Case Study: Cal Poly Hyperloop Team SLOs Down with Xometry Brakes
A team at the California Polytechnic Institute, San Luis Obispo, competed in their first SpaceX Hyperloop competition. Utilizing Xometry-manufactured aluminum brake frames, the team passed structural tests with flying colors.
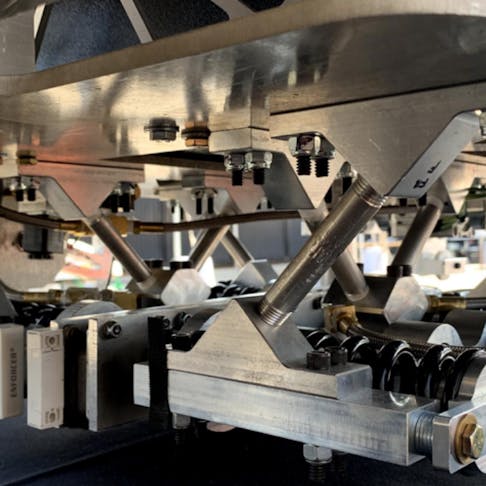
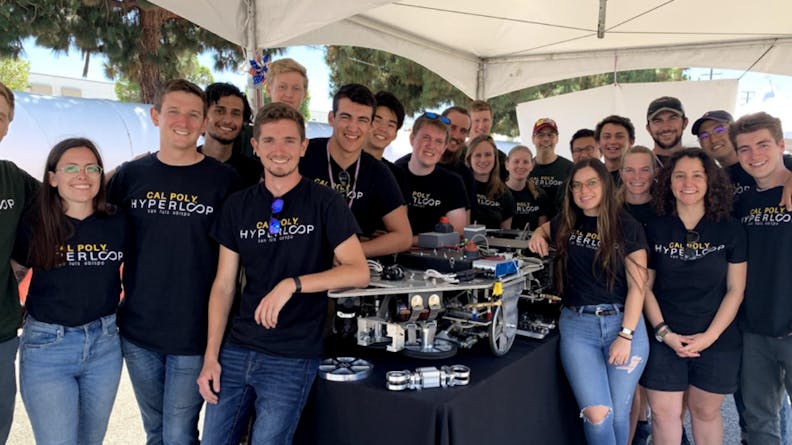
The Hyperloop team, SLOLoop, of Cal Poly San Luis Obispo
SLOLoop focused first on building a powerful braking mechanism. Brakes are among the biggest design challenges in the Hyperloop competition since the pods operate in a vacuum-sealed, zero-convection environment, and must safely decelerate from top speeds of up to 284 mph. “The important part of the pod is getting it to stop,” says SLOLoop’s Braking Design Lead, Bradley Albright. “The motor or electronics can fail, but not the brakes.”
The team’s solution was a set of six brake frames that, together with brake pneumatics and springs, would generate 90 lbs of frictional force between each brake pad and the monorail in the Hyperloop tunnel. The inward force of the brakes capitalizes on the greater surface area on the I-beam than the pod’s wheels.
For the rest of the pod, the team focused on building a simple, scalable design. To this end, the pod costs less than $20,000 to manufacture and can carry heavy loads of over 1,000 lbs. Additionally, the whole pod can be bolted together with no extra welding or assembly involved, making it cheap and time-efficient to mass-produce. SLOLoop’s pod design brings the future of high-speed mass transportation even closer.
After submitting a 120-page design report in January 2019, SLOLoop was one of 22 teams internationally invited to build and compete their pod in SpaceX headquarters in Hawthorne, California. By March 2019, SLOLoop was off to a fast start and began bringing their design to reality.
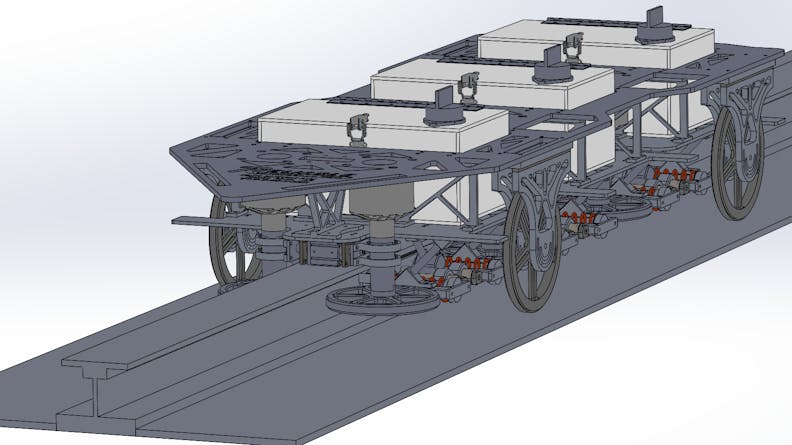
A CAD render of the final SLOLoop pod for the SpaceX Hyperloop competition
Building the Pod with Xometry’s Help
He saw Xometry in a trade magazine and the name stuck in his mind. He reached out to Xometry staff to confirm pricing for 6 components — the CNC processed brake frames — that would be too difficult and time-intensive for students to manufacture via casting methods on campus. Once the price was confirmed, Xometry engineers called to help the team optimize the CAD further by removing unnecessary radii and chamfers. Xometry engineers were helpful in reminding students of the vitality of design for manufacturability, DFM. The finalized design was manufactured by the Xometry Manufacturing Partner Network.
Xometry manufactured six brake housings for the team. The major design features that the Cal Poly team incorporated into these parts include:
- Two sections to hold the brake pneumatics and two sections to hold the springs. Xometry manufactured the part geometry exactly to specification to allow a precise brake assembly with off-the-shelf springs, pneumatics, and brake pads.
- Strategically placed tapped holes. Xometry manufactured the tapped holes to a low tolerance range to ensure the brakes would secure to the rest of the pod in the face of any stretching or frictional forces.
A high tensile material to withstand braking forces. Xometry manufactured the brake housings out of evenly cut Aluminum 6061-T6.
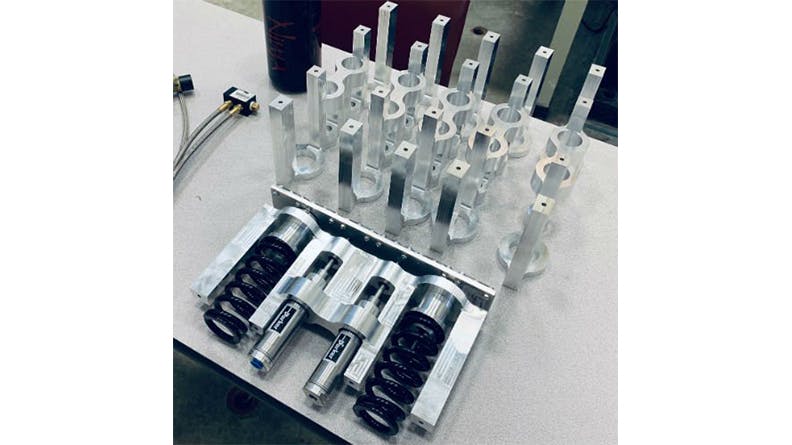
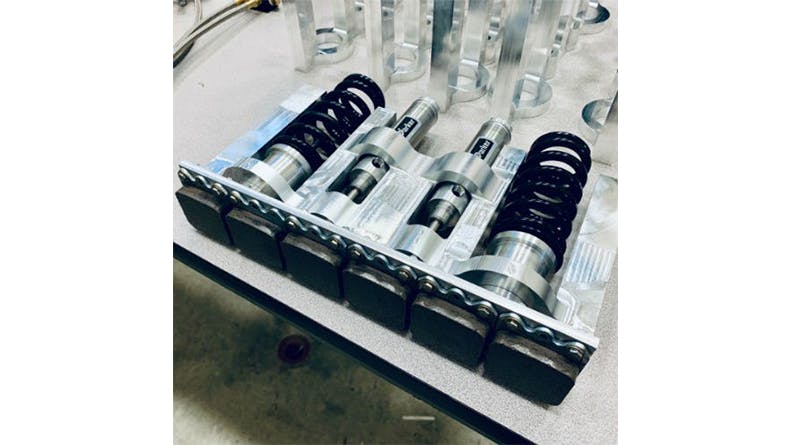
An assembled brake along with the five other brake frames that Xometry manufactured
When Dr. Bensky received the parts two weeks after ordering, he sent an image in the team’s group chat. There was an ecstatic flurry of hearts. “We were approaching our deadline and you guys got us the parts in much less time than we anticipated,” says Albright. Then, when Albright went into the lab to work on the brake assembly, he says it was almost too easy.
He adds, “I don’t think it’s supposed to work like that. There’s supposed to be more pain involved, like Ikea.”
Since the parts fit well into the complex assembly, there was greater certainty that the whole pod would fit onto the monorail’s precise width. This was an issue exposed by early tests on Arizona State University’s practice Hyperloop track, where SLOLoop’s pod prototype was off by just 3 millimeters. This inaccuracy threw the whole test off and took the team 24 hours to fix. Because of this, Albright was happy to confirm that for the Xometry parts, “Everything that was mission-critical, Xometry got spot-on.”
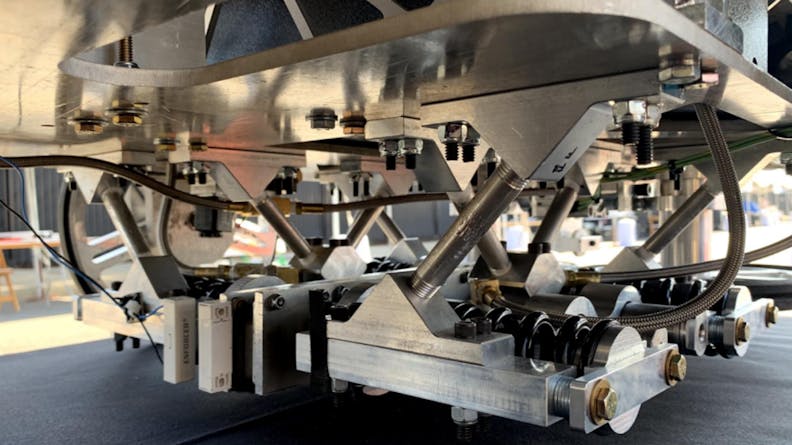
Final brake frames installed and ready for action
The Results of a Robust Design and Xometry Partnership
By manufacturing parts with Xometry, the Cal Poly Hyperloop team was able to save time by getting instant quotes and outsourcing their CNC machined parts rather than using limited study hours to machine the complex parts. In the ordering process, the team had “no delays, no hang-ups, and no confusion,” according to Dr. Bensky. The six parts meet Xometry’s guarantee of 100% quality, each with precise, repeated geometry that allows a sturdy brake and pod assembly.
SLOLoop competed the week of July 15, 2019, with a week of pod tests on everything from the electronics to the brakes. Although the team was not one of the four finalists chosen to load their pods into the Hyperloop tunnel, the team was one of 18 teams to pass the pressurized motors test and one of 11 teams to pass the structural test. The brakes, in particular, were deemed a success and noted to be extremely safe for the team’s intended cargo load design.
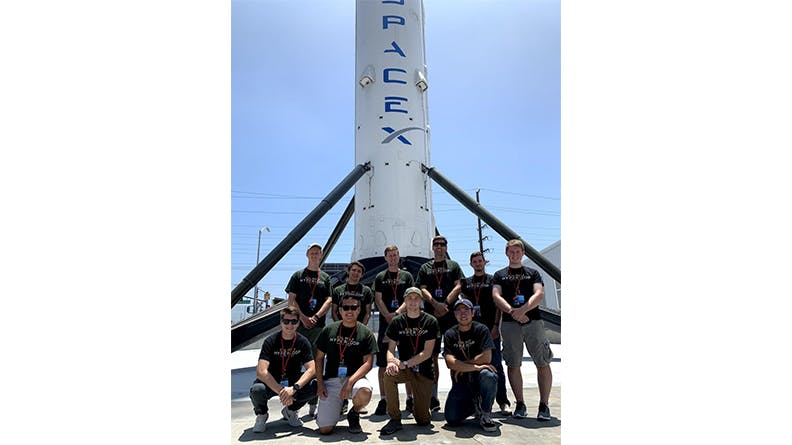
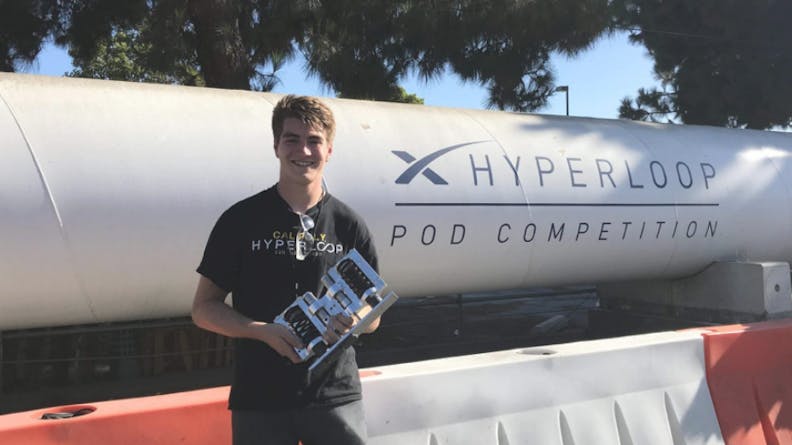
The SLOLoop team at the 2019 Hyperloop competition at the Hawthorne, CA, SpaceX headquarters. Key members include faculty advisor Dr. Bensky, top row and third from the right, and club president Sam Flood to his left. On the bottom row, far left in white shoes is braking design lead, Bradley Albright.
SLOLoop was also chosen as one of seven teams to present their pod, during which they discussed the scalability of their design and revealed the pod cost less than $20,000 (in contrast to the winning pod's build costs of over 4 million dollars). Albright says next year, the veteran team will be ready to compete on the elongated 10 km track with Xometry’s manufacturing help.
Xometry is a proud sponsor of SLOLoop at the California Polytechnic State University, San Luis Obispo. To learn more about manufacturing custom CNC parts, read about Xometry's CNC machining service. To learn more about Cal Poly SLO’s Hyperloop team, view their site.
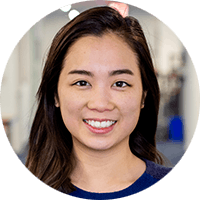