Stereolithography (SLA) is a 3D printing technology that builds parts by polymerizing a liquid photopolymer resin with a UV laser one layer at a time. Fused Deposition Modeling (FDM) is a 3D printing technology that builds parts by extruding a melted plastic onto the build plate one layer at a time. SLA produces parts with excellent surface finish and highly detailed features and can print quicker when compared to FDM. FDM on the other hand is cheaper, has more material options, and produces stronger parts. The main advantage of using SLA is the ability to create high-detail parts, whereas FDM produces functional parts with high strength.
This article will compare SLA vs. FDM in terms of their differences, materials used, and printing technology.
SLA Definition and Comparison to FDM
Stereolithography is a photopolymer-based 3D printing technology. It was first invented by Hideo Kodama in 1980 but commercialized and patented in 1986 by Charles Hull. The process works by shining a UV laser against a scanning mirror. The mirror directs the laser light in a pattern that traces out the cross-section of a single layer of the part. This laser then polymerizes the photosensitive material wherever the laser hits a solid surface – either the build platform or the previous layer. After each layer is polymerized, the build platform typically moves upwards with the part appearing to grow out of the liquid. alternatively, a bottom-up type process is also possible, but uncommon. SLA parts need to be post-processed in a solvent bath to remove excess resin and must be post-cured.
This is in contrast to FDM printers which extrude a plastic filament through a heated nozzle and deposit them onto the build plate. SLA can print parts with significantly better resolution than FDM. However, FDM printers are cheaper in general.
To learn more, see our guide on What is SLA.
Advantages of SLA Compared to FDM
Listed below are some key advantages of SLA vs. FDM:
- SLA has significantly improved resolution and print quality when compared to FDM.
- SLA can print significantly faster than FDM printers without compromising quality.
Disadvantages of SLA Compared to FDM
Listed below are some key disadvantages of SLA vs. FDM:
- SLA printing is significantly more expensive than FDM. This is both in terms of the materials and the machine.
- SLA parts tend to be weaker than FDM parts. This is due to the mechanical properties of photopolymers which are weaker than the thermoplastic materials used in FDM.
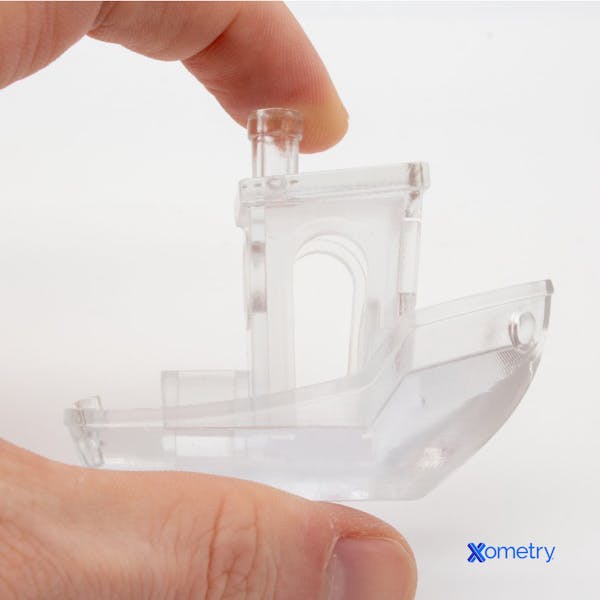
FDM Definition and Comparison to SLA
Fused deposition modeling is the most well-known 3D printing technology. It was first developed by Scott Crump in 1988 who later commercialized the first FDM printer. The process is relatively simple as it involves guiding a thin filament of thermoplastic through a heated nozzle/hot end. The plastic exits the nozzle and is placed on the build plate in the pattern of the part cross-section. Once a layer is complete, the print nozzle moves up one layer and deposits the plastic on the previous layer until the part is complete.
FDM is a simpler technology when compared to SLA. It is significantly cheaper for hobbyists, hence its popularity. There are many different thermoplastics and even flexible thermoplastic polyurethanes available.
For more information, see our guide on What is FDM.
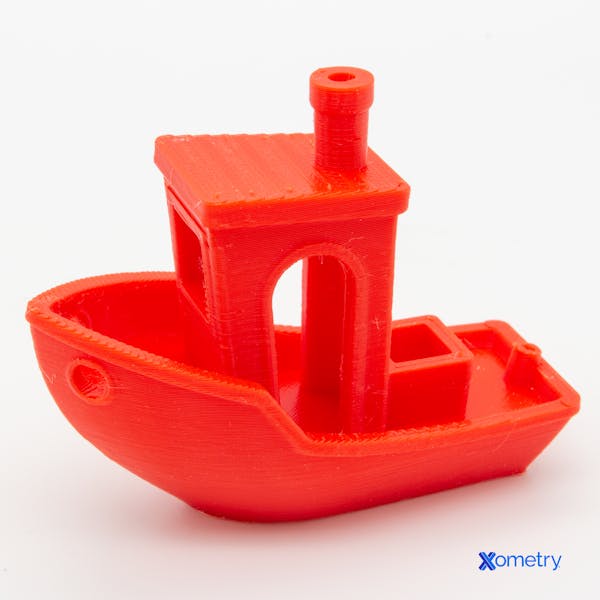
Advantages of FDM Compared to SLA
Listed below are some key advantages of FDM vs. SLA:
- FDM parts are stronger in general when compared to SLA parts. This is due to FDM making use of well-established and widely used thermoplastics that are significantly stronger than photopolymers.
- FDM has a large online community that offers pre-designed parts optimized for FDM. These communities can provide advice and instruction on any possible issue encountered during printing.
Disadvantages of FDM Compared to SLA
Listed below are some key disadvantages of FDM vs. SLA:
- FDM layer lines are very visible. Parts often need to be post-processed to get the smooth surface finishes commonly found with SLA parts.
- Despite the strength of the material used in FDM printing, the parts tend to be highly anisotropic in the direction of the print. This is due to the relatively weak interlayer bonding.
FREE SLA 3D Printing Design Guide
Attribute | SLA | FDM |
---|---|---|
Attribute Print resolution | SLA 25 to 300 Micron | FDM 50 to 500 Micron |
Attribute Typical maximum print volume | SLA 29” x 25” x 21” | FDM 36" x 36" x 24" |
Attribute Wide range of material colors | SLA No | FDM Yes |
Attribute Minimum feature size | SLA 100 Micron (.1 mm) | FDM 1 mm |
Attribute Has isotropic material properties | SLA Yes | FDM No |
Attribute Minimum recommend wall thickness | SLA 0.5 mm | FDM 1.5 mm |
Attribute Parts need support structures | SLA Yes | FDM Yes |
Table. SLA vs. FDM Comparison
SLA vs. FDM: Comparisons
FDM printers can have significantly larger build volumes, whereas SLA printers have much better resolution.
Technology Comparison
SLA and FDM technologies are not directly comparable. Each printer employs a fundamentally different technology and different materials. FDM technology is significantly simpler. It can be assembled by anyone with basic technical skills. However, SLA machines require specialized knowledge and tools to assemble. SLA makes use of a laser to solidify the part, whereas FDM simply allows the plastic to solidify through natural cooling.
Material Comparison
SLA resin is provided in liquid form. In general, the materials are relatively proprietary and cannot be exchanged between printers. Very few colors are available, and the material range is limited. FDM material is far more common and comes in any color. It also has fillers like carbon fiber to improve part strength. Most FDM machines can easily accept filaments from different suppliers.
Product Applications Comparison
SLA is suited to applications that need very fine detail while also not needing exceptional mechanical strength. These applications can include: jewelry patterns for molding, display figurines, and visual prototypes.
FDM is typically used by hobbyists and professionals to print functional and non-functional plastic parts. FDM materials offer more strength and the material properties cover a wide spectrum. Typical applications can include: jigs, brackets, and functional prototypes.
Print Volume Comparison
FDM printers have a wide range of build volumes, from as small as desktop printers to printers with a build volume of up to a cubic meter. SLA however has smaller build volumes due to the need to keep liquid photopolymer resin stored in the printer.
Surface Finish Comparison
SLA produces excellent surface finishes that are significantly better than those possible with FDM printing. FDM parts have visible layer lines that need to be removed with sanding or vapor smoothing, which is only possible with some materials.
Cost Comparison
SLA is significantly more expensive than FDM. This is due to the specialized nature of the photopolymers used in SLA. The high-precision UV laser required to print parts with the quality SLA is known for also adds to the cost. FDM printers can be bought for as little as $200 whereas an entry-level SLA printer can cost at least $1,295.
Alternative to SLA and FDM
Despite the benefits of SLA and FDM, there is an alternative technology that can achieve similar results:
- Polyjet: Polyjet printing is an advanced technology that works by spraying photopolymer drops onto a build plate. A UV light then passes over these droplets to solidify the layer. The next layer is then deposited on the top of the previous one until the part is complete. Polyjet printers have extremely high resolution, typically below 50 microns. The technology can be used to create multi-material parts that simulate rigid and rubber-like materials in a single print. At Xometry, our PolyJet printers are also capable of full-color prints, allowing you to print the part with not only custom colors but textures and images as well. Learn more by visiting our PolyJet printing service page.
How Xometry Can Help
We hope this article has helped clear up any questions you had between the SLA and FDM printing technologies.
At Xometry we offer nine different custom 3D printing services, including SLA printing and FDM printing! We have dozens of materials to choose from to fit your project's unique requirements. Best of all, we offer instant quoting on all of our 3D printing processes. You can start by uploading your 3D CAD files to the Xometry Instant Quoting Engine® and get instant pricing and lead times today!
Disclaimer
The content appearing on this webpage is for informational purposes only. Xometry makes no representation or warranty of any kind, be it expressed or implied, as to the accuracy, completeness, or validity of the information. Any performance parameters, geometric tolerances, specific design features, quality and types of materials, or processes should not be inferred to represent what will be delivered by third-party suppliers or manufacturers through Xometry’s network. Buyers seeking quotes for parts are responsible for defining the specific requirements for those parts. Please refer to our terms and conditions for more information.
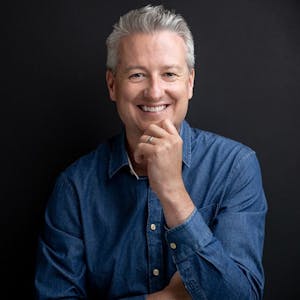