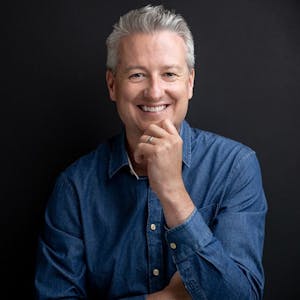