Mass production is the manufacturing of a large number of similar products using an efficient means. It often incorporates the use of automated processes and machinery and is highly repetitive. This article explores the definition and history of mass production, the five phases of production, and its advantages and disadvantages.
Defining Mass Production
Mass production uses specialized division of labor and automated processes to achieve high-volume manufacturing at a low cost. This highly efficient process is meant to drive down costs.
However, these principles are only effective when manufacturing standardized parts. Any custom parts will deduct from the efficiencies gained by automated machinery and a specialized workforce.
Mass production may also be called flow production, repetitive flow production, series production, and serial production.
The History of Mass Production
The use of specialized labor can be traced all the way back to ancient Greece. However, the most obvious examples of special manufacturing processes for mass production were first seen in the textile industry in 18th-century England whereby increasing the width of weaving textiles resulted in a higher rate of production.
One key development that led to the use of mass production was the use of James Watt’s improved steam engine which replaced humans and animals as an energy source. This allowed for the use of heavy machinery in production on a mass scale.
In more recent history, Henry Ford is recognized as the first person to use a moving assembly line for mass production. The use of a moving assembly line meant that workers had specialized jobs. This reduces the time taken for workers to move from one task to another; instead, they repeat one job continuously. This style of production allowed Ford to keep up with customer demands while keeping costs low. As a result, the Ford Model T is one of the best-selling cars of all time, with 16.5 million sales.
The Process of Mass Producing a Product
The steps taken to produce on a mass scale are different from creating small production batches. That is because large-scale production methods, such as injection molding, require processes that produce consistent-quality parts for many batches. Consideration also needs to be given to the efficiency of the design when produced on such a scale, i.e., how to reduce waste and post-processing time.
The five steps for mass production are listed below:
Concepting
The concept of a product forms the foundation for all the other production steps. If the concept is flawed, it will be hard to resolve in the latter stages. Creating a concept may be simple if the manufacturer has received a customer design specification. More commonly with mass-production parts, companies must carry out due diligence to understand the market, costs, risks, and rewards of the project before going ahead. To complete this stage, input from all departments may be necessary including engineering, sales, marketing, and senior management.
Turning a Concept Into a 3D CAD Model
Once a concept is established, a 3D CAD model can be created. There are many different examples of CAD software available, and the one used will depend on the project requirements. The use of 3D modeling software has improved all production processes due to its ability to assess a design before it is made. 3D models can be tested using finite element analysis (FEA) and computational fluid dynamics (CFD) which can predict mechanical and fluid properties respectively, as well as other properties including weight and strength. Specialized tooling designed for the manufacturing process can also be designed in CAD for use in mass production.
Prototyping
Now the product has been modeled, it is time to build a prototype. Creating a prototype is still necessary even with computer modeling software as computer models don’t always agree with real-world applications. There are many variables in the manufacturing process that can produce results that are different from those predicted by a computer model. Currently, 3D printing is being used in many prototyping scenarios as it can produce a cheap one-off part for testing before investing in tooling for mass production. Other processes that can be used to produce prototypes include CNC machining, injection molding, and casting.
Test Your Product on the Market
Testing your product is crucial before committing to mass production. Creating a limited run will give you a population sample from which you can identify the quality and performance of the product against the design criteria. The testing from this stage will provide feedback on the product which usually leads to an adjustment at the conceptual, 3D modeling, or prototyping stages of the project.
Mass Production
After completing the last four stages, the product is ready to be mass produced. Now, all of the tooling and materials need to be procured. With production on a mass scale, this is usually a major initial investment as large quantities of materials are required and high-performance machinery and tooling are needed that will last a large number of cycles with minimal failures. During mass production, the manufacturer must implement a quality management system to ensure quality does not degrade over time.
Check out our High Volume Production Manufacturing service to get started.
Advantages of Mass Production
- Low Cost Per Part: This is due to the cost of overheads and expenses being spread over many parts. In addition, labor costs are minimized with the use of automated processes.
- Consistent Quality: Mass-production parts are consistent in quality due to the repetitive nature of the production process. Mass-production parts are also of high quality, but usually, bespoke parts can offer a better quality, that is if cost isn’t a limiting factor.
- Fast Production: While it does take a long time to start a mass-production product and production line, the result is a high volume at a fast pace.
- Scalable Production: Not only is the production rate in mass production fast but it can also be scaled up easily to increase the production capacity.
- Increased Productivity: Due to the repetitive nature of the tasks in mass production, the process can be iteratively improved to increase productivity to a maximum.
Disadvantages of Mass Production
- High Initial Investment: Mass production requires a large layout to buy all of the tooling and materials ready to start the production process.
- Expensive Machine Downtime: In mass production, machines often work continuously to produce parts. If any point in the system fails, the product grinds to a halt and potential earnings are lost.
- Altering the Design or Process Can Take Time and Money: Once set up to make a specific part, any deviation from the original design may require changes to all of the equipment, machines, and processes already set up.
- Repetitive Work Can Disenfranchise Employees: Often staff will quickly become bored of carrying out repetitive tasks. This can lead to high staff turnover which can result in downtime and recruitment costs.
- Risk of Product Recalls: Any quality issues will likely be replicated in each product. The product may be sold many thousands of times before the realization that the product is faulty, resulting in large product recalls.
How Xometry Can Help
If you are getting ready for mass production, Xometry can help. Contact a Xometry representative to learn more.
Xometry provides a wide range of manufacturing capabilities and other value-added services for all of your prototyping and production needs. Visit our website to learn more or to request a free, no-obligation quote.
Disclaimer
The content appearing on this webpage is for informational purposes only. Xometry makes no representation or warranty of any kind, be it expressed or implied, as to the accuracy, completeness, or validity of the information. Any performance parameters, geometric tolerances, specific design features, quality and types of materials, or processes should not be inferred to represent what will be delivered by third-party suppliers or manufacturers through Xometry’s network. Buyers seeking quotes for parts are responsible for defining the specific requirements for those parts. Please refer to our terms and conditions for more information.
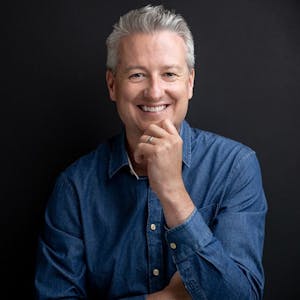