In the context of 3D printing, extrusion is the process whereby a semi-liquified slurry or paste is squeezed through an orifice or die to make a cylindrical (or other) shaped line of the material. It then hardens or cures, allowing a new layer of extruded material to be laid on top. Both fused deposition modeling (FDM) and fused filament fabrication (FFF) print using this technique.
Though S. Scott Crump’s first version of the FDM process used a glue gun, the technology has been refined to become far more precise and flexible. Material extrusion can employ a wide variety of materials such as polymer filaments, polymer pellets, wax filaments and pellets, ceramic slurries, and polymer bonded metal powder filaments.
This article will define and discuss the process, history, and applications of material extrusion as it relates to 3D printing.
What Is Material Extrusion In 3D Printing?
In the realm of 3D printing, the extrusion process means pushing bond-ready material through a heated nozzle in order to deposit it in successive layers. Each layer is effectively a 2D “slice” of the 3D object. Most printers heat either a polymer or wax to a gel-like state in order to make the material printable. Those materials may be modified with additives that give them desirable properties in either the gelled state (i.e. viscosity controllers) or the solid state.
For more information, see our guide on what to know about 3d printers.
What Materials Are Used in Material Extrusion?
Material extrusion machines can be designed to print the following:
- Polymers such as PLA, ABS, ASL, and nylon are common and receive a wide range of additives. Some others are technically waxes, but they function much the same as polymers.
- Ceramics are 3D-printed to form (generally artistic) pottery. The nozzles for this purpose are 10-50 times the size of plastic extruders.
- Concrete and various construction materials have garnered recent attention as 3D printing options. The idea is to print entire buildings, and the process differs from FDM primarily just in scale.
Where Is Material Extrusion Used?
Material extrusion is primarily used in FDM prototyping. This additive manufacturing method is more popular than others for this purpose because it is the cheapest, most accessible option. FDM prototypes are used in various industries, including marketing and product development. The parts are produced quickly and are usually functional enough for developers to test features (as long as they’re no smaller than 1-2 mm). The prototypes are not high-performance pieces, though.
When Did the First Material Extrusion Technology Emerge?
The material extrusion technology was first predicted by a science fiction author, Murray Leinster in his 1945 short story ‘Things Pass By.’ The real process, however, took practical form in the late 1980s and was commercialized by Stratasys. This became the backbone of the 3D printing sector.
What is the Registered Name for Material Extrusion?
Stratasys registered material extrusion under the name “fusion deposition modeling,” or FDM. Though the patents have expired, they still have rights to the name, though Stratasys does not appear to police it closely. Many other manufacturers call their process “fused filament fabrication” (FFF) even though the FDM moniker is more widely understood.
What Is the Material Extrusion Process?
Material extrusion in the 3D printing realm involves forcing polymer or wax feedstock through a temperature-controlled nozzle. This softens the material to a viscous fluid or near-fluid state so it can be applied to a build table or existing printed model layer. Each layer is effectively two-dimensional, but they combine to create a 3D construction.
The polymer (or wax) is heated in the nozzle until it reaches a gelled state. The material should be sufficiently melted to flex and bond with surrounding (cooler) materials but not so liquid that it flows away from the application point. The extruded material then rapidly cools and solidifies so that the next layer can be applied on top of it.
What Are the Advantages of Material Extrusion?
Material extrusion, as it applies to FDM/FFF 3D printing, offers several advantages:
- Polymers can be printed at low temperatures, so the printing equipment is simple and inexpensive.
- Very little process maintenance is necessary. Once machine settings are optimized, a printer can run unsupervised for very long periods.
- Extrudable materials are among the cheapest in the 3D printing sector. They are available from a wide range of competing suppliers.
- Models can achieve sufficient cosmetic and mechanical standards to be useful in a wide range of applications.
- FDM/FFF printers are cheaper and operate with lower overheads than other 3D printers. This gives them the lowest price tags of any 3D printing system.
What Are the Disadvantages of Material Extrusion?
The disadvantages of material extrusion are:
- Parts printed using material extrusion can exhibit as little as 20% of the material’s typical strength. The models tend to be intrinsically weak.
- The cosmetic finish often leaves much to be desired. FDM cannot print at high resolutions either in the X-Y direction or the Z-axis. More expensive equipment is better than cheaper systems. The process, however, is best suited to relatively coarse models that lack fine details and do not need precise surface finishes.
- Because the material is hot when it’s applied, many models retain internal stresses which distort them as they cool. The more expensive printers have heated build chambers that can help to reduce this effect.
- Intra-layer bonding is quite poor in some materials. This results in severely anisotropic properties. Some materials bond better than others, but there are always trade-offs in their properties.
What Is the Difference Between Material Jetting and Material Extrusion?
Material jetting and material extrusion differ in several ways:
- Process: Extrusion applies partially melted material in lines and dots. It has a minimum point resolution of between 0.5 mm and 1 mm in diameter (depending on the printer and specific plastic or wax). Material Jetting processes are an order of magnitude more precise, applying liquid resins with a dot size often smaller than 0.05 mm.
- Layer Construction: Extrusion-based systems use a single applicator nozzle (at any given moment) to build a model, which limits the build speed. Material jetting processes use inkjet printheads up to 100 mm wide to ‘draw’ wide stripes of a layer in a single table pass. This additional width makes each layer’s construction considerably faster.
- Z-Layer Builds: Extrusion-based systems have the advantage of building relatively thick layers. These are rarely thinner than 0.1 mm and often can be as much as 0.5 mm thick. Material Jetting layer thicknesses are generally 16 µm to 50 µm. This means that more layers are required to build up the Z height, making builds generally slower overall, despite the fact that each layer prints quickly.
- Cost of Equipment: Extrusion-based FDM/FFF technology is simple, making the machines among the cheapest of any 3D printers. Material Jetting is delicate and complex, so the equipment is generally 1-2 orders of magnitude more expensive than FDM/FFF.
Summary
This article reviewed the concept of material extrusion as it applies to 3D printing technology. To learn more about material extrusion and to determine if it is the right technology for your application, contact a Xometry representative.
Xometry provides a wide range of manufacturing capabilities, including 3D printing and value-added services for all of your prototyping and production needs. Visit our website to learn more or to request a free, no-obligation quote.
Disclaimer
The content appearing on this webpage is for informational purposes only. Xometry makes no representation or warranty of any kind, be it expressed or implied, as to the accuracy, completeness, or validity of the information. Any performance parameters, geometric tolerances, specific design features, quality and types of materials, or processes should not be inferred to represent what will be delivered by third-party suppliers or manufacturers through Xometry’s network. Buyers seeking quotes for parts are responsible for defining the specific requirements for those parts. Please refer to our terms and conditions for more information.
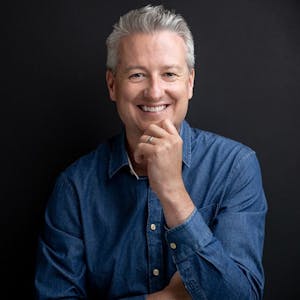