Case Study: Xometry Helps Zaiput Build Flow Technology for the Global Pharmaceutical Industry
Zaiput Flow Technologies, a chemical separation and extraction equipment company, is using quickly sourced, medical-grade custom parts from Xometry to improve its supply chain and better serve its customers in the pharmaceutical industry.
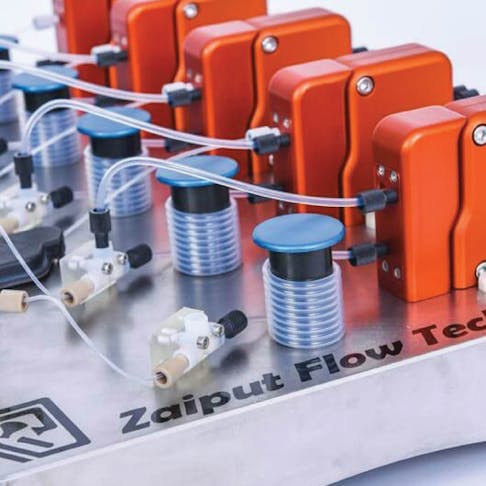
The Challenge | Technologies Used | Solution |
---|---|---|
The Challenge Zaiput Flow Technologies (Zaiput) is a technology company that enables pharmaceutical companies, academic researchers, and more to mix chemicals more efficiently. They needed to create various components for their liquid extraction and separator platforms. | Technologies Used Zaiput used Xometry’s capabilities for precision manufacturing of stainless steel 316L and aluminum 6061-T6 machined and sheet metal components. | Solution Xometry has worked with Zaiput for 4 years to create device main body housings and connecting components that are reliable and cost-effective. These are manufactured with tight tolerances and specific requirements that make the parts chemically inert, nonporous, and easily assembled and cleaned. |
Going with the Flow: Pharmaceutical Innovation
As a leader in flow technology, Zaiput Flow Technologies (Zaiput) is changing the game for pharmaceutical companies on five continents including well-known industry giants. Flow technology is a growing production method used in the manufacturing of pharmaceuticals, providing more efficient and robust operations over the traditional batch production method.
In the industry’s standard batch production method, discrete amounts of chemical material are processed while in flow technology, reagents are continuously pumped and deployed as they travel through the system. Zaiput provides a unique solution for process steps that require separation of liquids (immiscible phases). The technology commercialized by Zaiput was developed by Andrea Adamo, CEO and founder, while he was working at MIT in the department of chemical engineering.
With the help of quickly sourced, medical-grade custom parts from Xometry, Zaiput has created a product that helps pharmaceutical companies reach ideal extraction efficiency. This means these companies can improve their chemical processes, reduce chemical waste, and bring products to market cost-effectively.
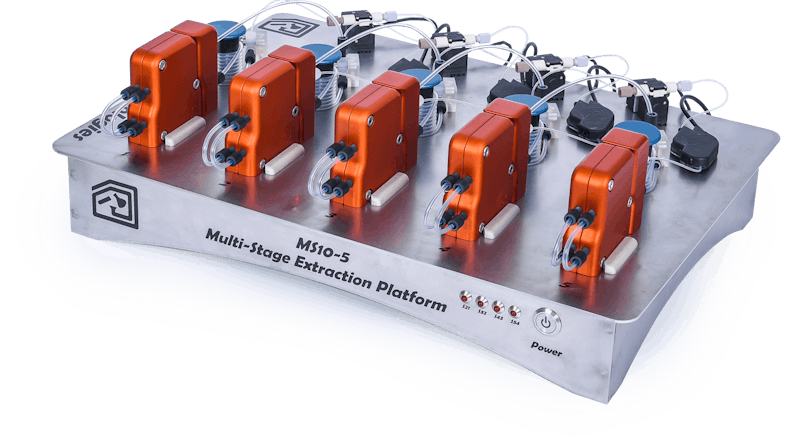
Zaiput’s product uses Xometry-made CNC machined extractor housings, shown in orange
Creating High Quality, Medical-Grade Parts With Xometry
Senior Design Engineer at Zaiput, Robert Butters, utilizes Xometry’s CNC machining services to create Zaiput’s extraction separator housing for its 3 major product lines. In its multi-stage extraction platform product, the housing (orange hardware components pictured below) combines advanced aesthetic design with the mechanical properties of Aluminum 6061. Xometry meets several manufacturing specifications to allow Zaiput to ensure a precise assembly, eliminate device error like chemical leakage, and easy cleaning per FDA standards.
Other manufacturing processes like Xometry’s metal 3D printing service provide the same level of medical-grade compatibility, or in other words, corrosion resistance from pharmaceutical compounds. Zaiput uses Xometry direct metal laser sintering (DMLS) to create stainless steel 316 tubing components. These parts are nonporous, which is suitable for the transfer of liquids because metal 3D printing sinters metal powder into fully dense cross-sections. 3D printing (instead of CNC machining) this component is the best option for Zaiput to achieve the part’s complex geometry while maintaining its structural integrity.
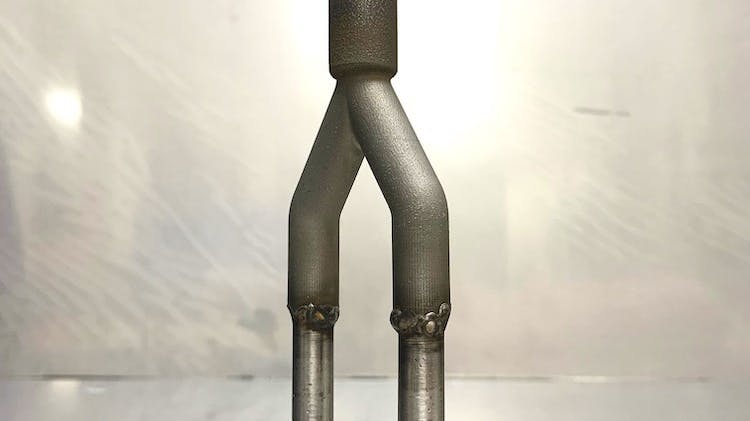
A Xometry metal 3D printed part for Zaiput separation extractors. This part interfaces with the separator as part of the tubing structure.
Zaiput also sources components from Xometry that allow the main device to switch out with a replacement in case of device failure. Xometry manufactured these parts with high precision— below +/- 0.002” in specified locations—due to the requirement to interface with other components.
All components Xometry manufactured for Zaiput must withstand high system pressure since some users require this feature. To meet this specification, the parts have high structural integrity based on sound manufacturing and high-quality materials.
Xometry’s capabilities for precision manufacturing of stainless steel 316L and aluminum 6061-T6 machined and sheet metal components have withstood the test for Zaiput’s growing list of Fortune 500 pharmaceutical customers. “Xometry is a very reliable manufacturer for our parts. The parts we receive always perform to the high health care standards set by U.S. and foreign regulators,” Butters says.
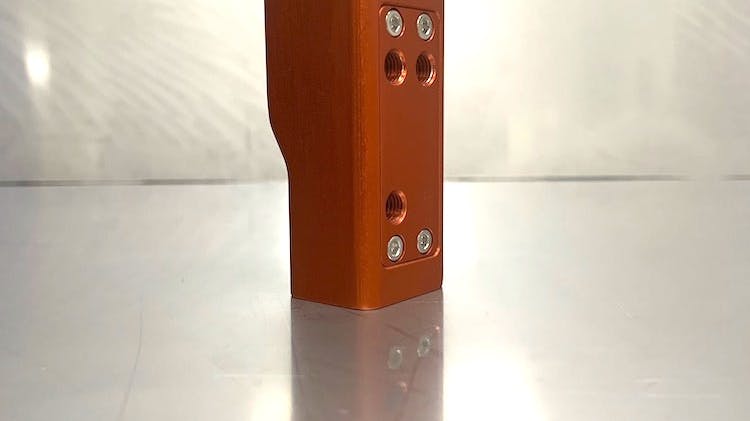
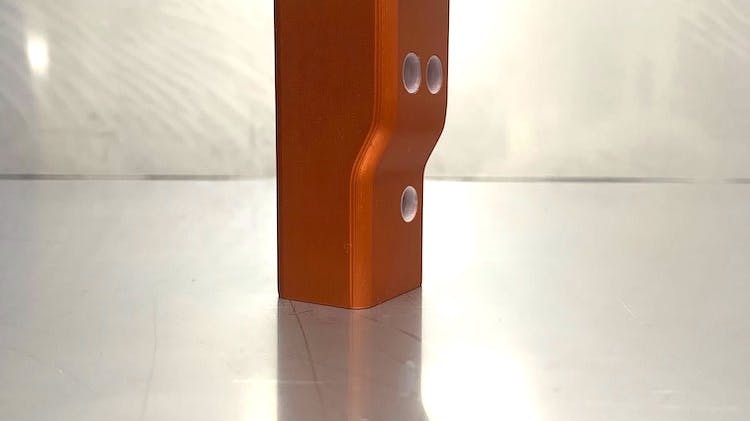
Zaiput’s product uses interchangeable extractor components made by Xometry
Manufacturing Solutions for the Pharmaceutical Industry
With the help of medical-grade custom parts manufactured by Xometry, Zaiput has created flow technology that allows pharmaceutical companies to meet demand more efficiently. Not only is Zaiput able to get its turnkey products to market faster, cost-effectively, and without product error, but Zaiput can break into an extensive range of new manufacturing technologies like metal 3D Printing, CNC machining, sheet metal fabrication, and post-processing without owning the equipment in-house.
Butters calls Xometry “fast, practical, and digital.” “With [the Xometry Instant Quoting Engine℠], I get an answer right away. I can play with the quantity, materials, and processes. No combination is too much.”
And importantly for Zaiput’s prototyping stages, Zaiput engineers can order low-volume prototypes from Xometry at any time. These orders are placed with open-capacity manufacturers in Xometry’s network of over 4,000 manufacturers with no questions asked.
With Xometry as a manufacturing supply chain consolidator for the last 4 years, Zaiput’s technology is revolutionizing the pharmaceutical and health care industries. Together, the companies are shaving down production costs and creating efficiencies across the supply chain with each custom part.
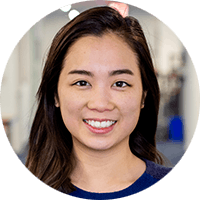