There are around 50 different types of nylon, but not all of them are suitable for 3D printing—it was originally designed as a textile fiber. Wallace H. Carothers, a researcher at DuPont, first discovered it in 1935 when he was trying to make the first fully synthetic fiber. Since then, nylon has gone on to serve many purposes, from pantyhose to high-performance parts used in construction, automotive, and even aerospace. Let’s learn more about it.
What is Nylon 3D Printing?
Nylons are a family of semicrystalline thermoplastic polyamides with similar compositions. It’s made through a process called condensation polymerization, where two different monomeric starting materials—a diamine and a diacid—are reacted together to form the polymer, producing a byproduct like water or HCl. But each type of nylon has a slightly different production method. Using Nylon 6,6 as an example, this is made through a condensation reaction between two common raw materials, hexamethylenediamine, and adipic acid. An alternative method is ring-opening polymerization, which uses caprolactam as a feedstock to produce Nylon 6. You’ll find more details about the different nylons and how they’re made a little further down.
Nylon has been used in 3D printing for over two decades now; in filament form, it’s used with fused deposition modeling (FDM) printers, and as a powder, it’s suitable for the selective laser sintering (SLS), and multi jet fusion (MJF) processes. The below image shows a part made on a 3D printer with nylon filament.
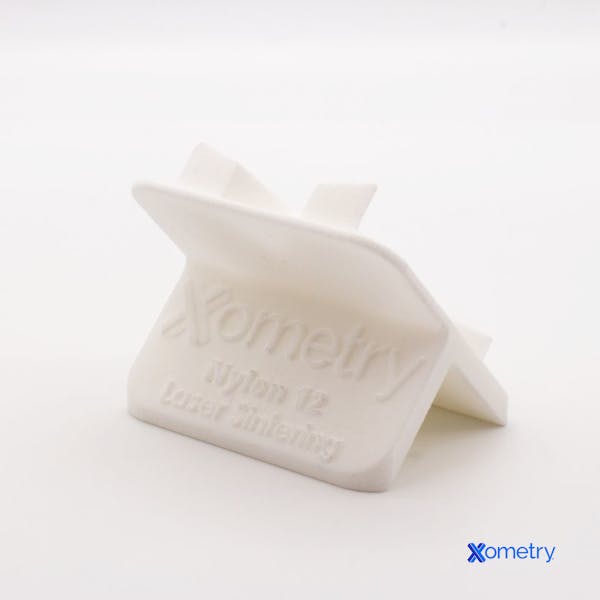
You might have heard that nylon is a difficult material to work with, and this is no lie. The problem with nylon is that it’s hygroscopic, meaning it absorbs moisture from the air. This makes it prone to warping, with poor layer adhesion, and inconsistent print quality if it’s not properly dried before printing.
The good news is that the addition of glass and carbon fibers does away with most of these hassles while at the same time improving its mechanical properties. Nylon carbon fiber filament is made by mixing short carbon fiber strands into nylon before extruding it into a filament. These fibers stabilize the material and prevent it from warping during printing. The even better news is that up to 25% of the nylon filament volume can be one of these fillers. When combined with the right filler and printer settings, nylon can be used to make strong, long-lasting, and functional parts for hard-wearing applications.
Advantages
- Flexible
- Tough
- Abrasion-resistant
- Resistant to alkalis, oils, fuel, and organic solvents
- Better impact-resistance than other engineering thermoplastics (i.e., PETG or ABS)
- More UV resistant than PLA or ABS (even more so when UV stabilizers are added)
- Recyclable
Disadvantages
- Tends to warp during printing and detach from print bed
- Is hygroscopic, so easily absorbs moisture before and after printing—could lead to defects
- Not as strong as other filaments, like PETG or ABS
- Not biodegradable
- Not resistant to halogens and inorganic acids
Applications
- Pulley sheaves
- Gears
- Fasteners
- Cable and zip ties
- Plastic buckles
- In dry, outdoor environments
What is the Composition of Nylon Filament?
Nylons are a family of semicrystalline thermoplastic polyamides with similar compositions. Nylon is generally synthesized through a process known as condensation polymerization. During this process, two different monomeric starting materials, a diamine, and a diacid are reacted together to form the polymer and a byproduct molecule such as water or HCl. For example, Nylon 66 is made by condensation reaction from two common raw materials, hexamethylenediamine, and adipic acid. An alternative processing method, called ring-opening polymerization, uses caprolactam as a feedstock to produce Nylon 6.
Nylon is often combined with carbon and glass fibers to improve its mechanical and thermal properties. Up to 25% of the filament volume can be one of these fillers.
What are the Properties of Nylon Filament?
Listed below are some common properties of nylon 3D printing filament:
- Nylon has excellent flexibility & toughness and can be used in applications that are exposed to harsh loading conditions.
- Nylon has good abrasion resistance and is often used for pulley sheaves.
- Nylon has excellent resistance to oils, fuel, and organic solvents.
- Nylon has excellent impact resistance when compared to common engineering plastics like ABS.
Comparison of Nylon Filament Properties
But how does nylon measure up against other popular 3D printing filaments, like ABS, PETG, and PP? We’ve put all the important details in the below table (Nylon 6 in there again for ease of reference).
Property | Nylon 6 | ABS | PETG | PP |
---|---|---|---|---|
Property Tensile Modulus (MPa) | Nylon 6 2300 ± 64 | ABS 1699 ± 113 | PETG 1711 ± 45 | PP 234 ± 16 |
Property Tensile Stress @ Yield (MPa) | Nylon 6 63.1 ± 1.1 (XY) | ABS 38.1 ± 0.3 (XY) | PETG 46.2 ± 0.8 (XY) | PP 8.6 ± 0.4 |
Property Elongation @ Yield (%) | Nylon 6 6.1 ± 0.2 (XY) | ABS 4.1 ± 0.1 (XY) | PETG 5.9 ± 0.1 (XY) | PP 18.7 ± 3.0 |
Property Flexural Modulus (MPa) | Nylon 6 1060 ± 58 | ABS 1317 ± 28 | PETG 1489 ± 25 | PP 250 ± 9 |
Property Flexural Strength (MPa) | Nylon 6 36.6 ± 3.0 | ABS 21.5 ± 1.8 | PETG 50 ± 3.5 | PP 9.4 ± 0.3 |
Property Charpy Impact Strength (kJ/m2) | Nylon 6 13.7 ± 1.2 (Notched) | ABS 1.5 ± 0.1 (Hinge) | PETG 7.9 ± 0.6 (Notched) | PP 49.1 ± 3.2 (Notched) |
Property Hardness (Shore D) | Nylon 6 81 | ABS 76 | PETG 76 | PP 42 |
Property Heat Deflection Temperature (0.455 MPa) | Nylon 6 89.2 ± 5.6 | ABS 86.6 ± 0.4 | PETG 76.2 ± 0.8 | PP 64.1 ± 3.6 |
Property Glass Transition Temperature (°C) | Nylon 6 55.1 | ABS 100.5 | PETG 77.4 | PP -20 |
Property Melting Temperature (°C) | Nylon 6 188.4* | ABS 200 | PETG 260 | PP 130.6 |
Nylon vs. Other Plastics
*While nylon’s melting temperature is 188.4°C, carbon or glass-filled nylon filaments will have the melting temperature of their base material
What are the Limitations of 3D Printing with Nylon?
Printing with nylon has some downsides, as listed below:
- Nylon tends to warp during printing and can detach from the print bed.
- Nylon easily absorbs moisture both before and after printing. Moisture absorption by the filament material often results in defects in the printed part.
- Nylon is not as strong as other printable materials such as PETG and ABS.
Some of the benefits of nylon 3D printing filament are listed below:
- Nylon has excellent abrasion resistance and is ideal for pulley sheaves and gears.
- Nylon has excellent impact resistance compared to other engineering thermoplastics like PETG or ABS.
- Nylon is more UV resistant than PLA or ABS and can be used in dry outdoor environments. Its UV resistance can be further improved by adding UV stabilizers to the raw material.
Why is Nylon Used in 3D Printing?
Nylon is used in 3D printing due to its toughness, chemical resistance, and abrasion resistance. It is a difficult material to work with but can be used to print functional parts. Nylon carbon fiber filament is a popular material that is made by mixing short carbon fiber strands into nylon before extruding it into a filament. These fibers stabilize the material, preventing warping during printing, increasing mechanical strength, and improving thermal properties.
How to Use Nylon in 3D Printing
Nylon 3D printing filament is difficult to print due to its tendency to warp and absorb moisture. However, if the correct printer settings are used there is no reason why excellent results can’t be achieved. Listed below are some tips for successfully printing nylon:
- Nylon easily absorbs moisture. This property can have a detrimental effect on the printed part due to porosity caused by expanding bubbles of boiling water as the moisture cooks off. It is therefore important to store filament material in an airtight container. Some containers can even store the filament during printing which is especially useful for long-duration prints.
- Nylon will warp during printing if the print environment is not maintained at around 45 °C.
The above-listed tips for 3D printing with nylon are generally applicable to all nylon plastics. However, carbon fiber nylon filament and glass-filled nylon filament do not warp as easily.
What are the Best Configuration Settings for Nylon 3D Printing?
As we mentioned, with the correct printer settings and right type of nylon, there’s no reason why you can’t get excellent results. Here are some of our top tips that are generally applicable to all nylon plastic filaments for successful 3D printing.
1. First, you’ll need to make sure your printer is adjusted to the best settings for this material. While the specific printer settings required will depend on the nylon’s formulation, here are the general rules:
- Extruder/nozzle temperature: 230–260 °C
- Bed temperature: 60–70 °C
- Print speed: 30–70 mm/s (50 mm/s is ideal for best results, especially for detailed parts)
- Infill density: 20% with a triangular infill pattern (should be adjusted as per application; load-bearing uses might need 50–80%)
- Best wall thickness: 1.5 mm (for most applications; will depend on the part’s end use)
2. As you can see, a heated printing bed is a must when working with nylon so that it doesn’t warp and lift off the bed, but you might also need to prep it with adhesives.
3. Keep the print environment at around 45°C.
4. Use carbon fiber or glass-filled nylon filaments that don’t warp as easily.
5. Store your nylon filament in a moisture-free, airtight container. Some containers can even store the filament during the printing process—handy for long-duration prints.
6. This goes for all 3D printing materials, but have a play around with the different speed settings until you find the perfect one. Every printer and material combination will behave slightly differently.
FAQs on Nylon 3D Printing Filament
How does Nylon differ from other plastic 3D printing filaments?
Nylon is more impact-resistant than PETG and ABS, and is a lot tougher, and more flexible than PLA. PLA is rigid and brittle, with poor fatigue resistance under cyclic loading—so nylon wins that round. Like nylon, ABS is a difficult material to print, but it is easier to use than nylon and also has better tensile strength. PETG, too, is a lot easier to print with and it’s also cheaper than nylon.
Is Nylon Recyclable?
It has to be recycled in industrial recycling facilities. Nylon 6 is more recyclable than Nylon 6,6, for instance, as it is made from a single molecule. This makes it easy to polymerize, whereas Nylon 6,6 is made from two molecules that are difficult to separate.
Why is moisture bad for 3D prints?
The printed part could be ruined if moisture has got into the material (and, as we’ve seen, nylon loves to absorb it). This is because of the porosity caused by expanding bubbles of boiling water; as the water evaporates during printing, it can cause the material to weaken.
What is the Best Nylon 3D Print Speed?
Nylon can be printed at speeds between 30 and 70 mm/s but the optimal speed tends to be around 50 mm/s, especially if high levels of detail are required in the print. As with any 3D printing process, it may be necessary to try a few different speed settings until the optimal operating speed is determined. Every printer/material combination behaves slightly differently.
What is the Melting Temperature of Nylon Filament?
The melting temperature of the nylon filament is 188.4 °C. Carbon or glass-filled nylon 3D printing filaments have melting temperatures equivalent to their base polymer melting temperatures.
Is a Heated Printing Bed Required When Printing with Nylon?
Yes, a heated print bed is required when printing with nylon. Nylon is prone to warping and can lift off the bed if it has not been sufficiently prepared with adhesives and heated.
What is a Good Wall Thickness for 3D Printing Nylon?
The optimal wall thickness for 3D printing of nylon depends on the end use of the part being printed. However, in general, a wall thickness of 1.5 mm will be ideal for most applications.
What is a Good Wall Density for 3D Printing Nylon?
The optimal infill density for a nonfunctional prototype nylon 3D printed part is 20%. However, this density must be adjusted depending on the intended application. Load-bearing applications may require between 50 and 80% infill density. The standard triangle-type infill will be sufficient for the majority of applications.
Is Nylon Biodegradable?
No, like most other commodities and engineering-grade thermoplastics, nylon is not biodegradable.
Is Nylon Hygroscopic?
Yes, nylon is hygroscopic and readily absorbs moisture. It is therefore recommended to keep nylon filament material in a moisture-free enclosure.
What is the Difference Between Nylon and PLA in 3D Printing?
PLA is a rigid and brittle material that has poor fatigue resistance. Nylon, on the other hand, is tougher, more flexible, and has better fatigue resistance under cyclic loading.
What is the Difference Between Nylon and ABS in 3D Printing?
Like nylon, ABS is a difficult material to print. However, it is easier to use than nylon. ABS also has better tensile strength. However, Nylon is significantly more impact resistant than ABS.
What is the Difference Between Nylon and PETG in 3D Printing?
PETG is not as impact resistant as nylon> However, it is much easier to print with and is cheaper than Nylon.
How Xometry Can Help
Thinking of using nylon for your next 3D printing project? Get in touch! 3D printing is our forte here at Xometry, and we offer lots of different methods and materials. You can get started today by uploading your designs to the Xometry Instant Quoting Engine® for a quick, free, and no-obligation quote.
Disclaimer
The content appearing on this webpage is for informational purposes only. Xometry makes no representation or warranty of any kind, be it expressed or implied, as to the accuracy, completeness, or validity of the information. Any performance parameters, geometric tolerances, specific design features, quality and types of materials, or processes should not be inferred to represent what will be delivered by third-party suppliers or manufacturers through Xometry’s network. Buyers seeking quotes for parts are responsible for defining the specific requirements for those parts. Please refer to our terms and conditions for more information.
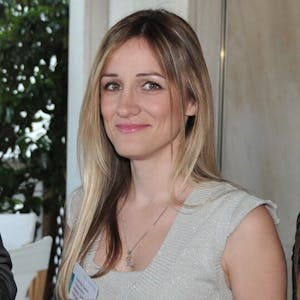