3D metal printing is one of the newest classes of 3D printing and it's an important part of what we do at Xometry. We offer binder jetting and direct metal laser sintering (DMLS) in our instant quoting engine.
In general, printing of metals falls into two material formats: building models by fusing metal powders or by the use of metal filaments (wire). The “liquid” origin materials are less common but are still bonded-powder based. While the development has been fast, metal 3D printers are expensive and require specialized skills to operate.
This article will discuss the four types of metal 3D printing processes and their corresponding materials.
1. Metal Powder Bed Fusion 3D Printing (SLS, SLM, DMP)
Powder 3D printer systems are referred to as Powder Bed Fusion (PBF) or Powder Bed Additive Manufacture (PBAM). This 3D printing technique uses either an electron beam, laser, or heat to melt and fuse metal. Common metal 3D printer processes are SLS (Selective Laser Sintering), SLM (Selective Laser Melting), and DMP (Direct Metal Printing — or commonly known as DMLS (Direct Metal Laser Sintering)). PBF works by depositing powder onto the build table and spreading it across the platform using a roller or recoater blade. A laser is scanned over the build area and pulsed to melt the powder. The table descends by the layer thickness, and the process repeats until all layers are printed.
Table 1 below summarizes the pros and cons of metal powder bed fusion 3D printing.
Pros | Cons |
---|---|
Pros Intrinsic support from the powder bed, no supports required | Cons Some manufacturers offer a limited range of material compositions |
Pros Smooth surfaces direct from the printer | Cons Requires high-quality, expensive lasers |
Pros 20 µm minimum layer thickness, commonly 35–50 µm | Cons Some systems offer relatively slow build |
Pros Builds more-porous parts | Cons High residual stresses result from unstable melt pools |
Pros | Cons Printed parts are not equally strong or resilient from all processes; always weaker and more fracture prone than EBM parts |
2. Directed Energy Deposition (DED)
DED (Directed Energy Deposition) is a metal 3D printing process that uses a focused energy source. This energy can either be a laser, a plasma arc, or an electron beam. DED uses powder and wire to create 3D printed parts. The DED powder and DED wire processes are quite different from PBF but similar to each other. With DED, deposition and fusion of metal occur at the same time. A nozzle deposits material into the energy source. The feedstock is melted and deposited as the X-Y traverse of the printhead progresses. When the layer is complete, the build table drops by the layer thickness resolution and the process repeats. When the build is complete, the part can be removed from the build table. Post-machining may be required for surface finish issues.
Table 2 below shows the pros and cons of DED.
Pros | Cons |
---|---|
Pros Fast printing speed | Cons Equipment costs are very high |
Pros Printed parts have high density and strength/resilience | Cons Support structures cannot be built, so overhangs are not printable, limiting applications |
Pros Can be used for repair of high-quality functional parts | Cons Relatively low build resolution |
Pros Large build tables available | Cons Poor surface finish requires post-processing |
Pros Native material properties in parts | Cons |
Pros Allows production of parts with minimal tooling | Cons |
Pros Reduced material waste | Cons |
Pros Can build parts with custom alloy (multi-material range capability) | Cons |
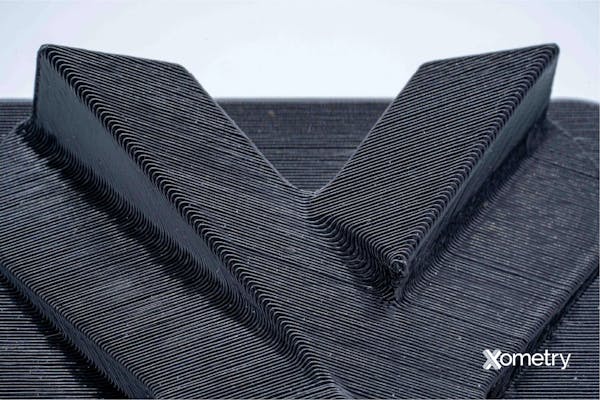
The fusion filament processes of FDM (Fused Deposition Modeling) and FFF (Fused Filament Fabrication) in metal printing are in the early stages and have obstacles to overcome. Metal filament extrusion works by heating a filament made from both thermoplastic material and metallic particles. The filament is drawn through a nozzle and deposited on the build platform, layer-by-layer. The complete part is placed in a sintering furnace to burn out the plastic and sinter the metal. Metal filament extrusion is most useful for making metallic-looking parts that can be as accurate and detailed as plastic FDM.
Table 3 shows the pros and cons of metal filament extrusion.
Pros | Cons |
---|---|
Pros No special build environment – room temp, normal atmosphere | Cons Difficult post-process to sinter parts |
Pros FFF stresses in printed parts | Cons Shrinkage makes dimensions in the finished part hard to control |
Pros Wide range of materials on the same machine | Cons Part accuracy is largely unrelated to X-Y-Z resolution of print |
Pros Lower-cost equipment | Cons Parts are low density and relatively weak after sintering |
Pros Lower technical skills required in operation | Cons |
Pros Great for prototypes | Cons |
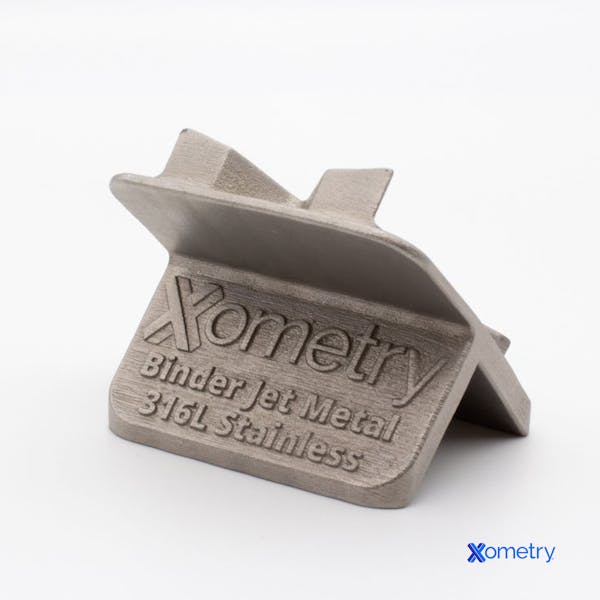
Binder jetting is similar to the various PBF techniques, except that the particles are bonded with an adhesive that is deposited to build layers via an inkjet. Material jetting, on the other hand, is a distinct process that is similar in many regards to DED but is closest in nature to PolyJet. In binder jetting, the first powder layer is laid down; then, a printhead passes over the layer applying adhesive to bind the slice. The table drops by the z-build height, and the process repeats until the model is complete. Material jetting works with the layer inkjet printed in a powder-loaded UV-cured polymer matrix. This forms the layer and is cured in place by a UV light source. The table drops by the layer thickness, and the process are repeated until the “green” model is completed. Binder jetting and material jetting must account for the shrinkage on 3 axes when scaling the print. A precise result can be achieved, however, with good control of the sintering process. While the processes are different, there are several similarities in the pros and cons of binder jetting and material jetting. These similarities are shown in table 4 below.
Pros | Cons |
---|---|
Pros No special build environment—room temp, normal atmosphere | Cons Two-stage process—powder bed is laid down, then the adhesive is ink-jetted to bond the layer |
Pros No internal stresses in printed parts | Cons Delicate post-process to sinter parts |
Pros Wide range of materials on the same machine with no alteration in setup | Cons Dimensional control requires finesse to ensure correct shrinkage |
Pros Lower-cost equipment | Cons Finished part accuracy is not purely a result of X-Y-Z resolution of print |
Pros Lower technical skills required in operation | Cons Parts are brittle and vulnerable before sintering |
Pros 35 µm minimum layer thickness | Cons |
Select the Best Metal 3D Printing Process for You
Selecting the best type of 3D printing is complex. Below are useful steps to go through when deciding which metal 3D printing processes to choose:
- Review part requirements. For example, give consideration to the layer resolution, the need for the reproduction of fine detail, as well as the required mechanical properties and cosmetic quality considerations.
- Choose a material family for the part.
- Once the material has been selected, review the available processes that use that material to consider the best one to produce the desired results.
- Check the availability of resources, including suppliers for the material, time, and costs.
Common Metal 3D Printing Materials
There is a long and growing list of metal-type options in metal 3D printing materials. The most common metal types are:
- Stainless Steel: Generally in 3 alloy groups: 304, 316, and 17-4. These are corrosion-resistant and of high strength when not porous.
- Tool Steels D2, A2, and H13: Have high strength, are hardenable, wear-resistant, and are applicable for dies and tools.
- Titanium and Ti64: Materials that are ideal for lightweight parts and have high strength.
- Aluminum 7075, 4047, 6061, 2319, 4043: These are various lightweight alloys for general, lightweight components.
- Inconel® 718, 625: These have low corrosion and high-temperature resistance for purposes such as engine parts.
- Cobalt Chrome: Superalloy for biomedical and aerospace applications.
- Gold/Silver: Pure metals for jewelry and limited biomedical uses.
- Niobium, Niobium-Zirconium: These are high-temperature and high–chemical–resistance alloys for aerospace use.
- Tantalum: Similar to Niobium but with better chemical resistance.
- Hastelloy® Nickel Chromium: Materials that are tough—temperature-resistant and crack-resistant. Commonly used for turbine and nuclear components.
- Tungsten and Alloys: Materials with super-high density. Used commonly for radiation shields, collimators, and engine parts.
Summary
Xometry provides a wide range of manufacturing capabilities, including metal 3D printing for all of your prototyping and production needs. Get your instant quote on metal 3D printing and more today.
Copyright and Trademark Notices
- Inconel® is a registered trademark of Huntington Alloys division of Special Metals Corp., Huntington, WV.
- Hastelloy® s a registered trademark of Haynes International, Kokomo, Indiana.
Disclaimer
The content appearing on this webpage is for informational purposes only. Xometry makes no representation or warranty of any kind, be it expressed or implied, as to the accuracy, completeness, or validity of the information. Any performance parameters, geometric tolerances, specific design features, quality and types of materials, or processes should not be inferred to represent what will be delivered by third-party suppliers or manufacturers through Xometry’s network. Buyers seeking quotes for parts are responsible for defining the specific requirements for those parts. Please refer to our terms and conditions for more information.
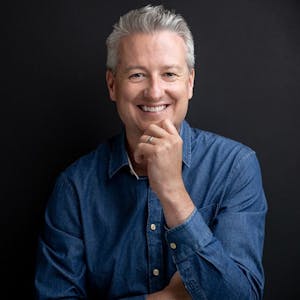