When it comes to making items for either business or home use, 3D printing has become one of the most popular and efficient ways for people to do it. Out of all the 3D printing tech available, Fused Deposition Modeling, or FDM, is one of the most popular. This type of printing presses a thermoplastic filament through a nozzle and onto the build plate. It’s so popular because of both its speed and its reliability. That said, there are some restrictions in FDM printers for industrial requirements that use glass or ceramic. While there are some constraints with print quality, FDM is still the most common 3D printing method.
In this article, we’ll talk about everything FDM—what it means, where it came from, what it’s good for, and where its limits lie. We’ll also compare it to other types of 3D printing.
What is Fused Deposition Modeling?
This 3D printing technique makes three-dimensional images by melting materials like thermoplastics and pushing them through a nozzle, creating multiple layers that fuse together. The technology was invented in 1988 by Scott Crump who thought to combine polyethylene and candle wax and pressed it through a glue gun so he could make a frog toy for his daughter. A year later, he patented FDM and founded Stratasys, Inc. with his wife. Multiple 3D manufacturers took inspiration from Crump’s creation and started to produce different brands of 3D printers.
Here’s a picture of one of the printers we use here at Xometry:
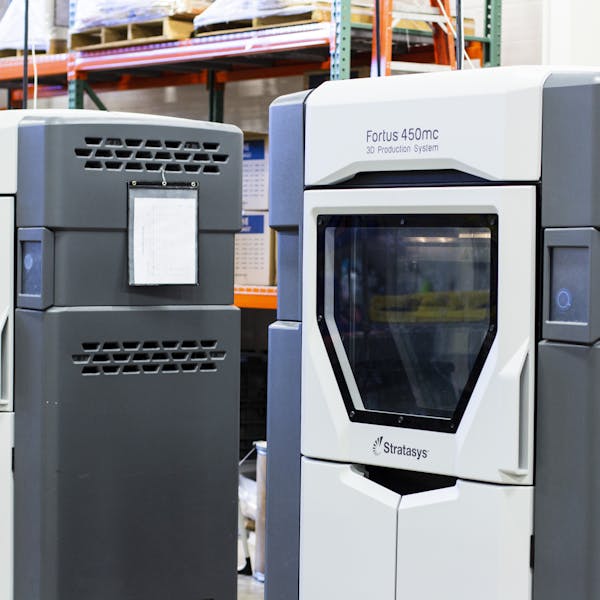
There are lots of benefits to using FDM technology, including the low cost of using thermoplastic polymers like nylon, polyethylene, and rubber. It’s an easy tech for hobbyists to use at home, since there are compact printers available that don’t compromise on precision. The thermoplastics are both mechanically and ecologically stable, since FDM can use engineering-grade thermoplastics.
This material has a notable impact strength, thermal steadiness, and biocompatibility. It’s also recyclable, which helps the environment by reducing pollution. FDM technology can build complex shapes that would be impractical or impossible using other methods. Since FDM technology builds objects in layers, the object can be crafted in almost any shape, no matter how complicated.
How it Works
This style of printing uses CAD files. Before printing an image, it has to be modified to a format that the printer understands, typically an STL file. During printing, the thermoplastic filament uncoils and gets pushed through an extruder nozzle. This nozzle heats the filament before it hits the platform, and the computer controls this process. It shares information about the X, Y, and Z measurements of the object, and the material cools and hardens in the dictated shape. Every new layer builds on the previous one, building the final product. As the layers grow, the platform moves down to give new layers space until the whole object is fully formed. Small objects can take a little bit, and more complicated ones take a long time to print.
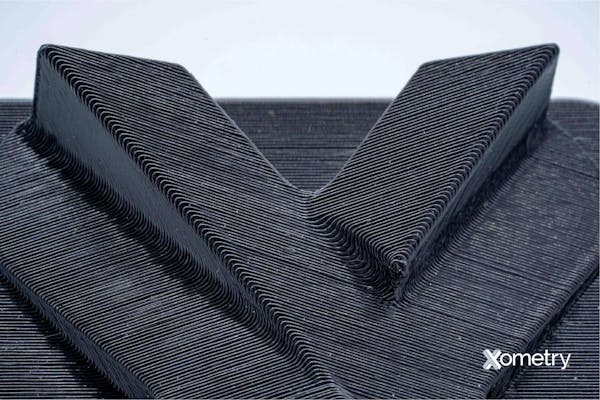
Materials
There are five materials that are most commonly used in FDM 3D printing. First is acrylonitrile butadiene styrene, also known as ABS. This thermoplastic polymer has a high rigidity, high impact resistance, and handles welding ideally. It does well with heat and provides toughness to an object. ABS is often used in surgical applications, kitchen equipment, and toys such as LEGO blocks.
Another common material is polylactic acid, also known as PLA. This polymer is brittle, yet biodegradable. It’s made from renewable sources like sugar cane or cornstarch. It’s mostly used in the food industry, as well as surgical use in health situations. Polyethylene terephthalate glycol, or PETG, is renowned for its excellent strength, and how easy it is to print with. In particular, engineering companies appreciate the chemical resistance, moisture retainage, and transparency of this polymer. They use it to build textile products, containers, and graphic showcasing.
Thermoplastic polyurethane, or TPU, has fantastic mechanical properties with an elasticity level similar to rubber. It’s most commonly found in items that call for flexibility. It shows up in footwear, sports equipment, and automotive parts. Finally, nylon (PA) is popular for its tremendous strength, as well as its resistance to both wear and chemicals. It’s particularly popular for use in non-flexible filaments, and it offers resistance to unbendable materials.
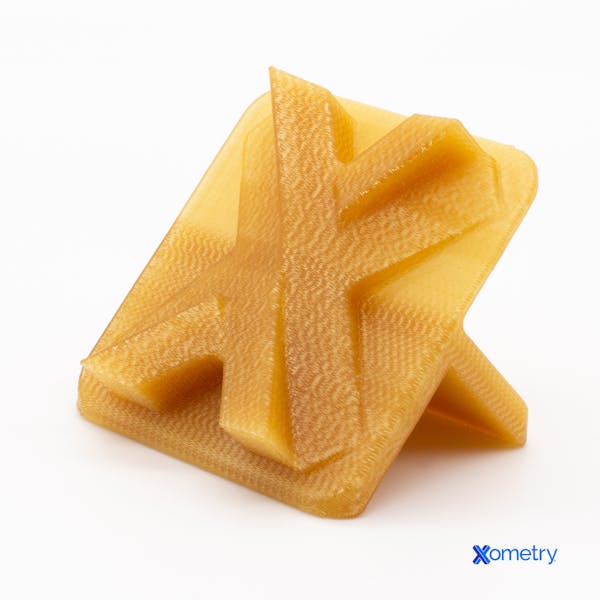
FDM Technology Limitations
For all the benefits of FDM technology, there are gaps in its abilities as well. For example, there are a limited number of materials that work with FDM printers. It can’t copy more advanced printing materials such as ceramics and glass, which ultimately limits durability. Since FDM prints in low resolution, it also has an issue with printing highly detailed items. It has a thicker-than-average layer height, which makes small, intricate parts a near impossibility.
There are also issues with the quality of the finished product. Objects produced on FDM printing are anisotropic, so they are easily broken with enough force parallel to the layers. It’s also possible to see lines between the layers after printing. While they can be gotten rid of using a chemical and mechanical process, it’s additional labor that takes away from the ease of FDM technology.
How Xometry Can Help
Here at Xometry, we offer a wide variety of manufacturing services, including FDM 3D printing, plastic 3D printing, and more. Our available materials include General-Purpose ABS, ASA, and PLA. These low-cost, rigid thermoplastics are typically produced via Fused Filament Fabrication (FFF) using an array of 3D printers. These materials can also access our global manufacturing network, providing significantly reduced pricing compared to branded Stratasys materials.
Upload your designs to the Xometry Instant Quoting Engine® to get started today!
Disclaimer
The content appearing on this webpage is for informational purposes only. Xometry makes no representation or warranty of any kind, be it expressed or implied, as to the accuracy, completeness, or validity of the information. Any performance parameters, geometric tolerances, specific design features, quality and types of materials, or processes should not be inferred to represent what will be delivered by third-party suppliers or manufacturers through Xometry’s network. Buyers seeking quotes for parts are responsible for defining the specific requirements for those parts. Please refer to our terms and conditions for more information.
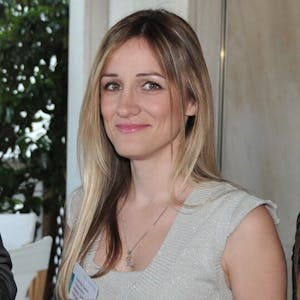