When manufacturers want to make 3D-printed parts with complex geometries, they often turn to powder bed fusion (PBF) machines. These parts are notoriously hard to make (sometimes impossible) with traditional manufacturing methods. Let’s learn more about it.
What Are PBF Machines?
PBF machines are 3D printers that can create high-quality, intricate, and complex parts for various applications in many different industries. They work by melting and fusing layers of metal or plastic powders using a laser or an electron beam to build the part layer by layer from a bed of powder. It can make customized parts with specific properties, such as strength or heat resistance, that meet the specific needs of customers. You can see what one of these machines looks like in the below picture.
The great thing about PBF is that it generally keeps waste to a minimum, as any excess powder is collected and recycled after the part is complete. There’s also quick iteration on designs, allowing engineers to update CAD designs and reprint flawed parts. When it comes to complex parts with intricate internal geometries, PBF is the preferred 3D printing method. A complete part can be designed, manufactured, tested, re-designed, and printed again much faster than with other methods like metal casting or MIM. PBF machines can produce multiple parts simultaneously, which improves productivity and reduces the time required to manufacture parts.
PBF can work with a wide range of plastics and metals, and the parts made require minimal support structures during printing; the unused powder acts as support. For example, when making cooling channels inside turbine blades, the excess powder can simply be poured out. Having said that, PBF is a relatively slow process with a long print time due to the need for powder preheating, vacuum generation, and cooling-off periods. In addition, as they’re made one layer at a time, the structural properties of PBF parts aren’t typically as strong as those made using other processes. The surface quality will also depend on the grain size of the powder and can resemble manufacturing processes like sand casting and die casting.
You’ll also have to watch out for thermal distortion that can cause the shrinking and warping of fabricated parts, particularly if they’re made from a polymer. Another drawback for some could be the high cost; both the equipment and materials are expensive. While it is possible to find end-to-end systems under $100,000, prices typically start in the $150,000–$200,000 range, with high-end models sometimes costing over $1,000,000. It’s also an energy-guzzling process. The unused powder that remains after printing and is removed in post-processing should be recycled efficiently, though preheating can still affect some of the unused material.

PBF Machine Types
There are two main types of PBF techniques: Laser Beam PBF (PBF-LB), which uses a laser to fuse materials, and Electron Beam PBF (PBF-EB), which, as the name suggests, uses an electron beam under vacuum. Each of these has specific branded or patented variations technologies, which we’ve put in the below table for ease of reference.
PBF Type | Description | Common Applications |
---|---|---|
PBF Type Direct Metal Laser Sintering (DMLS)/Selective Laser Melting (SLM) | Description Similar to SLS, but uses a high-powered laser to selectively fuse metal powders, producing highly accurate, complex metal parts | Common Applications Aerospace, medical, automotive |
PBF Type Selective Laser Sintering (SLS) | Description Uses a laser to fuse polymer powders (e.g., nylon) layer by layer, the surrounding unfused powder supports the structure, removing the need for support materials | Common Applications Prototyping, small-batch production |
PBF Type Electron Beam Melting (EBM) | Description Uses an electron beam in a vacuum to fuse metal powders; pre-sintering reduces powder dispersion, and the heated build chamber minimizes residual stress | Common Applications Large aerospace and medical components |
PBF Machine Types
How PBF Machines Work
The steps in the PBF 3D printing process are as follows:
- A CAD model has to be created and sliced into layers. The 3D printer is programmed with the build sequence before printing begins.
- A thin, even layer of powder (typically 0.1 mm) is spread across the build platform.
- The powder bed is heated to a temperature slightly below the material’s melting point to reduce thermal stress.
- A high-powered laser or electron beam selectively melts the powder layer based on the digital model. The material solidifies as it cools.
- The build platform lowers by one layer thickness, and the process repeats until the part is fully formed.
- Once printing is complete, the part is removed from the powder bed, and any post-processing steps can begin.
PBF Machines—At A Glance
Advantages
- Flexible
- Improved manufacturing times for parts with complex designs
- Reduced waste and, in turn, reduced costs and environmental impact
- Works with a range of materials
- Need minimal support structures during printing
Disadvantages
- Long print time and slow process
- Weak structural properties
- Surface texture depends on the powder’s grain size
- Expensive machinery and powder
- Thermal distortion
- Uses a lot of energy
Applications
- Aerospace (turbine blades, fuel nozzles, guide vanes)
- Medical (custom-made orthopedic parts, titanium alloy cranial/acetabular implants, artificial hip joints)
- Automotive (prototyping, brake pads with cooling ducts for motorsports)
- Military aircraft components
Suitable Materials
Plastics
- Nylon (including glass and mineral-filled)
- Polypropylene
- Polyetheretherketone (PEEK)
- Polyetherketoneketone (PEKK)
- TPU
Metals
- Aluminum and light alloys
- Chrome-cobalt alloys
- Precious metals (gold, silver)
- Copper and alloys (bronze, brass)
- Inconel®
- Steel (mild, alloy, and stainless steel 316 L and 17-4PH)
- Titanium and alloys
- Nickel and alloys
Post-Processing
Post-processing methods for PBF-printed parts vary based on the material and manufacturing process used. Metal PBF parts made via DMLS or SLM typically need heat treatment to relieve internal stresses caused by the printing process. After heat treatment, support structures are removed, followed by additional post-processing like CNC machining, polishing, or surface treatments.
Metal parts made with EBM, unlike laser-based metal PBF methods, are supported by a semi-sintered powder cake rather than a solid substrate. They must be extracted from the powder bed, but they generally don’t need heat treatment, as the high build temperatures keep residual stress to a minimum. Sacrificial supports may be added for heat control or post-processing. Plastic SLS parts are removed from the powder bed and cleaned to remove excess material, often using bead blasting for a uniform finish. These can be left as-is or dyed for color customization.
Safety Measures
Staying safe while making parts with PBF, just like with most manufacturing processes, should be a priority. Here are some things to consider relating to safety.
- PBF machines emit fumes and fine dust—make sure you’re working in a properly ventilated area to minimize inhalation risks.
- Wear PPE, including gloves, safety glasses, and respirators, when handling powders and operating the machine.
- Avoid touching heated components or printed parts until they have cooled, and be cautious of sharp edges, especially with metal prints.
- High temperatures and sparks pose fire hazards, so keep a fire extinguisher nearby and remove flammable materials from the area.
- Metal powders can be hazardous—handle them carefully and use protective equipment to avoid inhalation or skin contact.
- Regular inspections and maintenance will help prevent malfunctions and ensure safe operation.
FAQs on Powder Bed Fusing Machines
What’s the difference between PBF and DED machines?
PBF machines and DED (directed energy deposition) machines have different strengths and weaknesses, so it's difficult to make a blanket statement about which produces higher-quality solutions. PBF machines are generally better suited for producing high-precision parts with fine details, better surface finishes, and excellent mechanical properties. The powder bed fusion process allows for intricate geometries and precise control over the material distribution, resulting in parts with excellent dimensional accuracy and surface finish, although post-processing is sometimes required. PBF machines can also produce parts in a wide range of materials, including metals, ceramics, and plastics.
On the other hand, DED machines are better suited for producing large parts with complex geometries, such as aerospace components or industrial molds. DED machines are typically faster than PBF machines and can handle larger part sizes, but they may not have the same level of precision or surface finish. The cost of PBF and DED machines can vary depending on several factors, such as the manufacturer, the model, the size, and the features. However, in general, PBF machines tend to be more expensive than DED machines. PBF machines use more advanced technology and are capable of producing parts with higher precision and better surface finish.
How do PBF machines differ from other types of 3D printers?
PBF machines differ from other types of 3D printers in several ways, the main one being how they build parts layer by layer using powdered materials as opposed to filament or resin. While PBF machines use a high-powered laser or electron beam to selectively fuse the material, other 3D printers may use extrusion or photopolymerization methods. PBF machines are more precise and can make functional plastic parts with excellent mechanical properties—better than any other 3D printing technology. However, they often require post-processing to achieve the desired surface finish and may have limitations in terms of size and geometry. PBF machines also tend to be more expensive and require more specialized knowledge and training to operate.
What’s the best material to use with PBF machines?
This will depend on what you need to make and other factors, such as your budget. Each material has its unique properties, strengths, and weaknesses that can affect the printing process. Metals need high temperatures and energy to melt and solidify the material, which can increase printing time and cost. Polymers require lower temperatures and less energy than metals, which could mean faster printing times and lower costs. But it’s worth noting that polymers could have lower-quality mechanical properties than metals and can be more susceptible to warping and deformation. Again, the best material for your project will be based on what properties you need and how much you’ve got to spend.
Why is PBF good for prototyping?
PBF machines allow for faster prototyping, significantly reducing the time and cost required to develop new products. With rapid prototyping, manufacturers can quickly test their design concepts and make improvements before finalizing the production design.
How Xometry Can Help
If you have any questions about PBF machines, or you need help with a specific project, you can reach out to one of our representatives who would be happy to assist. Xometry also offers lots of related manufacturing services including laser cutting, CNC machining, and of course, 3D printing. You can get started today by uploading your designs to the Xometry Instant Quoting Engine®!
Copyright/Trademark
- Inconel® is a registered trademark of Special Metals Corporation
Disclaimer
The content appearing on this webpage is for informational purposes only. Xometry makes no representation or warranty of any kind, be it expressed or implied, as to the accuracy, completeness, or validity of the information. Any performance parameters, geometric tolerances, specific design features, quality and types of materials, or processes should not be inferred to represent what will be delivered by third-party suppliers or manufacturers through Xometry’s network. Buyers seeking quotes for parts are responsible for defining the specific requirements for those parts. Please refer to our terms and conditions for more information.
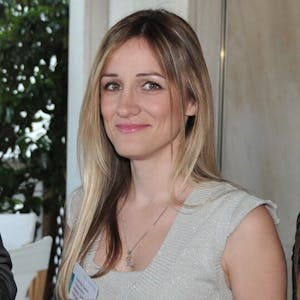