When choosing a manufacturing material, particularly plastic, the technical data sheet will give you a bunch of useful information to help in your selection. The heat deflection temperature (HDT) is one such tidbit, and it’s an important one to know if your product needs to keep its shape and size under pressure.
What is Heat Deflection Temperature?
A material’s HDT is the temperature at which it starts to deform when it’s put under a specific load at high heat. It measures the plastic’s ability to stay stiff or rigid in these circumstances. High HDT plastics will stay more rigid in higher heats, and low HDT ones, not so much. And yes, this is only relevant to polymers and plastics, so metals will have to sit this one out (they have their own versions, like hot hardness and creep tests).
HDT is valuable (a must, in fact) for the engineering, design, and manufacturing of plastic products (or those with any parts made of plastic) in many industries, including:
- Packaging
- Aerospace
- Automotive
- Electronic
- Medical
- Consumer goods
- Construction industry
- Injection-molding
In packaging, containers at the grocery store, post office, and even at home, are stacked and squashed—and sometimes in heat—but they can’t warp under pressure. The same goes for vehicle parts, like dashboards. A car often sits in direct sunlight for hours on end, but it would be a total disaster if the dash sunk in when you put your bag or phone on it. In injection molding, a material’s HDT is one of the factors that will determine the process cycle time. It’s also a big decider in whether or not a plastic is suitable for use as a structural component, as these understandably have a pretty tough job.
Measuring Heat Deflection Temperature
To work out a material’s HDT, we need heating, loading, and measuring systems—all of which are provided by the HDT test equipment/apparatus (pictured below).
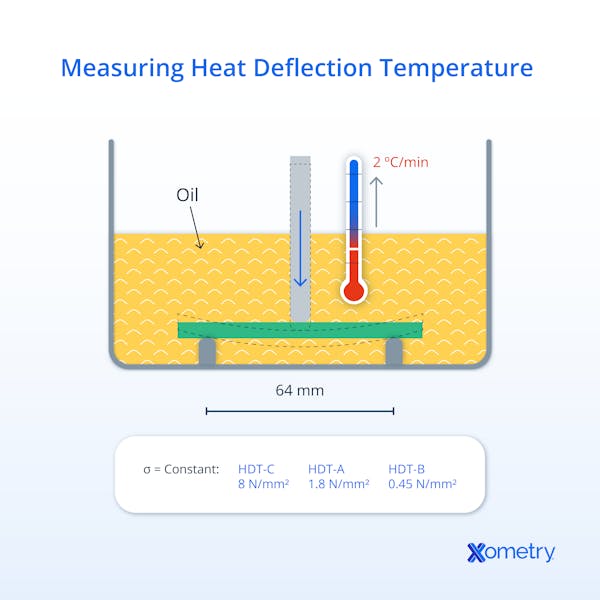
The standard measuring system for HDT is the American Society for Testing and Materials (ASTM) D 648—which is comparable to the ISO 75 international standard. To get a little more technical, the standard states that a material’s HDT is the temperature at which a bar measuring 127 x 13 x 12 mm (we’ll call this the “sample”) deflects by 0.25 mm when put under a centered standard flexural stress of either:
- 0.46 MPa (67 psi): This is used on soft plastics, like polyethylene (PE), or low-density PE, and other polymers for general use.
- 1.8 MPa (264 psi): For stronger and more durable thermoplastics/thermosetting materials for heavy-duty use, such as polyether ether ketone (PEEK), polycarbonate (PC), and epoxy resins.
The testing method for both of these is exactly the same, apart from the load amount. The higher 1.8 MPa load will make the material deform at a lower temperature than the 0.46 MPa one. Sometimes, higher 5.0 MPa (725 psi) or 8.0 MPa (1160 psi) loads are tested but as this is rare, we’ll just stick to the two common ones.
Steps
The HDT measuring process consists of the following 4 steps:
- The sample is prepped and loaded on the machine in a three-point bending configuration, meaning it’s supported at its two ends so that pressure can be applied in the middle.
- A constant bending stress (either 0.46 or 1.8 MPa, depending on what you’re testing) is applied to said middle.
- A mineral or silicone oil that won’t affect the plastic is used as the heat transfer, and its temperature is gradually increased at a controlled rate of 2°C/min (±0.2°C/min).
- The sample is monitored throughout all stages and temps, and when it deforms by 0.25 mm, we have the HDT.
Impacting Factors
Several things can affect the test’s outcome (which is why there are standards that should be followed for consistent results), such as:
- Duration of high-temperature exposure (more chance of deforming under load when exposed for longer)
- The part’s shape and thickness (can affect the heat transfer rate and stress distribution)
- The rate of temperature increase (if too quickly, the part can show a lower HDT)
- The operating conditions beyond load/temperature
- Additives/fillers in the material (change the material’s inherent properties)
- The specific grade of plastic
- Its molecular weight/distribution
- The molecular structure’s degree of crystallinity
As many things can affect a material’s HDT, it’s important to note that the test is just one of several factors to consider when selecting a material as its performance in any given situation will depend on various factors. For example, materials that absorb moisture (hygroscopic), like nylon, can exhibit different HDTs depending on moisture content, so they need to be pre-dried before testing.
Material | HDT at 0.46 MPa (°C) | HDT at 1.8 MPa (°C) | Melting Point (°C) |
---|---|---|---|
Material ABS | HDT at 0.46 MPa (°C) 98 | HDT at 1.8 MPa (°C) 88 | Melting Point (°C) - |
Material Acrylic | HDT at 0.46 MPa (°C) 95 | HDT at 1.8 MPa (°C) 85 | Melting Point (°C) - |
Material Nylon 6 | HDT at 0.46 MPa (°C) 160 | HDT at 1.8 MPa (°C) 60 | Melting Point (°C) 220 |
Material Polycarbonate | HDT at 0.46 MPa (°C) 140 | HDT at 1.8 MPa (°C) 130 | Melting Point (°C) - |
Material Polyethylene | HDT at 0.46 MPa (°C) 85 | HDT at 1.8 MPa (°C) 60 | Melting Point (°C) 130 |
Material PET | HDT at 0.46 MPa (°C) 70 | HDT at 1.8 MPa (°C) 65 | Melting Point (°C) 250 |
Material Polypropylene | HDT at 0.46 MPa (°C) 100 | HDT at 1.8 MPa (°C) 70 | Melting Point (°C) 160 |
Material Polystyrene (PS) | HDT at 0.46 MPa (°C) 95 | HDT at 1.8 MPa (°C) 85 | Melting Point (°C) - |
HDT of Common Polymers
As you can see, the HDT of any plastic will vary under different loads—increasing the load will lower the HDT. Let’s take unfilled and unmodified Nylon 6 and Nylon 6/6 as an example. The HDT at a load of 1.8 MPa can be anywhere from 70–120°C, but under a 0.46 MPa load, it jumps to 115–155°C.
FAQs on Heat Deflection Temperature
Is HDT important in 3D printing?
It is for two main reasons. The first and more obvious one is if the part you’re 3D printing will be subjected to loads in high temperatures, the HDT will help you decide the right material to use. The second is that 3D printing in itself subjects the filament to high heat—particularly with fused deposition modeling, where the material is pushed through a heated nozzle. Plastics with higher HDTs won’t be as prone to sagging during extrusion. In any event, most machines nowadays have built-in cooling fans, and there are ways around sagging if you’re set on using a plastic with a lower HDT (i.e., 3D printing supports).
HDT vs. glass transition temperature—what’s the difference?
HDT is a macroscopic measurement of a material’s stiffness as temperature increases and the point at which it deforms under load. The glass transition temperature (Tg) marks the point where an amorphous (or semi-crystalline) polymer—like PC, PS, and polymethyl methacrylate—transitions from a rigid to a softened state as molecular chain movements "freeze." Unlike crystalline materials, amorphous polymers don’t have a defined melting point; instead, they soften over a range of temperatures and are characterized by their Tg. The Tg is typically higher than the HDT, and is measured with DSC (differential scanning calorimetry) or DMA (dynamic mechanical analysis).
Is HDT known by any other names?
Yes, and we’re often asked by customers why they can’t find this stat on the data sheet. It’s also referred to as the deflection temperature under load (DTUL), heat deflection temperature under load (HDTUL), or heat distortion temperature.
How Xometry Can Help
Whether you’re in the process of choosing the best material for your product, or need to know the HDT of a material you’re already working with, we’re just a call/message away—feel free to get in touch with one of our representatives. You can also get a quick and free, no-obligation quote on any of our manufacturing services—of which there are many, including 3D printing, plastic injection molding, and CNC machining.
Disclaimer
The content appearing on this webpage is for informational purposes only. Xometry makes no representation or warranty of any kind, be it expressed or implied, as to the accuracy, completeness, or validity of the information. Any performance parameters, geometric tolerances, specific design features, quality and types of materials, or processes should not be inferred to represent what will be delivered by third-party suppliers or manufacturers through Xometry’s network. Buyers seeking quotes for parts are responsible for defining the specific requirements for those parts. Please refer to our terms and conditions for more information.
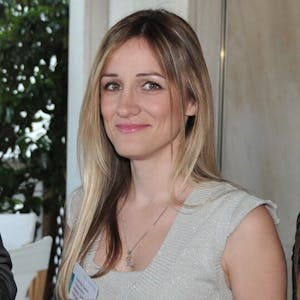