Comparing Additive vs. Subtractive Manufacturing
One of the most important up-front decisions when designing a new product is the choice of manufacturing technology. This is often when the comparison of additive vs. subtractive manufacturing comes into play. This article aims to compare these, highlight the benefits of each, and make suggestions on when to use them.
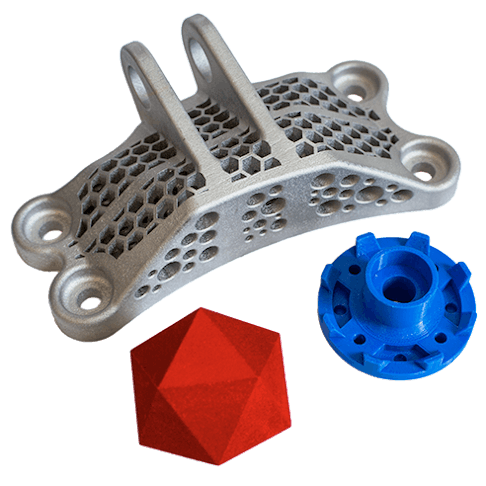
What is Subtractive Manufacturing?
Subtractive manufacturing refers to the process of removing material from raw stock supplied in plates, bars, billets, or other bulk forms. Rotating or stationary tools are employed to strip material away until the part takes on the right shape. This is the most common method used to manufacture metal parts, but plastics can also be manufactured using subtractive technologies. The vast majority of modern subtractive machines are CNC-based as manually operated machines cannot compete with the speed and precision of computer-controlled systems.
Subtractive Manufacturing Technologies
When it comes to additive vs subtractive manufacturing methods, the latter has a wide range of mature technologies that haven’t fundamentally changed over the past few decades. The most common are listed below.
1. Turning
Turning is performed on a machine called a lathe. It works by spinning material in a chuck or collet while a stationary tool is introduced into the side of the material. The cutting tool is moved parallel (Z-axis) and perpendicular (X-axis) to the axis of rotation. The tool typically does not move on the Y-axis at all. CNC lathes can simultaneously control a tools’ position along the X and Z axes to create complex geometries. Turning is ideal for cylindrical parts like shafts. There are many different configurations from very simple and cheap lathes to Swiss-style machines that can produce complex multi-feature parts to heavy-duty multi-spindle lathes.
2. Milling
Milling works by fixing a billet of raw material in a vice attached to the machine bed while a spinning tool is moved into contact to cut away material. Milling machines can be supplied with 3, 5, or 6 degrees of freedom. More degrees of freedom allow the machine to create more complex features. However, such machines are also more expensive to purchase and operate. Milling machines are ideal for multi-featured flat-faced parts.
3. Profile Cutting
Profile cutting is another type of subtractive technology that can create flat parts by cutting out a profile using a beam of energy (plasma or laser) or a high-pressure stream of water (waterjet). Each of these technologies has advantages and disadvantages. For example, waterjets can cut through thicker plates than laser cutters but require a lot more maintenance and auxiliary equipment.
4. Electrical Discharge Machining
Electrical discharge machining (EDM) is an advanced subtractive technology that removes material using an electrode to erode material from the part’s surface without ever touching it. This process is also known as spark erosion. EDM can produce highly accurate parts and can cut any conductive metal. The cutting/erosion tool can either be a wire to create profile parts of almost any thickness or a specially shaped electrode to create complex geometries for injection molds.
Advantages of Subtractive Manufacturing
There is a reason subtractive manufacturing is so common. When comparing additive vs subtractive manufacturing, this more classical method offers the following advantages.
1. Accuracy: Subtractive machines can be extremely accurate when compared to additive ones. Additive parts that need high-accuracy features often need to be machined after printing.
2. Surface Finish: CNC machines can achieve smoother, more precise surface finishes than additive machines.
3. High Production Volume: CNC machines can achieve much higher production rates than additive machines and can be easily set up to automate production runs. Raw material can be automatically loaded into the machine and completed parts can be removed without any human intervention.
When it comes to metal additive vs. subtractive manufacturing, the long history of subtractive technologies offers a more well-developed body of manufacturing knowledge. Subtractive is typically a safe bet when manufacturing metal parts.
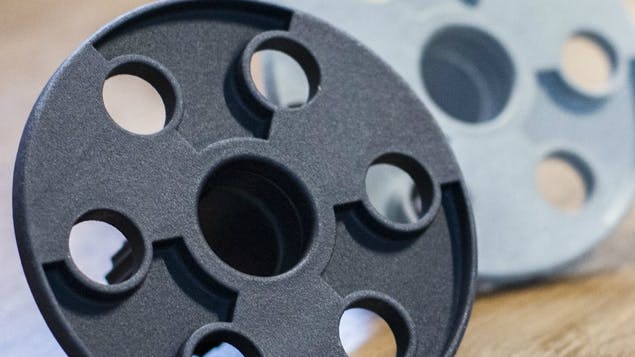
Parts made with additive manufacturing
What is Additive Manufacturing?
Additive manufacturing, also called 3D printing, refers to the process of manufacturing a part via the addition of material. This contrasts with most traditional methods that involve cutting away (subtracting) portions from a larger piece of raw material. In most additive processes, this is achieved by adding either plastic or metal in a layer-by-layer fashion until the part is complete. Additive technology has matured over the past decade to the point where these machines can be considered for use in actual production and not just for the manufacture of prototypes.
Additive Manufacturing Technologies
When it comes to additive vs subtractive manufacturing technologies, most additive ones are relatively new, and unique additive methods are constantly being developed. A wide range of different additive techniques is currently available. In general, these can be categorized by the type of material they print.
1. Plastic Additive Manufacturing
Plastic additive manufacturing can produce plastic parts using a wide range of different technologies from laser-bonded powder systems like selective laser sintering (SLS) to advanced photopolymerization techniques like stereolithography (SLA) or carbon digital light synthesis (DLS). Parts can be printed in hard thermoplastics or soft thermosetting polymers. In the contest between plastic additive vs. subtractive manufacturing, additive technologies offer more overall versatility in terms of materials and the ability to manufacture complex multi-material parts.
2. Metal Additive Manufacturing
Metal additive manufacturing has come a long way and is now considered a mature technology. There are many different styles but they can be broken down into two subcategories. Powder-based systems use lasers or electron beams to metal powder into a solid part. Fused deposition modeling (FDM) technologies, on the other hand, print the part with metal powder encased in a polymer binder. After the print, the part is fired in a furnace to evaporate the binders and sinter the metal particles together.
Advantages of Additive Manufacturing
When comparing additive vs subtractive manufacturing, additive manufacturing has many unique advantages such as those below.\
1. Easy Setup: Additive manufacturing is quite simple to set up. In most cases, the part can be designed in CAD, digitally sliced (turned into g-code), and printed immediately with a limited setup.
2. Complex Parts: Additive manufacturing can produce parts that are simply impossible on subtractive machines. Hollow or complex internal cavities are easy to make with additive machines but often cannot be achieved with other manufacturing techniques.
3. Rapid Manufacturing: Additive manufacturing can be used to quickly create a one-off part and rapidly iterate through design variations. This is due to the easy setup and the fact that raw material doesn’t need special preparations beforehand.
When to use Additive vs. Subtractive Manufacturing
Deciding between additive vs. subtractive manufacturing depends on many different factors. Metal additive manufacturing is currently more expensive per part than metal subtractive manufacturing. It is, however, cheaper to 3D print a plastic part than to machine it. When relatively short production runs of complex parts are needed, additive manufacturing is often the best option but subtractive wins out in low-complexity, high-volume situations. Contact a Xometry expert to learn which technology is best suited to your application. Alternatively, use the Xometry quoting tool to get an idea of the cost differences between subtractive vs. additive manufacturing.
Ready to Get Your Parts Started?
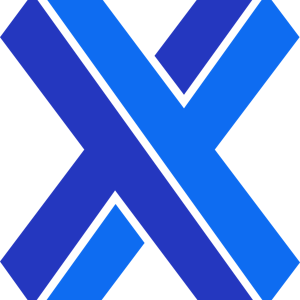