Commercial use of metal 3D printing services has found acceptance in most high-value industries. Even complex customized metal parts are relatively simple to produce.
There are multiple ways to 3D print metal items. The most established of these is known as powder bed fusion (PBF). This umbrella term includes electron beam melting (EBM), direct metal laser sintering (DMLS), and selective laser sintering (SLS), among others. Each technique melts or fuses metal powder layer by layer in an otherwise loose powder bed. A more recent technology is direct energy deposition (DED), which directly applies metal powder (DED powder) or wire feedstock (DED wire) through nozzles. A third approach is binder jetting, which bonds the powder bed with an adhesive that is later burned out in a sinter post-processing step, leaving behind only the solidified metal. An increasingly common approach is to use fused filament fabrication or fused deposition modeling (FFF/FDM) to print parts from polymer-bound metal powders which are then sintered to make high-density, full-strength metal components.
These processes offer advantages such as design flexibility, minimal waste, and the ability to create geometrically complex and lightweight structures. While they’re powerful technologies, strict quality control and monitoring of material integrity are critical.
Listed below are eight common metal 3D printing applications:
1. Custom Tools
Metal 3D printing has brought a quiet revolution to the manufacture of custom tools in many industry sectors. You can quickly and easily integrate multiple functions, simplify awkward tasks, and improve production and maintenance functions by 3D printing tools. In sectors as diverse as jet engine maintenance and surgical instruments, metal 3D-printed custom tools offer advantages like enhanced capability, improved productivity, and reduced costs. The range of applications is growing exponentially as prices and availability improve.
2. End-of-Arm Tooling
3D-printed metal end-of-arm tooling (EoAT) is an increasingly widespread and valuable application of metal additive manufacturing. EoAT is the generic description of the specialized attachments, actuators, or tooling at the end of a robot’s actuators/arms. These tools are designed to interact with and manipulate objects. EoAT can contain sensors, cameras, and other application-specific equipment, allowing automated functions to interface with the real world.
3D-printed metal EoAT devices are crucial in sectors like manufacturing, surgery, and orbital maintenance, where robots and automation have become increasingly important. It’s easier and quicker to adapt printed tools to rapidly evolving tasks. And it can be done in a streamlined, efficient, and cost-effective manner.
3. Low-Volume and Specialty Parts
Metal 3D printing is an ideal method for producing small numbers of specialty parts across a wide range of industries. Sectors as varied as race engineering, satellite development, antique restoration, and medical tools all benefit from metal additive manufacturing processes. Custom parts solve an extraordinarily diverse range of urgent and cost-sensitive needs.
Metal 3D printing is precise, gives you significant design freedom, and simplifies logistics. even with small production volumes. It empowers manufacturers and designers to use exotic designs that simplify assembly needs.
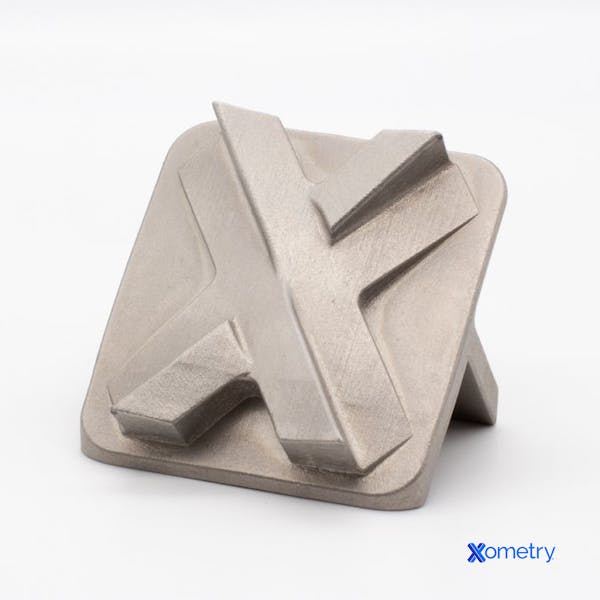
4. Surgical and Dental Implants
Metal 3D printing has been a boon for spinal injury treatment, joint prostheses, trauma reconstruction, and dental implants/bridges. The ability to make complex and customized geometries in biocompatible materials accelerates the preparation for treatment. Not only do the implants fit better, but implantation surgeries go quicker because doctors don’t need to spend as much time adapting parts for the patient’s body. Another benefit is for soft tissue or bone integration. Tissues can grow into and integrate with porous implant structures. Metal 3D printing integrates directly into digital workflows that start with medical 3D scans like magnetic resonance imaging. Scans feed patient data into precision processes that can directly initiate production.
Surgical and dental implants produced via metal 3D printing deliver better patient outcomes, surgery times, and patient-unique solutions than other methods. This sequence of technologies is revolutionizing the medical and dental implant fields with patient-centric solutions.
5. Jewelry and Decorative Arts
Metal 3D printing is beginning to impact the fields of jewelry and decorative arts. Artists can design unique, intricate, and personalized pieces. It is now possible to produce perfect, unique, complex, and precise objects in fast and repeatable ways that cost less than a skilled hands-on process to manufacture. It all amounts to minimal material waste, wider material selection, less design reinterpretation, and low costs. Beyond pure commercial interests, metal 3D printing is now also employed to replicate historical artifacts or restore damaged items with great precision.
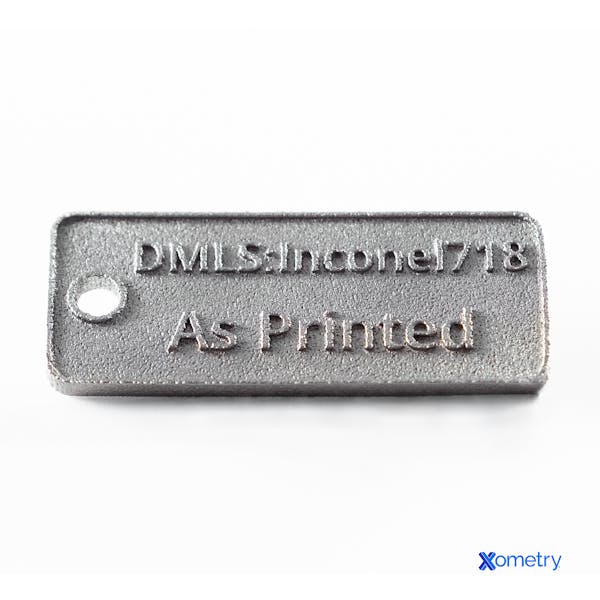
6. Complex Bracketry
When dissimilar components and devices must be affixed to one another, you often need specialty brackets. They can take the form of simple shelf brackets, mounting points on the International Space Station, spinal surgery joinery, and many other items. Whether the focus is on production speed, complexity, or strength, if customization is the goal, then 3D-printed parts are becoming the go-to option.
7. Functional Metal Prototypes
3D printing of metal parts is particularly important in the making of small functional prototypes. They cover everything from race-car control linkages to prosthetic hand gearbox parts, and furniture joints to robotic grippers. This “instant metal” technique presents great potential to accelerate the product development and testing process.
While dimensional precision for small parts can be good, printed surface finishes are often coarse. Post-machining is commonly required for moving parts such as bearings and gear surfaces. The parts’ responses to wear depend on the printing process, so you must evaluate printing methods carefully before choosing one.
For larger functional parts, the economics of 3D printing are different. The cost of parts grows disproportionately with size. However, lower resolution and coarser processes can still generate usable parts where cost sensitivity is not the main driver.
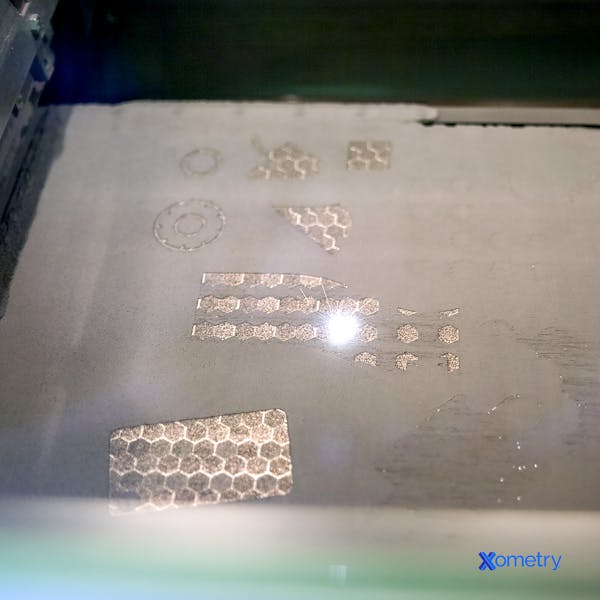
8. Spare and Obsolete Parts
Metal 3D-printed parts play a critical role in replacing or restoring parts. They’re often components for antique constructions like old firearms, cars, or aircraft.
Advantages of 3D Metal Printing
Metal 3D printing has several overwhelming advantages, especially since the technology is getting more accessible. Here are a few examples:
- 3D printing allows you to make highly intricate and complex geometries that are difficult or even impossible to achieve using traditional manufacturing methods.
- Designers have greater freedom to create innovative components, including lattice structures, internal channels, and lightweight parts that would otherwise be impossible to machine.
- This family of production processes allows for the manufacture of entirely custom and unique parts tailored to specific requirements. This is particularly significant in fields like: healthcare (custom implants), aerospace (intricate engine components), and automotive restorations (unique and obsolete parts).
- Printing facilitates quick and cost-effective prototyping, reducing development lead times and costs.
- Component weights can be adjusted using internal lattice structures, reducing weight where it adds no value, but doing so without compromising strength.
- An increasingly wide range of metals and alloys can be 3D printed, including: titanium, aluminum, stainless steel, bronze, and beryllium-copper.
- Complex assemblies can often be consolidated into single 3D-printed parts that wouldn’t be possible using any other methods. Driving complexity out of assemblies and into singular digitally manufactured parts can alleviate assembly struggles and improve end-product quality/performance
- On-demand manufacturing is a significant benefit in some contexts, reducing the need for large inventories and associated storage costs. As an example, it’s increasingly common for military repair facilities to print parts on-site.
- The ability to create parts constructively rather than subtractively enables you to optimize strength-to-weight ratios in ways that would be impossible otherwise.
- Metal 3D printing is a cost-effective way to produce small volumes of specialized components. Although the parts may be as expensive or more so than those from a subtractive process, the setup times and delivery schedules can be an overwhelming advantage.
Summary
Xometry provides a wide range of manufacturing capabilities including CNC machining, 3D printing (including DMLS and binder jetting metal 3D printing), injection molding, laser cutting, and sheet metal fabrication. Get your instant quote today.
Disclaimer
The content appearing on this webpage is for informational purposes only. Xometry makes no representation or warranty of any kind, be it expressed or implied, as to the accuracy, completeness, or validity of the information. Any performance parameters, geometric tolerances, specific design features, quality and types of materials, or processes should not be inferred to represent what will be delivered by third-party suppliers or manufacturers through Xometry’s network. Buyers seeking quotes for parts are responsible for defining the specific requirements for those parts. Please refer to our terms and conditions for more information.
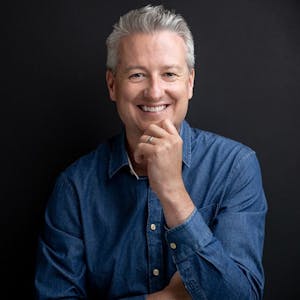