Design Best Practices for Tube Bending and Cutting
Summary
Tube is a versatile manufacturing material used in just about every application where structures need to be cost-effective. The Xometry team is excited to bring AI and machine learning to provide instant pricing and lead time on mandrel tube bending and laser tube cutting to its Instant Quoting Engine.
The event was hosted by Xometry’s Director of Applications Engineering, Greg Paulsen, and Vice President of Solutions Engineering, Mark Osterman. The webinar recording is one hour with live Q&A summarized in the section below.
Key Takeaways
→ How to use Xometry’s platform to get quotes and critical DFM feedback on tube designs
→ Different tube fabrication processes like mandrel tube bending and laser tube cutting
→ Resources on CAD best practices, including designing normalized cuts
→ Tips and best practices for tube design
Questions and Answers from the Webinar
What tubes do you autoquote?
Check out our Standard Tube Sizes resource page to see our selection of hundreds of tubes!
Where can I download the tube bending and cutting design guide?
You can download it from this link: https://www.xometry.com/resources/design-guides/tube-manufacturing-design-guide/
Does a normal-to-surface cut always prioritize the internal face?
Essentially, yes! We have a great article on normal-to-surface cuts, and it links to specific guides for making the cuts in CAD, like SOLIDWORKS.
Do you offer CNC wire bending or spring manufacturing?
Xometry is always exploring new processes to add to our platform and listens closely to our customers' demands. Our current tube offering is not inclusive of wire or springs but our team is happy to learn more about your project. You can reach out to support@xometry.com or directly to your sales lead if you have one.
Is it possible to quote tubes that are bent and laser cut?
Yes, just like in sheet metal, you cut the flat blank before bending. We will laser cut features in a tube (if present) and then bend. Just upload the CAD file of the final, bent product for us to quote and/or review.
Can you make a complete circular donut, welded?
This would have to be split and sectioned. Our team is happy to manually review the design.
Any plans to offer metric tube sizes/bending?
We launched our instant pricing and DFM based on our North American manufacturing network (US-based). This is all imperial units. As we expand our offerings we will explore instant quoting of metric tubes.
You can always load your project and submit it for a manual review if it is metric.
I'd like to get aluminum tubing bent for vehicle air conditioning systems. Can you do 3003 in addition to 6061? I also have some 5/16" tubing in my system.
If the material isn't listed on our Standard Tube Sizes you can still upload the CAD you desire and select the check box at the bottom of the Configure Quote page to provide a custom ask. Submit that quote for manual review for a team response.
Can your quoting tool for bending offer the additional process of interior or exterior threading at the ends?
We can manually review and add this to the quote. Select the check box at the bottom of the Configure Quote page to add any additional special requirements, and make sure to submit the quote for review.
Can Xometry make a CNC-machined aluminum part with a tubular portion and have Xometry laser cut holes in it?
This may autoquote under CNC machining and skip the laser if we can mill it! Upload your file for a quote here: https://www.xometry.com/quoting/home/
How about just tapping holes normal to the part surface?
Tapping holes in round tubes can be difficult due to the low real estate to add threads and normalized cuts. We can tap square or rectangular tubes.
Will you offer copper tube bending / cutting at some point?
The short answer is "It's probable!" We just launched with tube and plan to expand the offerings into scheduled pipe as we grow.
Do you have coiling capabilities, despite it not being on the instant quoting system?
Currently, no, but there may be an opportunity to find coiling capabilities through our manufacturing director, Thomas.
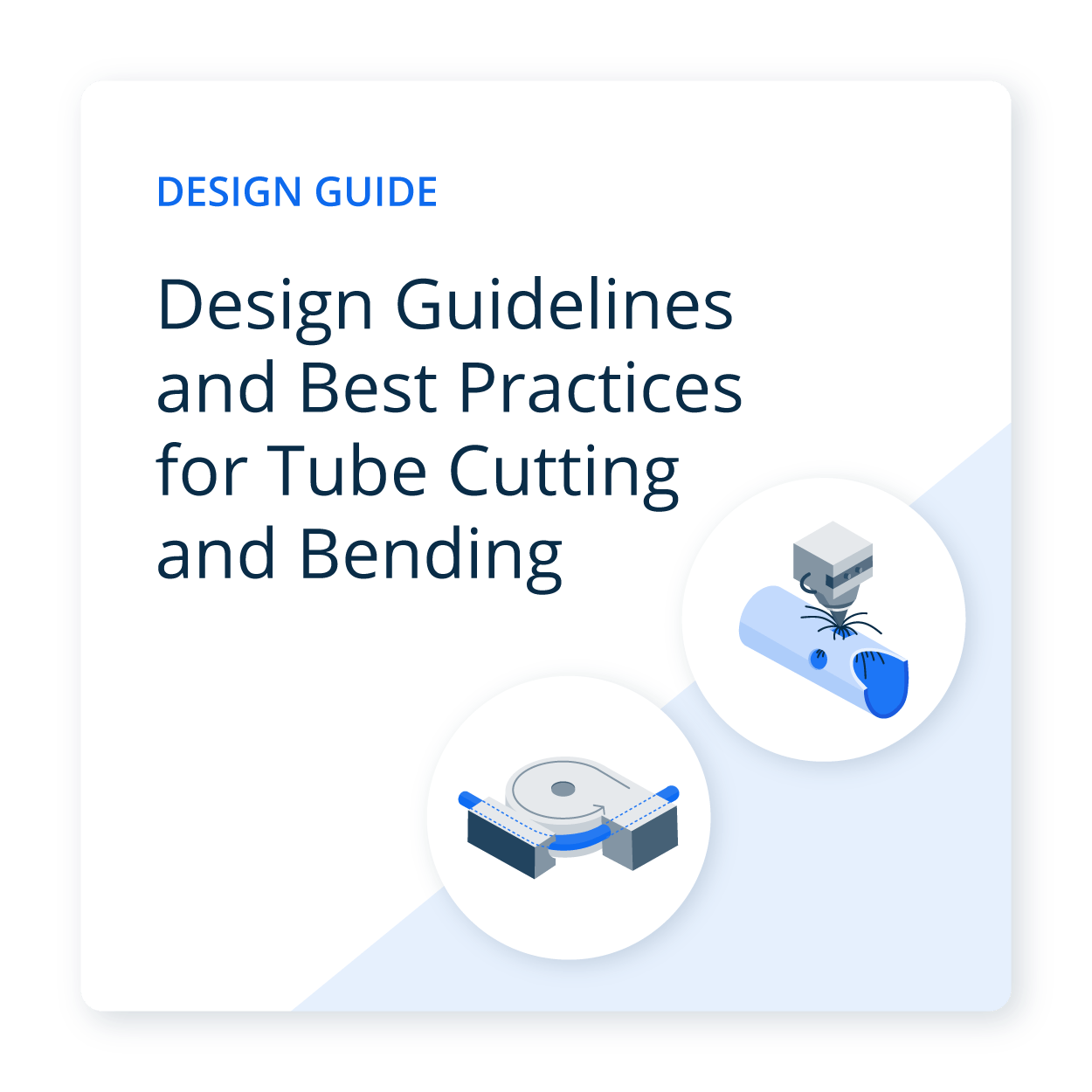
Design Guide: Laser Tube Cutting and Tube Bending
Full Transcript
Greg Paulsen:
Hello everybody. Thank you so much for joining, and we're really excited to talk about tube bending and tube cutting, these new processes that we're instant quoting at Xometry. My name is Greg Paulsen, and I'm just very excited today to talk about this subject as we're launching this out and showing everything that we can do with tube bending and tube cutting. Jumping into this, we have a lot of topics covered, but this is a fun day. We get to live demo, we get to show some other tools and tips along the way, and we're going to begin this webinar though with introductions.
I have Mark Osterman with me and we'll introduce him in just a moment. We'll tell you a little bit about Xometry and our digital manufacturing marketplace, and I'll run you through a live demo of how to use our tools for instant quoting, including tube bending processes and laser tube cutting. This is a new feature for us so we can now instantly price and give lead times with the upload of a CAD file. The pricing, by the way, is very cool because it's AI driven. It is all done using machine learning AI and the power of our manufacturing network. Mark Osterman will be joining us. He's the VP of Solutions Engineering.
We'll be going through those design tips and strategies with Mark and we'll finish with some very useful resources and guides that we have, including a brand new design guide that should be right around the time this webinar should magically appear on our website. The most important thing here is both for myself and Mark here, we work across thousands of projects, across all these manufacturing technologies, and we are professionals at answering your questions. So please use the Q&A tab that's within this Zoom webinar instance and ask questions along the way. We're going to save those till the end of the webinar.
But ask as many as you like because I also will, anything that we don't get to at the end of the webinar, I'm going to aggregate and put, along with the recording of this webinar, because we do have this recorded, on a blog post on Xometry site. We'll try to get to as much as possible. At the end of this we'll save about 15 minutes for Q&A. With that, let's just jump into things. As I mentioned, I'm Greg Paulsen, I'm the Director of Application Engineering and Marketing here at Xometry. I like to make parts, so I've worked for about 15 years both in product development as well as in the service side, so making parts for others across a variety of manufacturing technologies.
Really focus on spinning the CAD with designers, engineers, and procurement teams reading those prints, helping customers choose what process, what technology, and why to go that direction as well as giving design for manufacturability feedback. Mark, are you able to use your video? We're having this juggling of who can share video right now.
Mark Osterman:
I am not able to though.
Greg Paulsen:
Oh, man. What's going on here? All right. Well, Mark, if you want to give an introduction while I try to do some technical troubleshooting on our side.
Mark Osterman:
Yeah, absolutely. Well, I'm really happy to have everyone here today, and like Greg had said, we're excited about this new process technology within Xometry and really want to step through some of the things we do, give some design tips and those sorts of things. I lead the solution engineering team, which consists of our application engineers along with our manually quoting teams as we walk through that. And so, we're in a sense the technical arm of the company and I'm very excited to be with everyone here today.
Greg Paulsen:
Yeah, the solutions engineering team is, it is truly the solutions team by the way. I can't emphasize that enough. All right, we're good. Yeah, so apparently I need to have my video on and then I need to make you host and then you can turn the video on and I get grandfathered in, so that's technology for you. But Mark sees the encompassment of pre-sale as well as post-sale, like as far as the... Well, pre-sale is really where we have these consultative talks but also when we're quoting at work, and then we see what we accomplish with it. It is a really holistic position and it's very cool. It's a fun place to be.
Speaking to that, what do we do at Xometry? For those of you who may be new to us, Xometry, we are a digital manufacturing marketplace. We are almost like an Uber or Amazon for manufactured parts. You can use our platform, upload your technical file, get instant pricing and lead times, and we offer over 20 different manufacturing technologies. When you press buy, we do this AI driven matchmaking. We use AI machine learning to actually look at the scope of the project, and with our network of over 10,000 vetted suppliers, we're able to look at the scope and the capabilities required to make that work and match it with those right suppliers.
What this does for you is it reduces all this time of trying to find the right supplier for those jobs. If you have a bill of materials, you could toss it all on Xometry's website and it could be through various different processes and we essentially become your dispatcher and your quality assurance lead. We're offering a dozen processes, two which are going to be talked about today, tube bending and tube cutting, and we serve nearly 60,000 customers across the globe. A little bit about how this platform works, like this sandwich which is between the buyers and sellers. For you, you get instant pricing, 24/7 accesses to the website.
Assurance and quality and just this true access to a manufacturing network that you may not even know exists out there. Like access to technologies and millions of dollars of equipment just with the upload of a CAD file. Our AI machine learning provides that instant pricing. Then, when you press buy, as I mentioned, we have the seller side, so suppliers that are connected with our marketplace, they're vetted through our Xometry partner network. They have access to essentially a manufacturing execution system called a work center, where they're seeing work on demand, and they're able to take a look at that work. They can see how that fits their shop profile.
They'll get repeat work instantly as it comes through and they're able to make a decision, do I want to take that work? Yes or pass. We have redundant supply chains. Even in incidents, just like today we have terrible storms and hurricanes happening down south, supply chains are disrupted, Xometry has a self-healing supply chain so as people get back on their feet they could access supply chain elsewhere to get the parts they need. Manufacturers in the same way could get work on demand even when their customers are affected. That's the power of a digital manufacturing marketplace. Some of the process offerings that we have, bread and butter for us, machining, sheet metal fabrication, molding and printing.
All of these go together hand in hand with multiple projects both from low volume up to scale production. Then, we also have formative processes for production of metals like die casting, extrusion. We offer sheet cutting services like water jet cutting, laser cutting, and of course, today, we are talking about tube cutting and tube bending. Specifically, we're going to focus on laser tube cutting and mandrel tube bending, a little bit of draw as well, but like mandrel tube bending. Let's talk about, real quickly here, what is tube and tube manufacturing? Just to give you a concept of where and why you see it. Once you start thinking about tube manufacturing, it's like injection mold parts. You just start seeing it everywhere.
When we were launching this within Xometry, I was like, "Hey, guys, look at the hand rails, look at the ADA compliance things. Look at the handle that you just grabbed when you went into our office door." Tube is everywhere. Tube is a way to produce larger structural components effectively and less expensive than if you're using other traditional approaches like cutting it straight out of billet. I'm looking at my desk right here, tube. A lot of things around us that are large and structural, shelving units, et cetera, are made out of tube. When you look at vehicles, look at motorcycle frames, a lot of times that's going to be a tube cut and welded, rolling and falling over protection in the same realm.
Tube is also a conduit, so actual electrical conduits are tube as well as things like manifolds, ducting, piping. It is a very useful geometry. Why it's cheap is because you can get this geometry in a standard stock size, so you're ordering that standard stock and then you're shaping or forming that standard stock into what your application desires. Very similar to sheet metal and sheet cutting, where you're buying a standard stock that's relatively low price and then you're using cutting and forming tools in order to get your application specific so you're able to take advantage of that stock price within there. With that I'm going to jump into our website before we go and start going through design principles.
Because I do want to show you some really cool things that we do with Xometry and with our tube services. I actually have a bit tube design but we can also upload square or round tube for tube cutting as well. But let me just alt tab here and, Mark, you should see manufacturing on demand, right? Cool. All right, so this is Xometry.com's website. Before I jump into the get your instant quote side of this demo, I do want to tell you that as you learn these processes, no one knows 20 manufacturing processes back and forth. We built our website to build technical resources for you as an engineer to understand how to design, what materials are available, and learn more about these processes, especially if you do that.
You may be the best CNC machine part designer in the world, but you may not know much about metal 3D printing for instance, and this is a great place to start. I always recommend, if you're looking into a new process, check out our solutions tab. We have solutions across the board here and you can see here that sheeted tube fabrications right in the middle. You could see some of our sheet metal work, but you could also see things like our laser tube cutting, tube bending services page where you're able to read more about this, look at size of intolerance, materials, design tips, you name it. You're able to find those resources there and there's going to be links to other resources that will help you along the way.
I can't recommend this enough as a resource as you're learning more about processes, and a great way to also make a decision as you're starting your quote. The other resources that I have for tube I want to show is under the resources tab here for standard tube sizes. I'm going to click on that real quickly, but the reason why I want to show you our standard tube size resource is just because it's like a catch-all page that we made here for all the variety of tube and stock sizes that we offer. You can see a little bit of design rules here, but if you want to look at round stainless tube stock, you could see the sizes that we have, for example, for bending as well as the sizes for laser cutting as well.
With that I'm going to click and get your instant quote to show you what getting a quote with tube looks like. I'm already logged in, I am a Xometry customer, I'm logged into our instant quoting website. This is a secure portal, this is connected to me and my parts. I could actually go to recent uploads and take a look at parts that I've uploaded on this account and go and re-quote them. I can also start a new quote. We can upload most CAD files that are either native CAD or step is the universal file format for this. For things like tube bending and tube cutting, we're going to be looking for a solid CAD model. You can't upload a STL or a mesh file and get a tube quote. But like I said, we have plenty of other options available in order to get that quote.
I'm going to go click start a new instant quote and I'm going to go to my desktop here really quickly, and I'm going to take a manifold tube component and put this in. It's going to ask me about export restrictions. No, this does not require export restriction. If yours did, click yes, and we're a really great go-to source for ITAR parts because it's literally a checkbox and we take care of the rest here. What's happening right now, this 3D file is being interpreted. We're using computational geometry and machine learning to make a few guesses about this part, where we're going to be looking at the tube geometry, the size. First off, we're classifying that it is tube and we're going to start building out some pricing and lead time for this.
But wait a second, let's take a look at this. I see manual quote required and I see some information here. This as a trick here because I want to show you what happens when you have a tube design that doesn't fit the standard stock sizes that we have. I'm going to go and take a closer look. I'm going to click on the icon here, and this is DFM feedback. Like I said, not everybody knows how to design tube back and forth, so I purposely put mistakes into this design, which looks good in CAD, right? But there are certain things that are out there. So let's take a look at my manual quote reasons. So I have a design that doesn't have a standard stock available to it. In this case I uploaded a design where there's nothing standard.
This would be a custom extrusion in order to even get to the point where I'm making tube. I also have bend radius, bend radii that don't fit a standard center line radius, which we'll talk about in a moment here, and there are inconsistent bend radii between these two bends, which again, as we go through our designs, we'll talk through a little bit. Lastly, we have bend distance here, which is giving you some guidance, but in this case it's saying like, "Hey, this distance between these two bends here, it's too short." I really wanted to show you that first because this is something really important because you're still in a decision-making mode, you're in the design mode, and we are doing design checks on this tube to look at this feasibility.
You could always submit manual quote here and then it'll go to Mark's team and then he'll tell you the same thing too. But in this case, we're in the driver's seat. I'm going to go ahead and click revise CAD. I've got to go to my V2, boom. Okay, so this is for a 513 Type 5 DOM, drawn over mandrel tube. I just had the wrong stock, it wasn't available in aluminum 6061. This is what we see. We see our tube instant quoting. The DFM is now gone because I actually chose the right stock size for this, and it's going to be acting just like how you would get a quote from any other supplier. You could see my pricing breakdown, you could see my savings over quantity, so as I change my quantity, my unit price will dramatically decrease and that's one of the things, is tube can be a production viable system.
It's going to ask for a technical drawing as I specify this. What we want to know is information about my center line radius, distances that we have here. Tube style, we just want to have some references so we could measure against that when we qualify this and I could continue through adding my quantities and my parts needed, seeing now my price and lead time, and [inaudible 00:15:59]. Then, I could add other finishes like my inspection requirements, and if I have any extra restrictions, shop restrictions needed, or if I need something very custom here I could click on this and this will flag to go to our team to review internally. Mark, anything I should add there?
Mark Osterman:
No, I think that that covers it well.
Greg Paulsen:
Yeah, absolutely. Yeah, I didn't see the aluminum first but yeah, one inch tube is very common in processes, like this is drawn over mandrel. This is the same material, A513 DOM. I just didn't realize I had that when I was selecting through there. But yeah, this is what you see, is you're able to see this instant tube quoting experience online, which by the way is usually a two to three week process to get pricing for. If you're working through a normal vendor, you usually are waiting weeks to what we're doing in seconds. Awesome. All right, so as I mentioned I showed you the standard tube size pages. We offer round, square, rectangular tube, stainless steel alloys, alloy steel, aluminum, and A513, which is a mild steel and these are all very common.
We offer hundreds of options between round, rectangular, and square tubing. With that, let's jump into the remainder of this webinar, it's going to be about designing parts for these processes. The very first process that we're going to talk about is laser tube cutting. This is cutting this straight tube, so the raw stock material. We will cut from the material using a powerful laser. It can trace along the parts, make different designs, so holes, coping features, notches. You can really do intricate designs with a laser. It's very automated, it has very low material waste for it. It's very precise and repeatable. Instead of doing this manually, say you're doing a cope cut, for example, you could get the same cope every single time you make an iteration of this tube.
It can, as laser tube cutting, since we're not bending it, I can accept stock up to six inches both round and square. Laser tube cutting here, I got a little video, is also one of the most entertaining manufacturing processes out there. I dare you to tell me something that's more entertaining than watching sparks fly like this, but you have a clamping chuck that is holding onto the tube. There's actually a series of clamping chucks that is holding on the tube, moving it around. I'll give this a play again. Then, you have your laser head. Note that the laser head is always pointing straight down in this example, always pointing straight down and making those cuts. It can move a little bit left and right or forward and backwards if you're looking at it from the perspective of this video here, to go and create shapes.
But it is producing those parts very quickly and very, very efficiently. Our tube sizes that we have, we can do tubes as small as half an inch with the instant quoting, up to six inches. Square and rectangular are the same type of dimensional differences, and the wall thicknesses range from 35 thousands of an inch to half an inch. Just note that this is our auto quoting list, which is hundreds of materials, but it's what we auto quote and we are assuming all our quotes are normal to surface, which we'll talk about in a moment here. The typical tolerances are similar to our sheet cutting tolerances, at 10 thousands of an inch plus or minus. The other thing to note here is that thickness tolerances are based on the material stock.
Thickness tolerances are independent of the actual cut feature tolerances because they're coming from different worlds. Like that material stock is coming from raw material vendor, and then we're doing the detailing to that. I mentioned this a couple of times, but when we are cutting tube we are using normal to surface. This is probably the most important thing to understand when we're talking about laser tube cutting, because if I am designing a feature, a lot of times when you're designing tube you may be taking a cylinder. Say a tube that mates together, I may be taking a cylinder and then subtracting it from my other cylinder to make a feature. When you just subtract those, you're going to get sharp edges.
In reality, most of the industry standard for tube cutting is what we call normal to surface or a 90 degree cut. What that means is that the cutting angle on the outside of that tube cutting inwards is going to be perpendicular to the axis, essentially a perpendicular surface there, so that 90 degree cut. These very thin features when we interpret that in our CAM software to cut the tube will actually look more like this. Now, this tube, and I have a gallery after this as well, is very exaggerated on wall thickness. It looks pretty scary but it actually really isn't. Most of the time when you look at tube, this is a normal surface cut, it looks like cut tube. You may not even know that there was a difference on what you ordered and what you're getting.
But something to understand, especially as you think about designing for tube, because it does change a little bit of the actual, the physical results of the tube there. There's advantages to this, why do we do 2.5 D cutting? Why do we do normal to surface cutting? I am able to keep a consistent wall thickness around the entire part, so I'm able to keep the power level of my laser consistent as it moves around. It's much more quick, much more efficient. Something to note is that if I have a tube design like flat, you're not going to have any flaring or anything like that because it's going to act almost like if I'm cutting flat sheet metal on those faces.
You're only going to see differences usually when you have a long protruding feature or in these little corners where a cut will occur on the corners, it'll look a little bit different than what your CAD has. To show you more examples of this, this is a little gallery showing CAD designs. We actually have design resources online to teach you how to design in normal to surface cuts on your tubes. Once your tube design is done, you can actually do this yourself and take a look at your CAD. It's going to be a realistic preview of what you're going to receive, but just showing you, especially on round tube, when you have whole features they tend to have a little bit more of a flare on the outside.
The more off axis that feature is, so if you imagine the center of the circle as on axis, you can see it's one to one, as it moves off axis the way that the tube moves and the laser moves with that, you're going to have a little bit more of a flaring. That being said, the actual profile of that circle on the inside of the tube is still that circle. It cosmetically affects the outside, but the inside is what you designed in if you did the extrude cut within. Showing how the tips may look cut off with a normalized cut here. Here's an example from the side of a miter cut, and then on the square tube, similar thing where when you're miter cutting you'll see that those sharp features will almost be blunted out in the cut surface there.
Yeah, Mark, I'll leave it to you on some of the design guidelines though. Tell us about what you're seeing and some design tips.
Mark Osterman:
Yeah, thanks, Greg. Yeah, I want to roll through and go through different design guides, different design tips. One of the things is a general statement about tubes, whether they're cut tubes, whether they're bent tubes. Typically, this is going to be one of the later things designed in into a system. So, if you're looking at a vehicle, you're looking at a structural system, most of the time the other components are around you and then you're using a tube to go from point A to point B. How can we do that where we have the right processes, we have the right machine types, and can do that in a way that's cost-efficient and meets lead time and those sorts of things. It's always best to follow the design guidelines and to design it in there where you can.
Now, that being said, sometimes you're trying to fit something into an envelope where we might need to look at what we can't do with a design guidelines, but could it still be done in one way or another? There's always the option to request manual quote. It'll come in and we have a team of solution engineers and others who will take a look at that and we can always work with our partners on some what if type of situations. But again, always best is to look at the design guidelines, especially coming down to the end of the design. A couple of things to keep in mind is the minimum cut feature should be one time the tube wall thickness. Ideally, we're 1.5 times and more, but under one time it becomes very difficult to make that feature properly.
I think Greg went through normalized cutting and the importance of that as well. One of the things too is, again, we think tubes, a lot of times we think fluid running through tubes or electrical wires running through tubes. There's also a lot of assembly structural type of stuff as well. When you're thinking about it, there's really many, many different combinations we can use for notches, for tabs, for various things like that that go in and as well as text markings. There can be marking as far as branding, there can also be marking as far as part numbers, as far as lot numbers, as far as pointing towards what it hooks up to, so the installer has it farther out there. There's a lot of ways you can use the tube outside of just connecting something from point A to point B.
But when we do that, we just want to think through where those notches, where those tabs would be best to put in. Another big design feature, and you'll see me talk about this with tube bending as well, but we always wanted dimension from the center line of the tube. And so, when we talk about efficiency, talk about cost, keeping that at the best spot and those sorts of things, it's always best to have a 0.01 nominal tolerance to avoid secondary processing. So if we get into that, not impossible to do by any stretch, but anytime we get into secondary processing there gets cost and lead time added into that. Then, the final point I would make is, obviously, there's a lot of different types of materials out there, there's a lot of different types of finishings and things like that that will have different characteristics.
One is we see a lot is with aluminum you do get more slag and splash than a carbon steel. Are there materials stainless steels going through? It's always something to keep in mind as well as you design those, if it's going into a very clean system and those things, we'd want to look at cleaning and deburring but also could look at different material types as far as that goes as well.
Greg Paulsen:
Yeah, and I'll add, although you can't see it too much on this one, but usually slag is, so this is aluminum tube here that's laser cut. You can even see some notches that we have in the design here. But if I touch on the internal of these holes, I can see it's a little bit of roughness and that's not a burr in a traditional sense. Like what Mark mentioned, it's slag which is literally melted material that is in a melted state and then freezes in place once the energy is turned off in that area, and it comes off pretty quickly. Actually, like this thing, it essentially smoothen itself out with my thumb just from me holding onto this design.
But if we do have a critical need, let us know because slag, keeping a little bit of those remnants is fairly industry standard on a standard result product. But if you have additional need, we're always happy to take that. We make turnkey parts here so we just need those notes to be mindful of that.
Mark Osterman:
Thanks, Greg. Then, just some other features to avoid, we want to normalize the cutting wherever possible. If we get too normal to edge, then again, you get into cost, you get into lead time, a lot of these things can be there but we want to normalize wherever we can. Some of the small features and gaps, especially if they're very close to each other can be very difficult, can blend into each other. That can cause an issue. Same thing with as well, if you think about in the tube, if we'd want to do a split across the top, what happens there is we can do that and it splits, but when it relaxes depending on the length of the cut, depending on the thickness of the material, depending on the type of the material, it's going to spring open to a varying degree.
To do something like that and hold an exact tolerance and those sorts of things is difficult. Then, there's also the shipping of something like that can be difficult, including something as I would call as wispy. But if we have a part that's bent to an exact shape and exact tolerance, but it's a very thin material, it's a weaker material and it's moving around during shipping and things like that, it's always something to think about because with cut tubes and things like that, how we handle them, how it's going to be handled during the processes is always something to think about as well. As we have these come in, our team will always advise where there can be best practices along these features and things like that where we see these things. But yeah, these are some features to avoid
Greg Paulsen:
By the way, we also can get convinced, we're going to give you the best practices. I think Mark mentioned, as in know the rules so you know when to break them. Sometimes there are applications where your part essentially is cut with tiger stripes or something like that to have a really cool look, and candidly we're like, that's pretty cool. We also get excited about these projects but we put a sense of sanity because our job is to make the parts right and deliver to you. Ultimately, we wear two hats, which is the quality assurance hat and also the geeking out hat of manufacturing design. We're going to jump next into tube bending. Tube cutting is actually pretty viable. It's because you're cutting holes in the standard stock, you're moving around and there's fewer parts involved in the actual process of making this.
You could do a lot of things with laser tube cutting. Tube bending, there's a lot of ways to bend tube and we're focusing on mandrel and rotary draw tube bending. Really here at Xometry you have mostly mandrel tube bending which is a CNC machine-driven one. But we do want to talk about how parts are bent and then we'll go into some of these design tools here. The tube stock is loaded into a machine or equipment. You are using something to force and guide that bend. Depending on how you're bending that is going to have wide variations of repeatability and quality of those parts. Actually, I'll start at the bottom here. This is not a Xometry offering but a compression bending. If you've ever taken a straw and bent it over your thumb and you see that crimp, compression bending can do that pretty easily if you're not careful.
It's good if I'm making in-house wire conduit systems or something. I have a little floor bender where I can go and bend that part really quickly. But it's not typically used for precision mechanical goods, so it's not on the menu for us. Roll bending is more for things that are going to be seven X diameter or above gradual bends. That's not something we auto quote, but we do have access to that if we need to take a look at that. It would be a manual requirement, but roll bending would be, imagine three wheels pushing together on the tube to create a gradual curvature of that. But these top two here are really, we're using the instant quoting engine for Xometry. This is what we're looking at. So mandrel tube bending is a CNC driven approach.
I'll have a video here in just a moment where you're essentially, you have a mandrel and a chuck feature that's controlling the tube in the angle which is holding it. You have other features that are die features that are moving the tube and creating the bends. The mandrel holds the inner feature of the bend and helps reduce crimping of that, and we'll show you in a second what that looks like. Then, rotary draw is going to be also a die-based system where you have multiple dies holding that together and it can be either manual or automated to those bends, but it does not have the mandrel portion of that. You can still have things that happen on the internal of that tube like compression for example, kind of squeezing of that tube as it bends through.
This is what mandrel tube bending looks like though. This is actually a project that we were working on with the fabrication series. They were working with a launch project for us and we're going to have some cool videos about that coming out. But the mandrel is a piece of equipment. You can see this already has a first bend in it, so you could do multiple bends with this, and right now, the bend die is clamping down with the clamp box there, so bend die is right in the center of this. This is the clamp block. The follower block is coming in and now this whole thing's going to swing around and make the bend. It just completed the bend here, my clamp and my follower are going to open up, so clamps open up. Follower is going to open up.
When you see the person pull this tube out, the thing that's channeling the interior of the tube here, this very long rod, because tube could be 20 feet long, this golden feature at the end here is a mandrel. Imagine something that keeps the diameter but also has a little bit of flexibility. As that bend goes along, it's able to flex just a little bit into that bend curve and is pulling back as that follower is moving along to create a consistent interior diameter to prevent crimping of that. That's what mandrel tube bending looks like and Xometry suppliers, all our suppliers on our network have that capability in-house. The thing I want to note though is we saw a laser tube cutting. You have a chuck and you got a laser and it's cutting around.
The mandrel itself is specific to the inner diameter of the tube that you offered. The bend dies, the clamp box, the follower blocks, so bend die is specific to the center line radius. So what's that radii of the bend that I'm doing? Then, clamp and follower are specific to the outer diameter. You have these three entities that come together to make your custom part. There are common pairings and there are uncommon pairings, and we'll go into that in just a second. From a tube size standpoint, we go from a quarter inch to two inches on bent tube, 35 thou to 0.1875 by 188 thou max wall thickness, and you can do multiple bends. If you are a welder watching this, you may be used to putting together straights and elbows to make a manifold component.
Say you have something with multiple bends in it, you may be ordering an elbow and then a straight, and doing a weld, and then welding that straight to an elbow and so forth and so on, a J feature for example. But a long complex tube for you may be five six welding operations. With these two bending surfaces that we're offering in Xometry, you can upload your CAD and you get a single piece out of that. There's some pretty amazing things you can do with automated equipment. Again, these ranges are the things that we instantly quote and we are quoting right now round tube only for bending. When we look at bent tube, we are inspecting with basically a sheath envelope tolerance, which is pretty industry standard, which means if you imagine a floating tolerance around the entire CAD perfect design, if I can do a best fit of the bent tube within that CAD perfect design, it's a pass.
A lot of times you're using vision inspection systems to actually qualify if those parts are pass or fail there. The other thing that we have pass or fail for is ovality. Like I said, we don't want to have crimped tube for you, so we have an ovality rule which should not exceed 10% of average measured outer diameter versus nominal diameter. Yeah, Mark, if you want to go through some center line stuff.
Mark Osterman:
Yeah, so just some additional things to think about. Like what you saw on that video, there is the clamping die. That is going to be where the tube is formed around. If you picture that process there, one of the things is we want to, when we look at, okay, how we're going to bend it around, it's very important that again, we go from the center line radius of the tube, not the outer edge, not the inner edge. We go from the center line. Then, going from the center line we would want to be at least two times the outer diameter would be the bend radius. Now, with that as well, thinking back to that video, what you saw was the tube is being moved around one die.
If we were to think about one tube and you have four different center line radiis, we would need to have four different dies in there. There are technologies where you could stack dies on top of each other and things like that. But by far and away, to reduce cost and lead time, we want to keep that bend radius consistent all the way across the part and measure off the center line distance. Now, with these, bend dies are a tooling aspect and again in the status of reducing cost, reducing lead time, those sorts of things using common center line radii are going to result and be able to use common bend dies as well, which is very helpful. On here we have per OD center line radius recommendations.
This is where it's best to stay within the guideline where it's at least two times the outer diameter. Then using, per these OD, using these recommendations. Now, that being said, similar to what we were saying before, there's a lot of different options we could look at and things like that and we always wanted to take a look at those designs, but staying in here and staying within these guidelines is going to be the optimal way to design the bend too.
Greg Paulsen:
Yeah, and something I want to note is, you can even see that center line radius, so the internal bend die usually comes in the United States in quarter of an inch increments. If you're like 1.33, you're going to get a DFM flag on that. The other thing to note is most shops, if you go to your tube shop right now, I don't think any shop would say, "Hey, I have all these combinations." This is the power of our marketplace too, is we are actually able to reach and take a look at all of our suppliers holistically and say, "What do you offer?" Because what those suppliers offer is what we offer. And so, we're able to reflect a variety of different capabilities from different shops. And so, this is a pretty comprehensive list of what I call a standard setup.
But you'll even see sometimes some stuff is one inch to one inch, some things are not quite within the roles, but we do know we have those combinations available, so we wanted to show that to you so that you're aware of that as well.
Mark Osterman:
Yeah, and then as well, we were looking at there you see where the clamp block comes in into the tube. Obviously, there needs to be a distance, there needs to be a location, so to speak, for where that's to grab onto. Just when we saw in the video, multiple bends are okay and multiple bends could be 20 bends in a tube or something like that, as long as it's within the guidelines. We'll show some examples of things that don't work, but could do a lot of different bends there. But the big part here is that the straight distance between bends, and so you can see they're on the picture where the lines are. When we say between bends, that's where it'd be measured from, and we wanted two times the outer diameter. It would be the minimum between the bends.
That's where we're going to be able to grab onto and hold. The more space there is in that that could be allowable is better, it just gives us more to grab onto, to get to work with. Then, also, depending on the two bends on the side of it, what plane they're in as well, it can be very helpful to have more space between the bends so the bender's not bending back on itself so to speak. Now, with that being said, there are times when, again, back to the spirit of this as most likely the last thing designed into a system or an assembly or something like this, there are times where this rule won't be able to be had. There are other options where we could actually take you to look at this picture here. We could split the tube in half and weld two pieces together.
We would actually fabricate two bent tubes and weld them together in there. It's ideal if we can eliminate the weld from an additional leak path, additional cost, additional lead time. But if the design absolutely requires it, that can be done but always best to be at least two times the outer diameter between the two bends.
Greg Paulsen:
By the way, I see some great questions coming in, keep on asking away. I just sent a little chat to everybody as well there. This is awesome. All right, bends to avoid.
Mark Osterman:
Yeah, so the other bends to avoid are, again, like I touched on earlier is the multiple center line radii. It can be very difficult to deal with. The distance between is very important as well. But then, the other thing to think about, and the best way I can phrase it is just think about the video you saw and think about if the tube is overlapping itself, to where it's in a small coil or a knot or a Q shape or something like this. Really anywhere the bend exceeds 180 degrees, if it's folding over top of each other. The problem we run into is the bender starts to run into itself and you can't really twist it up. There are machines and technologies to do coils and coiling equipment and those sorts of things, which is different than tube bending there.
Always try to think about pictures like this or a knot or something like that. We would need to figure out a different way to do that than just bending on top of itself. That's really just the physical limitations of the benders.
Greg Paulsen:
Yeah, absolutely. This one could be, for example, a split. A split and weld maybe the way to get the geometry you need or rethink your design there. Hey, speak of the devil here, get your questions ready because we're just about to start the Q&A, but I did want to highlight, as we've gone through these design tools, that we have a lot of design tools. This is two out of 20 manufacturing processes we have. We have a lot of resources online. I highly recommend checking out some of the other live webinars that we've done. Just search webinar under the search bar at Xometry.com and you're going to see plenty of them.
We have downloadable design guides available for all our processes, so you're able to take a look. If we don't have a design guide for it, we have many guides available within our blog. Our blog post will have many guides, case studies and other product updates there. But we have a lot of resources because we cast a really wide net. We work with so many engineers, procurement leads, buyers, suppliers, you name it. And so, we try to build the tools available to help you do your work well and help scale. With that we have the guide, so the guide should be up. I haven't checked myself because we timed it just about the same time as this webinar here, but this is brand new.
Our design guidelines best practice for tube cutting and bending, it's going to go over a lot of what we discussed today in this webinar and have a little bit more information as well and resources. But it's something that's available for download as a PDF copy. So definitely get the guide, and on our follow-up email we'll give it a shoutout as well with that link. You don't need to write the link down right now, you'll get it in the email too. With that let's jump into some Q&A. I have a promotion for you, TUBEQ75, so you could get $75 off your tube orders, give it a go. We're going to have that running till the end of October, so please give us a try. If you have a file, upload that, and again, tube cutting, tube bending and take a look.
Also, if you're not sure what size tube, go under resources and that standard tube size resource will be your favorite page on our website. Megan, if you're available. Yeah, can we run through some questions?
Megan Conniff:
Let's do it. We have a couple people who are interested in learning if you can combine laser cutting and tube bending.
Greg Paulsen:
Yes, the short answer is yes. The laser cutting will happen first, and say for example, I'm making a fall-over protection frame. You can cut those features that you made in your 3D model to help you cope and join. You could have for example, this feature and then possibly the hole on the mating part within your design, but the file that you upload is going to be the bent file. Same thing in the rules of sheet metal at Xometry, is we want that file to be the thing you actually want to receive in the box. Just make sure that file reflects that and we'll take care of the rest.
Megan Conniff:
Sounds good. Someone else wants to know, can you make a complete circular donut welded?
Greg Paulsen:
I was going to say, Mark, I'll let you answer that. I have an idea.
Mark Osterman:
Yeah, it would depend. If we think about a circular donut there, what would be the overall radius of this? What would be the wall thickness there? But we assume that the inner diameter of the donut, so to speak, is big enough. Then, I believe we could weld it together. Obviously, how that tube is cut to get it together, we'd need to look at, but I think it'd be feasible. I would just need to look at the specific design, which we'd be glad to do.
Greg Paulsen:
Yeah, and something to note too is you mentioned the W word welding, weldments and assemblies, there's not a drop-down menu item on our instant quoting website, but we regularly do weldments and assemblies. It requires a conversation with one of Mark's team members, and what we usually will do is we'll add an upper-level line item to your quote for that welding operation, and that includes things like secondary processing. So, a lot of people are like they want it welded and powder coat black or something like that, and we're able to add those specifications. It just requires an extra conversation, but you could see your component-level quoting using the instant quoting engine to get started a rough order of magnitude.
Megan Conniff:
Great. There was actually a follow-up question. If you can make a continuous circular tube donut, can you then laser cut whole pattern into that?
Greg Paulsen:
You would cut first because after that you don't have, I can't chuck up the donut and flip it around. I would just thwack the machine. If you have that within your design, you would want to have that design with those cuts in it. That does add complexity when you think about adding cuts where you're putting bends, because donuts are just a bend, right? It's a continuous bend. Things may get weird. We're happy to have a conversation and see the CAD design and give it a spin and give you some suggestions. Because there may even be processes outside of tube where it may make more sense to go with that approach.
Megan Conniff:
Now, Greg, you were talking about welding earlier. What type of welding do you use for the split and weld?
Greg Paulsen:
I want to know that, but I think it depends on the material.
Mark Osterman:
Yeah, it's going to depend on the material type and the thickness as far as going in there, as far as the method used. It would depend on the specifics of the material.
Megan Conniff:
Great. Someone else is asking, how does the quoting module reflect an actual flattening that happens when tubes are bent?
Greg Paulsen:
Again, there are so many analogies between sheet metal bending and tube bending as far as the concepts go, but we want to see what your design looks like. That's why we want the bent file. A lot of times these mandrel tube bending machines, we are doing CAM dictation, so computer-aided manufacturing dictation, of what's going to happen. Different materials have different kind of stretch factor to them. I am actually not sure in tube, if we call it K-factor, we call it K-factor in sheet metal, but all of that is computed. There's also humans in the loop as we are looking in your bending tube, you'll look for things like bounce back. So you do a bend and you see how much it bounces back and you build in compensation that way.
But it wouldn't be in a traditional sense, if you sent to us a straight tube and said bend here and here and here. Some people will do that with a flat pattern to send out to a traditional bender. A lot of that now is CAM driven, is computer aided.
Megan Conniff:
Got it, so here's another question. Do you bend square tubes?
Mark Osterman:
To do a square design what we would need to do is look at four pieces that are joined together. But with the nature of the bending head, the bending clamp blocks and those sorts of things to do similar as the donut, to do a square with exactly, and as well with a 90 degree corners in there, we would need to do it in four pieces and join them together. But that being said, yes, it can be done, but that's the method it would be done with.
Greg Paulsen:
I think I saw someone order a picture frame today or a picture frame style design, but I think I may have interpreted that a different way, which is what you do, like mandrel bending of a square rectangular profile. Right now, our instant quoting, it's not taking that into account, although obviously, if you look around the products you'll see things with that. But as we've launched the instant quoting user AI machine learning, we've really focused on the tube sizes from, like I said, I think it's like a quarter inch to two-inch outer diameter round tube for our bending services.
Megan Conniff:
Got it. Now, we have a question about normal to surface cut. Does normal to surface cut always prioritize the internal diameter shape?
Greg Paulsen:
Yeah, so I could talk on this, Mark, because we built guides this summer as we were launching out this process and I was making mistakes left and right too as I'm designing and learning on designing tube, which is part of the fun of my job, is figuring out how to do it so I could teach it to others. But essentially, if I take a feature and I grab this on a plane and I do an extruded cut, imagine I just punch that rectangle down in my CAD environment, the laser and the way the laser is aligned is always aiming to that internal surface cut. The normal surface cut is basically the laser has to maintain 90 degrees to the tube surface as it's cutting because it's staying here and it could do a little bit of this, but it's pointing straight down and cutting through.
Yeah, in this case, and again, this is a normal to surface cut and you could barely see it because the diameter's relatively thin to the tube there, but these walls are a little bit flared out. But if I look at my CAD, the inner rectangle would be what I designed. The same thing with circles, so circles flared out by the edges, but the inner circle would be that feature that I designed in my CAD.
Megan Conniff:
Great. Next question. Any plans to offer metric tube sizes and bending?
Mark Osterman:
Yeah, metric tube sizes and bending, we don't see a lot of that here. One of the complications is, as you get into obviously a different raw material buy and inventory, you get into a whole different set of clamp dies and things like that. It's definitely something that can be done, but just by the nature of it, and the flip side of it is to have partners in Europe who stock these and have this tooling to be shipping over this type of product, and things like that can be inefficient. In general, right now, it's not in the forefront of our roadmap to have metric sizes here in the US. That being said, based on various projects, things like that, it is a matter of materials and tooling, which is not out of the question. But for our partner base to be working in that would be a little bit difficult without a project based to it here in the United States.
Megan Conniff:
Great. Now, we have a question about the quoting tool. Can the quoting tool for bending offer the additional process of interior or exterior threading at the NEDS?
Greg Paulsen:
I think in that case I would show, let me see if I still have my quoting engine open. I'm moving a quoting engine here. This is where if you go under configure part, at the very bottom, and again, this is yelling me a drawing because I don't have a drawing uploaded for this, but at the very bottom I have this item called custom manufacturing requirements. It allows you to type in what you need as well as attach a drawing. That is basically you sending a signal to our solutions engineering team. If I save properties out here... It's yelling at me for more information, but if I save properties here, it'll go to manual quote required, request manual quote, that's going to go to the Marks team.
A lot of these, if you have a design that is not auto-quoting, but you know this is something that's manufacturable, and you're looking for a new source, this is where you could press this button. It'll go to our team, we'll give it a manual review. We just don't have the AI trained to actually detect that information yet.
Megan Conniff:
Do you measure and inspect two parts?
Greg Paulsen:
Yeah, so measuring inspection, it's interesting because it's gotten more uniquely digital. In fact, actually, I was working on a manifold design and you see a lot more vision systems that are actually looking at tube and then comparing the actual results versus the manual results. This is all size dependent too. Obviously, straight tube and tube cut parts are maybe using more manual tools, and it's relatively, compared to machining plus or minus 10 thou is a pretty forgiving tolerance range for those processes. But when you look at larger bent tube, that jacket, that tolerance jacket is going to be the most important thing for us as we're trying to see, especially over for multiple bends, how things stack up.
Because it's not just stacking, stacking, stacking, and then all of a sudden we have something that's a quarter inch too long, that's something that you can't install. The overarching jacket of the tube within that tolerance range of eighth of an inch is going to be how we're going to be measuring that. Like I said, it's usually visual tools.
Megan Conniff:
Great. I know we're coming close on time, but we have another couple questions if we can get through them. Will you offer copper tube bending or cutting at some point?
Greg Paulsen:
Mark, I think at some point is the correct answer, right?
Mark Osterman:
Yeah. No, I think for sure we will at some point. With copper it's, obviously, a lot softer material. You can have some inner folds and some bends and some things like that. Yeah, I would think that is something we will look in our line but need to be really careful about the equipment available, things like that. But yes, I would expect that in the future.
Greg Paulsen:
Yeah. This is something, by the way, we're talking tube right now, so pipe and tube are two separate beasts. Pipe is usually for pressure holding work and that's actually a lot of times where you're going to see copper in other devices. It's also defined differently where in tube we define outer diameter and then wall thickness. Pipe, it's done by the inner diameter and then a thickness that they call schedule. It can be very confusing and if you ever ran between a standard tap and then an NPT tap, you'd know about that confusion where you ordered what you thought was going to be a eighth of an inch and it came out to over half an inch wide.
There's definitely a difference there, but it's not something that we have launched right now, so we're focusing on real tube and not the pipe products right now.
Megan Conniff:
Got it. Do you have coiling capabilities despite it not being in the instant quoting system?
Mark Osterman:
At the current moment, we don't, but that is something we're looking at as well. Within the partner base, the ability to coil is a different set of equipment than the ability to bend or cut tube, and so really it is looking at partners who either have that additional equipment or new partners and things like that. But yeah, certainly something we have on the roadmap and we'll get to down the road, but right now we don't have that. But that is planned and in a great way we've seen some requests for that, which gives us a lot of energy to get that capability added on here, both for auto quote and overall capability as well.
Greg Paulsen:
Yeah. I'll chime in because I also see another question, which someone ask something similar in my opinion, which is about things like solid wire and spring clips and et cetera. It's interesting, whenever we launch new process, we get those manual quotes for things like solid wire bedding and stuff, so we're able to review that, and what's good about that is that we're able to see, "Hey, what are our customers asking for?" It helps us understand where to prioritize our next commitments to adding processes and materials to our platform. All right. Well, I think we're a little over, so I think that's good. Megan, any last questions?
Megan Conniff:
I think we got to almost everything. Thank you, Greg. Thank you, Mark.
Greg Paulsen:
Awesome. Thank you all so much for attending and look forward to the email coming out with the recording as well as we're going to have a link to our design guide. Definitely check that out. As always, we're available for you. Please feel free to reach out with any questions that you have and upload some parts, get some quotes.
