Lasers have made a lasting mark on modern manufacturing- literally.
Technological advances in solid-state laser technology allow manufacturers to set permanent marks into parts with extreme precision. Processes such as laser cutting, laser engraving, color marking, and others are possible thanks to the advent of the fiber laser and the fiber laser marking machine. These processes are popular in both amateur workshops and dedicated manufacturing facilities, and marking is only possible thanks to laser marking systems--but what are fiber laser systems, and how do they work? This article will explore what a fiber laser marking machine is, how it functions, its advantages and disadvantages as a manufacturing process, and finally its industrial applications in modern industry.
What is Fiber Laser Marking?
A laser marking machine (also known as a fiber laser engraver, laser marking machine, laser marker, laser marker system, etc.) creates permanent markings onto a workpiece. This laser technology can be automated so that marking occurs within minutes (if not seconds) and works with many materials such as wood, paper, glass, plastic, stainless steel, etc. Before going any further though, it is important to define the differences between laser machines that perform laser engraving, laser etching, and laser marking:
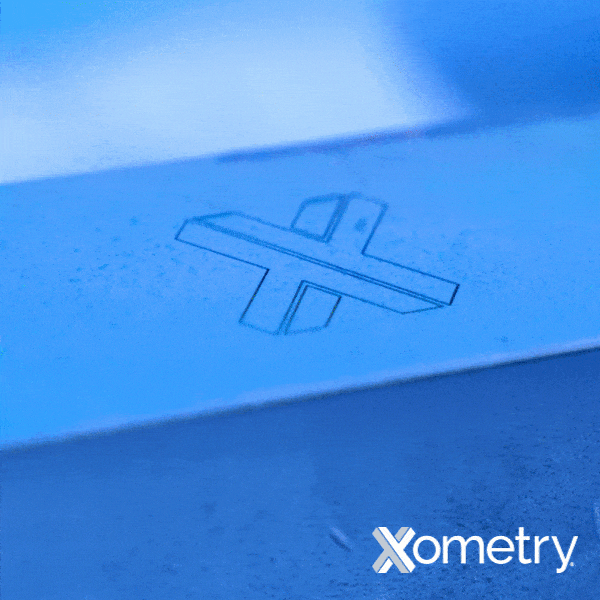
In general, laser engraving is the most subtractive manufacturing process, followed by laser etching, and then laser marking. Fiber laser engravers produce deep-set grooves that maintain their fidelity through extreme conditions and can be fine-tuned to the user’s desired depth. Laser etchings are shallow marks and include so-called laser ablations in which a top coating is lasered off, exposing the underlying material.
Laser marking is a category of its own, as it removes no material but changes its surface properties. The four most common reasons for marking a material are for:
- Annealing: changing the mechanical properties of the material in the laser’s path (this is typically performed with metals)
- Carbon migration: carbon at the material/laser interface chemically bonds to its surface, creating permanent black markings.
- Coloring: specific-colored marks made by heating the underlying material (ex. Titanium can become any desired color given a specific temperature is reached)
- Foaming: creating marks lighter than the underlying workpiece (only possible with plastics)
Most laser marking systems have the capacity to perform engraving, etching, and marking, so this article will not differentiate when speaking about specific models/specifications. However, understand that each term is not synonymous.
Regardless of the type of laser marking system, the chosen laser machine will employ uv lasers, CO2 lasers, and/or fiber lasers. This article will focus on the fiber laser, as it is a good balance between power, speed, and affordability, but know that other types are available.
Fiber lasers emit high-intensity light at wavelengths that are hundreds to thousands of nanometers in length, placing them somewhere between ultraviolet and infrared wavelengths (typically invisible to the human eye). For fiber lasers specifically, wavelengths of 1030-1090 nm are often chosen as those wavelengths correspond to ytterbium-based fiber lasers and provide the best results on metals. This contrasts with CO2 lasers, which generate high-intensity light at thousands to tens of thousands of nanometers that is more suited for organic materials.
To explain the basic operating procedure of a fiber laser marking machine, the next section will detail how fiber lasers work and how they can produce extremely high-quality marks.
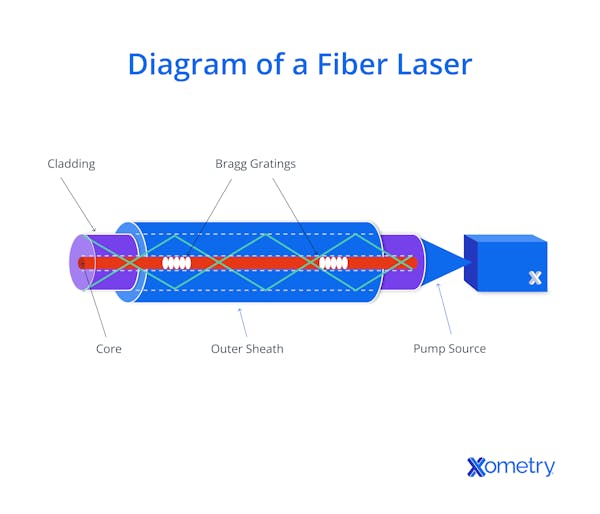
Laser is an acronym that stands for Light Amplification by the Stimulated Emission of Radiation. To briefly summarize without going too far into the particle-physics-weeds, lasers are set up so that the following steps occur in succession to produce superheated beams of light:
- Photons from a light source (or laser diodes) stimulate a material (in our case, ytterbium), heightening the energy state of its electrons.
- As the electrons change energy states, they absorb the incoming photons.
- More photons from the original light source come along and knock the electrons back down to their ground state.
- When the electrons return to their ground state, they emit more photons.
- These photons are “corralled” back towards the electrons and cause an exponential generation of photons via steps 1-4.
- These photons are directed so that their wavelengths fall in sync, forming a coherent, focused beam of light which is then amplified further and directed to the output of the laser.
Note this list is highly simplified, but it hints at the most important aspect of this process- the fiber optics.
The optical fiber is built with an outside cladding with a low refractive index and an inside core with a high refractive index. The difference in refractive indices causes the light beam to concentrate in the core, where the desired photon cascade occurs. Rare earth elements are used to dope the inner core, as these elements emit discrete wavelengths not found in more common elements. In our case, Ytterbium is doped in the core material because its electrons emit a specific and discrete wavelength that produces high peak power. Additional parts of typical fiber lasers are combiners, amplifiers, master oscillator, gain fibers, etc. but know that all these components work to increase, isolate, and coalesce the signal into a coherent laser at the output.
The X and Y galvanometers accept precise electromechanical movements from a programmable microcontroller. The lens focuses the incident laser beam onto the workpiece, while the galvanometers move the laser in X-Y coordinates based on the user’s design. This setup allows the user to create a design, load it into the microcontroller of the marking machine, and execute the command autonomously and at high speeds.
Table 1: Material selection in laser marking
Material | Advantages | Considerations |
---|---|---|
Material Acrylic | Advantages
| Considerations
|
Material Glass | Advantages
| Considerations
|
Material Leather | Advantages
| Considerations
|
Material Metals | Advantages
| Considerations
|
Material Plastic | Advantages
| Considerations
|
Material Wood | Advantages
| Considerations
|
Marking technology is flexible, accepting a wide range of materials. Below is a brief table exploring the different options for laser marking and their advantages and considerations. Note this table is not exhaustive.
Fiber Laser Marking Advantages/Disadvantages
As an emerging technology, the fiber laser marking machine is incredibly popular across many industries- but it is not without its limitations. This section will detail the main advantage of the fiber laser marker over other laser systems, as well as its disadvantages.
Advantages of Fiber Laser Technology
Below is a short list of some of the benefits of fiber laser systems:
- Fiber laser technology provides high contrast marks that can survive sterilization, chemically corrosive, and/or other extreme environments
- Fiber laser marking is a no-contact solution, and requires little to no maintenance over long periods of time
- Fiber laser markers provide high speed marking, are compact, can be easily deployable, require no recalibration, and offer low error
- Production is cheap, reaches faster speeds, waste-free, energy-efficient, and requires no additional resources apart from the workpiece
Disadvantages of Fiber Laser Technology
Below is a brief summary of some of the considerations and limitations of fiber laser systems:
- Laser marking only works in 2D applications
- Fiber laser marking machines have a high initial investment cost
- Materials with high hardness, low ignition points, and other unsuitable characteristics cannot be used, limiting election
- Fiber laser marking machines come in a variety of sizes and arrangements, with some suited towards use with an exclusive process
Automotive industry
- Parts traceability (country of origin, serial numbers, barcodes)
- Dashboard markings/buttons
Integrated Circuitry
- Tiny graphics and texts on ports, connection points, etc.
- Non-contact ablations to reveal underlying IC layers
Electronics industry
- Thin metals manufacturing/marking
- Exceptionally clean and aesthetically pleasing markings, logos, text, etc.
Medical industry
- Acid, corrosion, high temperatures, and sterilization resistant printed labels
- Traceability for LIS, hospital databases, biofluid storage, medical devices, etc.
Jewelry industry
- Text/graphics inscriptions into rings and necklaces
- Gem cutting/engraving
Food industry
- Packaging labels, text, graphics, etc,
- Cans, bottles, container labeling
General Manufacturing
- Burr removal
- Non-industry specific custom metal marking finishes
Summary
Fiber laser marking is a versatile process that provides exceptionally precise markings on a variety of materials. We hope this article has clarified what fiber laser marking is and how it is implemented in industry.
Are you in need of part marking? You can get your quote in seconds with Xometry. To learn more about our part marking capabilities, check out our Ultimate Guide to Direct Part Marking. In that guide, you will find our guidelines around each process and further information on the types of markings we perform and what we'll do in case of missing information to ensure your order gets to you on time while remaining to your specifications.
Disclaimer
The content appearing on this webpage is for informational purposes only. Xometry makes no representation or warranty of any kind, be it expressed or implied, as to the accuracy, completeness, or validity of the information. Any performance parameters, geometric tolerances, specific design features, quality and types of materials, or processes should not be inferred to represent what will be delivered by third-party suppliers or manufacturers through Xometry’s network. Buyers seeking quotes for parts are responsible for defining the specific requirements for those parts. Please refer to our terms and conditions for more information.
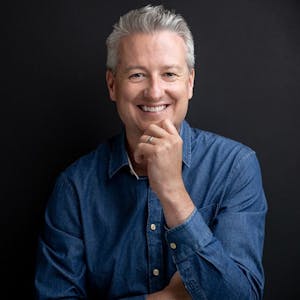