The debate between dry etching vs wet etching is one of the first things microelectronic manufacturers have to settle at the start of their project. Many considerations have to be taken into account to decide which type of etchants should be used on a wafer to create an electronic chip, be it liquid (wet etching) or gaseous (dry etching).
This article will go into depth on what the dry and wet etching processes are, their applications, and the various methods involved in those processes. We will also clarify what the differences between the two are and what factors to consider when considering which one to use. If you'd like to learn more about other types of part markings, you can also visit our guide on direct part marking.
Etching Definition
Etching is a manufacturing technique used to remove layers or slices of a material or part, including semiconductors, dielectrics, polymers, and metals. It can employ chemical corrosion, electrochemical electrolysis, or even mechanical polishing arts.
As such, different types of etching processes can be used, depending on the desired manufacturing outcome. The procedure for different applications can vary greatly in terms of etching chemicals, the temperature used in the process, and exposure time.
There is also the matter of safety, as condensation of the wet etching chemicals can become a serious issue if not adequately addressed. It’s also important for the manufacturer to take proper care around the cleaning solvents used after liquid immersion or vapor.
Etching Considerations and Performance Parameters
Subjecting a material or part to a liquid or vapor etchant causes complex interactions on a molecular level that have a significant impact on the surface of said part. Regardless of the type of etching we are talking about, an etching treatment can cause one of three outcomes:
- Isotropic etching: The material is removed uniformly in all directions, creating a semi-circular shape cut out of the material. Since it’s a less accurate form of etching, isotropic processes are usually used for cleaning wafers or substrates of chips.
- Completely anisotropic etching: The material is removed only vertically, creating a rectangle when viewed from the side.
- Anisotropic etching: The created shape has a form between the two mentioned above. Anisotropic etching is commonly used to create circuit patterns.
Manufacturers make use of the following performance parameters when determining the best way to etch a part, whether they're using wet or dry etching techniques:
- Etching rate – the speed at which etching occurs, or the thickness being etched per unit of time. It is usually measured in μm/min or nm/min (micrometers per minute or nanometers per minute).
- Selectivity – the ratio of two etches rates noted as R1/R2. This is a useful parameter when comparing the etch rate of the etchant and the material. It is vital when defining or choosing the mask for a specific process.
- Etch uniformity – the etch rate variation throughout one part, multiple parts, or multiple batches of parts. It is defined as the subtraction of the maximum etch rate and the minimum etch rate, over the addition of the two.
- Anisotropy – defined as the etching directionality, meaning that when A=0, the etching is considered isotropic, and when A=1, the process is completely anisotropic.
The Wet Etching Process
Wet etching is a technique that uses a liquid solution (usually called an etchant in the liquid phase) to remove layers or portions of a material or part such as a silicon wafer. This process is widely used in semiconductor fabrication in the manufacturing and treatment of wafers. The main advantage of using it is the ability to conduct surface removal on a part-wide scale. Etching intrinsic impurities in the materials (or surface) is especially sought-after and can be provided by etchants in the liquid phase.
Applying these etchants causes corrosion in the material, and this corrosion is controlled via masks. Masks are hardened materials that can resist the etching processes, making them perfect for adjusting the angles and shapes of the channels.
However, the depth of the etch is controlled by the etch duration and rate while the width of the channel can be reasonably estimated by the mask opening plus twice the channel depth. Some mask materials include gold, titanium, chromium, oxides, and nitrides, depending on which material is subjected to etching (for example, metal or silicon as the etching piece).
Generally speaking, in wet etching, engineers use substances such as hydrofluoric acid, nitric acids, phosphoric acids, and hydrochloric acids. The advantages of using these etchants are related to their corrosive properties.
Types of Wet Etching
There are two distinct techniques for wet etching:
- The dip method refers to when the part is laid into a tank full of chemical solutions of the type mentioned above. This is considered the ‘classic’ wet etching method - the one that involves a chemical bath.
- The spin/spray method relies on the etchant being sprayed on the material that’s being processed. At the same time, the part is rotated while being connected to an absorption mechanism. The rotating part of this system is optional, as the erosion of the material is heavily dependent on the crystal planes of the atoms that make up the part subjected to treatment.
The second method is more widely used since the dipping technique requires more acidic substances that are toxic to the human body. Silicon wet etching, typically used in semiconductor fabrication, is usually executed using the second method. Correcting another common misconception that may circulate around this process: a wet etching process does not necessarily rely solely on a chemical bath.
The Dry Etching Process
The dry etching process is sometimes referred to as plasma dry etching, although there are certain particularities to consider. Dry etching uses high kinetic energy beams to etch off regions of a material or part. Those beams contain high-energy particles (in the form of ionized gases in the plasma phase) that knock off atoms from the substrate surface, resulting in the evaporation of that specific region. The etched area is then controlled via masked patterns. The process allows for high aspect ratio geometry creation.
This technique is also heavily used in semiconductor fabrication. The dry etching process is a flexible process preferred due to its smaller undercut capability and the tendency toward anisotropism. Etching uniformity depends on the gases used and the distance to the substrate. Etching shape can be heavily influenced, depending on the technique used.
Typical gases used in this process include oxygen, fluorocarbons, chlorines and bromine species (in the plasma phase). Hydrogen plasma etching has also been investigated in the last few years, due to the highly reactive properties of the gas. Oxygen plasma can be used in etching activities of non-metals (such as glass and plastics), but it may be used in metals if combined with other reactive species (argon for example).
Types of Dry Etching
Depending on the equipment and plasma manipulation techniques, there are several types of dry etching:
- Ion beam etching (IBE): the most straightforward of the dry etching processes. This involves argon ions that are radiated onto the surface of the part in the form of an ion beam at energies of 1-3 keV (kilo electronvolts). These energies are enough to strike out material from the surface, hence the need for gases in the plasma phase.
- Reactive ion etching (RIE): a type of dry etching that makes use of chemically reactive species (reactive ions) that are accelerated toward a substrate (in most cases a silicon wafer). Inside the etching chamber, the part is placed on an HF electrode used to influence the ions that form inside the chamber and thus control directionality. This allows highly anisotropic channels to form. By increasing pressure in the etching chamber, the mean free path of particles can be reduced, which translates into a less directional etching resulting in a more isotropic channel.
- ICP-RIE etching (or simply ICP etching): makes use of an inductively coupled plasma source. The plasma in this case is generated with the help of an RF-powered magnetic field. This source is added on top of the existing etching system necessary to conduct normal RIE operations, allowing for more control over the properties of the dry etching process.
- Plasma etching: a subclass of the dry etching process, capable of creating isotropic etch profiles. The plasma etching process is used to remove whole film layers (especially relevant to silicon substrate manipulation). The accelerated plasma is held off at extraction grating, meaning that only neutral atoms pass into the etching chamber. Those then hit the part surface, causing chemical abrasion. Since all dry etching processes are variations of plasma etching, those two terms may erroneously be used interchangeably.
Considering the techniques described above, dry etching methods can be further categorized as follows:
- Chemical reaction processes – those that use plasma or reactive gases (plasma etching).
- Physical removal processes – that make use of momentum transfer to knock off material (IBE).
- A combination of the two above (RIE and ICP etching).
In terms of hazard management, reactive gases are of particular concern. However, since the equipment used in dry etching processes encompasses different types of chambers (including a vacuum chamber), the safety risks are considered rather low. While not the most straightforward approach in industrial manufacturing, dry etching can use chemicals to accomplish things like modifying wafer properties with high accuracy, depending on the specific process).
Dry Etching vs Wet Etching
Generally speaking, wet etching uses simpler equipment, is less complex, and has a high etch rate. It's also more highly selective. However, wet etching also requires large amounts of chemicals, is less safe, and offers less control over the etch. Dry etching, on the other hand, offers strong isotropic control, more precision, and is generally safer. Dry etching can also, depending on the process, offer a high etch rate, and it uses less chemicals. However, it is a more complex process, involving more complex equipment, and it doesn't feature as much selectivity.
Both techniques are used heavily in activities/industries such as:
- Semiconductor fabrication
- PCB etching
- Metal etching
- Transistor gate manufacturing
Both techniques also require etchants in either the gas phase or liquid phase to remove material from part surfaces. Silicon processing is the most common use case. With anisotropy being a quality of particular interest in microelectronic systems (i.e. printed circuit boards), dry etching offers many advantages over wet etching, even though the latter is the simpler process.
Etching with Xometry
Dry and wet etching are essential processes in the manufacturing of electronics and each can be used in different situations, depending on the project requirements. While the main difference between them is the main etching agent used and how it is manipulated, both entail the removal of some layers or material from a part.
Interested in how Xometry can help with your manufacturing needs? We offer a wide array of manufacturing services that can suit any requirement through our partner network. Set up volume orders ranging from prototypes to industrial-scale quantities with us by getting an instant quote today.
Disclaimer
The content appearing on this webpage is for informational purposes only. Xometry makes no representation or warranty of any kind, be it expressed or implied, as to the accuracy, completeness, or validity of the information. Any performance parameters, geometric tolerances, specific design features, quality and types of materials, or processes should not be inferred to represent what will be delivered by third-party suppliers or manufacturers through Xometry’s network. Buyers seeking quotes for parts are responsible for defining the specific requirements for those parts. Please refer to our terms and conditions for more information.
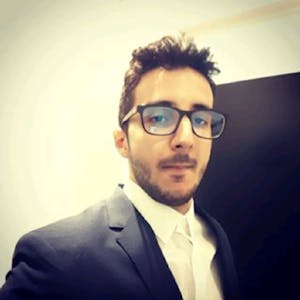