Polycarbonate is a plastic that—more specifically—falls under the thermoplastic category, meaning it’s pretty fantastic at melting down and hardening over and over again. Interestingly enough, this makes for a material that’s well equipped to go through the 3D printing process. Not only that, but it’s renowned for being durable and having a decent heat tolerance and chemical resistance.
If polycarbonate has caught your attention as a potential candidate for whatever types of products you’re creating with additive manufacturing, we have created a helpful explainer below that goes through exactly what this process entails and what its benefits (and limitations) are.
What is Polycarbonate 3D Printing?
Polycarbonate, or PC for short, is the material that’s used in this style of printing, and it’s usually a go-to choice for fused deposition modeling (FDM) printing systems, which layer up the material to build up several layers until your shape is finished.
The reason why polycarbonate has earned its spot in the 3D printing world is because of its useful characteristics that make it easy to work with and functional once the 3D object is printed out. It has a tensile strength of 70 MPa and a yield strength of 63 MPa—which, for context, is far higher than concrete. It also holds onto its structural integrity at high heats (up to 150 ℃). Understandably, these impressive feats have made it a staple of many industries, including aerospace and medical fields, but we’ll delve into applications later.
How it Works
If you’re curious about what the polycarbonate 3D printing process involves, we’ve broken down a general step by step below.
- For starters, you’ll need to design the 3D model you want to print through a computer-aided software program. This is what the printer will use as instructions so it can print exactly the dimensions, details, and shape you want.
- Then the preprocessing will start, which involves scaling, orienting, and positioning the model and ensuring that it’s correct and ready to be materialized with the help of a printer.
- Next, you’ll need to program the printer and get it prepped for its upcoming job. This can involve a variety of different tasks and jobs, including leveling the print bed, cleaning the nozzle, and setting the right parameters. In doing so, you’re making sure the print comes out successfully and won’t warp on the print bed—which polycarbonate is sometimes known to do.
- Once these steps are complete, the printing can finally begin. The nozzle or extruder will heat up the polycarbonate filament inside and then, following your 3D model, it’ll start moving around the print bed, depositing layers of the molten PC, which will fuse together and create your build.
- The last step has to do with post-processing and finishing, but will depend on the specific product that’s being printed and how much cleaning, sanding, and painting are needed. The bigger and more complex the build, the longer it may take to fully finish a print.
In the picture below, you can see an example of our Xometry logo that’s been 3D printed with polycarbonate.
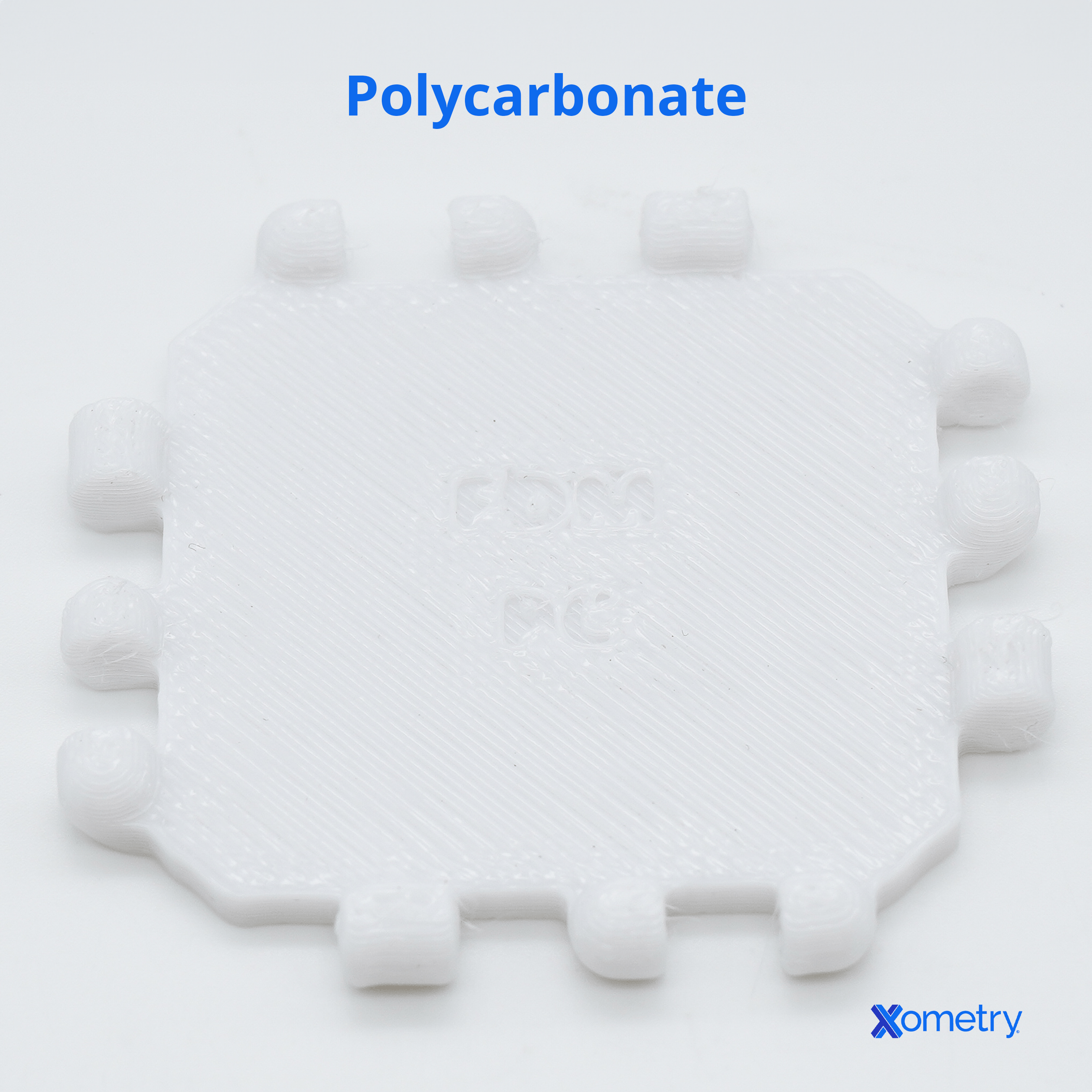
Applications
There are so many uses for polycarbonate 3D printed products, hence why the aerospace, automotive, medical, consumer and electronic industries all use them. We’ve listed out a few examples of items that can be produced this way:
- Light fixtures
- Vehicle headlights
- Safety goggles
- Window panes
- Carabiners
- Bike helmets
- Lenses for glasses
- Surgical guides
Types of Polycarbonate
You can, of course, just use regular polycarbonate for 3D printing, but there are a few other blends that might come in handy to know about as they offer different properties.
Polycarbonate
This pure form of PC is a top pick because of how strong it is and how much resistance it provides against heat, impact, and abrasion.
Polycarbonate/ABS Blends
Acrylonitrile butadiene styrene—or ABS—is another popular 3D printing filament, but you can find it mixed with polycarbonate, too. The result is a printable material that’s not too expensive and still has a decent amount of strength.
Polycarbonate/Carbon Fiber Composites
If you like the heat resistance of PC, but are looking for a little more strength and stiffness, you’ll want to consider this filament, which mixes polycarbonate’s thermoplastic characteristics with those of carbon fiber composites.
Polycarbonate/Fire-Retardant Blends
In instances where you build will be subject to flames, fire, or extreme heat, you might need more heat resistance than usual and a material that won’t go up in flames. The best filament for that is a polycarbonate that’s boosted with the help of fire-retardant additives.
Polycarbonate/Polyethylene Glycol Blends
Warping can be an issue with polycarbonate, but to prevent this, you can use a filament that has a mixture of PC and PEG. The most common use cases tend to be designs that have intricate details or geometries that are likely to become misshapen.
Our very own Colton Bamford, an Additive Production Manager here at Xometry said, "When choosing polycarbonate materials for 3D printing, I focus on several factors. First, its high impact strength and durability make it ideal for tool-making and creating functional prototypes. Dimensional stability ensures the printed parts retain their shape and precision, which is crucial for manufacturing tools. Heat resistance and compression strength are important for applications such as metal-forming dies or validating tool designs before full-scale production. Finally, the cost-effectiveness of polycarbonate compared to other high-performance materials makes it a practical choice for low-volume end-use parts."
Advantages and Disadvantages
Outside of its superb mechanical properties, polycarbonate makes a few other cases for why it’s such a good material to 3D print:
- PC products can be made to have a clarity and transparency that many other filaments can’t provide.
- It’s great when put up against high temperatures, chemicals, oils, and solvents.
- Polycarbonate is a useful electrical insulator.
- Compared to other materials, polycarbonate is pretty lightweight.
- You can also recycle PC.
There are also a few negatives to note when working with polycarbonate:
- It can have a higher cost than other filaments (but blends like PC/ABS can be more affordable).
- Polycarbonate has the tendency to absorb moisture from its surroundings, so it needs to be stored properly.
- Because of its heat resistance, polycarbonate needs to be used within a printer that can reach temperatures of at least 290 ℃ in order for it to successfully melt and funnel out.
- Polycarbonate tends to warp more than other materials, and without good temperature control, it may not adhere to the print bed very well.
- A lot of polycarbonate materials have BPA, which can be released during printing, so be sure to wear protective equipment like masks and work in a well ventilated room.
How Xometry Can Help
Whether you’re interested in polycarbonate 3D printing or plastic 3D printing, our services at Xometry have you covered. Outside of plastic, we have a long list of other additive manufacturing capabilities that you can get an instant quote for, including selective laser sintering, carbon DLS, metal 3D printing, and plenty more.
Disclaimer
The content appearing on this webpage is for informational purposes only. Xometry makes no representation or warranty of any kind, be it expressed or implied, as to the accuracy, completeness, or validity of the information. Any performance parameters, geometric tolerances, specific design features, quality and types of materials, or processes should not be inferred to represent what will be delivered by third-party suppliers or manufacturers through Xometry’s network. Buyers seeking quotes for parts are responsible for defining the specific requirements for those parts. Please refer to our terms and conditions for more information.
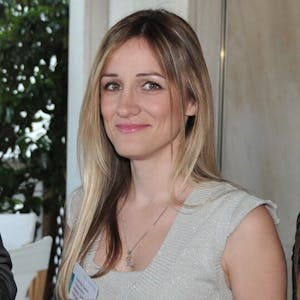