Sintering is a broad family of methods that forms integral and potentially highly complex parts from a wide range of materials, by compressing and then fusing powders and binders. The part goes through two stages. The first stage makes the required shape a weak and poorly integrated, oversize component. The second stage bakes that component to expel the binder material and causes the remaining particles to fuse together and coalesce into a full-strength part. This approach is becoming widespread in metals and ceramics, as a way of producing complex net-shape parts of great mechanical properties by a low per-part cost process that is highly repeatable. This article will define sintering, how it works, the types of sintering, and the different processes.
Figure 1 are examples of sintered parts:
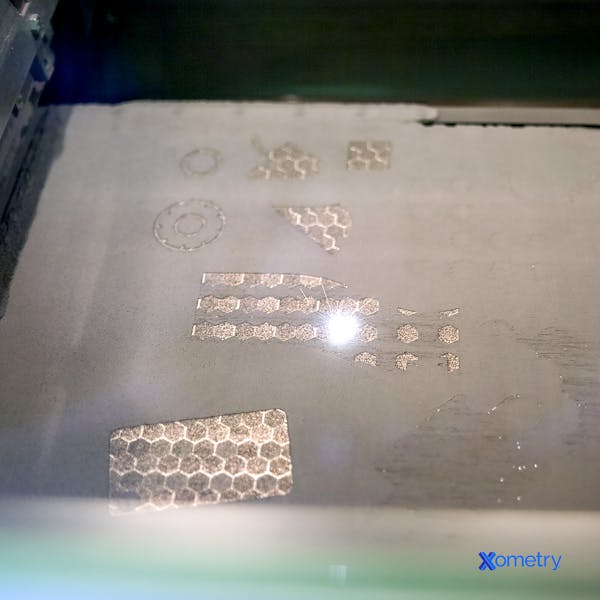
A variety of terms are commonly used to describe processes that are essentially sintering. These include powder metallurgy, MIM (metal injection molding), consolidation, caking, and firing. Powder metallurgy is the process of pressing or injecting metal powders into solid objects. MIM, on the other hand, injects metal powder slurry with a molten polymer into a plastic mold tool. The polymer is then burned away and the temperature is raised to fuse the particles.
Consolidation is widely used in the ceramics industry to describe the similar process of press molding ceramic powders to form solids that are then kiln cured. Caking is used to describe the forming of various powder particles which become bonded together to form a solid “cake”. Lastly, firing describes the heat integration of particle-based forms in the ceramics industry.
The Sintering Process
Sintering works in a three-stage process:
- A primary part powder blend, with a bonding agent, is formed into a desired shape. The bonding agent sticks the powder together to make the shape of the part. This bonding agent can be water but it is more commonly a wax or a polymer.
- When the green part is fired, the bonding agent evaporates or burns away.
- The temperature then rises sufficiently for one of two processes that are essentially identical to occur. Either the primary particles heat enough to just begin to melt, causing the individual particles to fuse at their surfaces, or an intermediate bonding agent such as bronze melts and couples between the particles, leaving the primary component power in an unaltered state.
Different Types of Sintering
Various approaches fall under the broad title of sintering, including:
- Solid-State Sintering: Powdered material is heated to a temperature just below the melting point. This bonds the particles together by atomic diffusion at the grain boundaries.
- Liquid Phase Sintering: Uses the addition of a small amount of a solvent liquid to the powder to induce low porosity and bonding. This liquid is then driven off, generally by heating, to create an integrated solid.
- Reactive Sintering: Uses a chemical reaction of at least one of the phases of powder particles during heating. It alters the chemistry which results in particle coupling in the chemically changed mass.
- Microwave Sintering: A novel approach applied to ceramics. Heat is induced using microwaves, and it is claimed that this results in the faster and more complete integration of the structure.
- Spark Plasma Sintering: Uses an electric current and physical compression of the powder to integrate the powder into a whole.
- Hot Isostatic Pressing: Uses high pressure and high temperature applied to a powder to form the required shape and fuse the particles.
- Cold sintering: Uses a transient solvent and pressure to consolidate polymer powders into a solid mass.
Materials Used in Sintering
As a wide spectrum of techniques, sintering finds application in a huge range of materials. These are listed below:
1. Metals
A wide range of metals can be used in sinter processes of several types. This includes iron, iron-copper, copper steels, nickel steels, stainless steels (300 and 400 series), high-strength low-alloy steels (HSLA), medium- and high-carbon steels, and diffusion hardenable steels, brass, and bronze, and soft iron magnetic alloys. All of these can be built as green parts by 3D printing and then sintered to high-quality, low-porosity parts of excellent properties. Metals can be sintered by pressing, molding, and injection molding. Xometry offers instant quoting on direct metal laser sintering (DMLS), a metal laser sintering process.
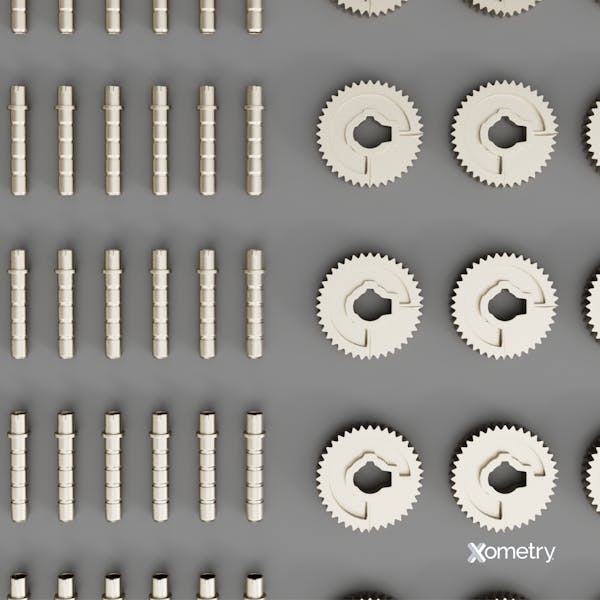
2. Ceramics
Most ceramic processes are considered either sintering or close to sintering. A selection of commonly 3D (SLS or paste deposited) printed and then sintered ceramics are: alumina, aluminum nitride, zirconia, silicon nitride, boron nitride, and silicon carbide. Ceramics are generally sintered by compression or press molding.
3. Polymers
Sintered polymers fall into two categories: large and small particle sintering. Large particle sintering with high porosity is commonly applied as filtration and pneumatic silencer materials and as flow diffusion controllers. These include polyethylene, polypropylene, and polytetrafluoroethylene. Small particle sintered polymers are used in 3D printing in processes such as selective laser sintering. This is used to produce integrated and high-strength components with near-native material properties and near-zero porosity. Examples are polyamides, polystyrene, thermoplastic elastomers, and polyether-ether ketones. Xometry's most popular process is selective laser sintering. You can get an instant quote on it any time.
4. Composites
Sintering of composites is a more complex group of processes, and various materials are processed in different ways. Tungsten carbide uses tungsten and carbon powders. Pressure-heat oxidation transforms the carbon to carbide. This couples the metal powder, which remains unaltered. Glass, carbon, and metal fibers are experimentally included in metal powder sinters, to enhance properties. In some regards, the processing of carbon fiber is a sintering process. An adhesive matrix is compressed and heat activated to bond the carbon component. Metal oxide ceramics are experimentally composited with polymers such as PEEK to manufacture forms of resistive semiconductors. Sintering of composites is highly varied and can be achieved by compression, molding, and in limited cases injection molding.
5. Glass
Various glass materials are used in sintering processes, including: ceramic glazes, silica glass, lead glass, as well as sintered glass slabs made from fused silica glass powder. Sintering of glass is generally done by compression molding.
Steps of the Sintering Process
Sintering consists of a series of steps, each of which is simple but requires great precision in control. The steps include:
- Composition: Add and mix the required primary materials and primary coupling agents.
- Compression: Press the powder (slurry or dry) to the required shape.
- Heat: Heating aims to achieve the removal of the primary coupling agent and fusion of the primary material into a low-porosity whole.
Components Produced Through the Sintering Process
Components that are produced through sintering are listed below:
- Automotive parts such as gears and actuators.
- Electrical components such as switchgear.
- Cutting tools of all types, for milling, drilling, and reaming.
- Aerospace components such as fuel valve components, actuators, and turbine blades.
- Biomedical implants such as prosthetic joints.
Benefits of Creating Your Parts With Sintering
Sintering offers a variety of benefits:
- The process can produce highly repeatable and accurate parts.
- The cost of establishing production is easily amortized over large production.
- Parts can achieve great cosmetic results and require no finishing processes.
- Non-machinable geometries for mass production are easily achieved.
Some Risks in Creating Your Parts With Sintering
Some of the risks of the sintering process including:
- Powder consistency can vary if not well controlled, altering shrinkages or overall component properties.
- Initial forming process controls must be precise to achieve consistent and repeatable results.
- Post-forming “cure” processes are varied and require very tight control to precisely set shrinkage and prevent distortion.
- The cost of establishing production is high, so if the product doesn’t sell this can be wasted.
- Production process variations can result in weak and variable parts.
Summary
Xometry provides a wide range of manufacturing capabilities including CNC machining, 3D printing services, injection molding, laser cutting, and sheet metal fabrication. Get your instant quote today.
Disclaimer
The content appearing on this webpage is for informational purposes only. Xometry makes no representation or warranty of any kind, be it expressed or implied, as to the accuracy, completeness, or validity of the information. Any performance parameters, geometric tolerances, specific design features, quality and types of materials, or processes should not be inferred to represent what will be delivered by third-party suppliers or manufacturers through Xometry’s network. Buyers seeking quotes for parts are responsible for defining the specific requirements for those parts. Please refer to our terms and conditions for more information.
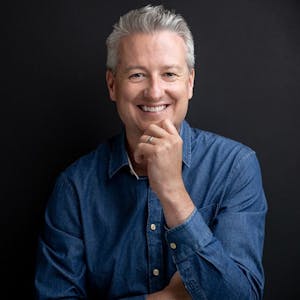