“Metal 3D printing” is an umbrella term that is used to describe several manufacturing processes for additive manufacturing of metal parts. The material is processed in a layer-by-layer manner, through sintering, welding, or melting. Two common metal 3D printing processes are Selective Laser Melting (SLM) and Direct Metal Laser Sintering (DMLS). Both of these use powder-bed fusion technology. While metal 3D printing can produce parts from a large range of metals and metal alloys, the best materials for metal 3D printing are stainless steel, tool steels, titanium, and Inconel® (nickel-based) alloys.
This article will define what metal 3D printing is, how it works, discuss the four best materials for metal 3D printing, and what materials work best in different applications.
1. Stainless Steel
Stainless steel is widely known for its ability to withstand corrosion, high strength, and excellent aesthetic appearance. Parts printed with stainless steel can have the same or even greater strength than parts created using traditional manufacturing methods. The strength, hardness, and other properties of 3D-printed stainless steel depend mainly on the specific technology used to print the part.
Stainless steel-printed parts have found application in many industries, including aerospace, automotive, military hardware, and medical. Compared to other metal 3D printing materials, stainless steel parts can be made with the smoothest surfaces because of the addition of chromium.
Stainless steel powder used for 3D printing comes in a variety of grades and alloys, including 316L, 304L, 630, 410, 420, 254, 17-4 PH, 15-5PH, PH1, and GP1. Of these, 316L is the most commonly used grade in metal 3D printing. It has a composition of 66-70% iron enhanced with 16-18% chromium, 11-14% nickel, 2-3% molybdenum, and less than 0.03% carbon. This 3D printing material is known for its ductility and good corrosion resistance.
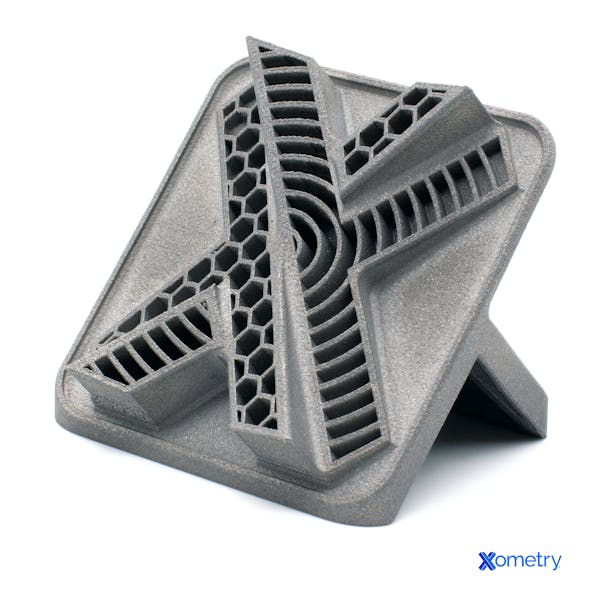
2. Tool Steels
Tool steels are a family of iron-based alloys containing relatively high levels of carbon, which form carbides with other alloying elements, including tungsten, chromium, vanadium, and molybdenum. Tool steels offer an excellent combination of high-temperature strength, hardness, and wear resistance. These steels are commonly applied in the production of molds, stamps, and cutting tools in multiple industries. The tools are used to manufacture geometries that are used in other product manufacturing processes, including extrusion, cutting, casting, injection molding, stamping, and component assembly. The following tool steel options are available for metal 3D printing—D2, M2, H13, H11, MS1, and 1.2709.
3. Titanium
Titanium is the most-used metal in the additive manufacturing industry. It is widely employed in the medical, aerospace, automotive, and electronic industries, among others. Titanium and its alloys have high mechanical strength. They also offer better corrosion resistance than stainless steel.
The following titanium material options are available for metal 3D printing—Ti-6Al-4V, Beta 21S, Cp-Ti (commercially pure titanium), and TA15.
4. Inconel® 625
Inconel® 625 is a nickel-based superalloy that offers high strength and can retain its strength over a wide temperature range. Due to its excellent corrosion and oxidation resistance, it is considered ideal for corrosive environments. Inconel®625 finds application in the marine, energy, and chemical processing industries. Some applications of Inconel® 625 include boat propellers and heat exchanger casings.
What Is Metal 3D Printing?
Metal 3D printing is a method of creating metal parts or products that adapts the general principles and methods of additive manufacturing methods and applies them to powdered metals. 3D printing always involves building a part using powder or filament wire, layer-by-layer, under computer control.
There are a number of ways to join together the successive layers of metal powder to form the final shape. They can be melted by a laser or electron beam, sprayed with a binding agent (binder jetting), or directly printed as molten droplets heated from metal filaments using Direct Energy Deposition (DED) or Direct Metal Laser Sintering (DMLS) printers.
Figure 1 below is an example of a metal 3D printer (DMLS):
Other Metals You Can 3D Print
Metal 3D printing can be performed using a wide range of metal powders. These include, but are not limited to, steel, aluminum, stainless steel, copper, cobalt, tungsten, titanium, and nickel-based alloys. Precious metals like platinum, gold, palladium, and silver can also be used in 3D printing.
How Metal 3D Printing Works
The working principles of a metal 3D printing method depend on the material used, whether that be a powder, filament, or wire. Out of these three options, printing with powder is the most common method.
With powdered metal 3D printing, the metal powder for the first layer is spread out by the powder coater, or recoater, on the floor of the build platform. A high-powered laser or electron beam is then used to selectively bind together the material as it scans the powder. This creates one solid layer of the object. The platform is then displaced downwards by 50-200 microns while another even layer of metallic powder is distributed over the previous layer and the process is repeated.
Metal wires, on the other hand, are the most affordable raw material form for metal 3D printing. The wire is melted with a plasma arc, laser, or electron beam. Direct Energy Deposition (DED) is an example of a 3D printing method that uses metal wires to produce parts. It is primarily used for repairs or for adding features to existing metal parts.
Metal filaments are just thin plastic wires impregnated with metal particles. This raw material choice makes sense when using Fused Deposition Modeling (FDM) printers. FDM works by extruding the heated filament through a nozzle onto the build platform to create a part. After printing, the part is placed on a debinding station to melt the plastic away using a solvent and then sent to a sintering furnace to fuse the metal particles together into a solid metal piece.
How To Select the Best Materials for Metal 3D Printing
To select the best metal 3D printing materials for your project, follow the steps below:
- Define the performance requirements of the part to be produced. The requirements can include both environmental conditions to which the part will be exposed as well as mechanical stresses that are expected in the operating state.
- Compare the performance requirements to the material specifications. This means checking the properties of the material to assure that that will satisfy the end-use requirements and operating conditions. For example, do you need a material with good mechanical strength or good corrosion resistance?
- Choose the material that best fits the performance and part requirements expected so that it will provide reliable operation and good service life.
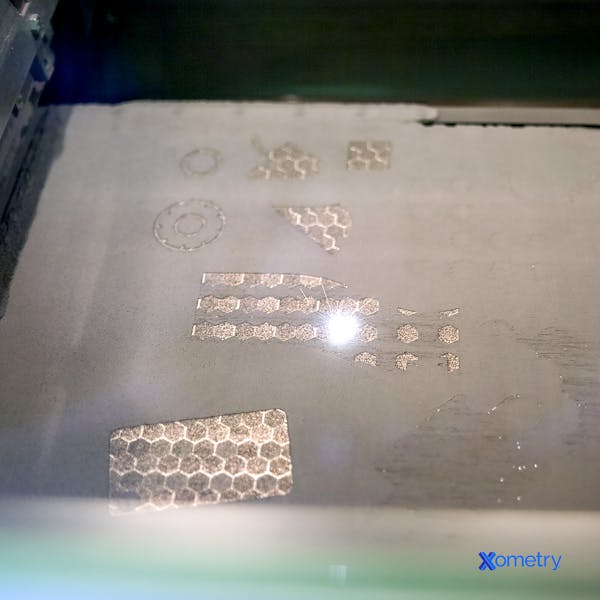
Summary
Xometry provides a wide range of manufacturing capabilities including metal 3D printing service, CNC machining, injection molding, laser cutting, and sheet metal fabrication. Get your instant quote today.
Copyright and Trademark Notices
- Inconel® is a registered trademark of Huntington Alloys division of Special Metals Corp., Huntington, WV.
Disclaimer
The content appearing on this webpage is for informational purposes only. Xometry makes no representation or warranty of any kind, be it expressed or implied, as to the accuracy, completeness, or validity of the information. Any performance parameters, geometric tolerances, specific design features, quality and types of materials, or processes should not be inferred to represent what will be delivered by third-party suppliers or manufacturers through Xometry’s network. Buyers seeking quotes for parts are responsible for defining the specific requirements for those parts. Please refer to our terms and conditions for more information.
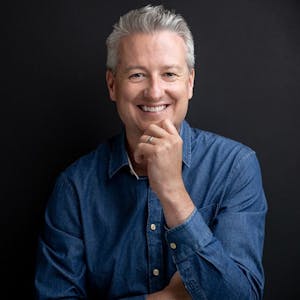