SLS and SLA do have a few similarities; they’re both 3D printing methods, and they both use lasers. But the way they work, how much they cost, and their capabilities differ quite a bit. If you’re not familiar with either (or both) of these options, read on to learn all about them, how they work, and the ways in which they are different.
What is SLS?
SLS (selective laser sintering) is a type of 3D printing invented in the ‘80s by Drs. Deckard and Beaman at Austin’s University of Texas. An SLS 3D printer makes solid parts by fusing powdered particles (like plastic, metal, glass, or ceramic) together with a powerful laser. While most SLS machines use nylon- or polymer-based materials, more high-end machines can work with materials with higher melting points. You can see how this machine is made up in the below image.
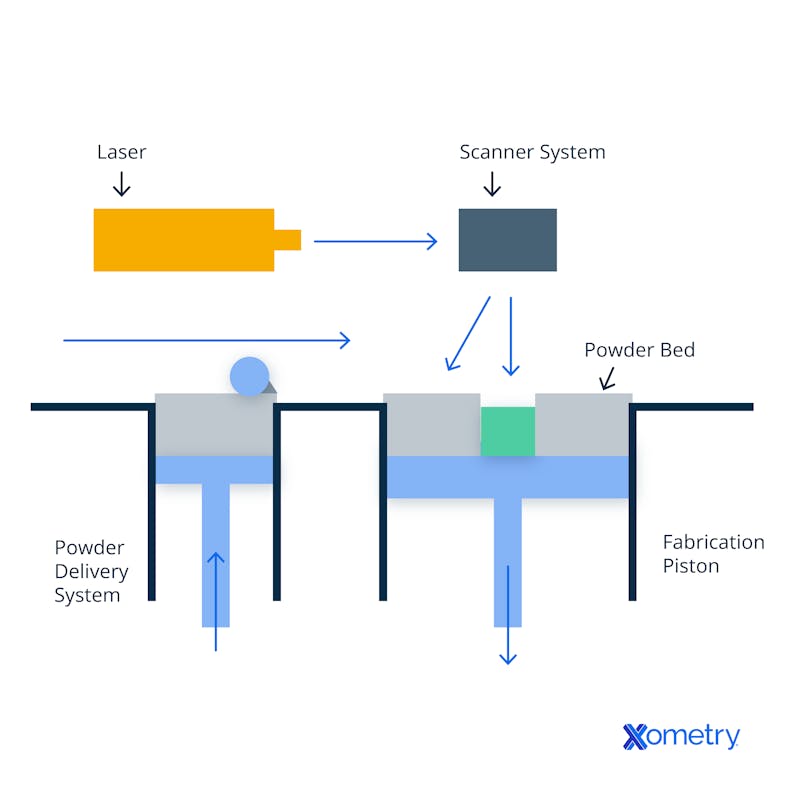
An SLS printer takes a digital design made on a computer and turns it into a physical model by first breaking it into 2D slices and then tracing them out individually. It then bonds the powder when necessary. It will then add more powder after each layer and the whole process repeats. Parts made with these printers are known for being tough, with great mechanical properties, but since the machine needs to be completely shielded and closed up during printing, you likely won’t be able to see your print until it’s finished. Here’s an example of an SLS-made part:
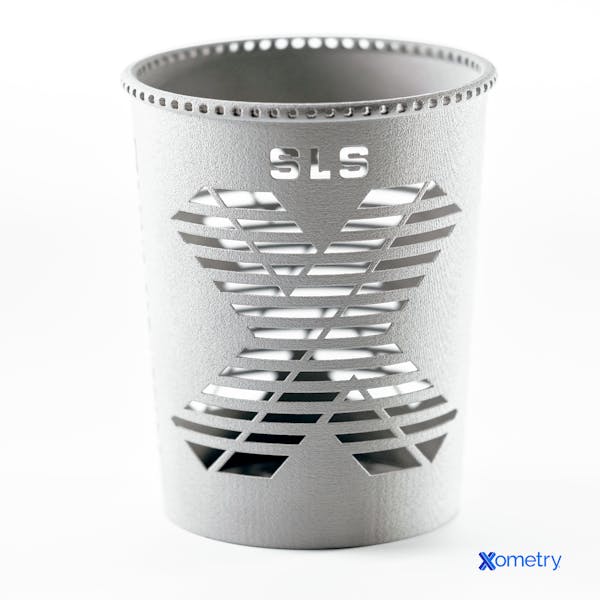
Another advantage SLS offers is that you don’t need any support structures during printing—the surrounding powder can actually provide support for any overhanging parts. A lot of our customers use it for their time-sensitive projects as it’s very quick. If you’re interested in buying one of these printers for your business, prepare to make a substantial investment. SLS machines are not only expensive to buy, but they also use up a lot of electricity, racking up those utility bills. You’ll also want to make sure you’ve got enough space in your office or lab for them as they’re on the bulky side.
What is SLA?
SLA, an abbreviation for stereolithography, is also a form of 3D printing that’s considered the oldest around. Invented in 1986 by 3D Systems’ founder Chuck Hall, SLA builds parts in a more peculiar way… upside down. It uses a type of laser, but this time it’s an ultraviolet laser that cures photosensitive resin into whichever shape you’ve chosen. While it prints, the build plate is always in contact with the resin tank. The laser points at specific parts until they’ve solidified, and then the plate raises out of the reservoir so the next layer can be cured. As this happens, each layer fuses with the one prior, and the whole process almost looks like the part is rising out of the liquid. You can see how these printers work in the following image:
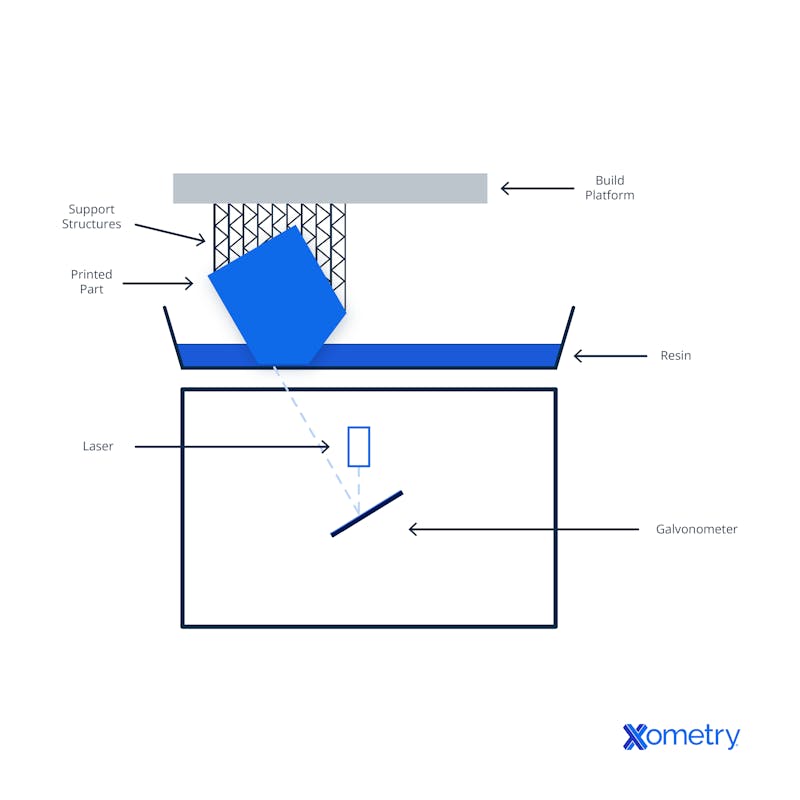
Around six years after it was initially introduced, the printer got a big upgrade that made it capable of printing more complex parts and much more quickly. It’s still used today, especially when tight tolerances are needed. SLA printers can make parts with great resolution and surface finishes (like injection-molded parts), and they’re much smaller than SLS machines and can fit on an average desk. Their small size does mean that they’re not able to print larger parts like an SLS printer.
Also, the resin used isn’t environmentally friendly, and the fumes can be quite nasty (remember to wear gloves and all the necessary PPE). Some polymer powders like nylon, though, aren’t too bad unless you have specific allergies. Finally, SLA parts are not as strong as SLA parts. That’s why they’re better for proofs of concept or experiments. The following picture shows some SLA 3D printed tags we made here at Xometry:
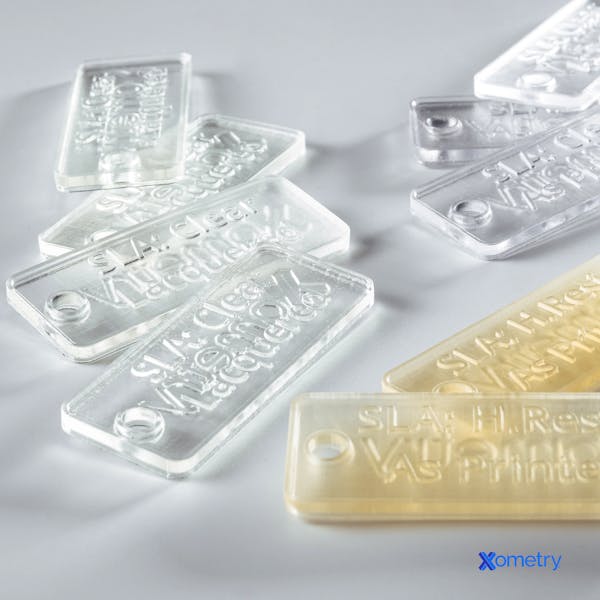
Attribute | SLS | SLA |
---|---|---|
Attribute Sensitivity to UV light | SLS No | SLA Yes |
Attribute It makes rough surface finishes | SLS Yes | SLA No |
Attribute It’s limited regarding material compatibility | SLS Yes | SLA No |
Attribute The process is quick | SLS Yes | SLA No |
SLS vs. SLA Comparison
What other compatible materials are there for SLS and SLA printers?
There are a few different materials that can be used with these machines. When it comes to SLS printing, it’s quite normal to use materials like thermoplastic elastomers, polyaryletherketones, polystyrenes, and nylon. For SLA, you’d normally use something like epoxy photopolymer, acrylic photopolymer, and other materials with polypropylene- or ABS-like properties.
How much do SLS and SLA printers cost?
Obviously, the cost involves more than just purchasing the machine and your first batch of material. Costs will accrue depending on use. But as a general rule, SLS machines can be found for as low as $10,000 and can be as expensive as $650,000, depending on the type of machine and what you want it to do. SLA machine prices are a lot easier on the eyes—and wallet—with costs varying between $3,750 and $5,000, depending on size. Usually, when purchasing a machine like this, it might help you to understand which category it falls under: DIY, advanced hobbyist, professional and performance, or business and industrial.
Are there any alternatives to SLS and SLA?
Of course. The mutual alternative to both would probably be MJF—or multi-jet fusion. It can be used to make functional prototypes, proofs of concept, and end-use parts and doesn’t need a high-powered laser to do so.
Here are some specific SLS alternatives:
- SLM (selective laser melting) uses metallic powder rather than polymer.
- EMB (electron beam melting) melts and prints metal parts under a vacuum with an electron beam.
- FDM (fused deposition modeling) uses a heated nozzle to melt and create layers of filament material.
There are two main alternatives to SLA:
- MJ (material jetting) machines use an inkjet-like print head that sprays liquid photopolymer in the pattern of the cross-section of the part. After the spraying, a UV light is used to cure the polymer.
- DLP (digital light processing) printers expose only parts of photopolymer resin to UV light to cure them. Unlike SLA, though, DLP printers use a projector light and thousands of tiny mirrors to direct it to or away from the print bed.
How Xometry Can Help
If you still have questions about SLS, SLA, FDM, or any other type of 3D printing, feel free to reach out to one of our representatives who will be happy to assist. Xometry also offers a vast array of manufacturing services, including CNC machining and laser cutting. Get started today by requesting a free, no-obligation quote.
Disclaimer
The content appearing on this webpage is for informational purposes only. Xometry makes no representation or warranty of any kind, be it expressed or implied, as to the accuracy, completeness, or validity of the information. Any performance parameters, geometric tolerances, specific design features, quality and types of materials, or processes should not be inferred to represent what will be delivered by third-party suppliers or manufacturers through Xometry’s network. Buyers seeking quotes for parts are responsible for defining the specific requirements for those parts. Please refer to our terms and conditions for more information.
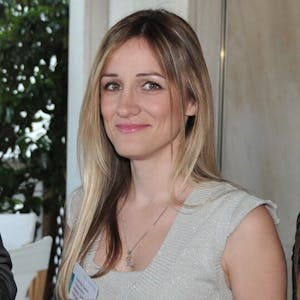