You’ll have no trouble finding a 3D printing method that works for the products you’re trying to build. The difficulty comes down to deciding between different additive manufacturing options. When you’re shopping around for options, two types that often go head to head in comparison are selective laser sintering (SLS) and selective laser melting (SLM), and understanding what both can offer makes it easier to determine what’s best for the products you’d like to develop.
What Is Selective Laser Sintering (SLS)?
Its name gives a pretty good idea of what SLS does. It uses a laser to sinter powder together into a layer and repeats this process until the full design is finished. This type of 3D printing came out of the University of Texas in the 1980s, but the patent has since expired, meaning that it’s a technology option many companies have redeveloped and lessened the price of.
To create parts with SLS, a CO2 laser is programmed to sinter and fuse together a polymer-based powder until it forms a layer. It’ll then create another layer until your build is complete. Then, it’ll need a period to properly cool off (usually 12 hours at the very least) and time for blasting and finishing. You can see an example of a product we made through SLS in the photo below.
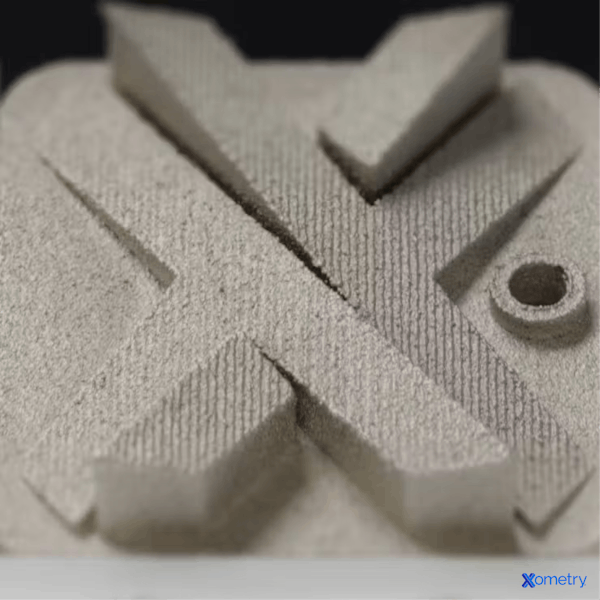
What Is Selective Laser Melting (SLM)?
This kind of 3D printing method came to be in the early 21st century from Fraunhofer Institute in Germany. SLM also uses a high-powered laser on powders, but it melts it rather than sinters and works with metal powders instead of plastic ones. It builds up layers through additive manufacturing, too, and does so in a more controlled environment filled with inert gases like argon and nitrogen. Below, you can see a photo of an SLM printer.
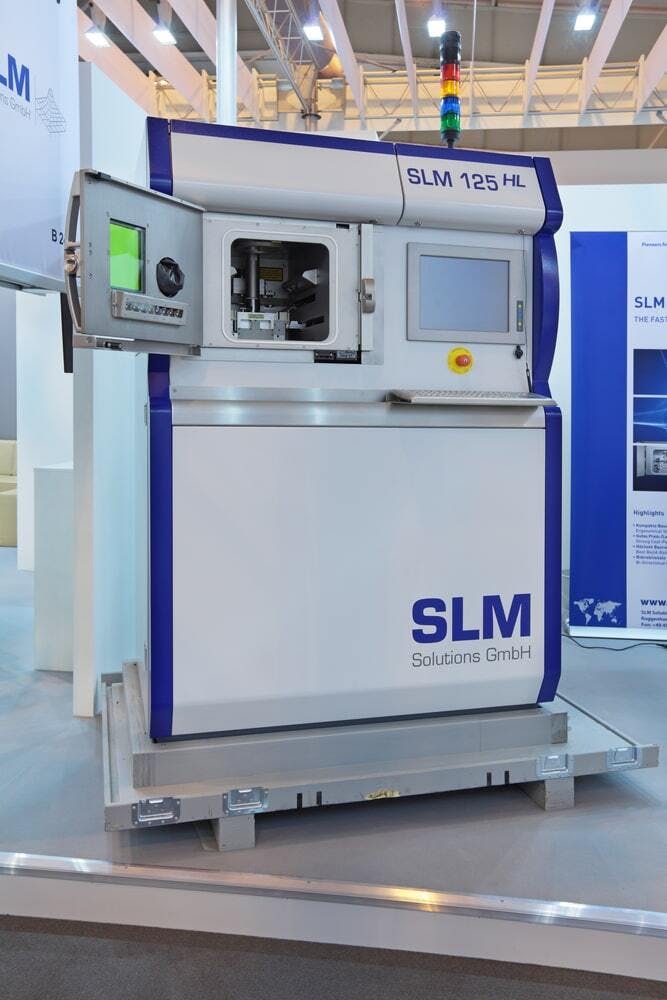
Property | SLS | SLM |
---|---|---|
Property Uses thermoplastic powders | SLS Yes, such as Nylon 11 and Nylon 12 | SLM No |
Property Uses metal powders | SLS No | SLM Yes, including pure metals and alloys |
Property Inert gas needed | SLS No | SLM Yes |
Property Extensive range of materials | SLS No | SLM Yes |
Property Used for small to medium prototypes and production runs | SLS Yes | SLM Yes |
Property Extensive post-processing required | SLS Yes | SLM No |
Property Need for supports while printing | SLS No | SLM Yes |
Property Complex geometries possible | SLS Yes | SLM Yes |
Property Costly | SLS Yes | SLM Yes |
Property Print volume | SLS Up to 550 x 550 x 750 mm | SLM Up to 350 x 350 x 350 mm |
Property Advantages | SLS Excellent mechanical properties, no supports are necessary even for complex designs, and powders can be recycled and reused | SLM Rarely requires post-processing for a clean finish, has quicker lead times, and cheaper tooling costs |
Property Disadvantages | SLS Can leave a grainy finish or texture, long lead times, warping, holes, and over-sintering is possible, especially on large, flat surfaces | SLM Systems are expensive to run, post-processing is necessary, and you need more material to provide support for overhangs |
SLS vs. SLM Comparisons
How are SLS and SLM similar?
These two printing types are similar in that they both use high-powered lasers to create layers and, thus fully made parts. They’re both great methods for prototyping and can both quickly and efficiently print products—even with complex designs.
What are the costs of SLS vs SLM?
Both 3D printing methods can be pretty expensive due to the technology and type of machinery needed. That said, SLS printers tend to be slightly less, ranging between $18,000 and $100,000, whereas SLM machines range between $55,000 to $350,000.
How Xometry Can Help
We have a long list of 3D printing technologies you can use here at Xometry, including SLS. Other options you can snag a free quote for are fused deposition modeling, stereolithography, and PolyJet.
Disclaimer
The content appearing on this webpage is for informational purposes only. Xometry makes no representation or warranty of any kind, be it expressed or implied, as to the accuracy, completeness, or validity of the information. Any performance parameters, geometric tolerances, specific design features, quality and types of materials, or processes should not be inferred to represent what will be delivered by third-party suppliers or manufacturers through Xometry’s network. Buyers seeking quotes for parts are responsible for defining the specific requirements for those parts. Please refer to our terms and conditions for more information.
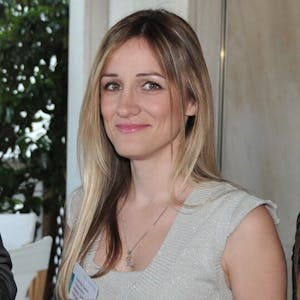