These two traditional methods have a lot in common. For example, they’re both additive manufacturing processes that use UV light to cure a liquid resin. They also both print layer by layer, albeit with some differences in the way they do so. So how exactly do they differ, and when would you use either one? Let’s find out.
What is PolyJet?
First developed by Objet-Geometries in 2000, PolyJet 3D printers work quite similarly to inkjet printers. But, instead of depositing drops of liquid ink, PolyJet works by releasing drops of photopolymer, one layer at a time, until it builds a whole 3D model. As it’s being built, UV light cures and solidifies each layer. This type of printer uses multiple heads that work at the same time to lay down the material as well as any support material, which can later be removed by water jetting. If the support material is too thick, it might need some more post-processing like using a chemical bath, peeling, and washing off. These printers can actually print materials other than resin, too, and they can tackle rather large production volumes. But they can’t really make large-format parts. Here’s an image of some parts being printed in a PolyJet printer here at Xometry:
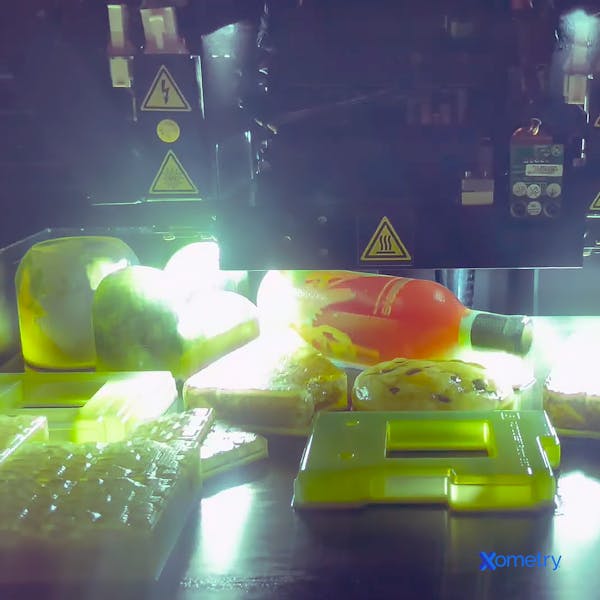
PolyJet printing has further advantages, too. For instance, it supports lots of different colors, and its parts have very good tensile strength. It also offers high-resolution parts, and when they’ve been printed, they’re cured well enough, so they won’t need to be placed into a UV oven like SLA parts would (more on this later). Lastly, it’s a very fast way of printing, especially for models that fit within a 5” cube. The one main drawback this technology has, especially over SLA, is that it tends to cost more because the materials are usually more expensive. You can find out more by checking out our guide on the PolyJet process.
What is SLA?
SLA stands for Stereolithography, and it’s the first-ever 3D printing technology to be invented. It was created by Chuck Hull in the 1980s before he went on to found 3D Systems. This type of printer uses a UV laser to trace each layer of a part on the surface of a liquid resin tank. After each layer, the build platform lowers into the tank, exposing the layer to fresh resin so it can harden and bond to the layer before it. When the printing process is finished, the model is cleaned in a chemical bath, the supports are removed by hand, and the part is cured in a UV oven. Sometimes, it will need to be sanded to get it a little smoother. Unlike PolyJet, SLA is much better at making large prototypes and hollow parts because it uses an internal honeycomb structure that makes parts solid and of high quality. That’s another reason why SLA parts are often used in the healthcare and jewelry sectors.
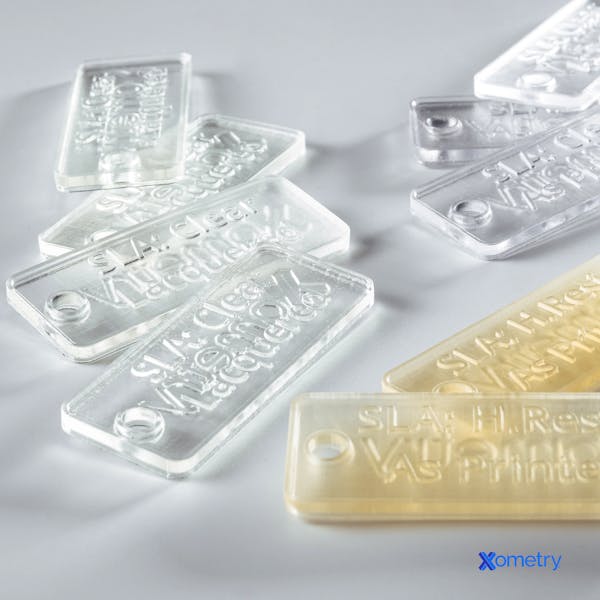
But, it does have some drawbacks. SLA printers are not as stable as PolyJet printers, which could result in variations between prints, especially if they’re supposed to be the same. Also, they’re not compatible with various materials, and they’re limited to gray, white, and clear color options. The layers these printers can make are usually much thicker, with SLA having a minimum thickness of around 50 microns and PolyJet going down to 16. The last two potential downsides are that SLA parts can be rather brittle and fragile (not great for functional prototypes), and the process can get quite messy—think resin spills, post-processing, and nasty odors.
Attribute | PolyJet | SLA |
---|---|---|
Attribute Degrades over time with light and heat exposure | PolyJet Yes | SLA Yes |
Attribute Good tensile strength | PolyJet Yes | SLA No |
Attribute Accuracy and detail | PolyJet Small detailed prototypes and intricate patterns | SLA Large models and intricate patterns |
Attribute Resolution | PolyJet Excellent - 0.00063” | SLA Good - 0.005–0.002” |
Attribute Printing speed | PolyJet Very fast | SLA Very fast |
Attribute Cost | PolyJet $6,000 to over $75,000 | SLA $1,200 to over $100,000 |
Attribute Surface finish | PolyJet Smooth right off the build | SLA Smooth with sanding |
PolyJet vs. SLA Attributes Comparisons
Frequently Asked Questions on PolyJet and SLA
Are there any mutual alternatives to these?
Of course; with two being the main ones: FDM and SLS. FDM stands for Fused Deposition Modeling, and it's a material extrusion method that works with plastic, and the parts need support structures, like SLA. It’s also quite similar to PolyJet in that they both use an orthogonal printer transport mechanism for Z-axis layering. SLS, an abbreviation for Selective Laser Sintering, is similar to SLA because they use lasers to fuse material. And like PolyJet, it produces parts with isotropic properties.
What’s the difference between PolyJet and Multijet?
Multijet printing (MJP) is quite similar to PolyJet in that it uses the same technology and process. They both cure liquid photopolymers using UV lamps. The main difference is that multijet uses multiple nozzles for much better precision, and sometimes it even has separate nozzles for support material. We have a guide on the differences between these two, which you can check out.
What’s the difference between SLA and DLP?
DLP stands for Direct Light Processing, and much like SLA, it builds models by curing liquid photopolymer materials. They’re both very accurate. The main difference is that DLP uses a digital light projector to flash an entire layer at once, making it faster for certain prints. You can read our article on SLA vs. DLP to learn more.
How Xometry Can Help
To learn more about PolyJet, SLA, or any related process or material, you can reach out to one of our representatives. Xometry provides lots of services for all your manufacturing, prototyping and production needs, including CNC machining, 3D printing, and laser cutting. Visit our website to learn more, or upload your designs to the Xometry Instant Quoting Engine® and get started straight away.
Disclaimer
The content appearing on this webpage is for informational purposes only. Xometry makes no representation or warranty of any kind, be it expressed or implied, as to the accuracy, completeness, or validity of the information. Any performance parameters, geometric tolerances, specific design features, quality and types of materials, or processes should not be inferred to represent what will be delivered by third-party suppliers or manufacturers through Xometry’s network. Buyers seeking quotes for parts are responsible for defining the specific requirements for those parts. Please refer to our terms and conditions for more information.
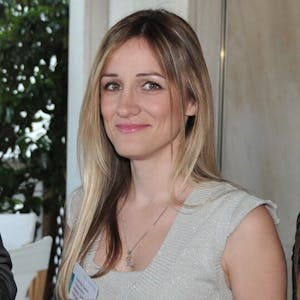