[Webinar Recording] Serial Production with Xometry
In this exclusive webinar, we dive into Xometry’s Serial Production and Program Management offerings. Learn about consignment and safety stock, protecting against supply shock, kanban management, and more.
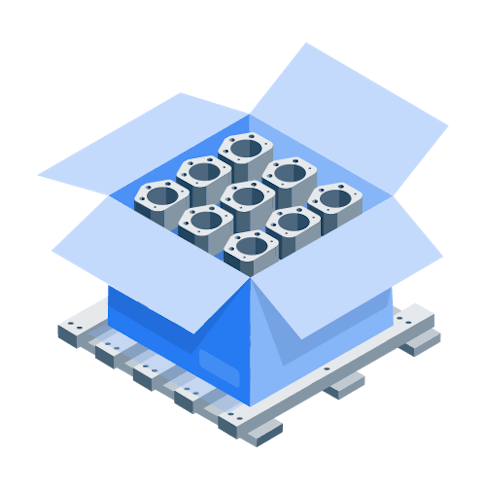
Serial Production with Xometry
Summary
In this webinar hosted by Xometry’s Rusty Haake, Principal Solutions Engineer, and Josh Blancet, Senior Account Executive, do a deep dive into Xometry’s Serial Production and Program Management offerings.
This webinar will provide a walkthrough of how Xometry manages your production needs with topics including:
✔ First articles, tooling, DFM, and on-ramp
✔ Multi-year program support
✔ Real-time WIP updates
✔ Protection against supply shock and contingency planning
✔ Consignment stock, safety stock, and kanban management
✔ Inspection and compliance: gauging, fitment, CMM, FAI, PPAP, AP/QP, traceability, etc.
You will also see real-world examples of Xometry's serial production capabilities in use with several case study highlights!
Questions and Answers from the Webinar
How do you ensure IP protection when multi-sources while promoting project transparency for quick sourcing transfers?
All of our partners enter mutual NDAs with us before we get started, similar to the ones we establish with our customers, forming a closed-loop system internally. We also redact sensitive information and specifications. Our ERP also allows us to identify trusted manufacturers who have worked on previous projects for you so we can offer bespoke manufacturing solutions.
How do you manage tooling between multiple suppliers?
"Tooling" is defined differently for different processes. For CNC projects, tooling often refers to specific tools like cutters, endmills, etc., which are procured as needed. Tools for these types of projects are expected investments and are often trivial in terms of overall cost.
For processes like injection molding or casting, tooling (e.g., molds) is a large part of the project, and there is no way around producing multiple tools if production needs to occur simultaneously at different locations. If a customer prefers to have two locations ready to do the work, but only one location has the tool and the other is intended as a backup, such as for geopolitical derisk reasons, then an NRE is associated with the backup location so they fully understand the project, are prepared and are ready to take over if needed.
How do you manage contract amendments between suppliers and product owners?
We try to manage as much as possible on the supplier side via dedicated production managers who are intended to be the primary point of contact. Minor ambiguities can usually be addressed this way. However, in some instances, a three-way conversation between supplier, customer, and Xometry is the most effective approach. We are happy to facilitate these discussions to ensure a rapid resolution for any amendments or concerns.
On the rare occasion a non-conformance is discovered, how is that handled?
As a company that has helped manufacture millions of parts, the occasional issue is bound to arise, and we have the personal experience to handle virtually any problem that crops up. Our QMS (quality management system) dictates specific processes and procedures to be followed to handle non-conformances. This includes investigating the issue, understanding how it happened through root-cause analysis, understanding who the responsible party was, etc. Once we fully understand why an NCR occurred, we can properly address it in an appropriate manner and offer remediation.
For production, will the same supplier always be used for manufacturing the part?
In most cases, we aim to have the same supplier complete repeat work or production orders, presuming there were no issues with previous orders. However, there are instances where resourcing may be necessary, such as if the production quantity is beyond the capacity of the original supplier.
Can you share some challenges or insights regarding providing production assistance to your customers?
Challenges vary; for example, a large enterprise will have different experiences and challenges than a fresh startup will. A common pain point is time, whether it's waiting for additional data or drawings to move forward or trying to align and synchronize everyone's timelines. We try to mitigate that as much as possible through our engineering resources and project managers.
How do you control special processes such as painting or anodizing with vendors, especially when there are strict requirements?
Xometry is familiar with applying dozens of finishes to various standards (e.g., MIL-Specs); however, there are cases where uncommon requirements arise. This is where we apply our dedicated finishing network, which is made up of suppliers who only specialize in finishing and are experts at what they do. We have established strong connections with various different types of finishing suppliers, allowing us to catch potential callout mistakes early on, hit unique specifications, and offer special testing to meet your quality control requirements. If you have a list of approved finishers, we are happy to work within that list as well.
How do you hold and maintain your supplier's capabilities and their inventories?
At Xometry, a large part of our work is data-driven engineering. We've built a robust ERP and database that tracks each supplier's exact capabilities and even which machinery they have available. This allows us to rapidly sort and assign the right suppliers to the required work. We maintain active relationships with our suppliers as well to foster a collaborative environment. With inventory management, Xometry is able to coordinate and assist with managing safety stocks in our facilities and is able to work with our suppliers to regulate production volume to match your current demand.
If our quality process requires us to perform inspections at the production facility, Xometry can accommodate that?
Yes, Xometry does this routinely, especially when it comes to production orders. We can facilitate on-site tours to meet your quality system requirements and offer advanced inspection options, such as source inspections.
For the semiconductor industry, we need a "copy exact" where all the production builds are with the same suppliers; how can you make this happen?
We utilize a PPAP (Production Part Approval Process) and accompanying documentation to achieve manufacturing consistency between suppliers and ensure the same group of suppliers is utilized for a given project.
Full Transcript
Greg Paulsen:
Hey, everybody. I see folks streaming in, but we're going to get going. We got some awesome things to cover today in today's webinar on serial production. We're excited to bring in some of our solutions experts today, and I'm really excited to have Josh and Rusty here. They're going to be discussing serial production, so what happens when you're doing a sustained production part and how can we be a solution for you?
So we'll go over our production experience and some case examples showing how Xometry could truly be an end-to-end supply chain partner. But before I hand this off to Josh and Rusty, I just want to emphasize that you, the audience, also have the opportunity to submit questions at any time using the Q&A tab on the Zoom platform. We'll try to get as many as possible on the tail end of this hour.
We'll also work to follow up on any outstanding questions. So ask away. This webinar will be recorded and we will send email with a recording for you to re-watch or share with your colleagues. And with that, I'm going to hand the reins over. So Josh and Rusty, you guys can take it from here.
Josh Blancet:
Thanks, Greg. Welcome, everybody. Just want to start off by saying thanks for all of you who have joined. We're excited to showcase Xometry's production capabilities and how we're executing on production programs across different industries. And we understand that production can mean different things across different companies and the requirements may differ.
So with that said, if you have a question, like Greg said, please put it into the Q&A chat so we can address those at the end. So my name is Josh Blancet. I'm a senior account executive here at Xometry. I've been with Xometry for five years working within the aerospace and energy segments tailoring, sourcing strategies, providing regional cost comparisons, inventory management, and overall support. And I'll let Rusty introduce himself.
Rusty Haake:
Yeah, hi, principal solutions engineer at Xometry. And as my bio there says, I've spent my career manufacturing a bizarre assortment of materials products. I've been up and down the product development roadmap. And for most of my career as what I colloquially call a real engineer, a service like Xometry would've been an enormous benefit to me. So I saw the light, I jumped ship, and now I hope to convince the remainder of the audience of the correctness of those previous statements. Looking forward to talking about this.
Josh Blancet:
Awesome. So before we jump in, I want to show our capabilities list to really set the stage, starting with nine different types of additive manufacturing and really moving those plastic parts into production with injection molding, urethane casting, plastic extrusion, et cetera. And then on the metal side with sheet metal, laser waterjet cutting, tube bending, tube cutting, CNC milling, turning, wire, sinker EDM, and then moving those to production with die casting, stamping, metal injection molding and extrusion as well.
So what we're going to cover today, Greg touched on this, we'll start with a brief overview of Xometry. We'll touch on our quoting methods and how production programs are quoted. We'll look at our production capabilities and how production works at Xometry. And then we'll dive into real life programs we have worked or are currently working on that will showcase different things from prototype to production, near-shoring, full bill of materials, flight components, and dual sourcing.
And then we'll close it out with some resources and then a Q&A as well. So for those who may not know, Xometry was founded in 2013 and we're headquartered in Maryland. We went public in 2021, which is also when we acquired Thomasnet. And real quick about Thomas, Thomas has been crucial in our path to becoming a production supplier.
Because whether it's a process we do not offer or a supplier base that's needed to perform certain programs or requirements, Thomas gives us access to over half a million suppliers so that we can add those new processes and vet and onboard new suppliers if and when needed. So that's been really instrumental in our growth. And since then, we've grown to almost 50,000 active buyers and our supplier network has grown to over 10,000 vetted suppliers worldwide.
And with this access to our supplier network, we offer over 20 different manufacturing processes, as you just saw, but that really allows us to offer a fully managed manufacturing service to you. So most people when they think about Xometry, they think of us as a prototype or a quick turn manufacturer, which when we started was not an incorrect statement. But we did start as an additive company back in 2013.
However, as our customers have grown, we have had to grow to meet their needs. So we still do a lot of prototype work, but we have grown to provide full life cycle production management. So what does this look like? Early on, like I said, we really stayed in the R&D and NPI space, but our customers began asking us if we could help move the work that we have done for them to launch a pilot run or assist in their validation process.
So we had to adapt to deliver there, whether that was higher quantity runs or increase quality requirements. And once that pilot run or validation was complete, we had already gone through the growing pains of revision after revision on a new part. And as you know, when manufacturing apart for the first time, there's a lot of learning there as well. And so it just made sense for them to have us take what we had learned through the development process and become a full scale production manufacturer.
So again, we have grown to provide solutions from anything from R&D to full scale production. And leaning on our growth, we now have three different ways to quote, and each method really corresponds with different times in a parts cycle. So the first is the instant quoting tool. This is the most common. And I'm not going to spend too much time here because I'm assuming most of you all are probably familiar with our quoting tool.
But essentially, you drag and drop your CAD models into our instant quoting engine, you configure your manufacturing inputs, and you're provided with instant price and lead time. And like I said, this generally correlates with the R&D and NPI phases. But the second way to quote is what we call manual quoting. This is typically for more complex parts, tighter tolerances, custom finishes, materials, et cetera.
So when you upload your parts, you'll sometimes see that it cannot provide instant pricing and lead times and a request a manual quote button pops up. If you click that, it goes directly to our team of engineers who have over 120 years of manufacturing experience to review your models, your drawings, and provide a quote back to you within 48 hours. But the third option is what we call partner engaged quoting, and this is how Xometry has moved from just a quick turn supplier into a full scale production supplier.
And what this looks like is we are going to work with you to get CAD models, drawings, bill of materials, quality and inspection requirements all up front, and we're going to discuss first articles, PPAPs, ramp periods, delivery schedules, et cetera. And then we're going to write up an SOW. Once that SOW is approved by you, we're going to work to find a few suppliers on our side that are capable of handling the program and ask them to quote it based on the requirements that you provided.
We then typically get a couple quotes back and we're going to work with you to select which one works best for the project, depending on, of course, the requirements, whether that's cost, lead time, et cetera. Obviously this was super high level. Rusty will dive into a more detailed workflow here in a few minutes. But depending on your program's requirements, Xometry leverages our global manufacturing network.
And we have headquarters in every major manufacturing region, North America, Europe, Asia, and India so that we can provide solutions for your production needs. And with boots on the ground in each of these regions, Xometry will manage these relationships for you. All right, let's shift gears into the execution of production programs. So whether that's a million units a year for some companies or it's a couple hundred units per year, most of the time this is where strict quality control is put into place.
So whether that is first articles, PPAPs, sampling plans, CMM inspections, et cetera, we're able to deliver across the board for your quality needs. And what I really mean by we is Xometry has a production management team that is solely responsible for managing long-term programs, which Rusty will touch on the next slide as well. But they're going to be involved on the project requirement side, like I mentioned, with that partner-engaged quoting. They're going to set up the program.
They're going to handle the PPAPs, the first articles, and they're going to manage ramp rates and also provide updates in real time on work in progress to you. So they're also going to set up delivery schedules to help mitigate supply shock. And in some cases, it may even make sense to set up safety stock that we can pull from in case demand upticks quicker than expected.
But really where Xometry's value add comes into play on the production side is reducing the risk of single source production. So we can establish dual or multi-sourcing with geographically diverse suppliers. A big example of this was COVID. People were struggling to get their operations up and running and it halted production. We can have multiple vetted suppliers ready to go at any time.
So if one shop has to shut down for COVID or for a hurricane or a wildfire, we can pick up production without losing any time at all. Or like I said, if demand increases, which is a great problem to have, we can run production in multiple locations to keep up with demand and we're going to manage everything for you. Our production capabilities are robust. This list does not showcase all of our production offerings.
However, it is the most common needs from our customers that we deliver. So if there's anything that you require that's not on this list, please throw it in the Q&A tab that Greg mentioned and we can address it at the end. Rusty, I'll hand it to you.
Rusty Haake:
Right on. Thanks, Josh. Going forward, let's talk about what production actually means. One of the most critical elements of running a production program through Xometry is the team of experts that supports it. This team is drawn from a matrix structure, which is to say we have a bunch of program managers, a bunch of quality engineers, a bunch of project engineers, who will be pulled for project by project support cases depending on individual strengths and backgrounds.
Because Xometry's customer base is so diverse, our production team backgrounds are also quite diverse. This ultimately is in the best interest of the customer because you're able to pull in aerospace experts, automotive experts, oil and gas experts, medical experts, and the expertises mingle and contribute meaningfully to each other. It provides a more robust problem solving environment.
So when you enter into a Xometry production arrangement, you'll have a diverse, qualified, dedicated team supporting all of your activities. Let's go to the next slide. Product lifecycle. This is us trying to say we understand what you're going through. This is our visibility into the wide and interesting world of product development. And in keeping with something Josh mentioned earlier, production means different things to different people.
But if you're on this webinar and you're looking at this slide and seeing things that feel familiar to you, you're probably interested in production services. From our perspective, if you feel like more than 60% of these stage gates or terms or methodologies are applicable to you, then we definitely want to be talking to you about production as opposed to individual spot buys and the other useful services that Xometry can provide. Next slide.
So what does it actually mean? We want to capture the user experience and simultaneously share what's actually happening within Xometry as a preview to what a new customer experience might look like. And for those of you who are on the call who are current customers, first, thanks for the business, and second, this should feel awfully familiar to you.
Our engagements would begin with you telling us what it is that you're working on, CAD RFQ, project description. We would call this initial discovery. And particularly with novel or Rev-A type activity, we're going to find ambiguities. We're going to find technical issues. We're going to find gaps. We call this program phase digestion and subsequently illumination.
And while we are doing this, we're already crunching on which would be the most appropriate manufacturing partners to support this activity based on the data you've provided. Sorry. We'll respond quickly with, we think it'll take us this long to provide you data. Because when you're in a production environment, data is king. You need something to go off of. So we'll tell you how long that'll take. Next slide.
So after initial digestion and illumination, we're going to tell you, we can provide this, we can do this, or we can do this and there's some fuzzies that we need to address, or this project's out of scope for us, which is rare. And things that are out of scope for us typically have a time boundary associated with them, which is to say they're out of scope for us now, but we'd like to come back to it later.
Meanwhile, while we're doing this, we're formulating a quote strategy. For us, that's all in the name of requirements digestion. It's a truism in the manufacturing world that manufacturers make good parts. Sometimes they're not told correctly what to do. Most problems in manufacturing space actually occur on the front end, but they're not manifested until the back end.
So this is where we're trying to do everything in our power to really understand what's going on with your project. We're converging on DFM. We're converging on baseline inspection. We're trying to figure out into which standard processes and procedures such as PPAP that we can do. And we're trying to figure out how we can get a mutually agreed upon statement of work, a document that just clearly indicates this is what's in scope, this is what's not.
This is the schedule as best we know it now. Let's go ahead and spend more effort on this. We'll then do a partner RFQ, which is to say we believe we know enough about your project to know which of our partners want to talk about it. And we'll get started with that. And functionally then we start down-selecting. The down-select isn't a all-at-once guillotining race to the bottom for the best price. In a production activity, there's a lot of conversation back and forth data and refinement.
Because if there's one thing that's universally true about production, it's never as simple as it seems. Next slide. We're going to provide you a preliminary estimate. In most production sequences, the first time we tell you, "Hey, this is what we think it's going to cost, hey, this is what we think it's going to take in terms of time," we know that conversation's not finished yet because production is complicated.
And the key messaging we're trying to get across here is that we understand that, appreciate it and want to be involved in as many refinement processes as possible so that we get our proposal to you exactly correct. And under the hood, we have dozens of engineers churning on every single one of these production activities, including extensive partner conversations.
And before anything gets to you, it's gone through several levels of approval, which include people with decades of experience in the field. Next slide. Project launch. This is an exciting time. Contract review is incredibly important to us and we'll make sure that the appropriate level of legal and engineering eyeballs are on all of the documentation that goes back and forth.
The work in process updates from a program manager provide you visibility at whatever interval is appropriate for your project into tooling development, NRE expenditure, what is actually happening on the ground, and this includes physically being on the ground. That is valid for any of our international locations, as well as domestic US locations. So under the hood, for every interaction you see, we have 10.
We are in routine high-velocity conversations back and forth with all of our production partners. It's about the furthest thing from a set it and forget it activity, particularly at the launch phase. An important deliverable is, of course, the PPAP documentation set. What you need to know about that is your involvement into PPAP investigation approval, et cetera, is whatever you need that involvement to be.
Our baseline is that we will ensure that every single T is crossed and I is dotted on all PPAP documentation before you see it. Which is to say, by the time it's gotten to you, it's gone through us and this should fundamentally save your QEs quite a bit of work in error-proofing and absorbing this product development documentation. Next slide. Yeah, execution.
Now we're running. The QC documentation flows seamlessly from our manufacturing partners through our quality group through to you. Shipping trackers are available in real time at all times. This is of particular importance on Kanban style projects, which we have several on work. Schedule adaptation is a valid consideration. We do this routinely. And I want to add that long-term agreements often involve making provision for these kinds of mid-flight changes, so to speak.
So all you're seeing is quality documentation, parts shipping in brown boxes with blue tape, if they're appropriately sized, otherwise, they're probably going in pallets, shipment, and you know who to go to for any mid-flight changes. Under the hood, we are doing everything that is necessary to ensure that your experience is as smooth as possible. So we're managing hiccups.
We're solving problems on the floor. We're dealing with contract and PO things that come up. Assuming this webinar audience is all people deeply experienced in production, you know stuff happens and we manage as much of that as is possible, convenient, and helpful to you for you. Next slide. Let's talk about what we've done. This is all just a PowerPoint until we talk about shipping product.
So we're going to go through some examples. These examples are intended to illustrate the diversity of services that we're able to provide and intended to keep our customers anonymous. All of our customers are NDA protected. We have a couple of case studies on the website with customers who've explicitly given us permission to share data. So other than that, we're not going to.
But there's an electric vehicle OEM with whom we're particularly close. We have been compelled to work at a breakneck speed with them. The EV market follows different rules, different patterns, different processes than the traditional hydrocarbon-based automobile world, which is to say it all basically started from zero 20 years ago and has been in hyperbolic technology growth since.
So with this customer, we saw a lot of instances of things that were intended to be prototype tools, particularly regarding the injection molding world. Prototype tools that ended up being refurbished, modified, altered, updated. Can we actually PPAP that prototype tool and get another 5,000 shots out of it?
These kinds of conversations sound trivial to maybe the uninitiated, but this is the very real world illustration of the prototype to production world that requires a steady hand at the wheel, creative solutions and a diverse array of partners to be able to do all of these things simultaneously. So at one point, we were fielding 32 simultaneous production RFQs.
And again, to the uninitiated, that's a lot. That is a lot of production content to be considering across multiple disciplines, which included multiple regions, all with the very stringent IATF 16949 partner group, the vast majority of which ended up with PPAP compliance if they didn't start with it. And we ended up with multidiscipline projects, stamping, molding, assembly.
We ended up with commercially sold goods, which in the automotive world is not a trivial statement, as well as on-vehicle production, which is the least trivial statement of it all. We're very proud of this relationship. We're particularly proud of the let's call it engineering agility that it involved and demonstrated, and we're eager to replicate it. Next slide. This is a completely different project.
And I'm probably going to say that at every slide because I chuckle when I point it out. Xometry's customers are extremely diverse. This is a downhole oil and gas valve, 15,000 PSI, Inconel construction, multiple single-digit micron tolerances, which in the CNC world is the cat's meow. These are difficult parts. We were approached for this for geographic diversity.
This was a multiple location simultaneous dual source to produce validation parts. The validation parts became stocked production-sellable parts, which permitted the customer to make a financially-based downselect. They now manufacture these parts in China. We have various 9102 controls. We have a production inspection methodology that is customer-specific with regard to keys and crits.
They didn't have to change their POC to go from, hey, we're talking about validation, a couple off parts to prove that we can do this, all the way through to, okay, let's have a couple $100,000 worth of product that ships a couple times a year from China to fulfill these needs. Single point of contact for the entire activity. We are now doing a similar procedure across multiple related product categories.
And it bears repeating that these are components of consequence. These are components which if they fail, Michael Moore makes a documentary about it. We're not making desk ornaments. These are the legitimate produced and sold products of our most consequential customers. Next slide. We do a lot of diverse things. I think I said I'll say that on every slide.
This is a completely different problem statement and one that perhaps you might find commonality with. This is a real estate lockbox. If you've ever bought or sold a home, you're familiar with this or very similar products. When you look at this product, you might have previously thought about it, but it's a complicated electromechanical device featuring multiple different methods of manufacture, all of which must be coordinated, controlled, and finally assembled.
So such a simple thing as a lockbox is not in fact a simple thing. So there was a redesign effort on this product simultaneous to a desire to reshore it. It was formally made in Asia in its entirety, trying to bring it back home. If you were to follow a prototype to production optimization stream for plastic components, you would start with additive. You would go to urethane casting.
You might CNC machine a couple of them. You'd go to a bridge tool and then a full-rate tool. And frequently in the plastics world, you have to talk to three or four different suppliers in order to do that. You at least have to talk to a dozen different engineers, and it takes a really long time. We were able to walk across the entire spectrum of let's call it productionizing this product, which was an ultimate success.
With a single point of contact, this was a engineer who used Xometry for the entire process, all of which took under six months, and ultimately was a success story in two ways. Well, three. In one, the part count for the entire assembly was cut in half, approximately 80 parts to approximately 40 parts. The Xometry focused iterations were critical to that success.
Two, timing. There was only so much stock of assemblable components at the assembly bay to keep everyone moving. Had this process gone on another two, three months, we're laying off employees because they can't have nothing to build. And three, the customer lead engineer on this project was actually so enamored with seeing it happen in real time that he's now a Xometry engineer.
Let's go to the next slide. Military drone reshoring. This is an interesting one. Our customers are very diverse. Our projects are very diverse. This is approximately a 200 part bill of materials for a real deal in use military kamikaze product, which is interesting for its internal diversity. We have CNC parts, additive parts, harnesses, metal, injection motor parts, and interesting assemblies.
The challenge for this was arranging for the diverse partner network support necessary to do it, commonizing all of the inspection certification quality requirements across this diverse bomb, maintaining a routine schedule for both quoting and ultimately producing it, managing deliveries for first article inspection for both us and for our ultimate customer, and finally, keeping it all together because as you can maybe imagine, customer instructions vary.
Hey, we have a new demand from our customer. We're going to scale demand up. We're going to scale demand down. We have these new certs. We're getting rid of these old certs. As often happens in the product development world, we're not working with static products and we're not working with static product demands. And responding to that dynamism with a diverse product such as this is the challenge and the rub and the reason to use us for these kinds of activities.
Next slide. I'm a big fan of this particular project. Like most engineers, my childhood dream was to make stuff that went into space. And it's a brutal irony that on this particular one, we caught an error. One of the reasons to trust a particular supplier or partner for manufacturing product isn't always upside. It's downside risk management. Downside risk management is critical to manufacturing.
It's critical to production. Because no matter how well color coded a PowerPoint is, something will go wrong at some point in your relationship with your partners. It's tautological. And in this instance, we included this not only because it's an interesting application, not only because it's failure critical spaceflight hardware, and not only because it was ultimately successful, but because we found problems here.
We had a partner who crossed an I and dotted a T instead of the inverse, and we had a paperwork issue on a raw material cert. I point this out because we caught it. We were able to recover lost lead time. We deployed boots on the ground to the partner in order to really understand what happened. And we took what could have been a disqualifying problem for both that partner working with us and for us working with our customer and solved it.
The criticality of your response is dictated by the experience of the team doing the responding. And one of the only guarantees in manufacturing is that at some point stuff will go wrong and you will need to demonstrate your experience in how you recover. Next slide. These are some of the resources that are available from us at any time for free. Our website is a vast treasure trove of useful documentation.
It's particularly useful for younger engineers who have a lot more responsibility than experience. We aim to be your catch-all production, manufacturing, prototyping, all of it, supplier and partner. If you have stuff to build, we want to talk to you about it. And now we've blown through the content that I had intended to discuss at this time.
Josh Blancet:
And also I want to chime in here and say, another great resource is to reach out to your primary point of contact at Xometry, your account executive, to start those conversations about production. And we can connect you with our team of engineers internally to do everything that Rusty just went through for you all. And like Rusty said, we blew through everything, so Q&A time.
Greg Paulsen:
Yeah, absolutely, guys. Awesome presentation. I think always encouraging, I'm seeing questions come in right now and I'll get to those just a second. But these case examples were also chosen because they show different use cases in serial production. And what we're able to do is utilize a massive supply chain and run in parallel depending on your needs. So you're seeing examples of near shore and you're seeing examples of dual sourcing and find new suppliers or bringing something that wasn't in production into production and sustaining that.
But really, really awesome stuff. So I'm going to jump in. I can see some questions. And again, please keep on asking away. So the first question I have is, how do you ensure IP protection when multi-sourcing while promoting project transparency for quick sourcing transfer? So how do we deal with that?
Rusty Haake:
Yeah, I'll take that one. All of our partners are compelled to enter into mutual NDAs with us before we even get started. It's a very similar NDA to the one we enter into with our customers. So the inner circle, if you will, is completely closed loop in that regard. For preliminary distribution of content, we also redact things like drawings and specifications. You can imagine that as the specificity of your project grows, the number of internal proprietary specs will also grow.
And at that point, it actually becomes an advantage for us to know if our partners have worked with you specifically before, and we maintain that data through our ERP. So it's kind of a spectrum, if you will, of highly specific bespoke interesting production opportunity. We already know who to talk to, and it's a trusted partner who's been in the network for some time who's proven their NDA validity in addition to manufacturing capability.
On the furthest opposite end of the spectrum, let's call that more fungible projects, things that are frankly less special, we do fully redact CAD, we do fully redact specifications, and we do still require all of our partners to sign NDAs, but we've demonstrated that that level of broadcasting is consistently safe and effective.
Greg Paulsen:
Absolutely. And actually I'm jumping back and forth because something related to this because we're talking about multi-sourcing here. And Spencer has a question, how do you manage tooling between multiple suppliers? Because often tooling between various machines are not directly interchangeable, right? You have a different tool bio and tool setup.
Rusty Haake:
Yeah, so let's first define tooling, right? This can mean different things in different contexts. If we're doing a largely CNC focused activity, tooling means tools, machine tools, the thing that cuts the metal. In these instances, the tooling is typically a very small part of the overall production project cost. And we would indicate, okay, if we're doing this at a location in India at the same time as a location in China, we're both investing in that tooling because we're doing stuff simultaneously and it's largely trivial compared to the cost.
On the flip side, if we're doing a molding or a casting project, the tooling is the project to a large extent. If we're multi-sourcing and intending for simultaneous operations, there's no other way to do it other than to produce tooling at two locations. It's standard Xometry practices that the tooling is owned by the customer. It's annotated in such a way that tooling cannot be used by anyone else. So if it is a customer's preference... Excuse me, I've been talking too much.
If it's a customer's preference to have two locations that are ready to do the work, but only one of them gets the tool and the other is intended as a geopolitical de-risk, then there's an NRE associated for having partner B be like aware, up to speed. They read in. They know all the specs. They have the material on hand. They have capability reserved, but partner A is actually getting to dance while the song's playing.
Greg Paulsen:
And definitely I think one of the things that we can come from here is experience with transfer tooling and understanding the tool bio and even knowing the right questions to ask when we're vetting these partners for these needs. So you're talking to the right folks for that.
Rusty Haake:
Can I add one more detail to that, Greg?
Greg Paulsen:
Yes, sir. Yeah.
Rusty Haake:
The example that concerned the real estate lockbox feature a great deal of transfer tooling. We had a bridge tool that was developed in China. It was sent over after producing a couple months of product. And by the time the bridge tool and couple months of product was complete, the production tool was done and also ready to be shipped.
So we have Chinese-made injection mold tooling operating down the block out of domestic mold house that's supplying the production quantities for this. And that's a fairly common method of achieving decreased tooling costs and local production for the molding business.
Greg Paulsen:
Absolutely. So got a question, this is around change orders, if you will. How do you manage contract amendments between suppliers and product owners? And that's a good question from Ben.
Rusty Haake:
How do we manage contract amendments between suppliers and product owners? Sure.
Greg Paulsen:
Yes.
Rusty Haake:
We try to manage as much as we can on the partner side. So you'll have a case manager, sorry, a production manager that is intended to be the single point of contact. And it's our assertion that a lot of the minor ambiguities can be addressed in that manner. But the reality is we do a lot of complicated stuff, and a three-way conversation is oftentimes the shortest path to really getting all the necessary nuance and detail out.
And it's our general assertion standing policy cultural norm that more conversations better than less, particularly when we're in the early stages of a program. And we would rather be redundant in our conversations and emails than be negligent and miss something of value.
Greg Paulsen:
And just on that note, if we see a change order, on the tooling side at least, sometimes a change order could be just grooming, which is typically part of the process and inclusive. But if it's adding a new feature or something like that, there may be additional charge or something that makes sense for that change. But we'll still continue to build to modify that tool in process. Let me go through here. So we were talking about this and finding a good supplier. So on the rare occasion that a non-conformance is discovered, how is that handled?
Rusty Haake:
Yeah, so this is where the experience of the team comes into play. I'll first say, Xometry's been in business for over a decade. We make a ton of parts for a ton of people. Let's roughly estimate, we've delivered 50 million parts. Let's roughly estimate that one-10th of 1% of those parts had a non-conformance. It's 50,000 problems. If you're trying to find a manufacturing partner, you probably want a manufacturing partner who has solved 50,000 problems.
So I don't bring that up to put it in your minds that there's some inconsistently high or inconsistently low or magically special rate of NCRs within Xometry. I bring that up to point out is that we do have a deep roster of people experienced in dealing with such things because the diversity of our work necessitates it. And NCR is managed by processes that are run by experienced people. So our QMS dictates a specific sequence that follows. We investigate.
We understand what happened. We try to understand who the responsible party was. Was it a requirements digestion error? Was it a human error? Was it something that we did wrong? Was it a design problem that just somehow made it all the way to manufacturing without being caught? So the real answer to what happens with an NCR is it depends because the most important thing we can do is understand how that NCR occurred.
Some of the remunerative things that we can do, we can reimburse on lost PO funds if it was truly that simple of an error. We can work to redline documents to prevent it from happening again. If it's a design problem, we can actually provide DFM feedback to resolve that. Oftentimes NCRs are such nuanced quality and documentation paperwork that the components themselves are fine and we can get them cleared and accepted.
We can also revert back to the auto and template defaults within our IT structure that dictate what documentation, paperwork, inspection certs, what have you, get packed in the box when the box is shipped to you. So I realize that wasn't maybe as concise of a response to your question, but I feel like concision is not the right way to answer that question. The right answer is it depends and we're going to figure it out.
Greg Paulsen:
Yeah, absolutely. And I think it's something important to notice that we are acting as your manufacturer and the QMS is Xometry. So we are dictating our quality management protocols down to our suppliers. And I think that's something really important about the value add, especially when we're looking at production and the supply chain. So on the production supply chain, will it always be the same supplier manufacturing the part?
Rusty Haake:
Most of the time. So let's look at some different ways that that can be approached. One of them is you've built parts with Xometry before. And in that instance, you were delighted to use our let's call it core business approach, which does not necessitate pre-sourcing. In that case, you'll have a supplier that gets the privilege of building your parts and they'll mail it.
And if you reorder that six months later or order 10 times as many six months later, if there were no remarks on the previous order, yeah, we stick with the incumbent. There's no good reason to avoid that. What catches that sometimes is when the incumbent is a smaller partner. You can do pretty incredible things with 10 employees and a 10,000 square foot machine shop, but you can't build 3 million of the same part in a year.
So we do have instances where we have an iteration where we did not know that this was bound to be a high volume production component and a 10 person shop knocked it out, and then they knocked it out again. And then we were informed, oh, by the way, this is a production thing. We're going to need 2 million of these delivered quarterly for the end of time.
We need to resource that. And that's where the production user experience walkthrough that we went through earlier comes into play. And then of course, there's black swan events where sometimes components will fight you and a given partner can't get it done, and we will simultaneously or in sequence resource that to ensure we're delivering it effectively.
Greg Paulsen:
I always like the phrase from our COO, which is we're not here to tell the weather. We're here to make out good outcomes. And I think it's really important. We're very proactive, especially on the project management side. Josh, I got something for you. They asked anonymously, but can you share a couple challenges and maybe some of your insights on helping customers in the production lifestyle assistance? So they're working on bringing up the next set of releases and releasing them. What type of pain points do you see? How do you work with those teams?
Josh Blancet:
It depends. I feel like that's the answer for everything because production, it means different things for different people. But in my experience, depending on the size of the company that you're working with, a lot of the pain points is time, speed to data, speed to release drawings from the customer side obviously and then us aligning timelines to their timelines. I find that that's been some of the biggest barriers.
But on our side, we try to help mitigate that with our engineering resources. If it's something we can do to help give you DFM quicker, to make a drawing adjustment faster, we really rely heavily on our team internally in that aspect. In terms of some post-order stuff off, I've had some difficulties in the past where someone leaves the company and we now have a new point of contact that's heading up that program and getting them up to speed to know our internal Xometry team and what we've done and how we've done it.
For the most part, my experience handling production programs, and like I said, I've been doing this for five years now, there's not a ton of issues that I run into as long as upfront I know that hey, if you're prototyping this part, we have production intent on this part. We can make sure we have supplier selection nailed down. We can make sure we have all the quality stuff set up in advance. And it really helps us mitigate any additional risk that may come of that.
So I try to understand as much as I can about the project regardless if we're printing one of them now, what's the future of that part? And I think that's why it's so crucial for us to really partner with you all to say, hey, we want to help be your prototype to production manufacturer. So you're working on X, Y, and Z. Tell me about X, Y and Z so we can deliver across all the different stages of the lifecycle I guess you should say.
Greg Paulsen:
And also you're hitting the nail on the head that we don't have minimums. So a lot of people are coming to us from the RP rapid prototyping stage and the editors find us and they also have this project or that project turns into the serial production need. And us having the information upfront on where you want to be helps Josh bring in Rusty.
It helps the team collaborate and make sure that we're setting you up for success as you move to these different stages, which may be different manufacturing processes, which may be different ways of production origins, et cetera, for this. I have a question, this is more specific, but how do you control special processes such as painting or anodizing with vendors? Often our customers have extremely strict requirements for these processes as inspection is not possible without destroying the product.
Rusty Haake:
You say vendors, we say partners, right? When we have special processes, special is the driving word there, processes that might be considered special to some are rather not to others. So there are dozens of finishes that we apply on a fairly routine basis. All your mil standard activity there. And we are comfortable enough with them to apply costing and apply lead time and just know that our partners can make it happen and let it rip.
When we encounter unique uncommon finishing requirements, we do have a partner network that is specifically finishing oriented. We don't just send stuff to the machine shop partners and say, use your own network and figure it out. We have the arrangements with the true experts in the field. We're able to get component level DFM feedback. We're able to identify whether finishes are called out correctly.
We see plenty of instances in the notes of assumed thicknesses of hardcoat anodize and reflectivity testing that's frankly just incorrect and we're able to catch it. Because as mentioned earlier, most problems manifest when you open the box, but they start when you open the project. We're capable of adding in special testing requirements. We're happy to run first articles.
We are happy to run particular NRE development campaigns that permit you to iterate and arrive at a fundamentally acceptable product. So in keeping with the tradition that Josh just pointed out, the answer is it depends and we find a way to make it work for you.
Greg Paulsen:
Yeah, I think both of you've also worked... We have several customers who they're more open to diversity of manufacturing, but they have a approved finishing list and we're also able to work within your finishing list. So if you have this subset of finishers that says, my parts need to go here, we are able to work within your system as well.
Rusty Haake:
We actually just did over the last 18 months a pretty significant production project requiring a customer-specific finishing list of a CARC finish, which is a I wouldn't say a common aerospace activity, but it's one that we encounter enough to know how it works.
Greg Paulsen:
Awesome.
Rusty Haake:
Yeah.
Greg Paulsen:
So this is about manufacturing inventory. So how do you hone and maintain your manufacturing partner's capabilities and inventory status?
Rusty Haake:
The capabilities one is a really interesting answer. It's actually a secret sauce thing for us. We have a lot of resources tied up in an internal ERP database that tracks all the way down to what machines are on the floor at each of our partners. So the partner onboarding for us isn't just like we mail you a stamp and you get to be part of the club now. It's an interactive relationship. There's a thousand people that work at Xometry and very few of us are in sales.
Most are on either crunching the math of how to make sure our... We're really powered by data engineering. We're really powered by being able to rapidly sort and respond quickly, effectively on complicated technical matters. That's how we really do a lot of what we do. And the partner network is, in my opinion, our greatest asset. This enormous well-understood hierarchically organized, dynamic and collaborative to us network, no one else has that.
It's an incredible asset. So we spend a great deal of time pruning, manicuring, promoting relegating, and organizing the capabilities within that network. So great software, great partner network management and making sure we feed the lions when we want them to do tricks for us. Go ahead.
Josh Blancet:
Yeah, I can add to the inventory part of that as well if I'm answering this correctly or thinking about it correctly. But inventory like what do you need? I just ran a program that we kicked off in India. They needed safety stock here domestically. So we stored three months worth of product at our facility in Gaithersburg. And every quarter I get a min-max report from them that says, hey, we are going to need a minimum of this, a maximum of this.
And then we can tell our suppliers, hey, this is the range that we're thinking. They can go ahead and start on the next quarter's worth of inventory. We will ship out of the safety stock that's in Gaithersburg, and we will then ship product from India to then replenish our inventory here. So they always have inventory on hand domestically. So in terms of inventory management, whatever you need or however your ERP system works with inventory, we can get creative in a solution for you.
Greg Paulsen:
Josh here mentioning our Gaithersburg facility, which was the OG Xometry location, and it's where parts flow. So we have sophisticated QA there, just about every inspection tool known to man because we see a lot of diversity of work coming through. And to your point too, it's really been converted into the value add services like location. So beyond QA, if we're doing inventory, if we're doing light kitting, some electromechanical assembly, all of that can be done within that facility as well.
So we're able to aggregate the demand and the work from different locations, get off the shelf components, et cetera, and do some value add work from that location. And by the way, I know, Russ, you said you ended early, but I think you ended right on time because I still got more questions. So we're going to keep on rolling. We got an hour, man. So someone asked, part of our quality process is to perform physical quality inspections at the facility producing the part. So boots on the ground. Is this something that we offer?
Rusty Haake:
Yeah, I actually just did it. Yeah, we had a customer tour of a facility in Southern California working on a satellite rocket thruster recently. My presenter instinct to talk too much is kicking in, but short answer is yes, we do this routinely. You're welcome to do it. We don't ever hide information from you. When you're doing production, you have the keys to the castle. We welcome it.
Greg Paulsen:
Absolutely. Also, Josh just said thank you. So thank you, Josh. And I got a question here from Nikki. So for the semiconductor industry, we need a Copy Exact where all the production builds are with the same suppliers. How can you make this happen? And thank you.
Rusty Haake:
Copy Exact I think is a cousin term to PPAP. I confess, it's a new term to me, but in production fungibility, when you're trying to assure identical stuff from one location to another or from one partner to another, the PPAP documentation is essential to this.
It's the common language of proving that you can do what you say you can do. And then different companies and different industry groups or industries themselves will have marginally different terminology for this kind of stuff. So Copy Exact appears to be either company specific or industry group specific, their flavor of PPAP documentation.
Greg Paulsen:
That makes sense. And with that, I think I just exhausted the audience question. So audience, you still have a couple minutes to ask some questions here. But one of the things I do want to highlight as we're talking about this is we are not just doing one project for a customer, we usually have multiple projects in parallel. And usually these customers, they're not just an island. They're working on teams.
One of the powers that we have is even when we're working on these serial production orders, you're going to get the extra TLC, but you still are able to see what's going on and the status within your platform. And you can't under emphasize the power of our digital platform at Xometry. You can go back to quotes, retrieve your quotes. You can share quotes in a team. We have something called team space that allows you to invite team members.
So whether it's your procurement lead, whether it's other project group members, all of the above, you could share relevant quotes for those projects. And you have a single view to see what's going on, order parts status, order information. And what I love the most, because I'm a documentation nerd, is everything's digitally stored, securely digitally stored on our platform. So if you need documentation, you could actually go.
You have a shipment and delivery status on those items, click the three little dots to the right of your item, click download documents and you can see everything you have, including inspection reports, material certs, et cetera. So that's all on demand and built within our platform. It's not a paid service. It's just there for you to use. So I don't have any more volunteers for questions. So I think you guys did really, really great here. Josh and Rusty, any closing comments?
Josh Blancet:
We're ready to do your production work. We're excited.
Greg Paulsen:
All right. Well, hey, I think with that, thank you all so much for your time. And as always, you see Josh's information below. We would love to see how we could work with you on your current or new projects coming up. And yeah, feel free to reach out directly. Thank you all so much.
Josh Blancet:
Thanks, everybody.
Greg Paulsen:
Cheers.
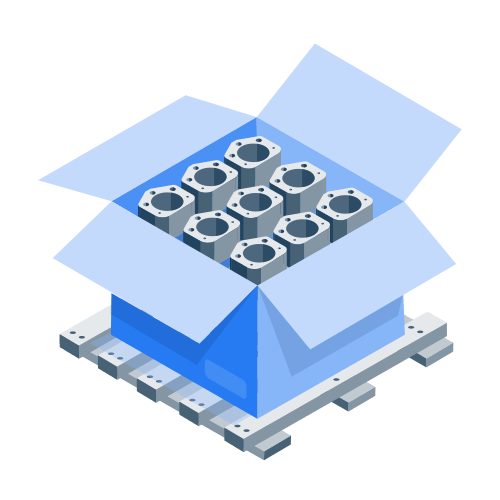
